IntroductionPower
supply sequencing is a necessary function for microcontrollers, FPGAs, DSPs, ADCs, and other devices that require multiple voltage rails. These applications typically require the core and analog blocks to be powered up before the digital I/O rails, but some designs may require other sequences. Regardless, proper power-up and power-down sequencing can prevent both immediate damage from latch-up and long-term damage from ESD. In addition, power supply sequencing can stagger inrush currents during power-up, a technique that is useful for applications powered from current-limited supplies.
This article discusses the pros and cons of using discrete components for power sequencing and introduces a simple and effective method for sequencing using the precision enable pins of the ADP5134, which has two 1.2-A buck regulators and two 300-mA LDOs. It also lists a range of ICs that can be used in applications that require more precise and flexible sequencing.
An application that requires multiple power rails is shown in Figure 1. These rails are the core power supply (VCCINT), I/O power supply (VCCO), auxiliary power supply (VCCAUX), and system memory power supply.
Figure 1. Typical power supply method for processors and FPGAs
For example, the Xilinx Spartan-3A FPGA has a built-in power-on reset circuit that ensures that all supplies reach their thresholds before allowing the device to be configured. This helps to reduce power supply sequencing requirements, but to achieve minimum inrush current levels and comply with the sequencing requirements of the circuits connected to the FPGA, the power rails should be powered up in the following sequence: VCC_INT → VCC_AUX → VCCO. Please note: Some applications require a specific sequence, so be sure to read the power supply requirements section of the data sheet.
Simplify Power Supply Sequencing Using Passive Delay Networks
A simple way to sequence power supplies is to use passive components such as resistors, capacitors, and diodes to delay the signal going to the regulator’s enable pin, as shown in Figure 2. When the switch is closed, D1 conducts while D2 remains open. Capacitor C1 charges and the voltage at EN2 rises at a rate determined by R1 and C1. When the switch is open, capacitor C1 discharges to ground through R2, D2, and RPULL. The voltage at EN2 decreases at a rate determined by R2, RPULL, and C2. Changing the values of R1 and R2 changes the charge and discharge times, thus setting the regulator’s turn-on and turn-off times.
Figure 2. A simple method for power supply sequencing using resistors, capacitors, and diodes.
This method can be used in applications that do not require precise timing control, and some applications that only need to delay the signal and may only require external R and C. The disadvantage of using this method for standard regulators is that the logic threshold of the enable pin can vary greatly due to voltage and temperature. In addition, the delay in the voltage ramp depends on the resistor and capacitor values and tolerances. Typical X5R capacitors vary by about ±15% over the temperature range of –55°C to +85°C, and another ±10% due to dc bias effects, making the timing control imprecise and sometimes unreliable.
Precision enables easy timing control
To achieve stable threshold levels for precise timing control, most regulators require an external reference voltage source. The ADP5134 solves this problem by integrating a precision reference voltage source, significantly saving cost and PCB area. Each regulator has an independent enable pin. When the voltage at the enable input rises above VIH_EN (minimum 0.9 V), the device exits shutdown mode and the management module is turned on, but the regulator is not activated. The voltage at the enable input is compared to a precision internal reference voltage (typically 0.97 V). Once the voltage at the enable pin rises above the precision enable threshold, the regulator is activated and the output voltage begins to increase. The reference voltage varies only ±3% at the input voltage and temperature transitions. This small range of variation ensures precise timing control and solves various problems encountered when using discrete components.
When the voltage at the enable input drops 80 mV (typical) below the reference voltage, the regulator is disabled. When the voltage on all enable inputs drops below VIL_EN (0.35 V maximum), the device enters shutdown mode. In this mode, the current consumption drops to less than 1 μA. Figure 3 and Figure 4 show the accuracy of the ADP5134 precision enable threshold for Buck1 over temperature.
Figure 3. Precision enable turn-on threshold over temperature (10 samples)
Figure 4. Precision enable shutdown threshold over temperature (10 samples) Simplifying power supply sequencing using resistor dividers
By connecting an attenuated version of the regulator output to the enable pin of the next regulator to be powered up, a multichannel power supply can be sequenced as shown in Figure 5, where the regulators are turned on or off in the following order: Buck1 → Buck2 → LDO1 → LDO2. Figure 6 shows the power-up sequence when EN1 is connected to VIN1. Figure 7 shows the shutdown sequence when EN1 is disconnected from VIN1.
Figure 5. Simple timing control using the ADP5134.
Figure 6. ADP5134 startup sequence.
Figure 7. ADP5134 shutdown sequence.
Sequencer ICs Improve Timing Accuracy
In some cases, achieving precise timing is more important than reducing PCB area and cost. For these applications, you can use a voltage monitoring and sequencer IC, such as the ADM1184 quad-channel voltage supervisor, which has an accuracy of ±0.8% over voltage and temperature. Alternatively, for applications that require more precise power-up and power-down sequence control, you can use the ADM1186 quad-channel voltage sequencer and supervisor with programmable timing control.
The ADP5034 quad regulator integrates two 3-MHz, 1200-mA step-down regulators and two 300 mA LDOs. A typical sequencing function can be implemented by using the ADM1184 to monitor the output voltage of one regulator and provide a logic high signal to the enable pin of the next regulator when the monitored output voltage reaches a certain level. This method (shown in Figure 8) can be used for regulators that do not have a precision enable function.
Figure 8. Sequencing the ADP5034 quad regulator using the ADM1184 quad voltage monitor.
in conclusion
Sequencing is simple and easy using the ADP5134 precision enable input, requiring only two external resistors per channel. More precise sequencing can be achieved with the ADM1184 or ADM1186 voltage supervisors.
Previous article:Digitally controlled multi-phase interleaved DC/DC step-down system solution
Next article:Golden Rule 11: DC/DC Power Conversion Solution Design
Recommended ReadingLatest update time:2024-11-17 00:05
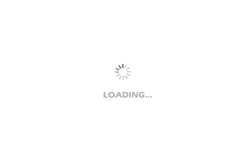
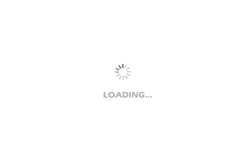
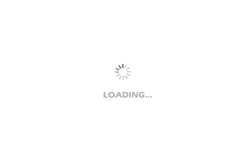
![[MCU framework][BSP layer][AT32F415][bsp_adc] ADC configuration and use](https://6.eewimg.cn/news/statics/images/loading.gif)
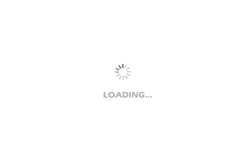
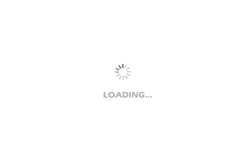
- Popular Resources
- Popular amplifiers
-
Analysis and Implementation of MAC Protocol for Wireless Sensor Networks (by Yang Zhijun, Xie Xianjie, and Ding Hongwei)
-
MATLAB and FPGA implementation of wireless communication
-
Modern arc welding power supply and its control
-
Intelligent Control Technology of Permanent Magnet Synchronous Motor (Written by Wang Jun)
- MathWorks and NXP Collaborate to Launch Model-Based Design Toolbox for Battery Management Systems
- STMicroelectronics' advanced galvanically isolated gate driver STGAP3S provides flexible protection for IGBTs and SiC MOSFETs
- New diaphragm-free solid-state lithium battery technology is launched: the distance between the positive and negative electrodes is less than 0.000001 meters
- [“Source” Observe the Autumn Series] Application and testing of the next generation of semiconductor gallium oxide device photodetectors
- 采用自主设计封装,绝缘电阻显著提高!ROHM开发出更高电压xEV系统的SiC肖特基势垒二极管
- Will GaN replace SiC? PI's disruptive 1700V InnoMux2 is here to demonstrate
- From Isolation to the Third and a Half Generation: Understanding Naxinwei's Gate Driver IC in One Article
- The appeal of 48 V technology: importance, benefits and key factors in system-level applications
- Important breakthrough in recycling of used lithium-ion batteries
- Innolux's intelligent steer-by-wire solution makes cars smarter and safer
- 8051 MCU - Parity Check
- How to efficiently balance the sensitivity of tactile sensing interfaces
- What should I do if the servo motor shakes? What causes the servo motor to shake quickly?
- 【Brushless Motor】Analysis of three-phase BLDC motor and sharing of two popular development boards
- Midea Industrial Technology's subsidiaries Clou Electronics and Hekang New Energy jointly appeared at the Munich Battery Energy Storage Exhibition and Solar Energy Exhibition
- Guoxin Sichen | Application of ferroelectric memory PB85RS2MC in power battery management, with a capacity of 2M
- Analysis of common faults of frequency converter
- In a head-on competition with Qualcomm, what kind of cockpit products has Intel come up with?
- Dalian Rongke's all-vanadium liquid flow battery energy storage equipment industrialization project has entered the sprint stage before production
- Allegro MicroSystems Introduces Advanced Magnetic and Inductive Position Sensing Solutions at Electronica 2024
- Car key in the left hand, liveness detection radar in the right hand, UWB is imperative for cars!
- After a decade of rapid development, domestic CIS has entered the market
- Aegis Dagger Battery + Thor EM-i Super Hybrid, Geely New Energy has thrown out two "king bombs"
- A brief discussion on functional safety - fault, error, and failure
- In the smart car 2.0 cycle, these core industry chains are facing major opportunities!
- The United States and Japan are developing new batteries. CATL faces challenges? How should China's new energy battery industry respond?
- Murata launches high-precision 6-axis inertial sensor for automobiles
- Ford patents pre-charge alarm to help save costs and respond to emergencies
- New real-time microcontroller system from Texas Instruments enables smarter processing in automotive and industrial applications
- KiCAD JLCPCB Tools
- RISC-V MCU Development Practice (Part 3): Porting Hongmeng OS Project
- How to allocate time?
- 【1】First look at Silicon Labs development kit
- The Definitive Guide to Visual Studio Code
- LPC1788--TIMER match interrupt setting--register operation
- Please help explain this circuit, it should be a voltage regulator
- MSP430F149 two port functions and settings
- DCDC Chip
- Download the information to win a Jingdong card | Tektronix combines both "software" and "hardware" to create a super-value oscilloscope