1 High-voltage pulse power supply system structure
1.1 Topology of high-voltage pulse power supply The
commonly used main circuit topologies of high-voltage pulse power supplies can be summarized into two categories: capacitor charging and discharging type and two-stage type of high-voltage DC switching power supply plus pulse generation. The capacitor charging and discharging type achieves the purpose of energy compression and outputting high-voltage and high-power pulses by charging for a long time and discharging instantly, that is, by controlling the time ratio of charging and discharging. The advantage is that the output pulse power and voltage level are higher, and the pulse rising edge is steeper; however, the accuracy of the output pulse is difficult to control, and the repetition frequency is low, so the application range is relatively limited, mainly used in nuclear electromagnetic physics research, flue gas dust removal, sewage treatment, liquid sterilization and other occasions. The two-stage structure is a structure of a high-voltage DC switching power supply stage plus a pulse forming stage. This two-stage topology is adopted in this paper, and the power system structure block diagram is shown in Figure 1. The two-stage type has the characteristics of stable pulse, good controllability, high precision, and a large range of repetition frequency variation. Therefore, it has a wide range of applications and good versatility.
1.2 Power supply main circuit structure and working principle
The power supply main circuit schematic diagram is shown in Figure 2. The circuit consists of power frequency AC input, rectification and filtering, LCC series-parallel resonant converter, capacitor charging and energy storage, inductor buffer isolation, IGBT full-bridge inverter, pulse boost transformer and other units. Circuit working process: 220 V AC is rectified and filtered to obtain low-voltage DC output, which is charged to the energy storage capacitor C after high-frequency boost through LCC series-parallel resonant inverter, and bipolar pulse output is achieved through IGBT full-bridge inverter topology.
The LCC series-parallel resonant converter in Figure 2 is the core part of this high-voltage pulse power charging circuit. It consists of four power switch tubes IGBT and resonant inductor Ls, series resonant capacitor Cs, and parallel resonant capacitor Cp. The working principle is: using the effect of resonant elements such as inductors and capacitors to make the current or voltage waveform of the power switch tube into a sine wave, quasi-sine wave or partial sine wave, so that the power switch tube can be turned on or off under zero voltage or zero current conditions, reducing the loss when the switch tube is turned on and off, while increasing the switching frequency, reducing switching noise, and reducing EMI interference and switching stress.
When analyzing the LCC series-parallel resonant charging circuit, it is assumed that: 1) all switching devices and diodes are ideal devices; 2) the distributed capacitance of the transformer is 0; 3) n2C>>Cs; 4) the switching device works in a full soft switching state.
According to the relationship between the switching frequency fs and the basic resonant frequency fr, the LCC resonant converter has three working modes: 1) fs<0.5fr current discontinuous mode (DCM), the switch tube works in zero current/zero voltage shutdown and zero current turn-on state, and the anti-parallel diode is naturally turned on and turned off; 2) fr>fs>0.5fr current continuous mode (CCM), the switch tube is zero current/zero voltage shutdown and hard turn-on, the anti-parallel diode is naturally turned on, but the diode has reverse recovery current when turned off, and the circuit switching loss is large; 3) fs>fr is still the current continuous mode (CCM), the difference from 2) is that the switch tube is zero current/zero voltage turn-on and hard turn-off, and the circuit switching loss is also large. The resonant frequency is:
where Lr is the resonant inductor and is the resonant capacitor. Depending on the working conditions, it is jointly determined by the series capacitor Cs and the parallel capacitor Cp.
In this design, reasonable inverter design parameters are selected to make the LCC series-parallel resonant converter work in DCM mode, combined with soft switching technology to minimize the switching loss. 1.3 High-voltage pulse forming circuit
The formation of high-voltage pulses is to use the full-bridge topology structure composed of IGBT to switch the high voltage generated by the previous stage to achieve bipolar pulse output, as shown in Figure 2.
Switches Q5, Q7 and switches Q6, Q8 are turned on alternately in the positive and negative half cycles, respectively, to obtain bipolar pulse output. By changing the switching frequency of the two sets of switches, the frequency of the output bipolar pulse can be changed, and the duty cycle of the output pulse can be adjusted by controlling the on-time of the switch tube, so as to obtain a bipolar high-voltage pulse wave with adjustable pulse width and frequency.
1.4 Control of high-voltage pulse power supply The
control of the entire system is realized by
the
TMS320F2812
DSP chip and IGBT driver. It mainly realizes the soft switching of the LCC series-parallel resonant charging circuit through the constant on-time-constant frequency control method, reduces switching losses, and adjusts the output voltage; and uses the variable frequency and variable width control method to realize the output pulse control of the subsequent pulse forming circuit and the synchronous triggering of IGBT.
The TMS320F2812 development board integrates 16 12-bit A/D converters, two event manager modules, and a high-performance CPLD device XC95144XL. It can realize full digital control of the power system including overvoltage and overcurrent protection, and improve the accuracy and stability of the output voltage. And the control algorithm is implemented by software programming, making system upgrades and modifications more flexible and convenient.
1) Overvoltage protection
The voltage signal Ui is obtained by detecting the primary voltage of the pulse boost transformer through a high-frequency step-down transformer. Ui is used as the input voltage of the overvoltage protection circuit, and the output signal of the overvoltage protection circuit is connected to the pin of DSPF2812, which forces the system to restart and achieve the purpose of overvoltage protection, so as to protect the safety of the load.
2) Overcurrent protection
When the load current exceeds the set value or a short circuit occurs, the power supply itself needs to be protected. The overcurrent protection of the system plays an important role in the safety of the system. The overcurrent protection circuit is similar to the overvoltage protection circuit, as shown in Figure 4. The converted voltage signal is input to the F2812, the protection program is started, the fault latch is set, and the system is reset and restarted.
2 Circuit simulation analysis
Let k = Cp/Cs, Figure 5(a) shows the resonant current and voltage waveforms when k = 0.25. Select the DC bus voltage Vin = 300 V, switching frequency fs = 25 kHz, pulse width tw = 10μs, Lr = 50 μH, Cs = 0.2μF, resonant frequency kHz, that is, satisfy fs < 1/2fr, LCC series-parallel resonant converter works in DCM mode, and the high-frequency boost transformer ratio is 1:4. In the high-voltage pulse forming circuit, the pulse boost transformer ratio is 1:12, and the bipolar pulse simulation waveform is shown in Figure 5(b).
3 Conclusions
This paper designs a high-voltage pulse power supply based on IGBT, analyzes the various components and functions of the power supply, and generates a trigger signal to control the IGBT by DSP to achieve overvoltage and overcurrent protection, realize digital control of the power supply, and can accurately control the output pulse voltage, output pulse width, frequency and output pulse number, etc., and uses the LCC series-parallel resonant charging circuit as the structure for charging the intermediate energy storage capacitor, which is conducive to the rapid charging and miniaturization of the device.
Previous article:Thermal Analysis and Processing Design of Module Power Supply
Next article:Behavioral Simulation of Pipeline ADC
Recommended ReadingLatest update time:2024-11-16 20:46
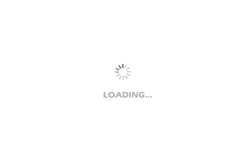
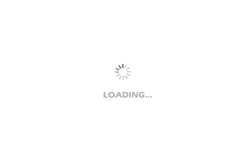
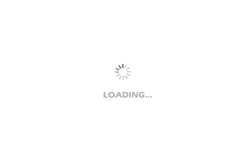
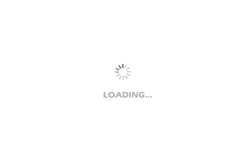
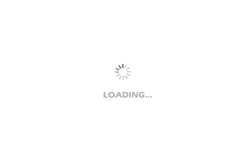
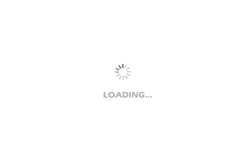
- Popular Resources
- Popular amplifiers
- MathWorks and NXP Collaborate to Launch Model-Based Design Toolbox for Battery Management Systems
- STMicroelectronics' advanced galvanically isolated gate driver STGAP3S provides flexible protection for IGBTs and SiC MOSFETs
- New diaphragm-free solid-state lithium battery technology is launched: the distance between the positive and negative electrodes is less than 0.000001 meters
- [“Source” Observe the Autumn Series] Application and testing of the next generation of semiconductor gallium oxide device photodetectors
- 采用自主设计封装,绝缘电阻显著提高!ROHM开发出更高电压xEV系统的SiC肖特基势垒二极管
- Will GaN replace SiC? PI's disruptive 1700V InnoMux2 is here to demonstrate
- From Isolation to the Third and a Half Generation: Understanding Naxinwei's Gate Driver IC in One Article
- The appeal of 48 V technology: importance, benefits and key factors in system-level applications
- Important breakthrough in recycling of used lithium-ion batteries
- Innolux's intelligent steer-by-wire solution makes cars smarter and safer
- 8051 MCU - Parity Check
- How to efficiently balance the sensitivity of tactile sensing interfaces
- What should I do if the servo motor shakes? What causes the servo motor to shake quickly?
- 【Brushless Motor】Analysis of three-phase BLDC motor and sharing of two popular development boards
- Midea Industrial Technology's subsidiaries Clou Electronics and Hekang New Energy jointly appeared at the Munich Battery Energy Storage Exhibition and Solar Energy Exhibition
- Guoxin Sichen | Application of ferroelectric memory PB85RS2MC in power battery management, with a capacity of 2M
- Analysis of common faults of frequency converter
- In a head-on competition with Qualcomm, what kind of cockpit products has Intel come up with?
- Dalian Rongke's all-vanadium liquid flow battery energy storage equipment industrialization project has entered the sprint stage before production
- Allegro MicroSystems Introduces Advanced Magnetic and Inductive Position Sensing Solutions at Electronica 2024
- Car key in the left hand, liveness detection radar in the right hand, UWB is imperative for cars!
- After a decade of rapid development, domestic CIS has entered the market
- Aegis Dagger Battery + Thor EM-i Super Hybrid, Geely New Energy has thrown out two "king bombs"
- A brief discussion on functional safety - fault, error, and failure
- In the smart car 2.0 cycle, these core industry chains are facing major opportunities!
- The United States and Japan are developing new batteries. CATL faces challenges? How should China's new energy battery industry respond?
- Murata launches high-precision 6-axis inertial sensor for automobiles
- Ford patents pre-charge alarm to help save costs and respond to emergencies
- New real-time microcontroller system from Texas Instruments enables smarter processing in automotive and industrial applications
- BQ24610 Intelligent Li-ion Battery Charging System
- Application of X-NUCLEO-IKS01A3 sensor based on STM32F401RE development board
- Research and Design of SDTVHDTV Conversion Based on FPGA
- esp32 makes an open source handheld game console
- Some questions about DC-DC2596
- To show your companionship, you will get twice the result. Tektronix’s universal lucky bags are being delivered. There are seven lucky bags for you to choose from!
- High frequency power resonant amplifier, how to adjust the optimal impedance
- Wireless technology comparison (ZigBee, UWB, Wi-Fi, Bluetooth, NFC)
- TouchGFX design" + online battery status monitoring
- MicroPyhton-NodeMcuEsp8266, driving ultrasonic detector-buzzer-OLED screen