The structure of multilayer board:
In order to control the impedance of PCB well, we must first understand the structure of PCB:
The multilayer boards we usually refer to are made of core boards and prepregs laminated on each other. The core board is a hard, copper-clad board with a specific thickness on both sides, which is the basic material for printed circuit boards. The prepregs constitute the so-called wetting layer, which plays the role of bonding the core board. Although they also have a certain initial thickness, their thickness will change during the pressing process.
Usually, the two outermost dielectric layers of a multilayer board are both wetting layers, and a separate copper foil layer is used outside these two layers as the outer copper foil. The original thickness specifications of the outer copper foil and the inner copper foil are generally 0.5OZ, 1OZ, and 2OZ (1OZ is about 35um or 1.4mil), but after a series of surface treatments, the final thickness of the outer copper foil will generally increase by nearly 1OZ. The inner copper foil is the copper clad on both sides of the core board, and its final thickness is very close to the original thickness, but due to etching, it will generally be reduced by a few um.
The outermost layer of a multilayer board is the solder mask, which is what we often call "green oil". Of course, it can also be yellow or other colors. The thickness of the solder mask is generally not easy to accurately determine. The area without copper foil on the surface is slightly thicker than the area with copper foil. However, due to the lack of copper foil, the copper foil still appears more prominent, and we can feel it when we touch the surface of the printed circuit board with our fingers.
When making a printed circuit board of a certain thickness, on the one hand, it is required to reasonably select the parameters of various materials, and on the other hand, the final thickness of the prepreg will be smaller than the initial thickness. The following is a typical 6-layer stacking structure:
PCB parameters:
Different printed circuit board factories have slightly different PCB parameters. Through communication with the technical support of Shanghai Jiajietong Circuit Board Factory, we obtained some parameter data of the factory:
Surface copper foil:
There are three thicknesses of surface copper foil materials that can be used: 12um, 18um and 35um. The final thickness after processing is approximately 44um, 50um and 67um.
Core board: The board we commonly use is S1141A, standard FR-4, copper-clad on both sides. The optional specifications can be determined by contacting the manufacturer.
Prepreg:
The specifications (original thickness) are 7628 (0.185mm), 2116 (0.105mm), 1080 (0.075mm), 3313 (0.095mm). The actual thickness after pressing is usually about 10-15um smaller than the original value. Up to 3 prepregs can be used for the same wetting layer, and the thickness of the 3 prepregs cannot be the same. At least one prepreg can be used, but some manufacturers require at least two. If the thickness of the prepreg is not enough, the copper foil on both sides of the core board can be etched off, and then the two sides are bonded with prepregs, so that a thicker wetting layer can be achieved.
Solder Mask:
The thickness of the solder mask layer on the copper foil is C2≈8-10um, and the thickness of the solder mask layer C1 in the surface area without copper foil varies according to the surface copper thickness. When the surface copper thickness is 45um, C1≈13-15um, and when the surface copper thickness is 70um, C1≈17-18um.
Conductor cross section:
I used to think that the cross section of the wire was a rectangle, but it is actually a trapezoid. Take the TOP layer as an example. When the copper foil thickness is 1OZ, the upper base of the trapezoid is 1MIL shorter than the lower base. For example, if the line width is 5MIL, then its upper base is about 4MIL and the lower base is 5MIL. The difference between the upper and lower bases is related to the copper thickness. The following table shows the relationship between the upper and lower bases of the trapezoid under different conditions.
Dielectric constant: The dielectric constant of the prepreg is related to its thickness. The following table shows the thickness and dielectric constant parameters of prepregs of different models:
The dielectric constant of the board is related to the resin material used. The dielectric constant of FR4 board is 4.2-4.7, and it decreases with the increase of frequency.
Dielectric loss factor: The energy consumed by dielectric materials due to heat under the action of an alternating electric field is called dielectric loss, usually expressed as dielectric loss factor tanδ. The typical value of S1141A is 0.015.
The minimum line width and line spacing that can be ensured for processing is 4mil/4mil.
After we understand the structure of the multilayer board and master the required parameters, we can calculate the impedance through EDA software. You can use Allegro to calculate, but here I recommend another tool Polar SI9000, which is a good tool for calculating characteristic impedance. Now many printed circuit board factories are using this software.
Whether it is a differential line or a single-ended line, when calculating the characteristic impedance of the inner layer signal, you will find that there is only a slight difference between the calculation results of Polar SI9000 and Allegro, which is related to some details, such as the shape of the wire cross section. But if you are calculating the characteristic impedance of the surface signal, I suggest you choose the Coated model instead of the Surface model , because this type of model takes into account the existence of the solder mask, so the result will be more accurate. The following figure is a partial screenshot of the surface differential line impedance calculated by Polar SI9000 with the solder mask layer taken into account:
Since the thickness of the solder mask is difficult to control, you can also use an approximate method based on the board manufacturer's recommendations: subtract a specific value from the result calculated by the Surface model. I recommend subtracting 8 ohms from the differential impedance and 2 ohms from the single-ended impedance.
Previous article:Design of transceiver circuit for parametric transducer
Next article:Introduction to complete solar energy green energy-saving solutions
Recommended ReadingLatest update time:2024-11-16 15:42
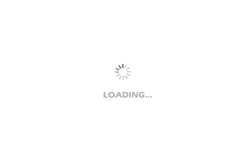
- MathWorks and NXP Collaborate to Launch Model-Based Design Toolbox for Battery Management Systems
- STMicroelectronics' advanced galvanically isolated gate driver STGAP3S provides flexible protection for IGBTs and SiC MOSFETs
- New diaphragm-free solid-state lithium battery technology is launched: the distance between the positive and negative electrodes is less than 0.000001 meters
- [“Source” Observe the Autumn Series] Application and testing of the next generation of semiconductor gallium oxide device photodetectors
- 采用自主设计封装,绝缘电阻显著提高!ROHM开发出更高电压xEV系统的SiC肖特基势垒二极管
- Will GaN replace SiC? PI's disruptive 1700V InnoMux2 is here to demonstrate
- From Isolation to the Third and a Half Generation: Understanding Naxinwei's Gate Driver IC in One Article
- The appeal of 48 V technology: importance, benefits and key factors in system-level applications
- Important breakthrough in recycling of used lithium-ion batteries
- Innolux's intelligent steer-by-wire solution makes cars smarter and safer
- 8051 MCU - Parity Check
- How to efficiently balance the sensitivity of tactile sensing interfaces
- What should I do if the servo motor shakes? What causes the servo motor to shake quickly?
- 【Brushless Motor】Analysis of three-phase BLDC motor and sharing of two popular development boards
- Midea Industrial Technology's subsidiaries Clou Electronics and Hekang New Energy jointly appeared at the Munich Battery Energy Storage Exhibition and Solar Energy Exhibition
- Guoxin Sichen | Application of ferroelectric memory PB85RS2MC in power battery management, with a capacity of 2M
- Analysis of common faults of frequency converter
- In a head-on competition with Qualcomm, what kind of cockpit products has Intel come up with?
- Dalian Rongke's all-vanadium liquid flow battery energy storage equipment industrialization project has entered the sprint stage before production
- Allegro MicroSystems Introduces Advanced Magnetic and Inductive Position Sensing Solutions at Electronica 2024
- Car key in the left hand, liveness detection radar in the right hand, UWB is imperative for cars!
- After a decade of rapid development, domestic CIS has entered the market
- Aegis Dagger Battery + Thor EM-i Super Hybrid, Geely New Energy has thrown out two "king bombs"
- A brief discussion on functional safety - fault, error, and failure
- In the smart car 2.0 cycle, these core industry chains are facing major opportunities!
- The United States and Japan are developing new batteries. CATL faces challenges? How should China's new energy battery industry respond?
- Murata launches high-precision 6-axis inertial sensor for automobiles
- Ford patents pre-charge alarm to help save costs and respond to emergencies
- New real-time microcontroller system from Texas Instruments enables smarter processing in automotive and industrial applications
- What kind of operation circuit is U2?
- Those who want to learn ROS system should read this (video teaching materials are updated continuously...)
- A large number of books have been released after graduation, including C/C++, Linux, algorithms, and other books. They are on sale now. Only 3 days left
- IWR1642Boost people counting DEMO program operation process
- I would like to ask the experts to introduce the generation of 2HZ in detail. Now the buzzer circuit 2HZ does not work! ! ! ! ! !
- Why doesn't the CPU top cover use silver, which has better heat dissipation?
- Summary of low power consumption STM32L151+RTC wake-up application
- LLC design information collection (for learning only)
- Do the read and write registers of the ds2438 coulomb meter have a lifespan?
- Raspberry Pi based smartphone