Analog Core Insight | Power Factor Correction Using Peak Current Mode Control
Click on the blue words to follow us



Welcome to Analog Core Vision

In the previous issue, we introduced three different control architectures to achieve 1mV output voltage ripple and provided test data using the same electrical specifications and comparison results of output voltage ripple, solution size, load transient, and efficiency.
In this issue, we bring you "Power Factor Correction Using Peak Current Mode Control" , we will explore in depth a new way to control PFC and achieve unity power factor - a special peak current mode. This method does not require a current sampling resistor, thus eliminating power loss. Although it still uses a current transformer to detect the switch current, it does not need to be sampled in the middle of the PWM on time, thus avoiding the sampling position offset problem. There are other benefits besides this.

introduction
When dealing with power levels above 75W, offline power supplies require power factor correction (PFC). The goal of PFC is to control the input current to follow the input voltage so that the load looks like a pure resistor . For a sinusoidal AC input voltage, the input current also needs to be sinusoidal. To control the input current, it must be sensed.
Designers typically use one of two current sensing methods in PFC applications. The first method places a current sensing resistor (designated as R1 in Figure 1) in the PFC ground return to sense the input current, which is fed to the average current mode controller (shown in Figure 2) to force the input current to follow the input voltage. Since the current sensing resistor senses the entire boost inductor current, this current sensing method provides good power factor and reduces total harmonic distortion (THD). However, the current sensing resistor results in additional power loss, which can be a problem in applications that require high efficiency.

Figure 1. Common current sensing methods for PFC

Figure 2. Conventional average current mode control of PFC
The second method is to place a current transformer in series with the boost switch to sense the switch current (designated as CT and R2 in Figure 1). This method is best used when a current sensing resistor cannot be used (for example, for interleaved PFC and semi-bridgeless PFC). The current transformer only senses the switch current (I Q ) (not the full inductor current), so to control the full inductor current, a simple solution is to sample in the middle of the current transformer output (the middle of the pulse-width modulation [PWM] on-time). Sampling works because the midpoint instantaneous current value is equal to the average inductor current value in continuous conduction mode (CCM) (as shown in Figure 3). This method has less power loss than the first method, but it also has limitations: The duty cycle of PFC varies between 0% and 100%. When the duty cycle is small, the PWM on-time is short; therefore, it is difficult to accurately sample in the middle of the PWM on-time. Any sampling position offset will cause feedback signal errors and deteriorate THD and power factor.

Figure 3. PFC inductor current waveform in CCM
This document introduces a new method to control PFC and achieve unity power factor - a special peak current mode. This method does not require a current sampling resistor, thus eliminating power loss. Although it still uses a current transformer to sense the switch current, it does not need to sample in the middle of the PWM on time, thus avoiding the sampling position offset problem. There are other benefits besides this.
Peak Current Mode Control of CCM PFC
Peak current mode control is widely used in DC/DC converters, but it is not suitable for PFC because PFC needs to control the average current instead of the peak current. Controlling the inductor peak current will result in poor THD and low power factor.
By using a special PWM generator (as shown in Figure 4), PFC can achieve peak current mode control. Figure 4 compares the sensed switch current I Q with a sawtooth wave. The sawtooth peak voltage (V RAMP ) starts at the beginning of each switching cycle, and its amplitude decreases linearly to 0V at the end of the switching cycle. The boost switch (Q) is turned on at the beginning of the switching cycle. When I Q exceeds the sawtooth wave, Q turns off.
This PWM generator is already present in almost all digital power controllers, such as TI's C2000™ real-time microcontrollers and UCD3138. These digital controllers have a peak current mode control block with programmable slope compensation. Programming the compensation with slope V RAMP /T generates the desired sawtooth wave.

Figure 4. PWM waveform generation of the proposed method in CCM
To achieve unity power factor, the peak value of the sawtooth wave VRAMP can be calculated using Equation 1 :

Equation 1
Where Gv is the voltage loop output, Vout is the PFC output voltage, L is the inductance of the boost inductor, R is the current sense resistor at the output of the current transformer, and Ton is the PFC PWM on-time.
Since the PWM on-time is almost the same in two consecutive switching cycles, you can use the T on information from the previous switching cycle to calculate the V RAMP value for this switching cycle.
Learn how to achieve unity power factor using this control method. From Figure 3, we can see that during the T on time, the input voltage is applied to the inductor, causing the inductor current to rise from I 1 to I 2 . Using Equation 2:

Equation 2
Where Vin is the PFC input voltage. Equation 3 calculates the average inductor current in each switching cycle:

Equation 3
Substituting Equation 2 into Equation 3 yields Equation 4:

Equation 4
From Figure 4, Equation 5 is:

Equation 5
Equation 6 applies to the PFC operating in CCM steady state:

Equation 6
Substituting Equation 6 into Equation 5 and solving for I 2 yields Equation 7:

Equation 7
Substituting Equation 1 and Equation 7 into Equation 4 yields Equation 8:

Equation 8
In Equation 8, Gv is the PFC voltage loop output. It is constant in steady state; therefore, Iavg is proportional to Vin and follows the shape of Vin. If Vin is a sine wave, then Iavg is also a sine wave. Controlling the inductor peak current can achieve unity power factor.
Compared to conventional average current mode control, this method eliminates the power loss caused by the current sampling resistor. Compared to the current transformer detection method that requires precise sampling position, this method does not require current sampling. The analog comparator determines the PWM turn-off instant, thus avoiding the sampling offset problem.
To save system cost, some designers prefer to use a combination control, where a single controller controls both the PFC and the DC/DC controller. You can place the combination controller on the primary or secondary side of the AC/DC power supply; each side has its advantages and disadvantages. If you choose to place the combination controller on the primary side, the DC/DC output voltage and current information needs to be sent across the isolation boundary to the primary side, and the communication between the controller and the host also needs to cross the isolation boundary. If you choose to place the combination controller on the secondary side, because the traditional average current mode control method requires input AC voltage information, the input voltage must be sensed and used to modulate the current loop reference. Sensing the input voltage across the isolation boundary is challenging.
In the new control method, Equation 1 includes only V out and not V in . Because there is no need to detect V in , the V in detection circuit can be removed. This control method only requires the current transformer output and V out information. Since the current transformer provides isolation, a low-cost optocoupler can detect V out and send it to the secondary side. Then, you can place the PFC controller on the secondary side of the AC/DC power supply and combine it with a DC/DC controller also on the secondary side to build a combined controller, greatly reducing system cost.
Peak Current Mode Control for DCM PFC
You can extend the same algorithm to discontinuous conduction mode (DCM) operation. Figure 5 shows the inductor current waveform in DCM. The inductor current drops to zero at the end of T off and remains zero for the rest of T dcm ; therefore, T = T on + T off + T dcm . The PWM waveform generator is the same as Figure 4, but the PWM off time is T off + T dcm instead of T off (as shown in Figure 6).

Figure 5. PFC inductor current waveform in DCM

Figure 6. PWM waveform generation of the proposed method in DCM
Rewriting Equation 4 as Equation 9 calculates the average current in DCM during one switching cycle:

Equation 9
In steady state, the inductor volt-seconds must be balanced during each switching cycle, resulting in Equation 10:

Equation 10
Solving for T off and substituting into Equation 9 yields Equation 11:

Equation 11
From Equation 6, Equation 12 is:

Equation 12
Equation 13 calculates the peak value of the sawtooth wave V ramp :

Equation 13
Substituting Equation 13 into Equation 12 and solving for I 2 yields Equation 14:

Equation 14
Substituting I 2 into Equation 11 yields Equation 15:

Equation 15
In Equation 15, Gv is constant in steady state; therefore, Iavg is proportional to Vin and follows the shape of Vin . If Vin is a sine wave, then Iavg is also a sine wave, achieving unity power factor.
Equation 9 to Equation 15 are valid for both CCM and DCM, so if the sawtooth signal peak is generated according to Equation 13, unity power factor can be achieved for both CCM and DCM.
Equation 1 is a special case of Equation 13, where T = T on + T off . For applications with light loads (PFC is in DCM at light loads), where THD and power factor are not critical, Equation 1 can be used to simplify the implementation.
Test Results
The proposed control method has been verified on a 360W PFC Evaluation Module (EVM). Figure 7 shows the input current waveform, where a good sinusoidal current waveform can be seen.
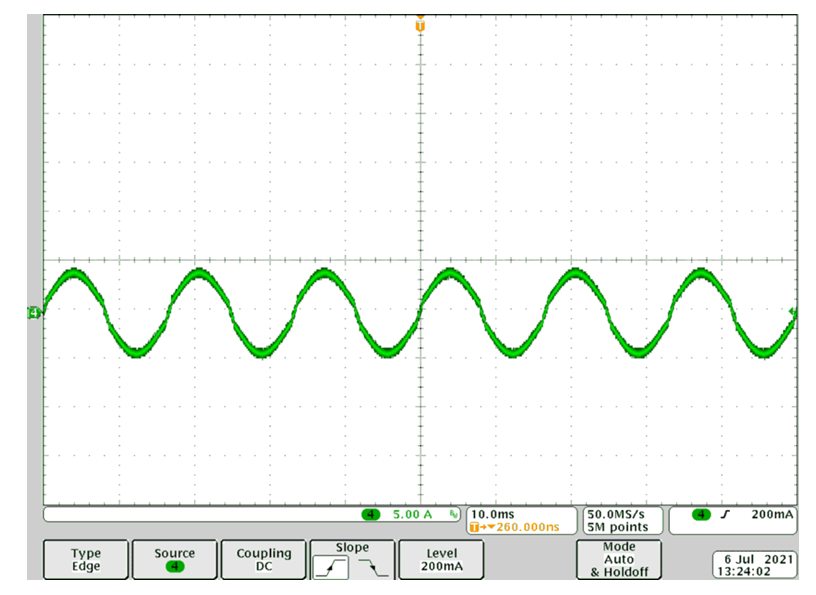
Figure 7. Test results on 360W PFC EVM
in conclusion
This new PFC peak current mode control method has many advantages over the traditional average current mode control method. Building a combined controller with a DC/DC controller by placing the PFC controller on the secondary side of the AC/DC power supply can reduce costs. Eliminating the current shunt resistor eliminates power losses, thereby improving efficiency. When using a current transformer, THD can be improved by eliminating the feedback signal error caused by the small PWM duty cycle. Finally, this control method can be easily implemented with existing digital power controllers such as the C2000 MCU and UCD3138.
Click Read original article
Read the e-version of Analog Design Journal now to unlock more relevant knowledge!