Embedded engineers are often very good at using microcontrollers, ARM, DSP, and FPGA. However, once they start system design and power the power system, although they can make their carefully designed programs run, for novices, it may sometimes be inefficient, and there are often problems such as insufficient or excessive power supply current. The ten golden rules in this article can easily solve the DCDC power conversion circuit design.
First, understand what DC/DC power supply is all about
The DC/DC power supply circuit is also called the DC/DC conversion circuit. Its main function is to convert the input and output voltages. Generally, we call the voltage conversion process within 72V as DC/DC conversion. Common power supplies are mainly divided into vehicle-mounted and communication series and general industrial and consumer series. The voltage used by the former is generally 48V, 36V, 24V, etc., and the power supply voltage used by the latter is generally below 24V. Different application fields have different rules. For example, 12V, 5V, and 3.3V are commonly used in PCs, 5V 15V is commonly used for analog circuit power supplies, and 3.3V is commonly used for digital circuits. Now FPGA and DSP still use voltages below 2V, such as 1.8V, 1.5V, 1.2V, etc. In the communication system, it is also called the secondary power supply. It is provided by a primary power supply or a DC battery pack to provide a DC input voltage, and after DC/DC conversion, one or several DC voltages are obtained at the output end.
Article 2: Classification of DC/DC conversion circuits that need to be known
DC/DC conversion circuits are mainly divided into the following three categories:
① Zener diode voltage regulator circuit. ② Linear (analog) voltage regulator circuit. ③ Switching voltage regulator circuit
Article 3. The simplest voltage regulator circuit design solution
The voltage regulator circuit has a simple structure, but has poor load capacity and low output power. It generally only provides reference voltage for the chip and is not used as a power supply. The most commonly used is the parallel voltage regulator circuit, whose circuit diagram is shown in Figure (1).
When selecting a Zener diode, it can generally be estimated according to the following formula: (1) Uz=Vout; (2) Izmax=(1.5-3)ILmax (3) Vin=(2-3)Vout This circuit has a simple structure and can suppress input voltage disturbances. However, it is limited by the maximum operating current of the Zener diode and the output voltage cannot be adjusted arbitrarily. Therefore, this circuit is suitable for occasions where the output voltage does not need to be adjusted, the load current is small, and the requirements are not high. This circuit is often used to power chips that do not have high requirements for the supply voltage.
Article 4. Voltage stabilization circuit of reference voltage source chip
Another form of voltage stabilization circuit, some chips have relatively high requirements for power supply voltage, such as the reference voltage of AD DA chips, etc. At this time, some commonly used voltage reference chips such as TL431, MC1403, REF02, etc. TL431 is the most commonly used reference source chip, a three-terminal adjustable shunt reference voltage source with good thermal stability. Its output voltage can be arbitrarily set to any value from Vref (2.5V) to 36V with two resistors. The most commonly used circuit application is shown in the figure below, at this time Vo= (1+R1/R2) Vref. Selecting different values of R1 and R2 can obtain any voltage output from 2.5V to 36V, especially when R1=R2, Vo=5V.
The circuits of several other reference voltage source chips are similar. Article 5. Understanding the circuit of series voltage regulator
The series voltage regulator circuit is a type of DC voltage regulator. In fact, it was a common DC power supply method before the three-terminal voltage regulator appeared. Before the three-terminal voltage regulator appeared, the series voltage regulator usually had an OP amplifier and a voltage regulator diode to form an error detection circuit, as shown in the figure below. In this circuit, the reverse input terminal of the OP amplifier is connected to the detection signal of the output voltage, and the forward input terminal is connected to the reference voltage Vref, Vs=Vout*R2/(R1+R2). Since the amplified signal ΔVs is a negative value, the base voltage of the control transistor decreases, so the output voltage decreases. Under normal circumstances, Vref=Vs=Vout*R2/(R1+R2). Adjusting the ratio of R1 and R2 can set the required output voltage value.
The figure shows that this is the basic principle of the three-terminal voltage regulator. In fact, the load size can be changed by replacing the transistor with a Darlington tube, etc. This series voltage regulator circuit is used to form a DC voltage regulator. If it is not handled properly, it is very easy to oscillate. Engineers who do not have a certain simulation foundation generally do not use this method, but directly use an integrated three-terminal voltage regulator circuit for the use of DC/DC conversion circuits.
Article 6. Commonly used design schemes for linear (analog) integrated voltage regulator circuits
The design of linear voltage regulator circuit is mainly based on three-terminal integrated voltage regulator. There are two main types of three-terminal voltage regulators:
A type of three-terminal voltage regulator has a fixed output voltage. The common products of three-terminal voltage regulators are 78 series (positive power supply) and 79 series (negative power supply). The output voltage is represented by the last two digits in the specific model, and there are 5V, 6V, 8V, 9V, 12V, 15V, 18V, 24V and other grades. The output current is distinguished by adding a letter after 78 (or 79). L means 0.1A, M means 0.5A, and no letter means 1.5A, such as 78L05 table for 5V 0.1A.
Another type of linear voltage regulator circuit with adjustable output voltage is called an adjustable output three-terminal voltage regulator. Representative chips of this type are the LM317 (positive output) and LM337 (negative output) series. Its maximum input-output limit difference is 40V, the output voltage is 1.2V-35V (-1.2V--35V) continuously adjustable, the output current is 0.5-1.5A, the voltage between the output terminal and the adjustment terminal is 1.25V, and the static current of the adjustment terminal is 50uA.
The basic principle is the same, and both use a series voltage regulator circuit. Among linear integrated voltage regulators, the three-terminal voltage regulator has only three lead terminals, has the advantages of few external components, easy use, stable performance, and low price, so it is widely used.
Article 7. Design of DC/DC conversion switch type voltage regulator circuit
The several DCDC conversion circuits described above are all series feedback voltage regulator circuits. In this working mode, the adjustment tube in the integrated voltage regulator works in a linear amplification state. Therefore, when the load current is large, the loss is relatively large, that is, the conversion efficiency is not high. Therefore, the power of the power supply circuit using the integrated voltage regulator will not be very large, generally only 2-3W, and this design is only suitable for low-power power supply circuits.
The DCDC conversion circuit designed with switching power supply chip has high conversion efficiency and is suitable for larger power supply circuits. It has been widely used and is commonly divided into non-isolated switching power supply and isolated switching power supply circuits.
DCDC conversion switch type voltage regulator circuit design scheme, the DCDC conversion circuit designed with switching power supply chip has high conversion efficiency and is suitable for larger power supply circuits. It has been widely used at present, and the commonly used ones are divided into non-isolated switching power supply and isolated switching power supply circuits. Of course, the basic topologies of switching power supplies include buck type, boost type, buck-boost type, flyback, forward, bridge type, etc. Article 8. Non-isolated DC/DC switching conversion integrated circuit chip circuit design scheme
DCDC switch conversion integrated circuit chip, the use of this type of chip is very similar to the LM317 in Article 6. Here, L4960 is used as an example. Generally, a 50Hz power transformer is used for AC-AC conversion, and the ~220V is reduced to the input voltage range of the switching power supply integrated conversion chip, such as 1.2~34V, and the L4960 performs DC-DC conversion. At this time, the output voltage can be adjusted to 5V and 40V, and the maximum output current can reach 2.5A (it can also be connected to a high-power switch tube for current expansion), and it has perfect protection functions such as overcurrent protection and overheating protection. Although the use of L4960 is similar to that of LM317, the efficiency of L4960, a switching power supply, is not the same as that of LM317, a linear power supply. L4960 can output a maximum power of 100W (Pmax=40V*2.5A=100W), but it only consumes 7W at most, so the heat sink is very small and easy to make. Similar to L4960 is L296, which has the same basic parameters as L4960, but the maximum output current can be up to 4A, and it has more protection functions and different packaging. There are many such chips, such as LM2576 series, TPS54350, LTC3770, etc. Generally, when using these chips, the manufacturer will provide detailed instructions and typical circuits for reference.
Article 9. Isolated DC/DC switching power supply module circuit design scheme
Commonly used isolated DC/DC conversions are mainly divided into three categories: 1. Flyback conversion. 2. Forward conversion. 3. Bridge conversion.
Commonly used single-ended flyback DC/DC conversion circuits, there are many types of isolated control chips. The typical representative of the control chip is the commonly used UC3842 series. This is a high-performance fixed-frequency current controller, mainly used to isolate AC/DC and DC/DC conversion circuits. Its main application principle is: the circuit consists of four parts: main circuit, control circuit, startup circuit and feedback circuit. The main circuit adopts a single-ended flyback topology, which is formed by adding an isolation transformer after the evolution of the buck-boost chopper circuit. The circuit has the advantages of simple structure, high efficiency and wide input voltage range. The control circuit is the core of the entire switching power supply, and the quality of control directly determines the overall performance of the power supply. This circuit adopts peak current dual-loop control, that is, adding peak current feedback control to the voltage closed-loop control system. This type of solution can make the power very large by selecting a suitable transformer and MOS tube. Compared with the previous design schemes, the circuit structure is complex, the component parameters are difficult to determine, and the development cost is high. Therefore, when this solution is needed, the relatively cheap DC/DC isolation module on the market can be given priority.
Article 10. DC/DC switch integrated power module solution
Many microprocessors and digital signal processors (DSPs) require a core power supply and an input/output (I/O) power supply that must be sequenced at startup. Designers must consider the relative voltage and timing of the core and I/O voltage sources during power-up and power-down operations to meet the performance specifications specified by the manufacturer. Without proper power sequencing, latch-up or excessive current consumption may occur, which may cause damage to the microprocessor I/O ports or the I/O ports of supporting devices such as memory, programmable logic devices (PLDs), field programmable gate arrays (FPGAs), or data converters. In order to ensure that the I/O load is not driven before the core voltage is correctly biased, core power and I/O power supply tracking is required. There are now specialized power module companies that tailor some dedicated switching power modules, mainly those that are small in size, high in power density, high in conversion efficiency, low in heat, long mean time between failures, good in reliability, lower in cost and higher in performance DC/DC power modules in addition to conventional electrical performance indicators. These modules combine most or all of the components required to implement a plug-and-play solution and can replace up to 40 different components. This simplifies integration and speeds up design while reducing the board space occupied by the power management section.
The most traditional and common non-isolated DC/DC power modules are still single in-line (SiP) packages. These open frame solutions have indeed made progress in reducing design complexity. However, the simplest ones use components in standard packages on a printed circuit board .
Article 11. Considerations for selecting DC/DC power conversion solutions
This golden rule is also the summary of this article, which is very important. This article mainly introduces several commonly used design methods for three circuit modes of DCDC power conversion: Zener voltage regulation, linear (analog) voltage regulation, and DCDC switch voltage regulation.
①It should be noted that the voltage regulator circuit cannot be used as a power supply, and can only be used to power chips without power requirements; ②The linear voltage regulator circuit has a simple circuit structure, but due to its low conversion efficiency, it can only be used in low-power voltage regulators; ③The switching voltage regulator circuit has a high conversion efficiency and can be used in high-power occasions, but its limitation is that the circuit structure is relatively complex (especially high-power circuits), which is not conducive to miniaturization. Therefore, in the design process, you can choose a suitable design scheme according to actual needs.
Previous article:How to Simplify and Implement Complex Power Supply Sequencing
Next article:Miniaturized remote monitoring intelligent power supply system based on ARM Cortex-M3
Recommended ReadingLatest update time:2024-11-16 21:27
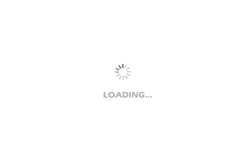
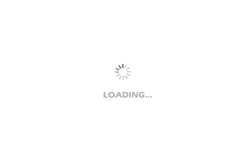
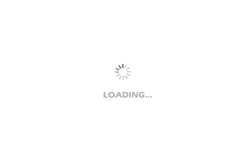
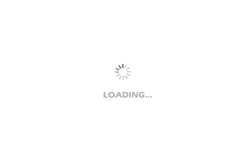
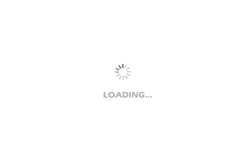
- Popular Resources
- Popular amplifiers
-
西门子S7-12001500 PLC SCL语言编程从入门到精通 (北岛李工)
-
New Energy Vehicle Detection and Diagnosis Experiment (Edited by Mao Caiyun, Zhou Xien, and Long Jiwen)
-
Virtualization Technology Practice Guide - High-efficiency and low-cost solutions for small and medium-sized enterprises (Wang Chunhai)
-
ESP32-S3 source code
- MathWorks and NXP Collaborate to Launch Model-Based Design Toolbox for Battery Management Systems
- STMicroelectronics' advanced galvanically isolated gate driver STGAP3S provides flexible protection for IGBTs and SiC MOSFETs
- New diaphragm-free solid-state lithium battery technology is launched: the distance between the positive and negative electrodes is less than 0.000001 meters
- [“Source” Observe the Autumn Series] Application and testing of the next generation of semiconductor gallium oxide device photodetectors
- 采用自主设计封装,绝缘电阻显著提高!ROHM开发出更高电压xEV系统的SiC肖特基势垒二极管
- Will GaN replace SiC? PI's disruptive 1700V InnoMux2 is here to demonstrate
- From Isolation to the Third and a Half Generation: Understanding Naxinwei's Gate Driver IC in One Article
- The appeal of 48 V technology: importance, benefits and key factors in system-level applications
- Important breakthrough in recycling of used lithium-ion batteries
- Innolux's intelligent steer-by-wire solution makes cars smarter and safer
- 8051 MCU - Parity Check
- How to efficiently balance the sensitivity of tactile sensing interfaces
- What should I do if the servo motor shakes? What causes the servo motor to shake quickly?
- 【Brushless Motor】Analysis of three-phase BLDC motor and sharing of two popular development boards
- Midea Industrial Technology's subsidiaries Clou Electronics and Hekang New Energy jointly appeared at the Munich Battery Energy Storage Exhibition and Solar Energy Exhibition
- Guoxin Sichen | Application of ferroelectric memory PB85RS2MC in power battery management, with a capacity of 2M
- Analysis of common faults of frequency converter
- In a head-on competition with Qualcomm, what kind of cockpit products has Intel come up with?
- Dalian Rongke's all-vanadium liquid flow battery energy storage equipment industrialization project has entered the sprint stage before production
- Allegro MicroSystems Introduces Advanced Magnetic and Inductive Position Sensing Solutions at Electronica 2024
- Car key in the left hand, liveness detection radar in the right hand, UWB is imperative for cars!
- After a decade of rapid development, domestic CIS has entered the market
- Aegis Dagger Battery + Thor EM-i Super Hybrid, Geely New Energy has thrown out two "king bombs"
- A brief discussion on functional safety - fault, error, and failure
- In the smart car 2.0 cycle, these core industry chains are facing major opportunities!
- The United States and Japan are developing new batteries. CATL faces challenges? How should China's new energy battery industry respond?
- Murata launches high-precision 6-axis inertial sensor for automobiles
- Ford patents pre-charge alarm to help save costs and respond to emergencies
- New real-time microcontroller system from Texas Instruments enables smarter processing in automotive and industrial applications
- HTS221 self-heating function test
- Understanding the configuration of C2000 series CMD files
- A batch of STM32F103RBT6 10 packages in stock
- PYPL October 2022 Rankings
- Looking for a voltage detection circuit or chip, 3v to 12v
- Weekly review information broadcast ~ Watch it all at once!
- Creative poker clock based on ESP32
- "Wanli" Raspberry Pi car launched
- You must call ros::init() before creating the first NodeHandle
- CSL library for GPIO of C6000 series DSP