The following is a circuit schematic diagram drawn based on the actual object: (There are many ways to install components on the circuit board. Please refer to the schematic diagram and the actual picture for installation. Some component holes on the PCB board should not be installed, and some components should be installed in other component holes. Please pay attention to this!)
Note: In order to simplify the circuit and achieve the purpose of learning, a 1-ohm resistor F1 is used as a fuse in the figure, and a diode D1 is used to complete the rectification. After the power is turned on, C1 will have a DC voltage of about 300V, which provides current to the base of Q1 through R2. The emitter of Q1 has a current detection resistor R1. After the base of Q1 is energized, it will generate collector current through T1's (3, 4) and simultaneously generate induced voltage on T1's (5, 6) (1, 2). These two secondary insulated coils have the same number of turns. The output of T1 (1, 2) is rectified by D7 and filtered by C5, and then powered by the USB socket to the load; T1 (5, 6) is rectified by D6 and filtered by C2, and then passes through IC1 (actually a 4.3V voltage regulator) and Q2 to form a sampling and comparison circuit to detect the output voltage; T1 (5, 6), C3, and R4 also form the positive feedback circuit of the Q1 transistor, allowing Q1 to work at a high frequency oscillation and continuously power the T1 (3, 4) switch. When the output voltage increases due to any reason, such as the load becoming lighter or the power supply voltage becoming higher, T1 (5, 6) and IC1 sampling and comparison cause Q2 to turn on, Q1 base current decreases, collector current decreases, and load capacity decreases, thereby causing the output voltage to decrease; when the output voltage decreases, Q2 will be cut off after sampling, Q1's load capacity will increase, and the output voltage will increase again; this plays an automatic voltage stabilization role.
Although this circuit has few components, it is also designed with overcurrent, overload and short-circuit protection functions. When the load is overloaded or short-circuited, the collector current of Q1 increases greatly, and the emitter resistor R1 of Q1 will produce a higher voltage drop. The high voltage generated by this overload or short circuit will pass through R3 to saturate Q2 and turn on, thereby stopping Q1 from outputting to prevent overload damage. Therefore, changing the size of R1 can change the load capacity. If a small output current is required, for example, only 5V100MA needs to be output, the resistance value of R1 can be increased. Of course, if 5V500MA needs to be output, R1 needs to be appropriately reduced. Note: Reducing R1 will increase the possibility of burning Q1. If a large current output is required, it is recommended to replace the high-power tube 13003 or 13007. What are the functions of C4, R5, and D5? Transformer T1 is an inductive component, and Q1 works in a switching state. When Q1 is cut off, a very high voltage will be induced at the collector, which may be as high as 1000 volts or more, which will cause Q1 to break down and be damaged. Now we have a high-speed switching tube D5, and this voltage can charge C4 and absorb this high voltage. After C4 is charged, it can be discharged immediately through R5, so that Q1 will not be damaged by the high voltage breakdown of the collector. Therefore, if these three components are switched or damaged, Q1 is very dangerous and may be damaged at any time.
Previous article:A design scheme of switching power supply based on PWM soft switching mode
Next article:USB Charging Solutions: High-Efficiency AC Adapters
Recommended ReadingLatest update time:2024-11-16 01:22
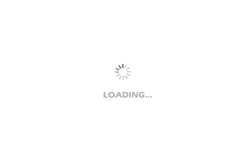
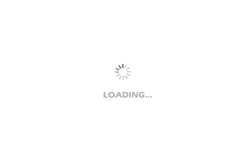
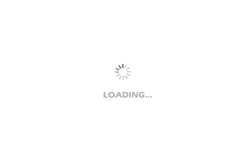
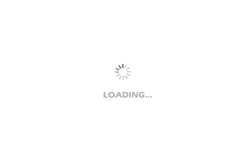
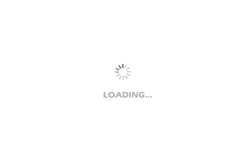
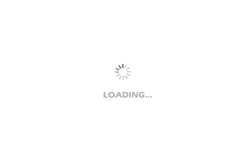
- Popular Resources
- Popular amplifiers
-
Virtualization Technology Practice Guide - High-efficiency and low-cost solutions for small and medium-sized enterprises (Wang Chunhai)
-
usb_host_device_code
-
Image acquisition and processing system for panoramic map applications
-
Teach you to learn 51 single chip microcomputer-C language version (Second Edition) (Song Xuefeng)
- MathWorks and NXP Collaborate to Launch Model-Based Design Toolbox for Battery Management Systems
- STMicroelectronics' advanced galvanically isolated gate driver STGAP3S provides flexible protection for IGBTs and SiC MOSFETs
- New diaphragm-free solid-state lithium battery technology is launched: the distance between the positive and negative electrodes is less than 0.000001 meters
- [“Source” Observe the Autumn Series] Application and testing of the next generation of semiconductor gallium oxide device photodetectors
- 采用自主设计封装,绝缘电阻显著提高!ROHM开发出更高电压xEV系统的SiC肖特基势垒二极管
- Will GaN replace SiC? PI's disruptive 1700V InnoMux2 is here to demonstrate
- From Isolation to the Third and a Half Generation: Understanding Naxinwei's Gate Driver IC in One Article
- The appeal of 48 V technology: importance, benefits and key factors in system-level applications
- Important breakthrough in recycling of used lithium-ion batteries
- LED chemical incompatibility test to see which chemicals LEDs can be used with
- Application of ARM9 hardware coprocessor on WinCE embedded motherboard
- What are the key points for selecting rotor flowmeter?
- LM317 high power charger circuit
- A brief analysis of Embest's application and development of embedded medical devices
- Single-phase RC protection circuit
- stm32 PVD programmable voltage monitor
- Introduction and measurement of edge trigger and level trigger of 51 single chip microcomputer
- Improved design of Linux system software shell protection technology
- What to do if the ABB robot protection device stops
- Allegro MicroSystems Introduces Advanced Magnetic and Inductive Position Sensing Solutions at Electronica 2024
- Car key in the left hand, liveness detection radar in the right hand, UWB is imperative for cars!
- After a decade of rapid development, domestic CIS has entered the market
- Aegis Dagger Battery + Thor EM-i Super Hybrid, Geely New Energy has thrown out two "king bombs"
- A brief discussion on functional safety - fault, error, and failure
- In the smart car 2.0 cycle, these core industry chains are facing major opportunities!
- The United States and Japan are developing new batteries. CATL faces challenges? How should China's new energy battery industry respond?
- Murata launches high-precision 6-axis inertial sensor for automobiles
- Ford patents pre-charge alarm to help save costs and respond to emergencies
- New real-time microcontroller system from Texas Instruments enables smarter processing in automotive and industrial applications
- China's first batch of autonomous driving unmanned commercial licenses issued! Do you dare to sit in an unmanned car? ?
- GDB debugging and DSP
- The IO pin of MSP430 is set as input, but it receives the output signal of the Hall sensor, and the chip-side signal does not switch.
- [Serial] [Starlight Lightning STM32F407 Development Board] Chapter 10 Serial Communication Experiment
- Where do errors in vector network analyzers come from?
- [Perf-V Evaluation] Environment Construction and Marquee Program Running
- The relationship between serial port communication and interruption
- How to use a wiring harness tester to measure small resistance? Here's a method
- Those who don't know about RF MEMS, please take a look. This is what the technology is like.
- Ten important facts and trends in motor control