With motors now responsible for two-thirds of industrial electricity consumption and one-quarter of residential electricity consumption, motor efficiency continues to receive greater attention. Standard motor applications are perfectly capable of operating at higher energy efficiencies, but most motors are inefficient in terms of converting electrical energy to mechanical energy. This means that they waste a lot of energy, which is dissipated as heat rather than converted into useful mechanical energy.
Furthermore, since an uncontrolled motor must overcome the effects of transient mechanical loads, designers have little choice but to oversize the motor, and an oversized AC induction motor (the most common type of motor) is necessarily less efficient because the motor is operating at a load less than it was designed for.
Improve the efficiency of the motor
These problems can be overcome by intelligent control, which can greatly improve the efficiency of the motor in two ways. First, intelligent control uses advanced algorithms to improve the operating performance of the motor. The most common method is to use vector control to operate the AC induction motor, which allows the motor to be reasonably sized to achieve optimal efficiency. In addition, adjustable speed also allows the system to operate at a higher efficiency. For example, a vector-controlled adjustable speed drive can avoid the use of transmissions, thereby reducing energy losses caused by the mechanical components of the system.
Secondly, because the system uses intelligent control, it is possible to replace the existing motor with a more efficient motor. The gradual use of permanent magnet motors in electrical appliances is a reflection of this development trend.
Permanent magnet synchronous motors are inherently more efficient than AC induction motors because they do not have the conduction losses associated with the induced rotor currents, and they also have superior mechanical properties, such as lower torque ripple, quieter operation, and they are smaller in size while producing the same mechanical power output. Switched reluctance motors can also be extremely efficient in fixed or moderately variable speed applications that require the precise, complex control capabilities of a DSP controller.
All of these solutions have one thing in common: they use intensive numerical calculations to improve system performance. Vector control algorithms require the orientation of the rotor flux to be measured or predicted, and then optimize the position of the stator flux generated by a multi-phase winding to produce the maximum torque given the flux structure. For a permanent magnet motor, the stator flux needs to be separated by 90 degrees (electrical angle), which is the best way to produce torque. This is because the torque generated is directly proportional to the sine of the angle between the two fluxes. (In AC induction motors, the relationship between the fluxes is more complicated due to the magnetizing components of the flux, but the basic principle is the same.)
Implementation of intelligent control
The challenge in implementing economical intelligent control lies in the mathematical complexity of the algorithms involved, because most microcontrollers (MCUs) cannot handle such complex calculations in real time. However, a new generation of inexpensive digital signal processor (DSP) controllers provide the computing power required for intelligent control, as well as system-on-chip (SOC) integration and software development support that helps simplify motor control system design.
DSP controllers running intelligent control software enable applications to respond to load changes with smaller or more efficient motors, reducing cost, space and cooling requirements. Smaller motors are also cheaper, and the cost of power electronics is reduced because the current required to withstand these circuits is also lower. Intelligent control based on DSP controllers has the advantage of good economics, and automobiles, industrial equipment, household appliances, heating, ventilation and air conditioning (HVAC) systems and many other motor applications will benefit from it.
What can advanced controls do for end equipment?
In addition to making motors more efficient, advanced control technology also allows system designers to innovate, improve systems and reduce costs. In complex motor applications, the need for embedded intelligent control is obvious. For example, positioning servo motors on assembly lines must be able to adapt to changes in belt friction, load weight and other factors. The speed of fan motors used to provide constant airflow in HVAC systems must be constantly adjusted to compensate for pressure changes caused by door opening and closing.
Essentially, intelligent motor control requires instant calculation of the rotor's flux position and speed in order to properly adjust the current flowing through the motor windings to ensure low torque ripple. However, while the basic requirements of intelligent motor control design are rotor positioning and speed, they are not limited to this. Other challenges include: power factor correction (PFC) to eliminate transient spikes in the power supply, elimination of torque ripple effects, and compliance with electromagnetic compatibility regulations.
Designing with Intelligent Control
Microcontrollers lack critical numerical processing capabilities, making them an inefficient and less economical solution for intelligent control in terms of system cost and performance. High-performance DSP controllers can perform rotor position and speed calculations in real time without table lookups. External sensors are not necessary because the DSP controller can calculate these vectors from voltage and current feedback provided by internal online sensors. The processing power of the DSP controller enables field-oriented control (FOC), which allows the stator magnetic field to be orthogonal to the rotor flux to achieve a dynamic machine. The entire 32-bit FOC algorithm loop, including feedback, can be completed in 10ms, leaving ample time for flux estimator, PFC and other algorithm processing. In addition, these algorithms can be reused in other products based on the same DSP controller platform, reducing development costs and shortening the time to market for new motors.
High level of integration and development support
The new generation of DSP controllers offers peripheral integration that is easier to use than those based on MCUs. One example is TI's 150MIPS TMS320F2812 digital signal processor (see Figure 1), which uses a single-cycle 32-bit multiple accumulation (MAC) data path or dual 16-bit MACs to combine the performance and accuracy of a DSP with the flexibility of a high-end MCU. Fast interrupt handling, coupled with operation codes for common control (such as bit manipulation and branching), makes the device suitable for multi-purpose, multi-tasking environments. On-chip functional modules include flash memory, analog/digital converters, pulse width modulation outputs, and CAN bus support.
Software development support for DSP is provided by an integrated development environment (IDE). The highly efficient C compiler allows developers to generate object code that is almost as compact as assembly, achieving excellent performance after a fast learning curve. Tools such as IQMath provide programmers with an automatic online code editor and a library for floating-point functions, simplifying the use of real arithmetic functions in control algorithms. For faster development, manufacturers and third parties provide ready-made motor control modules.
Conclusion
The monolithic DSP controller solution, including easy-to-use software, enables manufacturers to embed intelligent control functions with minimal development investment. As a result, equipment manufacturers and end users can use motors of appropriate size with lower cost, lower power consumption and higher reliability. The intelligent control technology implemented by the high-performance programmable DSP controller will provide motor system designers with the methods needed to develop a new generation of environmentally friendly "green" motors.
Previous article:Single-chip DSP intelligent motor control solution
Next article:Design of human-machine interface based on DSP chip TMS320LF2407
Recommended ReadingLatest update time:2024-11-16 16:20
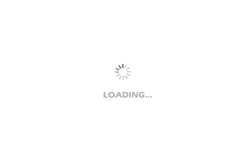
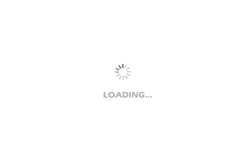
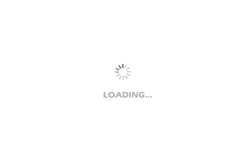
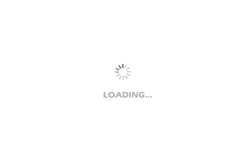
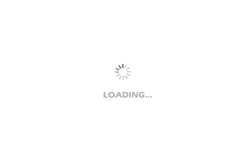
- Popular Resources
- Popular amplifiers
- Huawei's Strategic Department Director Gai Gang: The cumulative installed base of open source Euler operating system exceeds 10 million sets
- Analysis of the application of several common contact parts in high-voltage connectors of new energy vehicles
- Wiring harness durability test and contact voltage drop test method
- Sn-doped CuO nanostructure-based ethanol gas sensor for real-time drunk driving detection in vehicles
- Design considerations for automotive battery wiring harness
- Do you know all the various motors commonly used in automotive electronics?
- What are the functions of the Internet of Vehicles? What are the uses and benefits of the Internet of Vehicles?
- Power Inverter - A critical safety system for electric vehicles
- Analysis of the information security mechanism of AUTOSAR, the automotive embedded software framework
Professor at Beihang University, dedicated to promoting microcontrollers and embedded systems for over 20 years.
- Innolux's intelligent steer-by-wire solution makes cars smarter and safer
- 8051 MCU - Parity Check
- How to efficiently balance the sensitivity of tactile sensing interfaces
- What should I do if the servo motor shakes? What causes the servo motor to shake quickly?
- 【Brushless Motor】Analysis of three-phase BLDC motor and sharing of two popular development boards
- Midea Industrial Technology's subsidiaries Clou Electronics and Hekang New Energy jointly appeared at the Munich Battery Energy Storage Exhibition and Solar Energy Exhibition
- Guoxin Sichen | Application of ferroelectric memory PB85RS2MC in power battery management, with a capacity of 2M
- Analysis of common faults of frequency converter
- In a head-on competition with Qualcomm, what kind of cockpit products has Intel come up with?
- Dalian Rongke's all-vanadium liquid flow battery energy storage equipment industrialization project has entered the sprint stage before production
- Allegro MicroSystems Introduces Advanced Magnetic and Inductive Position Sensing Solutions at Electronica 2024
- Car key in the left hand, liveness detection radar in the right hand, UWB is imperative for cars!
- After a decade of rapid development, domestic CIS has entered the market
- Aegis Dagger Battery + Thor EM-i Super Hybrid, Geely New Energy has thrown out two "king bombs"
- A brief discussion on functional safety - fault, error, and failure
- In the smart car 2.0 cycle, these core industry chains are facing major opportunities!
- The United States and Japan are developing new batteries. CATL faces challenges? How should China's new energy battery industry respond?
- Murata launches high-precision 6-axis inertial sensor for automobiles
- Ford patents pre-charge alarm to help save costs and respond to emergencies
- New real-time microcontroller system from Texas Instruments enables smarter processing in automotive and industrial applications
- EEWORLD University ---- Using lithium-ion batteries more safely and efficiently - Battery Management System (BMS) Solution
- Talk: Small capital investment
- Where does the EG8010 dead time go?
- Downloads|Selected Courseware & Latest Materials from Tektronix 2019 Semiconductor Seminar
- GaN Power HEMT > 650 V: Parametric Analysis and Comparison with SiC MOSFET
- Voltage controlled current source composed of opa547
- [GUIX①, one of threadX components] guix text button
- Qorvo Technology Video: GaN Solutions for Sub-6 GHz 5G Base Station Applications
- [Jihai M3 core APM32E103VET6S MINI development board] 02. USART online interaction function
- PCB design of RF devices