Power MOSFET has the advantages of low on-resistance and large load current, so it is very suitable for use as a rectifier component of a switching power supply (SMPS). However, there are some precautions when selecting MOSFET.
Unlike bipolar transistors, power MOSFETs have a relatively large gate capacitance, which must be charged before turning on. When the capacitor voltage exceeds the threshold voltage (VGS-TH), the MOSFET starts to turn on. Therefore, the gate driver's load capacity must be large enough to ensure that the equivalent gate capacitance (CEI) is charged within the time required by the system.
One of the most common mistakes when calculating gate drive current is to confuse the MOSFET's input capacitance (CISS) with CEI, and then use the following formula to calculate the peak gate current.
I = C (dv/dt)
In fact, the value of CEI is much higher than CISS and must be calculated based on the gate charge (QG) indicator provided by the MOSFET manufacturer.
QG is the portion of the MOSFET gate capacitance that is calculated as follows:
QG = QGS + QGD + QOD
in:
QG--Total gate charge
QGS - Gate-Source Charge
QGD--gate-drain charge (Miller)
QOD - Miller capacitor overcharge after full charge
A typical MOSFET curve is shown in Figure 1, and many MOSFET manufacturers provide this curve. It can be seen that in order to ensure that the MOSFET is turned on, the VGS used to charge CGS must be higher than the rated value, and CGS must also be higher than VTH. The gate charge divided by VGS equals CEI, and the gate charge divided by the on-time equals the required drive current (turn on within the specified time).
The formula is as follows:
QG = (CEI)(VGS)
IG = QG/tON
in:
● QG Total gate charge, same definition as above.
● CEI equivalent gate capacitance
● VGS voltage between the electrode and the source
● IG is the gate drive current required to turn on the MOSFET within the specified time
Figure 1
In the past, the driver was directly integrated into the SMPS controller, which is very practical for some products. However, since the output peak current of this driver is generally less than 1A, its application range is relatively limited. In addition, the heat generated by the driver will also cause the voltage reference to drift.
As the market calls for "intelligent" power devices become increasingly strong, people have developed SMPS controllers with more complete functions. These new controllers all use sophisticated CMOS technology, with a supply voltage lower than 12V, and the integrated MOSFET driver can also be used as a level converter to convert TTL levels to MOSFET drive levels. Taking TC4427A as an example, the device's input voltage range (VIL = 0.8V, VIH = 2.4V) and output voltage range (equal to the maximum supply voltage, up to 18V) meet the requirements of end-to-end (rail-to-rail) output.
Anti-latch capability is a very important indicator, because MOSFET is generally connected to an inductive circuit, which will generate a relatively strong reverse impact current. The output end of the TC4427 MOSFET driver can withstand a reverse current of up to 0.5A without damage, and the performance is not affected at all.
Another issue that needs attention is the ability to withstand instantaneous short-circuit current, especially for high-frequency SMPS. The generation of instantaneous short-circuit current is usually due to the fact that the rise or fall process of the driving level pulse is too long, or the transmission delay is too large. At this time, the MOSFETs on the high-voltage side and the low-voltage side are in the state of simultaneous conduction for a very short time, forming a short circuit between the power supply and the ground. The instantaneous short-circuit current will significantly reduce the efficiency of the power supply. Using a dedicated MOSFET driver can improve this problem in two ways:
1. The rise time and fall time of the MOSFET gate drive level must be equal and as short as possible. When the TC4427 driver is equipped with a 1000pF load, the pulse rise time tR and fall time tF are about 25ns. These two indicators of some other drivers with higher output peak current can be even shorter.
Figure 2
2. The propagation delay of the drive pulse must be very short (matching the switching frequency) to ensure that the MOSFETs on the high-voltage side and the low-voltage side have equal turn-on delay and cut-off delay. For example, the propagation delay of the pulse rising edge and falling edge of the TC4427A driver is less than 2ns (as shown in Figure 2). These two indicators will vary with voltage and temperature. Microchip's products have already taken the lead in this indicator (comparable products have this indicator at least 4 times larger, and the driver integrated in the SMPS controller has this indicator is even worse).
These issues (which are directly related to cost and reliability) have been relatively well handled in stand-alone, dedicated drivers, but not in integrated devices or traditional discrete device circuits.
Typical Applications
Portable Computer Power Supply
Figure 3 shows a high-efficiency synchronous boost converter circuit with an input voltage range of 5V to 30V. It can be connected to an AC/DC rectifier (14V/30V) or powered by a battery (7.2V to 10.8V).
Figure 3
The TC1411N in Figure 3 is a low-voltage side driver with an output peak current of 1A. Since it uses a +5V power supply, it can reduce the cut-off delay caused by gate overcharge. The TC4431 is a high-voltage side driver with an output peak current of up to 1.5A. The MOSFET driven by these two devices can withstand a drain current of 10A for 30ns.
Desktop computer power supply
Figure 4 shows a power supply circuit for a desktop computer, in which a synchronous buck converter is generally used to power the CPU, and its output current is generally not less than 6 A. This circuit can provide an adjustable voltage, which is not possible with the currently common discrete device power supply.
The circuit in Figure 4 is simpler than that in Figure 3. TC4428A is used as the driver for the high-voltage side and the low-voltage side, and shares the power supply VDD. In order to reduce the cost, N-channel MOSFET is used in the circuit. TC4428A has a strong output capability, and it can drive MOSFET to withstand a drain current of 10A for 25ns.
Figure 4
Power MOSFET has become the best choice of switch components in SMPS controllers with its outstanding advantages of low on-resistance and large load current. The emergence of dedicated MOSFET drivers has brought opportunities for optimizing SMPS controllers. Drivers integrated with SMPS controllers are only suitable for products with simple circuits and small output currents; and those drive circuits built with discrete active or passive devices can neither meet the requirements for high performance nor obtain the cost advantages of dedicated monolithic driver devices. The pulse rise delay, fall delay and propagation delay of dedicated drivers are very short, and the circuit types are also very complete, which can meet the design needs of various products.
Previous article:Detailed explanation of high-power MOSFET driving technology
Next article:Supercapacitor-based backup power prevents data loss in RAID systems
Recommended ReadingLatest update time:2024-11-17 01:58
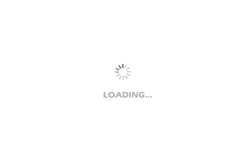
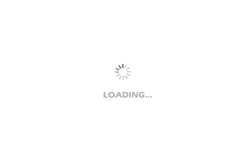
- Popular Resources
- Popular amplifiers
-
Siemens Motion Control Technology and Engineering Applications (Tongxue, edited by Wu Xiaojun)
-
Modern Product Design Guide
-
Modern arc welding power supply and its control
-
Small AC Servo Motor Control Circuit Design (by Masaru Ishijima; translated by Xue Liang and Zhu Jianjun, by Masaru Ishijima, Xue Liang, and Zhu Jianjun)
- MathWorks and NXP Collaborate to Launch Model-Based Design Toolbox for Battery Management Systems
- STMicroelectronics' advanced galvanically isolated gate driver STGAP3S provides flexible protection for IGBTs and SiC MOSFETs
- New diaphragm-free solid-state lithium battery technology is launched: the distance between the positive and negative electrodes is less than 0.000001 meters
- [“Source” Observe the Autumn Series] Application and testing of the next generation of semiconductor gallium oxide device photodetectors
- 采用自主设计封装,绝缘电阻显著提高!ROHM开发出更高电压xEV系统的SiC肖特基势垒二极管
- Will GaN replace SiC? PI's disruptive 1700V InnoMux2 is here to demonstrate
- From Isolation to the Third and a Half Generation: Understanding Naxinwei's Gate Driver IC in One Article
- The appeal of 48 V technology: importance, benefits and key factors in system-level applications
- Important breakthrough in recycling of used lithium-ion batteries
- Innolux's intelligent steer-by-wire solution makes cars smarter and safer
- 8051 MCU - Parity Check
- How to efficiently balance the sensitivity of tactile sensing interfaces
- What should I do if the servo motor shakes? What causes the servo motor to shake quickly?
- 【Brushless Motor】Analysis of three-phase BLDC motor and sharing of two popular development boards
- Midea Industrial Technology's subsidiaries Clou Electronics and Hekang New Energy jointly appeared at the Munich Battery Energy Storage Exhibition and Solar Energy Exhibition
- Guoxin Sichen | Application of ferroelectric memory PB85RS2MC in power battery management, with a capacity of 2M
- Analysis of common faults of frequency converter
- In a head-on competition with Qualcomm, what kind of cockpit products has Intel come up with?
- Dalian Rongke's all-vanadium liquid flow battery energy storage equipment industrialization project has entered the sprint stage before production
- Allegro MicroSystems Introduces Advanced Magnetic and Inductive Position Sensing Solutions at Electronica 2024
- Car key in the left hand, liveness detection radar in the right hand, UWB is imperative for cars!
- After a decade of rapid development, domestic CIS has entered the market
- Aegis Dagger Battery + Thor EM-i Super Hybrid, Geely New Energy has thrown out two "king bombs"
- A brief discussion on functional safety - fault, error, and failure
- In the smart car 2.0 cycle, these core industry chains are facing major opportunities!
- Rambus Launches Industry's First HBM 4 Controller IP: What Are the Technical Details Behind It?
- The United States and Japan are developing new batteries. CATL faces challenges? How should China's new energy battery industry respond?
- Murata launches high-precision 6-axis inertial sensor for automobiles
- Ford patents pre-charge alarm to help save costs and respond to emergencies
- RISC-V MCU Development (V): Debug Configuration
- I want to ask about the difference between EL357 and LTV354, two optocouplers.
- Playing with Zynq Serial 39——[ex58] XADC acquisition control example based on Zynq
- [AD21] How to solve the error Board Clearance Constraint
- Read the good book "Operational Amplifier Parameter Analysis and LTspice Application Simulation" + Reading to learn about amplifiers
- Can anyone make a 433M remote control?
- 【DFRobot Wireless Communication Module】+ DFRobot Gravity: UART A6 GSM & GPRS Wireless Communication Module Review
- Creative PCB display
- LPC2478 Timer 2 and Timer 3 enable
- Design and implementation of optical transceiver UART interface based on FPGA.pdf