For many central processing units (CPUs), the specification requires that the power supply must be able to provide large and fast charging output currents, especially when the processor changes operating modes. For example, in a 1V system, a 100 A/uS load transient may require the power supply voltage to be stabilized within 3%. The key to solving this problem is to realize that it is not just a power supply problem, the power distribution system is also an important factor, and it is difficult to strictly distinguish the two in a solution.
The implication of these high di/dt requirements is that the voltage source must have very low inductance. Rearranging the following equation and solving for the allowable source inductance gives:
The inductance during fast load current transients is only 0.3 nH. For comparison, a 0.1 inch (0.25 cm) wide board trace on a four-layer board has an inductance of about 0.7 nH/inch (0.3 nH/cm). The typical inductance of bond wires in IC packages is in the 1 nH range, and the inductance of printed circuit board vias is in the 0.2 nH range.
Additionally, there is a series inductance associated with the bypass capacitor, as shown in Figure 1. The top curve is the impedance of a 22 uF, X5R, 16V, 1210 ceramic capacitor mounted on a four-layer board. As we would expect (below 100 kHz), the impedance decreases with increasing frequency. However, there is a series inductance at 800 kHz, at which point the capacitor becomes inductive. This inductance (which can be calculated from the capacitor value and the resonant frequency) is 1.7 nH, which is much higher than our target value of 0.3 nH. Fortunately, you can use capacitors in parallel to reduce the effective ESL. The bottom curve in Figure 1 is the impedance of two capacitors in parallel. It is interesting that the resonance is slightly lower, indicating that the effective inductance is not exactly half. Based on the resonant frequency, the new inductance for the two capacitors in parallel is 1.0 nH or a 40% reduction in ESL, not a 50% reduction. This result can be attributed to two reasons: interconnect inductance and mutual inductance between the two capacitors.
Figure 1: Parallel capacitor impedance parasitic phenomenon attenuation effect
The size of the loop in the current path determines, to some extent, the parasitic inductance in the connected components, and the size of the component determines the area of the loop. The size-to-inductance correlation coefficient is shown in Table 1, which shows the capacitor inductance of various sizes of ceramic surface mount capacitors. Generally speaking, larger capacitors have greater inductance. This table does not include the inductance of the capacitor mounted on the board, which increased from 1 nH to 1.7 nH in our previous measurements. Another interesting point is that the location of the termination has a great impact on the inductance. The 0805 capacitor has terminations on the shorter side of the capacitor while the 0508 capacitor has terminations on the longer side. This almost splits the current path in half, greatly reducing the inductance. This changed structure reduces the inductance by one quarter.
Table 1 Ceramic SMT capacitor size affects parasitic inductance
Dimensions ESL (nH)
0603 0.6
0805 0.8
0508 0.2
1206 1.0
0612 0.2
1210 1.0
In summary, high di/dt loads require careful consideration of bypassing to maintain dynamic regulation of the supply. Surface mount capacitors need to be very close to the load to minimize their interconnection inductance. Capacitors have parasitic inductance that can prevent a lot of decoupling. Shunt capacitors to reduce this parasitic inductance are effective, but interconnect and mutual inductance reduce this effect. Using capacitors with shorter current paths is also effective. This can be implemented with smaller parts or parts with AC terminations that use shorter dimensions for current.
Please join us next time when we discuss high di/dt transient loads and their implications when designing and testing power supplies. We will then shift the focus from local bypassing to power supply design implications.
For more information on this and other power solutions, visit www.ti.com/power.
Previous article:Offset Voltage Design Based on MAX4080 Current-Sense Amplifier
Next article:Analyzing the benefits of remote power management for you
Recommended ReadingLatest update time:2024-11-16 15:51
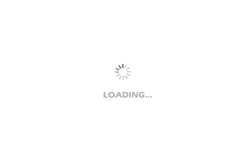
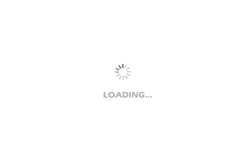
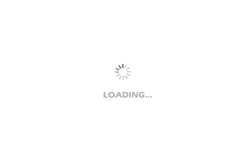
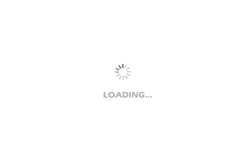
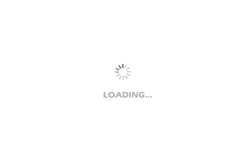
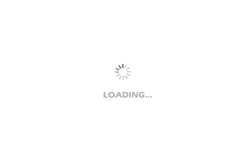
- MathWorks and NXP Collaborate to Launch Model-Based Design Toolbox for Battery Management Systems
- STMicroelectronics' advanced galvanically isolated gate driver STGAP3S provides flexible protection for IGBTs and SiC MOSFETs
- New diaphragm-free solid-state lithium battery technology is launched: the distance between the positive and negative electrodes is less than 0.000001 meters
- [“Source” Observe the Autumn Series] Application and testing of the next generation of semiconductor gallium oxide device photodetectors
- 采用自主设计封装,绝缘电阻显著提高!ROHM开发出更高电压xEV系统的SiC肖特基势垒二极管
- Will GaN replace SiC? PI's disruptive 1700V InnoMux2 is here to demonstrate
- From Isolation to the Third and a Half Generation: Understanding Naxinwei's Gate Driver IC in One Article
- The appeal of 48 V technology: importance, benefits and key factors in system-level applications
- Important breakthrough in recycling of used lithium-ion batteries
- Innolux's intelligent steer-by-wire solution makes cars smarter and safer
- 8051 MCU - Parity Check
- How to efficiently balance the sensitivity of tactile sensing interfaces
- What should I do if the servo motor shakes? What causes the servo motor to shake quickly?
- 【Brushless Motor】Analysis of three-phase BLDC motor and sharing of two popular development boards
- Midea Industrial Technology's subsidiaries Clou Electronics and Hekang New Energy jointly appeared at the Munich Battery Energy Storage Exhibition and Solar Energy Exhibition
- Guoxin Sichen | Application of ferroelectric memory PB85RS2MC in power battery management, with a capacity of 2M
- Analysis of common faults of frequency converter
- In a head-on competition with Qualcomm, what kind of cockpit products has Intel come up with?
- Dalian Rongke's all-vanadium liquid flow battery energy storage equipment industrialization project has entered the sprint stage before production
- Allegro MicroSystems Introduces Advanced Magnetic and Inductive Position Sensing Solutions at Electronica 2024
- Car key in the left hand, liveness detection radar in the right hand, UWB is imperative for cars!
- After a decade of rapid development, domestic CIS has entered the market
- Aegis Dagger Battery + Thor EM-i Super Hybrid, Geely New Energy has thrown out two "king bombs"
- A brief discussion on functional safety - fault, error, and failure
- In the smart car 2.0 cycle, these core industry chains are facing major opportunities!
- The United States and Japan are developing new batteries. CATL faces challenges? How should China's new energy battery industry respond?
- Murata launches high-precision 6-axis inertial sensor for automobiles
- Ford patents pre-charge alarm to help save costs and respond to emergencies
- New real-time microcontroller system from Texas Instruments enables smarter processing in automotive and industrial applications
- A feasible solution to the problem that the USB-Blaster driver cannot be successfully installed during the Quartus II 9 software installation and configuration
- The SGM42507 is a full-bridge driver designed for small motors and electromagnets.
- EEWORLD University ---- HVI Series: Design Considerations for High Power Density and High Efficiency Adapters
- MSP430Ware use notes to initialize XT1
- Open source program for automatic generation of dq current lookup table for permanent magnet synchronous motor of electric vehicle based on weak magnetic field lookup method
- What are the causes of IGBT damage in variable frequency power supply?
- Design and Application of Serial Communication Interface between TMS320F24x and PC
- A new interpretation of the principle of integral circuits: the transformation of amplifiers and capacitors
- Is there anyone who knows Mitsubishi PLC?
- Bidirectional 5V, 3.3V logic level conversion circuit