1. Introduction
As a composite device, the insulated gate field effect transistor (IGBT) integrates the voltage drive and high switching frequency of MOSFET and the low loss and high power characteristics of power tube. It is widely used in motor control, switching power supply, converter and many fields requiring fast speed and low loss. This paper discusses the characteristics of IGBT used in active power filter and the design of its proprietary EXB84l driver, and proposes a driver circuit with perfect protection function.
In the design of active power filter, 4 IGBTs are used as switches, and 4 EXB841s form a drive circuit, the principle of which is shown in Figure 1. In the experiment, according to the relationship between the compensation current and the command current, the digital signal processor (DSP) controls the high and low levels of the PWM pin, and the drive circuit controls the on and off of the IGBT. The drive circuit also monitors overcurrent faults, and the DSP takes measures such as blocking the control signal and shutting down the machine.
2. Design of driving circuit
2.1 Drive circuit power supply
The drive circuit requires 4 mutually isolated DC power supplies to power the 4 IGBT drive circuits. The 4 AC power supplies are rectified separately with a 220V/22V transformer, and then stabilized with capacitors and a 78L24 voltage regulator to output 4 24V DC voltages, as shown in Figure 2.
2.2 Gate voltage
IGBT is usually driven by gate voltage, which has special requirements for the gate drive circuit.
The rise rate and fall rate of the voltage pulse should be large enough. When turned on, the steep gate voltage UGE can make the IGBT turn on quickly and reduce the conduction loss. When turned off, the gate drive circuit should provide the IGBT with a steep turn-off voltage and apply an appropriate reverse negative bias between the gate and the emitter to make the IGBT turn off quickly and reduce the turn-off loss. After the IGBT is turned on, the gate drive voltage and current should have enough width to ensure that the IGBT does not exit the saturation region and be damaged during instantaneous overload. The recommended value of the gate drive voltage is 15 V ± 1.5 V. This voltage value makes the IGBT fully saturated and turned on, and minimizes the conduction loss. Applying a negative turn-off bias can suppress the mis-conduction of the IGBT when du/dt appears between CE, and can also reduce the turn-off loss.
2.3 Gate resistor R1
The selection of gate resistor R1 has different degrees of influence on the on-state voltage, switching time, switching loss and short-circuit tolerance. When the gate resistance increases, the turn-on and turn-off time of the IGBT increases, thereby increasing the turn-on and turn-off losses. When the gate resistance decreases, it will cause di/dt to increase, causing mis-conduction of the IGBT. Therefore, the resistance value of R1 should be selected according to the current capacity and voltage rating of the IGBT and the switching frequency.
The value of Rl can be calculated using the following formula:
IC is the collector current of IGBT. As shown in Figure 3, R1 is usually between 10 ohms and several tens of ohms, and R2 is 30 Ω. Since IGBT is a voltage-controlled device, when high voltage is applied between collector and emitter, it is easily interfered by the outside world, and the voltage between gate and emitter exceeds a certain value, causing the device to be mis-conducted. In order to prevent this phenomenon from happening, a resistor R6 connected in parallel between gate and emitter can play a certain role. Generally, the resistance value of R6 is 1 000~5 000 times that of R2, and it should be connected in parallel at the nearest point between gate and emitter. Capacitors Cl and C2 in the circuit are used to suppress the supply voltage changes caused by the power supply wiring impedance, rather than for power supply filtering.
2.4 EXB841 driver link
The author used the EXB841 special IGBT driver module in the experiment, which has a maximum operating frequency of 40 kHz, and the input signal is isolated by an internal optocoupler. The optical isolation drive current is 10 mA, and the maximum delay is about 1 μs. The operating temperature range is -10℃~+85℃, and the power supply voltage is +20 V~+25 V. The author expanded the function of EXB841, and Figure 3 shows the drive link circuit.
The diode connected to the 6th pin of EXB841 can detect the saturation voltage drop of the IGBT to complete the overcurrent protection function. The overcurrent protection signal of the 4th pin is output with a delay of 10μs. When the IGBT has overcurrent, if UCE is greater than 7.5V, the internal overcurrent protection circuit starts to work and softly shuts down the IGBT. Usually, when the IGBT passes the rated current, UCE is 3.5 V. When UCE=7.5 V, the IGBT has overcurrent, and its value is about 3~5 times the rated current. However, since the protection threshold is not reached, the protection circuit does not work. If it works in this state for a long time, it will cause damage to the IGBT. In order to reliably protect the IGBT, the overcurrent protection threshold should be lowered. A voltage regulator can be connected in series between D1 and the collector of the IGBT, or several fast recovery diodes with the same specifications as D1 can be connected in series. As shown in Figure 3, the protection threshold is reduced to 4.2V by connecting an IN4728 3.3 V voltage regulator in series. When an IGBT overcurrent is detected, pin 5 becomes low level, the TPL521 optocoupler outputs a low level, blocks the control signal input through the AND gate, and simultaneously makes the 4-input NAND gate output a low level, triggering the power drive protection interrupt and completing the corresponding protection processing.
2.5 Isolation of the control part and the drive part
The control circuit is a weak current part and is very susceptible to interference; the drive circuit is directly connected to the external circuit and is a strong interference source; in order to achieve electromagnetic compatibility of the entire device, the control circuit part must be isolated from the drive part. In order to avoid interference from the common power supply to the control circuit, the control circuit and the drive circuit should be powered separately. The power supply voltage of EXB84l is +20 V, and the power supply voltage of the general control circuit is 5 V. Therefore, the DC-DC micro-power module shown in Figure 4 can be used for power isolation, and the A2405D micro-power module can be used to achieve power isolation.
3. Protection of IGBT and drive circuit
3.1 IGBT overvoltage protection
IGBT集-射极之间的瞬时过压会对IGBT造成损坏,笔者采用箝位式吸收电路对瞬时过电压进行抑制。当IGBT导通时,由于二极管的作用,电容器的电荷不会被放掉,电容器电压仍为电源电压。IGBT关断时,负载电流仍流过IGBT,直到IGBT集-射极之间电压达到电源电压,续流二极管导通。应用该电路,可以使杂散电感中的能量通过二极管转储到吸收电容器中,而IGBT的集电极电位被箝位在电容电压上,这样就可以抑制IGBT集电极的尖峰电压。吸收电容器的容值可以按公式(2)选取:
Where L is the lead inductance; i is the current when the IGBT is turned off; △U is the voltage overshoot on the absorption capacitor.
当吸收回路中的电容器电压高于直流侧电容器上的电压时,通过电阻器向直流侧电容器回送能量,一直到与直流侧电容器的电压相等。当IGBT关断时,线路电感在集电极和发射极二端产生很高的尖峰电压,加上箝位式吸收电路以后,UCE被箝位在电容器电压上,当UCE高于电容器电压时,线路电感的能量被转移到吸收电容器上,当尖峰电压过去以后,吸收电容高于主电容的那部分电压会由于能量回进而达到与主电容相等。这样就抑制了集-射极间的尖峰电压。吸收电容越大,吸收效果越好。由于吸收电容器上过
Most of the energy of the impulse is sent back to the DC side capacitor, thus reducing the power consumption of the resistor.
3.2 Eliminating du/dt between IGBT collector and gate
Figure 5 shows the schematic diagram of the connection circuit between EXB841 and the gate-emitter of the IGBT. When V4 in the drive circuit is turned on, the IGBT is in a normal conduction state. When V5 is turned on, a -5V voltage is applied to both ends of the gate-emitter of the IGBT through the voltage regulator VZ2, which turns off the IGBT. At this time, V5 is in a critical conduction state, and the voltage regulator VZ2 is in a reverse bias state. However, due to the influence of the distributed capacitance between the collector and the gate, when the du/dt between the collector and the gate increases, the current formed by the distributed capacitance passes through. Therefore, it is necessary to overcome the du/dt between the collector and the gate to ensure that the voltage regulator is not over-voltage and avoid mis-conduction of the IGBT. There are two ways to overcome du/dt: one is to use a twisted shielded cable with a grounded shielding layer for the connection between the output of the drive circuit and the gate-emitter of the IGBT; the other is to use a fast absorption circuit to absorb overvoltage.
3.3 EXB841 overcurrent protection function expansion
EXB841自身具有过流保护功能,其保护原理是利用IGBT的集电极通态饱和压降与集电极电流呈近似线性关系。当IGBT工作在正常状态时,EXB841的6脚电位箝制在8 V,内部保护不动作,当IGBT因承受过流而退出饱和状态时,IGBT集-射极间的电压上升很多,与EXB84l的6引脚相连的快速二极管截止,EXB841的6引脚被悬空,内部保护动作,输出驱动电压慢慢下降,实现IGBT的软关断。
In practical applications, it is not enough to effectively protect the IGBT by detecting the collector voltage of the IGBT through the 6-pin of EXB841 to achieve overcurrent protection. Therefore, it is necessary to add a Hall current sensor to the main circuit to detect overcurrent in the circuit, as shown in Figure 6. After the overcurrent occurs, the detection circuit detects the current, and if the signal still exists after a delay of 8μs, the drive signal is blocked to turn off the IGBT. In the figure, if the Hall current sensor detects an overcurrent signal in the main circuit, the PNP transistor will be turned on, and at the same time, the NPN transistor will be turned off, and the 6-pin of EXB841 will be suspended; when there is no overcurrent signal, the PNP transistor is not turned on, and the NPN transistor is turned on. At this time, the circuit is equivalent to the circuit before expansion.
4 Conclusion
This design uses the above circuit to drive and protect the IGBT. This drive circuit is improved and perfected on the basis of the typical drive circuit, and the isolation part and overcurrent protection extension part are designed by ourselves. This drive circuit is relatively simple and practical, has perfect protection capability for the driven IGBT, low output impedance, and strong anti-interference performance.
The prototype of the active filter using this IGBT module has passed the test, proving that the hardware can coordinate and cooperate, and the control effect is stable and accurate, and it has been mass-produced.
Previous article:A low power consumption design scheme for smart phones
Next article:Smartphone system architecture and low power design
Recommended ReadingLatest update time:2024-11-16 22:51
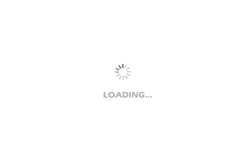
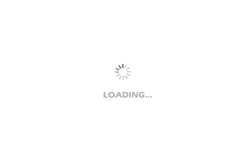
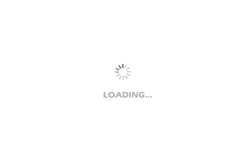
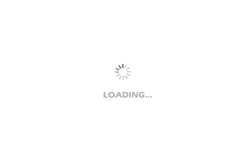
- Popular Resources
- Popular amplifiers
- MathWorks and NXP Collaborate to Launch Model-Based Design Toolbox for Battery Management Systems
- STMicroelectronics' advanced galvanically isolated gate driver STGAP3S provides flexible protection for IGBTs and SiC MOSFETs
- New diaphragm-free solid-state lithium battery technology is launched: the distance between the positive and negative electrodes is less than 0.000001 meters
- [“Source” Observe the Autumn Series] Application and testing of the next generation of semiconductor gallium oxide device photodetectors
- 采用自主设计封装,绝缘电阻显著提高!ROHM开发出更高电压xEV系统的SiC肖特基势垒二极管
- Will GaN replace SiC? PI's disruptive 1700V InnoMux2 is here to demonstrate
- From Isolation to the Third and a Half Generation: Understanding Naxinwei's Gate Driver IC in One Article
- The appeal of 48 V technology: importance, benefits and key factors in system-level applications
- Important breakthrough in recycling of used lithium-ion batteries
- Innolux's intelligent steer-by-wire solution makes cars smarter and safer
- 8051 MCU - Parity Check
- How to efficiently balance the sensitivity of tactile sensing interfaces
- What should I do if the servo motor shakes? What causes the servo motor to shake quickly?
- 【Brushless Motor】Analysis of three-phase BLDC motor and sharing of two popular development boards
- Midea Industrial Technology's subsidiaries Clou Electronics and Hekang New Energy jointly appeared at the Munich Battery Energy Storage Exhibition and Solar Energy Exhibition
- Guoxin Sichen | Application of ferroelectric memory PB85RS2MC in power battery management, with a capacity of 2M
- Analysis of common faults of frequency converter
- In a head-on competition with Qualcomm, what kind of cockpit products has Intel come up with?
- Dalian Rongke's all-vanadium liquid flow battery energy storage equipment industrialization project has entered the sprint stage before production
- Allegro MicroSystems Introduces Advanced Magnetic and Inductive Position Sensing Solutions at Electronica 2024
- Car key in the left hand, liveness detection radar in the right hand, UWB is imperative for cars!
- After a decade of rapid development, domestic CIS has entered the market
- Aegis Dagger Battery + Thor EM-i Super Hybrid, Geely New Energy has thrown out two "king bombs"
- A brief discussion on functional safety - fault, error, and failure
- In the smart car 2.0 cycle, these core industry chains are facing major opportunities!
- The United States and Japan are developing new batteries. CATL faces challenges? How should China's new energy battery industry respond?
- Murata launches high-precision 6-axis inertial sensor for automobiles
- Ford patents pre-charge alarm to help save costs and respond to emergencies
- New real-time microcontroller system from Texas Instruments enables smarter processing in automotive and industrial applications
- New typec interface M2 solid state drive box board 3 yuan a piece 10 pieces free shipping
- Real-time video processing set-top box.rar
- Three simple steps to operate the msp430 serial port interrupt
- 【Ufan Learning】How small is the Ufan learning board? ?
- [MicroPython] STM32 branch fixes a CDC problem when USB is reconnected
- Is Raspberry Pi considered open source hardware?
- How to debug with ST-Link in Embedded Studio for ARM?
- Comment to win a gift | TI SK-AM64 evaluation kit review
- I want to borrow a mm32f103 board
- Please help explain the principle of PWM2 generated in the following picture