With MSP430 processor as the core, combined with photoelectric micro-loss blood glucose monitoring technology, and using three-probe fiber bundle sensor, a new blood glucose monitoring system is designed.
Keywords:
MSP430; micro-loss; blood glucose; fiber optic sensor
The World Health Organization pointed out in a 2007 report that there are currently 170 million patients with diabetes mellitus (DM) in the world, and it is predicted that this number will increase dramatically to 299 million by 2025. Diabetes has become the fifth leading cause of death in the world
[1]
. DM patients in China account for 3.3%. Insulin therapy is the main treatment for all insulin-dependent diabetics. The basis for determining insulin dosage is to closely monitor blood sugar control. Among the commonly used methods for evaluating the condition, venous blood sugar and capillary blood sugar measurement are currently the most direct methods for evaluating blood sugar control, and the latter is more suitable for family and patient self-blood sugar monitoring. Studies have shown that long-term and strict blood sugar monitoring can prevent or delay the occurrence and development of diabetic complications
[2]
. Therefore, this paper designs a monitoring system suitable for diabetic patients to achieve blood sugar self-monitoring at home.
1 Design principle
1.1 Measurement principle
Drop a blood sample on a test paper containing glucose oxidase (GOD). The glucose in the blood sample is oxidized by GOD to gluconic acid. This substance reacts with another enzyme in the reagent, peroxidase, to generate a light-absorbing substance. During the test, the test paper is placed in the optical path of the reflective intensity modulated fiber optic sensor, as shown in Figure 1. The entire sensor system includes a light source, a transmitting fiber, a receiving fiber, and a photodetector [3]. The light emitted by the light source is filtered and transmitted to the surface of the blood sample to be tested through the transmitting fiber. Due to the modulation of the light-absorbing substance, the reflected light carrying blood sugar concentration information is received by the receiving fiber, and finally the photoelectric receiver converts the received light into an electrical signal. When the light source power and the distance between the fiber probe and the reflecting surface remain unchanged, the ratio of the light intensity of a certain wavelength received by the receiving fiber to the incident light intensity of the wavelength corresponds to the blood sugar concentration. Based on the detected light intensity signal, the blood sugar concentration can be calculated. However, the main disadvantage of this fiber optic sensor is that when the light source excitation is unstable, the light source power will change, resulting in measurement errors. In addition, the different reflectivity of the reflector surface and the transmission loss of light in the optical fiber will cause errors in the measurement. Therefore, this paper proposes a three-probe optical fiber sensor compensation measurement method to eliminate the influence of various unstable factors in the measurement environment.
1.2 Principle of compensation measurement method of three-probe fiber bundle sensor
Since the traditional reflective intensity modulation fiber sensor uses a single optical fiber to send and receive very weak light energy, this design uses a fiber bundle composed of thousands of optical fibers to send and receive light, and adds a reference optical path to form a three-probe fiber bundle sensor, as shown in Figure 2. In order to make the reference light have a reference significance for the measurement light, it is required that the light spots irradiated on the sample to be measured by the reference and measurement light are consistent. Therefore, the entire fiber optic sensor probe adopts a concentric circle structure, with two transmitting fiber bundles as the inner circle, which are randomly and evenly distributed, and the outer ring is the receiving fiber bundle. When there are enough measuring fibers and reference fibers, the light spot area irradiated on the object by the two wavelengths is approximately equal. In the actual production process, the measurement and reference fiber bundles each use 4,000 glass optical fiber strands, so it can be approximately considered that the measurement light and the reference light are in the same optical path, and its structure is shown in Figure 3. According to spectral analysis theory, light with a wavelength of 635nm cannot be effectively absorbed by the absorbing substances in the blood sample, and is only related to factors other than the absorbing substances in the blood sample, so it can be used as a reference wavelength. The light with a wavelength of 700nm is related to both the concentration of the absorbing substance and factors other than the absorbing substance, so it can be used as the measurement wavelength. In Figure 2, the light emitting diodes D1 and D2 emit light with the same intensity and wavelength of 635nm and 700nm, respectively, which are incident on the optical fiber, are guided out by D3 after reflection, and then separated into lights of different wavelengths by the spectroscopic element and filter. The light intensity ratio reflects the size of the blood sugar concentration. This type of optical fiber probe is closely arranged without gaps, with the same optical fiber size and optical path, and can be easily made into a strip shape. It can automatically compensate for the influence of changes in light source intensity, reflectivity, and environmental factors on the measurement accuracy.
2 Hardware Design
2.1 System Design
The monitoring device consists of a CPU, a three-probe fiber bundle sensor, an amplifier circuit, an LCD, a keyboard, a Y-type beam splitter, an alarm part, a filter, etc., as shown in Figure 4. Its working process is: the program solidified in the CPU makes its I/O port control the LED drive circuit to generate a reference wavelength and a measurement wavelength of 10kHz, and the three-probe fiber bundle sensor irradiates the measurement light and the reference light to the blood sample to be tested, and the reflected light is introduced into the Y-type beam splitter. After passing through the filter, the two beams of light with different wavelengths enter the logarithmic and differential amplifiers to convert into electrical signals, and then enter the CPU for A/D conversion and data analysis, and the results are displayed on the LCD.
2.2 Control circuit and sensor design
The control circuit consists of CPU, CD4049, LCD, light source, keyboard and other devices, as shown in Figure 5.
The CPU uses TI's high-end processor
MSP430F149
, which is an ultra-low power, high-performance 16-bit embedded processor with advanced RISC structure and operates at 32MHz
[4]
. Timer 0 is used to control the P1.3 pin to generate a square wave with a period of 10kHz to control the light source. Since the MSP430F149 has an internal integrated 60KB programmable Flash that can be erased and written 10,000 times, there is no need to expand the program memory, which greatly saves the circuit board manufacturing area and improves the integration. The display part is composed of a 122×32 graphic dot matrix LCD EW12A03GLY. The LCD read and write pins E1, E2, and A0 are controlled by the CPU's P2.0, P2.1, and P2.2 respectively. VLED and VLSS provide backlight voltage for the LCD screen. Since the MSP430F149 has an internal integrated high-precision 12-bit A/D converter, there is no need to add an additional A/D chip. The output of the differential amplifier is connected to the P6.0/A0 pin of the MSP430F149 for A/D conversion after filtering.
2.3 Design of photoelectric conversion and amplifier circuit
According to theoretical analysis, the measurement of blood glucose concentration is converted into the measurement of light intensity ratio, which is converted into the measurement of current ratio after photoelectric conversion. Therefore, logarithmic amplification and differential amplification are required to obtain the current ratio. The LOG114 amplifier of TI is selected, which integrates two logarithmic amplifiers, two independent differential amplifiers and an internal reference voltage of 2.5V to meet the detection needs. This amplifier is dedicated to detecting the photodiode signal output by the optical fiber cable without the need for an external circuit. It supports a dynamic range of 8 orders of magnitude from 100pA to 10mA, and has high-speed and high-precision performance, thereby avoiding the secondary error caused by the circuit composed of discrete components, which is very suitable for light control systems. The circuit is shown in Figure 6. The two optical signals are input from pins 1, 3, 4, and 5 respectively. The amplification factor can be adjusted by adjusting the ratio of R1/R2. The relationship between the output voltage and the input current is:
3 Software Design
The software structure mainly consists of modules such as the main program, interrupt subroutine and display program. The program flow is shown in Figure 7.
The basic process is: press the start button, the system generates a 10kHz pulse at P1.3 to control the light source, so that the light source emits pulses with the same frequency, intensity, and wavelengths of 635nm and 700nm respectively;
MSP430F149
selects channel A0 for A/D conversion through ACTL (2-4). When the conversion is completed, the EOC signal becomes high, and the interrupt flag ADIFG is set to activate the interrupt; the 12-bit result ADAT (low 12 bits are valid) generated by the ADC is stored in the interrupt program, and after sampling 10 times, the sampling and pulse sending are stopped. Analyze the sampled data. If the measured value exceeds the preset warning value, an alarm will sound, and the measurement result will be displayed on the LCD, and the main program will be returned to wait for the next measurement interrupt.
4 Experimental results
This system is used to collect blood samples between two meals. The sampling data is shown in Table 1. The measurement results are fitted and compared with the results of the Prestige blood glucose meter using MATLAB, as shown in Figure 8.
The experimental results show that the measurement results of this system reflect the blood glucose concentration well, and it has the advantages of low power consumption and portability. Diabetic patients can easily achieve self-monitoring at home.
Previous article:Design and Implementation of a Function Generator Based on Single Chip Microcomputer
Next article:Fault Diagnosis Method and Implementation of Single Chip Microcomputer Application Circuit Board
Recommended ReadingLatest update time:2024-11-16 19:42
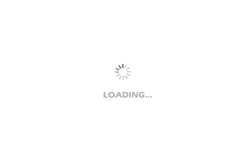
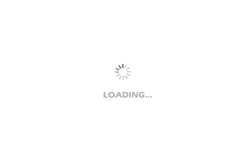
- Popular Resources
- Popular amplifiers
-
MSP430 series single chip microcomputer system engineering design and practice
-
oled multi-chip calling program
-
Microcontroller Principles and Applications Tutorial (2nd Edition) (Zhang Yuanliang)
-
Getting Started and Improving MSP430 Microcontrollers - National Undergraduate Electronic Design Competition Training Course
- Molex leverages SAP solutions to drive smart supply chain collaboration
- Pickering Launches New Future-Proof PXIe Single-Slot Controller for High-Performance Test and Measurement Applications
- CGD and Qorvo to jointly revolutionize motor control solutions
- Advanced gameplay, Harting takes your PCB board connection to a new level!
- Nidec Intelligent Motion is the first to launch an electric clutch ECU for two-wheeled vehicles
- Bosch and Tsinghua University renew cooperation agreement on artificial intelligence research to jointly promote the development of artificial intelligence in the industrial field
- GigaDevice unveils new MCU products, deeply unlocking industrial application scenarios with diversified products and solutions
- Advantech: Investing in Edge AI Innovation to Drive an Intelligent Future
- CGD and QORVO will revolutionize motor control solutions
- Innolux's intelligent steer-by-wire solution makes cars smarter and safer
- 8051 MCU - Parity Check
- How to efficiently balance the sensitivity of tactile sensing interfaces
- What should I do if the servo motor shakes? What causes the servo motor to shake quickly?
- 【Brushless Motor】Analysis of three-phase BLDC motor and sharing of two popular development boards
- Midea Industrial Technology's subsidiaries Clou Electronics and Hekang New Energy jointly appeared at the Munich Battery Energy Storage Exhibition and Solar Energy Exhibition
- Guoxin Sichen | Application of ferroelectric memory PB85RS2MC in power battery management, with a capacity of 2M
- Analysis of common faults of frequency converter
- In a head-on competition with Qualcomm, what kind of cockpit products has Intel come up with?
- Dalian Rongke's all-vanadium liquid flow battery energy storage equipment industrialization project has entered the sprint stage before production
- Allegro MicroSystems Introduces Advanced Magnetic and Inductive Position Sensing Solutions at Electronica 2024
- Car key in the left hand, liveness detection radar in the right hand, UWB is imperative for cars!
- After a decade of rapid development, domestic CIS has entered the market
- Aegis Dagger Battery + Thor EM-i Super Hybrid, Geely New Energy has thrown out two "king bombs"
- A brief discussion on functional safety - fault, error, and failure
- In the smart car 2.0 cycle, these core industry chains are facing major opportunities!
- The United States and Japan are developing new batteries. CATL faces challenges? How should China's new energy battery industry respond?
- Murata launches high-precision 6-axis inertial sensor for automobiles
- Ford patents pre-charge alarm to help save costs and respond to emergencies
- New real-time microcontroller system from Texas Instruments enables smarter processing in automotive and industrial applications
- [Evaluation of EC-01F-Kit, the NB-IoT development board of Anxinke] + Try to connect the serial port assistant to Alibaba Cloud
- [Jihai APM32E103VET6S MINI Development Board Review] Part 4: Key Interrupt
- Technology Popularization: Do you know why base stations are painted in colors?
- A brief list of long and short distance wireless communication technologies
- A classic foreign book about semaphores
- If there is a hidden function on the right side, the reading area will be larger.
- Online ESP32 simulator is awesome! It takes more than ten minutes to help netizens light a lamp
- STLINK power supply has problems
- ANT Visualization
- pwm