TI Chip Technology Empowers China's New Infrastructure - Intercity Rail Transit: The "Chips" of Speed
Intercity trains are only slightly different in appearance from high-speed trains. However, as intercity transportation becomes more like public transportation, with higher operating frequencies and more boarding and alighting stations, this means that more reconnections and reorganizations are required, which places and ensures that the train communication network is accurate and efficient. On the other hand, as the speed of high-speed trains has basically met demand, people are more concerned about the comfort and entertainment of riding, and technologies such as wireless charging, massage chairs, and even projection will be used in trains. These new development directions require the support of new technologies, and big data analysis, artificial intelligence, wireless sensors, Ethernet, etc. will be increasingly introduced into rail transit facilities.
Since the birth of the first electric locomotive in 1879, power electronics have been on the scene, initially mainly to help achieve faster train speeds and greater loading capacity. A series of innovations in rail transit since then have been inseparable from chips . Today, chips play an important role in applications such as track sensing and monitoring, auxiliary power supplies, electric propulsion, information systems, control management, and trackside signaling and control . According to the estimate of Leo Chen, regional sales manager of Texas Instruments (TI), a complete high-speed train will contain up to 200,000 chips, of which TI chips alone will account for tens of thousands.
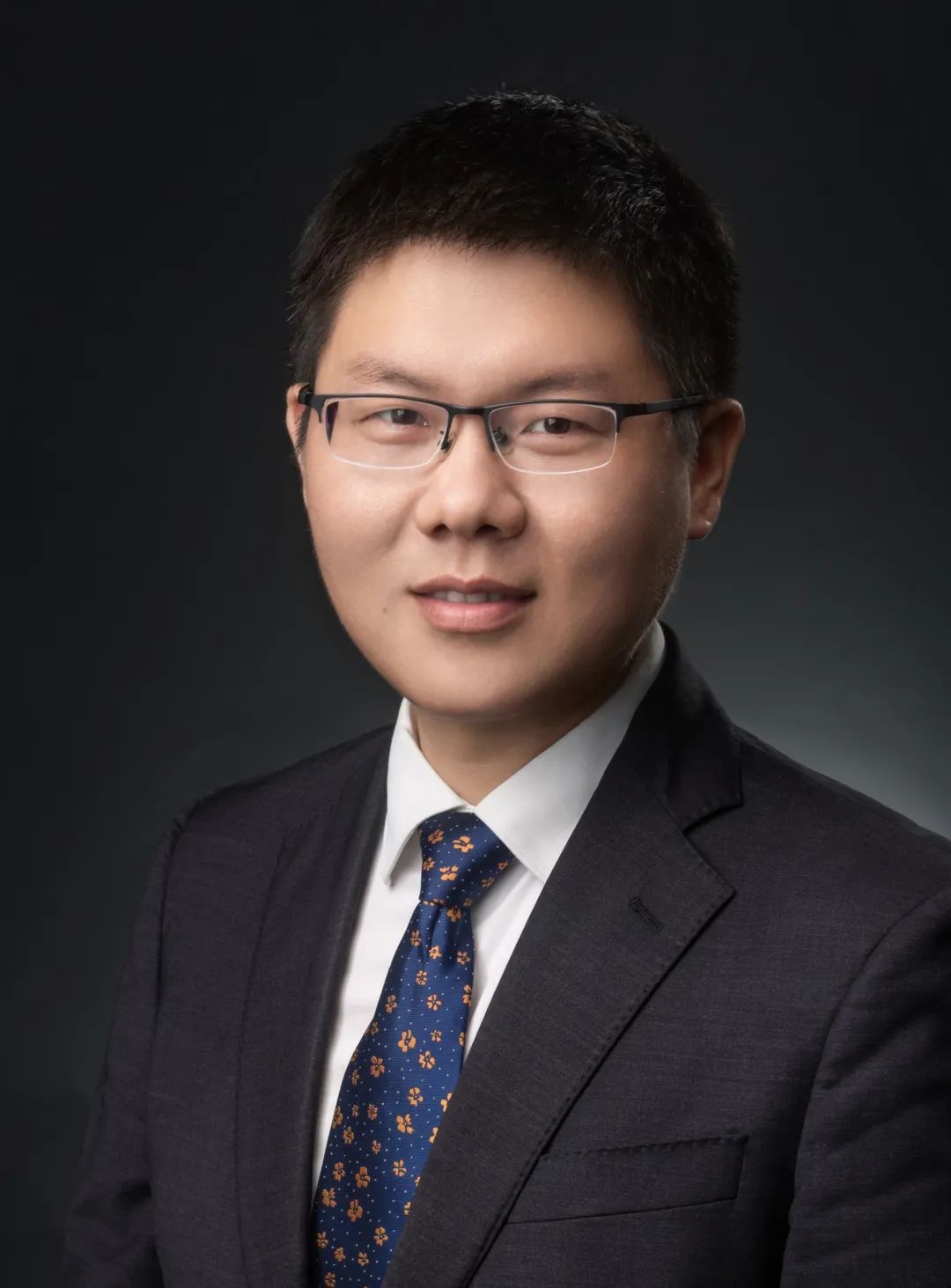
Leo Chen, Regional Sales Manager, Texas Instruments
Challenges on the road to autonomy
When China first entered the high-speed rail industry in 2008, it took the same path of trade, industry and technology as many other fields, importing equipment from abroad and assembling and producing it domestically. Ten years later, the "Fuxing" with completely independent intellectual property rights is designed entirely with independent standards, and more than 90% of the basic components have been completely localized. The future development of high-speed rail cannot avoid two major difficulties (also the focus) - complexity and reliability.
my country has a vast territory. A train must run safely in the snowy northeast and the humid south. It must meet the high altitude of Tibet and the dry and hot climate of Xinjiang. Such a complex application environment makes system design more complicated. The extreme climate and geographical differences require chip manufacturers to provide products with greater versatility, temperature resistance and reliability.
There is no similar application environment in the world, and due to the narrow industry, there are few players, and designers need to continuously upgrade and iterate based on demand. This means that China's high-speed rail research and development has entered a "no man's land". No one has done it before, and no one knows how to do it after. To cross the high-tech no man's land, partners in the chip field are needed to move forward together, but the requirements for partners are higher than in other industries. Chip and solution suppliers need to have good system know-how and be able to provide complete systems and perfect technical support. At the same time, due to the long life cycle, products need to have consistency and continuous and stable supply capabilities, and they must also meet the requirements of the next 8 to 10 years.
Fortunately, the road to independence is not all about loneliness and coldness. In the mid-1990s, China's first domestically produced electric locomotive drive circuit board used TI's C2000™ controller. The C2000 processor, which was mass-produced in the 1980s, is still serving China's rail transit industry today. TI has always been committed to helping Chinese customers solve difficulties and challenges in design.
Simple pursuit
The design complexity caused by the vastly different application scenarios and different application requirements requires suppliers to provide flexible solutions. Taking digital power supply as an example, there are many types of electrical equipment in high-speed rail, and different types of loads have different requirements for power supply solutions. TI's C2000 digital power supply products can support any control mode and loop topology design, and support different switching frequencies, so that customers can use one platform to cover the design of diverse and complex circuits.
At the same time, C2000 also has real-time processing features and complete power monitoring and protection functions. The next generation C2000 also meets the functional safety features of SIL-D, thereby simplifying complex safety design process requirements. TI's processor integrates high-performance Arm® cores and DSPs, which can meet complex computing and control requirements on a single chip. It also supports multi-protocol communication interfaces to achieve highly reliable interconnection.
The most secure protection
As we all know, the service life of the railway system is as long as several decades, so each link has high requirements for reliability. As for the power system, the power voltage in the train is very high. The DC voltage obtained from the pantograph is about 1500 volts, and then there are a series of different voltages such as AC 380 volts and DC 110 volts. Therefore, in order to avoid the chip from being broken down and burned, and to ensure the high reliability of signal transmission, it is imperative to use high-performance isolation technology.
TI's silicon dioxide-based capacitive isolation technology has three major features: first, an isolation voltage of up to 2100V; second, the life of the isolation layer is up to 100 years, meeting the time requirements of functional safety; and third, extremely low electromagnetic radiation. These three features make it very suitable for the rail transit industry.
In terms of processors, in response to the railway transit's need for backup redundancy, TI's dual-core and multi-core processors can provide lock-step or redundancy functions to meet reliability requirements.
In terms of functional safety, all TI products are subject to qualification and reliability testing or identification based on similarity proof before release to ensure high reliability of the products. TI's analog and embedded processing products meet strict functional safety standards (such as ISO 26262 and IEC 61508). And use TÜV SÜD-certified functional safety hardware and software development processes to develop and produce products. TI has a large number of HiRel and automotive-grade products that can meet functional safety requirements.
A new high-speed train needs to go through a long process from design to testing to mass production, during which a 600,000-kilometer test is required to ensure the safety and reliability of the product. TI always provides customers with high reliability, stable and ultra-long supply cycle and commitment support without interruption of production, and can provide a rich product portfolio and system solutions ranging from processors to simulation, from power supply to sensors, from isolation protection to wireless.
Companions on the road to high-speed rail independence
In addition to the two design pain points of complexity and reliability, another headache in the design process is the restriction on the iteration of the solution. Due to various reasons, once the high-speed rail system design is finalized, it is almost impossible to modify it, so the development team needs to think long-term. As a supplier, TI's solution is to work closely with customers from the beginning of product definition to jointly promote system development.
As early as 2008, TI established a joint laboratory with CSR Zhuzhou Research Institute (now CRRC Zhuzhou Electric Locomotive Research Institute), and the two sides discussed future scenarios and how technology needs to develop. In April 2021, the joint laboratory was upgraded, and designers at the Zhuzhou Institute can use TI's full range of analog and embedded processing products for design, including real-time digital signal processors, gallium nitride (GaN) power integrated circuits, industry-leading data converters and other high-reliability products. The laboratory can support CRRC Zhuzhou in doing some cutting-edge design and research, and TI will also invest resources to define and develop products specifically for it.
Behind the upgrade of the joint laboratory, it reflects the progress of China's high-speed rail independent technology, and also reflects that TI has entered China for more than 35 years, witnessing the history of China's railway development. From the initial import assembly to the launch of the "Fuxing", China now leads the global rail transit market, and high-speed rail has become a national business card. In this process from following to learning and then to surpassing, TI's highly localized team has been accompanying this road of introduction, digestion, absorption, and re-innovation.
In the future, in addition to the current high-speed rail, subway, and intercity, perhaps maglev trains and trackless trains will be applied to daily urban transportation, and intelligent transportation systems need to be intelligent, data-based, and interconnected. TI is conducting deeper exchanges and interactions with CRRC based on the joint laboratory to gain a deeper understanding of the system, and to explore together in order to provide more support. Leo said that he hopes to see more Chinese trains speeding through the cooperation between TI and CRRC in every corner of the world along with the development of the "Belt and Road Initiative", which is also the original intention of a TIer to "innovate the world with cores for China".
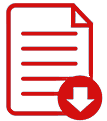
Click "Read original text" to learn more about TI empowering China's new infrastructure - intercity rail transit