Robots have been around in the industrial sector for decades, but technological innovation is driving a whole new wave of factory automation trends. For small businesses that once couldn’t afford (or didn’t need) industrial robots, the emergence of collaborative robots and smaller robots the size of collaborative robots will help them achieve a new level of efficiency and productivity.
Compared with traditional industrial robots, collaborative robots are smaller, more economical, easier to program, and their flexibility is greatly improved. Modern robots can meet the needs of rapid reassignment of tasks to perform new tasks or move to different areas such as factories or warehouses. Collaborative robots can work safely with workers and are particularly suitable for performing dangerous or repetitive tasks, and can also assist workers in tasks that require extremely high precision.
It’s no surprise, then, that collaborative robots are one of the fastest-growing segments of the robotics industry. Global shipments of collaborative robots are expected to exceed 47,000 units per year by 2026, up from 10,000 in 2021[1] and at a faster rate than the expected growth in industrial robots[2].
In order to further optimize the design of collaborative robots to better meet market demand, TE Connectivity (TE) has long focused on realizing key trends in future factory automation, including improving the flexibility of collaborative robots, reducing total costs, and enhancing their safety and durability.
Collaborative robots:
A machine that can perform multiple tasks
While industrial robots are designed to perform the same tasks over and over again for decades, a collaborative robot must be able to adapt to a variety of task types. For example, a company may need a collaborative robot that can easily transition from simple pick and place tasks to assisting with maintenance on machines that require higher precision.
The challenge for collaborative robot designers is that they need to create robotic arms that can not only cover the range of motion required for different tasks, but also keep costs under control. Each possible movement requires a separate axis, each with its own set of motors, sensors, cables, and connectors - all of which increase costs. For this reason, collaborative robot manufacturers have reached a consensus on a standard six-axis design for soft robots. This structure simulates the range of motion of the human arm, making the robotic arm suitable for most collaborative tasks.
However, in this standard setting, designers still need to find the best balance between durability, sensitivity and cost when selecting internal components. For example, a resolver (a system for measuring the angle of rotation) is low cost and highly durable, but may not provide the accuracy required for fine operations. At the other extreme, an optical encoder can provide higher accuracy, but it is easily damaged and expensive. In order to help more customers have the opportunity to use collaborative robots, TE provides a solution between these two options - a magnetic encoder. It can provide higher accuracy than a resolver, but it is cheaper and more durable than an optical encoder.
Optimizing factory robots
Ensure operator safety
By definition, collaborative robots work alongside humans. They can be installed without the use of safety cages, which reduces installation costs and their footprint in a factory or warehouse. However, such structures do require additional safety features to ensure the safety of the operator.
Advances in torque sensors can make collaborative robots safer and more reliable. Torque sensors are installed on each axis of the collaborative robot arm to measure the mechanical tension within the axis motor and gearbox. The torque can be programmed to remain below a certain threshold so that the collaborative robot automatically shuts down before a possible hazard occurs, avoiding operator injury or damage to the collaborative robot arm itself.
As the adoption of collaborative robots continues to rise, we expect to see further improvements in other safety features, such as proximity sensors and absolute position sensors. For example, by using a series of optical sensors and pressure sensors, an invisible fence can be built around a collaborative robot, triggering the machine to slow down or stop immediately if a person enters the collaborative robot's workspace.
Ensure reliability in harsh environments
Reducing downtime and repair costs is critical to keeping the cost of collaborative robots in check, which is one of the challenges designers need to face because collaborative robots often need to work in environments that are not friendly to electronic components and moving parts. Dust, humidity, oil, heat, vibration and electromagnetic interference are very common in factory and warehouse environments.
Therefore, TE has designed components such as position and angle sensors specifically for harsh environments. However, designers tend to overlook other components that are critical to the reliability of collaborative robots, such as cables and connectors.
Cables and connectors for axis components such as sensors and motors are often installed inside the cobot arm. Even with this layer of protection, it is still necessary to use specially designed industrial-grade cable assemblies to achieve the required range of motion for each arm joint while avoiding any unnecessary movement when the arm performs repetitive tasks.
When the task involves coordinating changes between end-of-arm tooling and sensing, connectivity becomes even trickier. Switching between tasks often requires installing a new set of tools at the end of the collaborative robot arm, including grippers, sensors, cameras, and lights. In addition to the collaborative robot arm protection, each of these components requires power and data connections.
Since adaptability is one of the main advantages of collaborative robots, we are committed to helping designers reduce the complexity of wiring and connections without sacrificing functionality. We are developing solutions that combine power and data connectivity in a single cable, such as Single Pair Ethernet (SPE). Such a single cable can provide sufficient power and data transmission rate for any end-of-arm peripheral device.
Supporting future factory architecture
Just a few years ago, collaborative robots were either immature or too expensive, but now their rise has taken automation to a new level. Collaborative robots are constantly replacing humans to perform more tasks, while also helping manufacturers optimize production processes and achieve greater efficiency and flexibility.
In the future, we will see: modular unit-configured manufacturing workshops, each unit can achieve the flexibility to switch between discrete tasks or customized processes. In addition, advances in wireless connectivity will help factories monitor and analyze the production of each semi-automatic unit. At the same time, the continuous development of artificial intelligence and machine learning will also help collaborative robots learn new tasks faster.
The increase in factory automation can meet the growing demands of manufacturers in terms of speed, efficiency and customization, while also helping them cope with other challenges, including the continued shortage of labor. Although it will still take some time to move from semi-automatic production to fully automated production, the combination of collaborative robots with seamless connectivity and enhanced intelligence technology will be the only way to achieve this goal.
As an authorized distributor of TE Connectivity, Heilind can provide relevant product services and support to the market. In addition, Heilind also supplies products from many of the world's top manufacturers, covering 25 different component categories. It attaches importance to all market segments and all customers, and constantly seeks a wide range of product supplies to cover all markets.
Previous article:How to achieve universal robotic assembly through compliant contact
Next article:Can the mobile robot industry also replicate the essence of the "Wintel Alliance" model?
Recommended ReadingLatest update time:2024-11-16 11:49
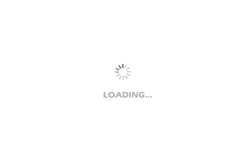
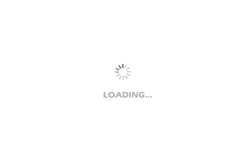
- Popular Resources
- Popular amplifiers
- Using IMU to enhance robot positioning: a fundamental technology for accurate navigation
- Researchers develop self-learning robot that can clean washbasins like humans
- Universal Robots launches UR AI Accelerator to inject new AI power into collaborative robots
- The first batch of national standards for embodied intelligence of humanoid robots were released: divided into 4 levels according to limb movement, upper limb operation, etc.
- New chapter in payload: Universal Robots’ new generation UR20 and UR30 have upgraded performance
- Humanoid robots drive the demand for frameless torque motors, and manufacturers are actively deploying
- MiR Launches New Fleet Management Software MiR Fleet Enterprise, Setting New Standards in Scalability and Cybersecurity for Autonomous Mobile Robots
- Nidec Drive Technology produces harmonic reducers for the first time in China, growing together with the Chinese robotics industry
- DC motor driver chip, low voltage, high current, single full-bridge driver - Ruimeng MS31211
- Innolux's intelligent steer-by-wire solution makes cars smarter and safer
- 8051 MCU - Parity Check
- How to efficiently balance the sensitivity of tactile sensing interfaces
- What should I do if the servo motor shakes? What causes the servo motor to shake quickly?
- 【Brushless Motor】Analysis of three-phase BLDC motor and sharing of two popular development boards
- Midea Industrial Technology's subsidiaries Clou Electronics and Hekang New Energy jointly appeared at the Munich Battery Energy Storage Exhibition and Solar Energy Exhibition
- Guoxin Sichen | Application of ferroelectric memory PB85RS2MC in power battery management, with a capacity of 2M
- Analysis of common faults of frequency converter
- In a head-on competition with Qualcomm, what kind of cockpit products has Intel come up with?
- Dalian Rongke's all-vanadium liquid flow battery energy storage equipment industrialization project has entered the sprint stage before production
- Allegro MicroSystems Introduces Advanced Magnetic and Inductive Position Sensing Solutions at Electronica 2024
- Car key in the left hand, liveness detection radar in the right hand, UWB is imperative for cars!
- After a decade of rapid development, domestic CIS has entered the market
- Aegis Dagger Battery + Thor EM-i Super Hybrid, Geely New Energy has thrown out two "king bombs"
- A brief discussion on functional safety - fault, error, and failure
- In the smart car 2.0 cycle, these core industry chains are facing major opportunities!
- The United States and Japan are developing new batteries. CATL faces challenges? How should China's new energy battery industry respond?
- Murata launches high-precision 6-axis inertial sensor for automobiles
- Ford patents pre-charge alarm to help save costs and respond to emergencies
- New real-time microcontroller system from Texas Instruments enables smarter processing in automotive and industrial applications
- 【Repost】Everything you want to know about rectifier diodes is here
- Square wave double frequency
- Enhanced performance 100-bit gate driver improves efficiency of advanced communications power modules
- How to implement interruption of USB virtual serial port
- How can Kicad batch convert yellow words into silk screen words?
- High cost-effective single-chip microcomputer application system structure design
- The rapid entry of UWB centimeter-level positioning solutions has brought strong momentum to indoor positioning
- [ST NUCLEO-H743ZI Review] (1) SPI DMA flashing TFT screen
- Over View can customize the format and content of the audio body according to your needs
- Architecture Issues