1 Voltage regulator (regulator)
The 7.42V reference voltage output from the VREF pin is used as the reference for the control logic voltage. Vcc is usually 12.7V. Before outputting VREF, Vcc must be at least 9.3V. In the range of 0-85℃, the accuracy of VREF is ±3.5%.
2 Lamp voltage regulator
Under conditions such as preheating, ignition and lamp shutdown, the maximum open-circuit voltage across the lamp load must be limited. During voltage regulation, the lamp voltage is controlled by the arc voltage of the lamp and is not controlled by the control circuit. When the VLAMP pin voltage exceeds VREF, the lamp voltage comparator detects the VLAMP pin voltage. During this period, the lamp voltage reaches the maximum allowable open-circuit voltage value, and the VLAMP voltage is reduced by the fast frequency increase circuit. The RXCX time constant determines the frequency deviation time of the startup circuit (ratio is 2:1).
3 Undervoltage lockout protection
When the PFC and half-bridge control circuit should be turned on or off, the protection circuit uses the Schmidt trigger to detect the DC power supply voltage at the Vcc pin and determine the upper and lower limit trip points of the power supply voltage. Before Vcc rises from zero volts to the upper voltage limit (11V), the PFC and half-bridge control circuits remain in the off state. Once Vcc exceeds the upper voltage limit, the PFC and half-bridge oscillator circuits start to work. When Vcc is lower than the lower voltage limit (10V), the PFC and half-bridge circuits are turned off. Before Vcc exceeds the upper trip point, the PFC and half-bridge oscillator are not allowed to work. The minimum delay is set by the components outside the DMAX pin.
4 Lamp startup and PFC overvoltage protection
The half-bridge undervoltage lockout circuit samples the DC output voltage of the PFC. Before the PFC output voltage reaches the set value (such as 400VDC), the undervoltage lockout circuit prohibits the lamp from igniting. When the OV pin input voltage exceeds 5/7 VREF, the inverter frequency shifts from the maximum value when the lamp is preheated to the lower frequency when the lamp is normally ignited, and the ignition procedure begins. The
overvoltage protection circuit prevents the PFC DC output voltage from exceeding the set value. When the voltage at the overvoltage comparator input pin OV is much higher than VREF, the PFC buffer gate drive output OUTP is turned off to prevent the PFC DC output voltage from increasing further. The overvoltage protection circuit only protects against overvoltage or overshoot generated by the PFC circuit, and cannot suppress transient voltages on the AC line.
5 Capacitive load protection
The capacitive load protection circuit is used to prevent the half-bridge power transistor from failing when the lamp is removed. When the frequency exceeds the resonant frequency of the half-bridge LC load network, the primary voltage will lead the primary current. The protection logic detects the phase relationship between the resonant current and the voltage of the LC network. The IPRIM pin input voltage is the primary current signal of the LC network. If the IPRIM pin voltage is higher than -100mV (positive), that is, when the gate drive signal is high, the system fails and the frequency of the half-bridge oscillator increases.
6 Half-bridge oscillator
The half-bridge oscillator is a triangle wave generator used to generate a square wave signal to drive the buffer circuit. The oscillation frequency is determined by the resistance and capacitance values of the RT and CT pins, and the CT pin voltage is a triangle wave voltage.
7 Output Buffer Driver
The output buffer is used as a level shifter to convert the low-level logic signals of the half-bridge oscillator and the pulse width modulator into a 10V drive signal to drive the two power switches of the external half-bridge circuit. The OUTH half-bridge buffer/driver circuit drives the external level shift circuit, which then drives the half-bridge power switch. The OUTP output can directly drive the MOSFET or the external level shift circuit combined with the power MOSFET.
8 Pulse Width Modulator
PWM control circuit is used to control the duty cycle of the PFC. The PWM frequency is determined by the half-bridge oscillator. The ramp voltage appears at the CP output pin and is synchronized with the half-bridge oscillator. Therefore, at the valley point of the CT triangle wave, the CP pin ramp voltage starts. When the CP pin ramp voltage exceeds the DC pin output voltage, the capacitor connected to the CP pin is discharged. The resistor and capacitor connected to the DMAX pin control the maximum duty cycle, soft start function and half-bridge cut-off time.
9 Overcurrent Protection
The current value can be detected by the resistor connected to the CSI pin. When the CSI voltage is -500mV, the overcurrent protection circuit is triggered and the OUTP output is turned off. When an overcurrent occurs in the PFC input circuit, the capacitor on the DMAX pin is forced to discharge.
10 Power Factor Amplifier
To modulate the duty cycle of the PFC power switch, the rectified peak AC voltage and phase are detected by the PF amplifier. The power factor input is received through the PF pin. When the AC voltage reaches its peak and crosses zero, the PF pin input voltage is 1V and 0V respectively.
11 DC Error Amplifier
This circuit is used to provide negative feedback of the PFC DC output voltage. The DC output voltage of the PFC is input to the DC pin through a resistor divider and a filter network. The reference voltage of the DC error amplifier is VREF. The DC error amplifier output should be connected to a filter capacitor to eliminate switching noise.
12 Lamp Current Rectifier
The lamp current rectifier is used to provide negative feedback control of the average lamp current. The lamp current transformer (T2) and the load resistor convert the lamp current signal into a voltage, which is added to the L1 and L12 pins. The CRECT pin provides a full-wave rectified output. The external resistors and capacitors determine the gain and time constant of the circuit. The differential error amplifier compares the CRECT pin voltage with the internal 2/7 VREF reference voltage and adjusts the frequency of the half-bridge oscillator to minimize the error voltage and force the average lamp current to be constant.
Keywords:NE5565
Reference address:Explanation of NE5565 electronic ballast controller
The 7.42V reference voltage output from the VREF pin is used as the reference for the control logic voltage. Vcc is usually 12.7V. Before outputting VREF, Vcc must be at least 9.3V. In the range of 0-85℃, the accuracy of VREF is ±3.5%.
2 Lamp voltage regulator
Under conditions such as preheating, ignition and lamp shutdown, the maximum open-circuit voltage across the lamp load must be limited. During voltage regulation, the lamp voltage is controlled by the arc voltage of the lamp and is not controlled by the control circuit. When the VLAMP pin voltage exceeds VREF, the lamp voltage comparator detects the VLAMP pin voltage. During this period, the lamp voltage reaches the maximum allowable open-circuit voltage value, and the VLAMP voltage is reduced by the fast frequency increase circuit. The RXCX time constant determines the frequency deviation time of the startup circuit (ratio is 2:1).
3 Undervoltage lockout protection
When the PFC and half-bridge control circuit should be turned on or off, the protection circuit uses the Schmidt trigger to detect the DC power supply voltage at the Vcc pin and determine the upper and lower limit trip points of the power supply voltage. Before Vcc rises from zero volts to the upper voltage limit (11V), the PFC and half-bridge control circuits remain in the off state. Once Vcc exceeds the upper voltage limit, the PFC and half-bridge oscillator circuits start to work. When Vcc is lower than the lower voltage limit (10V), the PFC and half-bridge circuits are turned off. Before Vcc exceeds the upper trip point, the PFC and half-bridge oscillator are not allowed to work. The minimum delay is set by the components outside the DMAX pin.
4 Lamp startup and PFC overvoltage protection
The half-bridge undervoltage lockout circuit samples the DC output voltage of the PFC. Before the PFC output voltage reaches the set value (such as 400VDC), the undervoltage lockout circuit prohibits the lamp from igniting. When the OV pin input voltage exceeds 5/7 VREF, the inverter frequency shifts from the maximum value when the lamp is preheated to the lower frequency when the lamp is normally ignited, and the ignition procedure begins. The
overvoltage protection circuit prevents the PFC DC output voltage from exceeding the set value. When the voltage at the overvoltage comparator input pin OV is much higher than VREF, the PFC buffer gate drive output OUTP is turned off to prevent the PFC DC output voltage from increasing further. The overvoltage protection circuit only protects against overvoltage or overshoot generated by the PFC circuit, and cannot suppress transient voltages on the AC line.
5 Capacitive load protection
The capacitive load protection circuit is used to prevent the half-bridge power transistor from failing when the lamp is removed. When the frequency exceeds the resonant frequency of the half-bridge LC load network, the primary voltage will lead the primary current. The protection logic detects the phase relationship between the resonant current and the voltage of the LC network. The IPRIM pin input voltage is the primary current signal of the LC network. If the IPRIM pin voltage is higher than -100mV (positive), that is, when the gate drive signal is high, the system fails and the frequency of the half-bridge oscillator increases.
6 Half-bridge oscillator
The half-bridge oscillator is a triangle wave generator used to generate a square wave signal to drive the buffer circuit. The oscillation frequency is determined by the resistance and capacitance values of the RT and CT pins, and the CT pin voltage is a triangle wave voltage.
7 Output Buffer Driver
The output buffer is used as a level shifter to convert the low-level logic signals of the half-bridge oscillator and the pulse width modulator into a 10V drive signal to drive the two power switches of the external half-bridge circuit. The OUTH half-bridge buffer/driver circuit drives the external level shift circuit, which then drives the half-bridge power switch. The OUTP output can directly drive the MOSFET or the external level shift circuit combined with the power MOSFET.
8 Pulse Width Modulator
PWM control circuit is used to control the duty cycle of the PFC. The PWM frequency is determined by the half-bridge oscillator. The ramp voltage appears at the CP output pin and is synchronized with the half-bridge oscillator. Therefore, at the valley point of the CT triangle wave, the CP pin ramp voltage starts. When the CP pin ramp voltage exceeds the DC pin output voltage, the capacitor connected to the CP pin is discharged. The resistor and capacitor connected to the DMAX pin control the maximum duty cycle, soft start function and half-bridge cut-off time.
9 Overcurrent Protection
The current value can be detected by the resistor connected to the CSI pin. When the CSI voltage is -500mV, the overcurrent protection circuit is triggered and the OUTP output is turned off. When an overcurrent occurs in the PFC input circuit, the capacitor on the DMAX pin is forced to discharge.
10 Power Factor Amplifier
To modulate the duty cycle of the PFC power switch, the rectified peak AC voltage and phase are detected by the PF amplifier. The power factor input is received through the PF pin. When the AC voltage reaches its peak and crosses zero, the PF pin input voltage is 1V and 0V respectively.
11 DC Error Amplifier
This circuit is used to provide negative feedback of the PFC DC output voltage. The DC output voltage of the PFC is input to the DC pin through a resistor divider and a filter network. The reference voltage of the DC error amplifier is VREF. The DC error amplifier output should be connected to a filter capacitor to eliminate switching noise.
12 Lamp Current Rectifier
The lamp current rectifier is used to provide negative feedback control of the average lamp current. The lamp current transformer (T2) and the load resistor convert the lamp current signal into a voltage, which is added to the L1 and L12 pins. The CRECT pin provides a full-wave rectified output. The external resistors and capacitors determine the gain and time constant of the circuit. The differential error amplifier compares the CRECT pin voltage with the internal 2/7 VREF reference voltage and adjusts the frequency of the half-bridge oscillator to minimize the error voltage and force the average lamp current to be constant.
Previous article:Isolation method of high frequency switching power supply control circuit and drive circuit
Next article:Classification and working principle of switching power supply design
Recommended ReadingLatest update time:2024-11-16 16:00
MEMORY CONTROLLER
1. S3C6410 address space
For memory at the table details
2. SDRAM diagram
3. SDRAM chip capacity calculation: Number of L_BANKs * Number of cells in a L_BANK * Bit width of each cell
4. Complete the SDRAM controller initialization and SDRAM chip initialization according
[Microcontroller]
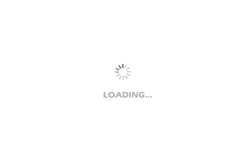
Recommended Content
Latest Power Management Articles
- MathWorks and NXP Collaborate to Launch Model-Based Design Toolbox for Battery Management Systems
- STMicroelectronics' advanced galvanically isolated gate driver STGAP3S provides flexible protection for IGBTs and SiC MOSFETs
- New diaphragm-free solid-state lithium battery technology is launched: the distance between the positive and negative electrodes is less than 0.000001 meters
- [“Source” Observe the Autumn Series] Application and testing of the next generation of semiconductor gallium oxide device photodetectors
- 采用自主设计封装,绝缘电阻显著提高!ROHM开发出更高电压xEV系统的SiC肖特基势垒二极管
- Will GaN replace SiC? PI's disruptive 1700V InnoMux2 is here to demonstrate
- From Isolation to the Third and a Half Generation: Understanding Naxinwei's Gate Driver IC in One Article
- The appeal of 48 V technology: importance, benefits and key factors in system-level applications
- Important breakthrough in recycling of used lithium-ion batteries
MoreSelected Circuit Diagrams
MorePopular Articles
- Innolux's intelligent steer-by-wire solution makes cars smarter and safer
- 8051 MCU - Parity Check
- How to efficiently balance the sensitivity of tactile sensing interfaces
- What should I do if the servo motor shakes? What causes the servo motor to shake quickly?
- 【Brushless Motor】Analysis of three-phase BLDC motor and sharing of two popular development boards
- Midea Industrial Technology's subsidiaries Clou Electronics and Hekang New Energy jointly appeared at the Munich Battery Energy Storage Exhibition and Solar Energy Exhibition
- Guoxin Sichen | Application of ferroelectric memory PB85RS2MC in power battery management, with a capacity of 2M
- Analysis of common faults of frequency converter
- In a head-on competition with Qualcomm, what kind of cockpit products has Intel come up with?
- Dalian Rongke's all-vanadium liquid flow battery energy storage equipment industrialization project has entered the sprint stage before production
MoreDaily News
- Allegro MicroSystems Introduces Advanced Magnetic and Inductive Position Sensing Solutions at Electronica 2024
- Car key in the left hand, liveness detection radar in the right hand, UWB is imperative for cars!
- After a decade of rapid development, domestic CIS has entered the market
- Aegis Dagger Battery + Thor EM-i Super Hybrid, Geely New Energy has thrown out two "king bombs"
- A brief discussion on functional safety - fault, error, and failure
- In the smart car 2.0 cycle, these core industry chains are facing major opportunities!
- The United States and Japan are developing new batteries. CATL faces challenges? How should China's new energy battery industry respond?
- Murata launches high-precision 6-axis inertial sensor for automobiles
- Ford patents pre-charge alarm to help save costs and respond to emergencies
- New real-time microcontroller system from Texas Instruments enables smarter processing in automotive and industrial applications
Guess you like
- 【GD32450I-EVAL】SPI transceiver and touch chip XPT2046 driver and pen interrupt
- Reading Notes on Operational Amplifier Parameter Analysis and LTspice Application Simulation Part 2 - Error Estimation
- 【Beijing】Recruiting embedded (video direction) R&D engineers
- UART interface algorithm transplantation encryption chip debugging skills - communication debugging
- Free sharing video - introduction to common electronic components such as resistors, capacitors and inductors------------The key is free
- MicroPython adds lightsleep() functionality to STM32
- Have you watched "Avengers 4"?
- TI CC2540 USB CDC Serial Port driver installation failure reasons and solutions
- TMS320DM642 learning connection method
- How to copy the files used in the compiler and IDE installation directory to the project folder when creating a new CCS project