Abstract: This paper introduces the design of a four-story elevator control system based on FPGA. The system uses Altera's CycloneⅡ series FPGA chip EP2C5T144 as the main control chip, and uses Verilog-HDL programming description to realize intelligent control of the elevator. After simulation verification, the required functions are completed. The design adopts modular programming, and the upgrade can realize any multi-story elevator system, which has strong adaptability and practicality.
Keywords: elevator control; FPGA; Verilog; control module
0 Introduction
With the development of society, the use of elevators is becoming more and more common, and the requirements for elevator functions are constantly increasing, and the corresponding control methods are also constantly changing. The microcomputer control of elevators mainly includes: PLC control, single-board computer control, single-chip microcomputer control, single microcomputer control, multi-microcomputer control and artificial intelligence control. With the development of application-specific integrated circuit ASIC design technology and EDA technology, the widespread use of programmable logic devices has brought revolutionary changes to digital system design, changing the shortcomings of traditional circuit design, such as the use of many chips, complex circuits, difficulty in finding problems, and difficulty in function expansion. This design uses FPGA devices as the main control chip and Verilog-HDL language to design a four-story single passenger box elevator control system. The design adopts modular design, which is easy to modify and upgrade. It can be slightly improved to realize multi-story elevator control.
1 Overall design of elevator control system
1.1 Design tasks and requirements
Design a four-story elevator control system with the following requirements:
(1) Internal signals of each floor elevator: request buttons for each floor, door opening and closing request buttons, floor display, and elevator operation status display. External signals: up and down request buttons, floor display, and elevator operation status display.
(2) Able to store request signals. During the elevator ascent (descent) process, according to the elevator operation status, first respond to each request in direction priority and cyclic order.
(3) After reaching the requested floor, the indicator light of the floor lights up, the elevator door automatically opens, and the door opening indicator light lights up. After the delay waiting time, the elevator door automatically closes (the door opening indicator light goes out), and the elevator continues to run. When the elevator is idle, it stops at the 0th floor.
(4) It has an overload alarm function.
1.2 Hardware structure of the elevator control system
The hardware structure of the elevator control system is shown in Figure 1.
As shown in Figure 1, the system is mainly composed of FPGA controller, input signal modules, and output drive modules. The input signals of the FPGA control module include: elevator internal and external request signals, floor arrival signals, restart overload alarm signals, etc.; its output signals drive the display circuit, elevator door switch circuit, motor drive circuit, and other alarm circuits. The FPGA control module is the core of this design.
2 Design and implementation of FPGA controller
The development software of this design uses Altera's QuartusⅡ integrated development environment, adopts a top-down design method, and combines module design with Verilog-HDL description input method to facilitate program maintenance and upgrade. The overall design of the FPGA controller is shown in Figure 2.
As shown in Figure 2, FPGA control programming mainly consists of six modules: key request module, state control module, motor drive module, display and alarm module, switch door control module, and frequency division module. The signals and functions of each module are as follows:
Module 1: Key request module
The interface signals of this module are shown in Table 1, and the module functions are as follows:
(1) Use the latch to store the input request signal and clear it to 0 when the request is met. For the convenience of data representation, the suffixes 0 to 3 in this design represent the 1st to 4th floors respectively.
(2) According to the running status of the elevator, according to the principle of direction priority and cyclic execution, the floor signal of the next stop of the elevator is extracted from the request signal and output. If the current floor is 2 and the state is rising, then the judgment priority is: p2/up2→p3/down3→down2→downl→p0/up0.
(3) When there is no request signal, the next stop floor is 0.
Module 2: State control module
This module is the core control module of the system design. This paper divides the elevator operation into 4 states: ascending, descending, stopping, and idle. The state transition diagram of the control system is shown in Figure 3.
When the system restarts (res=1), it enters the idle state (Idle). In the idle state, the output signal posit=up=down=open=0. When the input signal goto is 0, it remains in the idle state; when the goto signal is not 0, it enters the rising state (Stop). When the first floor rising signal is triggered, it enters the stop state. In the stop state, the rising edge of the open signal triggers the elevator door to open; up=down =0, posit=goto. During the elevator door opening delay period (dooropen=1), it remains in the stop state; when the elevator door is closed (dooropen=0), the next floor is determined. If it is greater than the current floor, it enters the rising state; if it is less than the current floor, it enters the descending state. In the ascending state, up=1, updown=01, posit=goto, triggering the motor control module to drag the motor up. The floor reaches the signal, causing the system to enter the stop state. The descending state is the same. The interface signals of this module are shown in Table 2.
Module 3: Motor control module
The input signals of this module are: rising trigger signal (up), falling trigger signal (down), current floor (posit) and next floor (goto), and the output signal is: 4 motor drive signals with different phases. The module is triggered by the lifting signal, and generates 4-phase motor drive signals P[3:0] through the motor state controller, which are output to the motor drive circuit. Its frequency determines the motor rotation, and its phase determines the direction of motor rotation. Each frequency signal of P[3:0] is provided by the divider module.
Module 4: Display module
The function of this module is used for the seven-segment code display or LED display of the elevator floor (posit) and the elevator operation status (updown). And the alarm and display of the overload signal (over).
Module 5: Door control module
This module is used to control the elevator door state. The door opening is triggered by the input door control signal open signal (doorstat=1). After a delay, the elevator door automatically closes (doorstat=0). If the elevator is overloaded (over=1), the elevator door will not close, and the elevator will remain in the open state until the overload signal is cleared.
Module 6: Frequency division module
The frequency division module is used to divide the system clock signal to generate various frequency signals provided to the motor control module.
3 Simulation verification
This design adopts modular design at the top level, and each module uses VerilogHDL hardware description language. The top-down design method is convenient for program error checking, upgrading and improvement. This design can realize elevator control on any floor with slight modification. Functional simulation and timing simulation of the circuit generated after analyzing, compiling, synthesizing and wiring the designed program can obtain logical values that meet the design requirements. The timing simulation waveform is shown in Figure 4.
As can be seen from Figure 4: the controller can always effectively store the request signals of each floor, and can execute the requests of each floor according to the direction priority and cyclic order. The status of each signal meets the design requirements. The signal delay is 10 ns, which is within the allowable range.
The hardware implementation of this design adopts the Kangxin KX_7CH minimum system version. The program is locked by pins and programmed to download to the device. After testing, the logic is completely correct and meets the design requirements.
4 Conclusion
The digital circuit design method based on FPGA has huge advantages in reliability, volume and cost. It has become one of the main means to realize digital circuits. The four-story elevator controller designed in this paper is suitable for any floor with a little improvement. It has strong flexibility, reliable operation, and strong adaptability and practicality.
Previous article:FPGA Implementation of PN Code Capture and Tracking in Direct Sequence Spread Spectrum System
Next article:Using LabVIEW FPGA Module to Realize Continuous Data Transmission in Different Clock Domains
Recommended ReadingLatest update time:2024-11-17 01:59
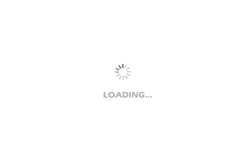
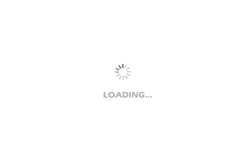
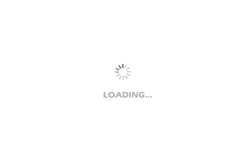
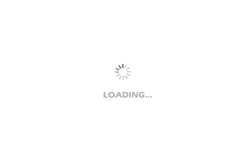
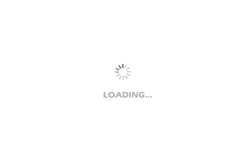
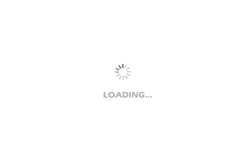
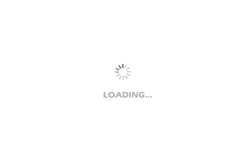
- Popular Resources
- Popular amplifiers
-
Analysis and Implementation of MAC Protocol for Wireless Sensor Networks (by Yang Zhijun, Xie Xianjie, and Ding Hongwei)
-
MATLAB and FPGA implementation of wireless communication
-
Intelligent computing systems (Chen Yunji, Li Ling, Li Wei, Guo Qi, Du Zidong)
-
Summary of non-synthesizable statements in FPGA
- Huawei's Strategic Department Director Gai Gang: The cumulative installed base of open source Euler operating system exceeds 10 million sets
- Analysis of the application of several common contact parts in high-voltage connectors of new energy vehicles
- Wiring harness durability test and contact voltage drop test method
- Sn-doped CuO nanostructure-based ethanol gas sensor for real-time drunk driving detection in vehicles
- Design considerations for automotive battery wiring harness
- Do you know all the various motors commonly used in automotive electronics?
- What are the functions of the Internet of Vehicles? What are the uses and benefits of the Internet of Vehicles?
- Power Inverter - A critical safety system for electric vehicles
- Analysis of the information security mechanism of AUTOSAR, the automotive embedded software framework
Professor at Beihang University, dedicated to promoting microcontrollers and embedded systems for over 20 years.
- Innolux's intelligent steer-by-wire solution makes cars smarter and safer
- 8051 MCU - Parity Check
- How to efficiently balance the sensitivity of tactile sensing interfaces
- What should I do if the servo motor shakes? What causes the servo motor to shake quickly?
- 【Brushless Motor】Analysis of three-phase BLDC motor and sharing of two popular development boards
- Midea Industrial Technology's subsidiaries Clou Electronics and Hekang New Energy jointly appeared at the Munich Battery Energy Storage Exhibition and Solar Energy Exhibition
- Guoxin Sichen | Application of ferroelectric memory PB85RS2MC in power battery management, with a capacity of 2M
- Analysis of common faults of frequency converter
- In a head-on competition with Qualcomm, what kind of cockpit products has Intel come up with?
- Dalian Rongke's all-vanadium liquid flow battery energy storage equipment industrialization project has entered the sprint stage before production
- Allegro MicroSystems Introduces Advanced Magnetic and Inductive Position Sensing Solutions at Electronica 2024
- Car key in the left hand, liveness detection radar in the right hand, UWB is imperative for cars!
- After a decade of rapid development, domestic CIS has entered the market
- Aegis Dagger Battery + Thor EM-i Super Hybrid, Geely New Energy has thrown out two "king bombs"
- A brief discussion on functional safety - fault, error, and failure
- In the smart car 2.0 cycle, these core industry chains are facing major opportunities!
- Rambus Launches Industry's First HBM 4 Controller IP: What Are the Technical Details Behind It?
- The United States and Japan are developing new batteries. CATL faces challenges? How should China's new energy battery industry respond?
- Murata launches high-precision 6-axis inertial sensor for automobiles
- Ford patents pre-charge alarm to help save costs and respond to emergencies
- The channel for exchanging TI points for chip points has been opened. Full redemption within a limited time. The ultimate redemption is coming~
- An error occurred when simulating and debugging the program: no contex-m device found in jtag chain. How to deal with it?
- GPIO principle of TMS320F28335
- I really need help with this strange linking error. It has been bothering me for days.
- Oh my god, the teacher actually organized a high school student to take the college entrance examination for him (photo)
- Introduction to the working principle and characteristics of rectifier transformer
- TD1509 has large output voltage ripple
- Design of data forwarder based on MSP430F149
- Mini Adafruit QT Py Development Board
- openmv3 serial port hangs up