Keywords: ultrasonic; CPLD; thickness measurement
0 Introduction
In industrial production and product quality inspection, it is often necessary to measure the thickness of the workpiece under non-destructive conditions to determine whether it meets the design requirements. At present, steel plate is one of the four major types of steel (plate, tube, type, wire), which is widely used in engineering projects such as high-rise buildings, bridges, offshore oil platforms, and large ships. Its thickness is directly related to the safety and reliability of these engineering projects. In terms of steel plate thickness measurement, ultrasonic non-destructive thickness measurement method will be widely used.
1 Principle of ultrasonic thickness measurement
The basic principle of ultrasonic thickness measurement is to use the propagation characteristics of ultrasonic waves in the medium to find material defects and wall thickness. The pulse reflection thickness measurement method is essentially to measure the round-trip propagation time of ultrasonic pulses in the material.
According to the working principle, ultrasonic measurement can be divided into several methods, such as resonance method, interference method and pulse echo method. Since the pulse echo method does not involve the resonance mechanism and is not closely related to the surface finish of the object being measured, the ultrasonic pulse echo method is also a widely used method. Its principle is to use an ultrasonic probe to send an ultrasonic pulse to the object being measured. This ultrasonic pulse propagates in the object being measured and is reflected when it propagates to the bottom surface of the object being measured. The reflected ultrasonic wave is received by the ultrasonic probe again. In this way, the time t from the ultrasonic probe sending the ultrasonic pulse to the ultrasonic probe receiving the reflected pulse can be accurately detected by the circuit. In the time t, the ultrasonic wave completes a round trip in the object being measured, as shown in Figure 1. If the thickness of the object being measured is represented by d, the total stroke of the ultrasonic wave is 2d. Since the speed c of sound wave propagation in a certain object is a constant, the thickness of the object being measured can be calculated by the following formula: d=vt/2. In the formula: d-thickness of the object being measured; v-ultrasonic wave speed; t-time from the ultrasonic wave being emitted from the tube to receiving the echo.
The ultrasonic sensor is divided into two parts: the transmitter and the receiver. According to its working principle, the ultrasonic sensor can be divided into several types such as piezoelectric, magnetostrictive, and electromagnetic. The most commonly used is the piezoelectric sensor.
The core of the piezoelectric ultrasonic sensor probe is the piezoelectric chip, which uses the piezoelectric effect to realize the acoustic-electric conversion. Its vibration frequency is above several hundred kilohertz. When the pulse signal (trigger pulse) is added to its two electrodes, if its frequency is equal to the natural frequency of the chip, the piezoelectric chip will resonate and drive the resonance plate to vibrate, thereby generating ultrasonic waves. On the contrary, if no voltage is added between the electrodes, when the resonance plate receives the echo signal, it will compress the two piezoelectric chips to vibrate, thereby converting mechanical energy into electrical signals. At this time, the sensor becomes an ultrasonic receiver.
2 Overall structure and working principle of ultrasonic thickness measurement system circuit
The main task of the ultrasonic thickness measurement system module is to generate an ultrasonic signal, amplify the ultrasonic signal and load it onto the ultrasonic probe. The ultrasonic probe drives the object to be measured to resonate, then samples the obtained data and holds the peak value, and then sends it to the signal processing module. Therefore, it is the basic part of this design and the key to achieving the output of detection information and obtaining good ultrasonic echo information.
This ultrasonic thickness measurement system module is mainly composed of a trigger signal generating circuit, a transmitting and receiving amplifying circuit, an amplifying and detecting circuit, a sampling peak holding circuit,
an analog-to-digital conversion
circuit, a liquid crystal display circuit, and a CPLD operation and control circuit. The circuit structure design is shown in Figure 2:
When the power is turned on and the thickness measurement starts, the CPU (central processing unit) sends a thickness measurement synchronization signal to trigger the transmitting circuit, so that the straight probe generates ultrasonic waves to be incident on the workpiece. When the ultrasonic waves return to the probe, they are first attenuated, then amplified and detected for sampling, and the resulting thickness time square wave is sent to the ADC574 analog-to-digital converter through the integral holder. After the analog-to-digital conversion, it is sent to the CPLD for data processing and displayed on the 12864 LCD display module.
3 Software Programming
The software programming block diagram is shown in Figure 3. The system software is designed according to the function of this instrument. In the main program, initialization is first performed. In the initialization, the stack pointer is set, the display unit is defined, the display buffer address is set, the data address is displayed, and then the switch quantity is read. According to the requirements of the manual switch, the calibration, flaw detection or thickness measurement processing program is transferred. If none of the above three situations are true, the digital tube will display zero, and finally return to read the switch quantity.
4 Thickness measurement program design
Since this system uses a 12-bit output ADC574 analog-to-digital converter, it can ensure high thickness measurement accuracy. The ultrasonic thickness gauge of this system uses VerilogHD programming to implement the data acquisition and processing module gate. Its CPLD software implementation method is shown in Figure 4. The measurement process is as follows.
(1) The instrument is powered on and enters the measurement state. The CPU first initializes the CPLD to clear the counter and latch, and the CPLD waits for the CPU's transmission request.
(2) If the CPU's transmission request is received, the CPLD generates a trigger signal of several hundred nanoseconds, opens the high-voltage circuit, stimulates the probe to generate ultrasonic waves, and starts the counter to start counting. According to the measurement range of the thickness gauge of 1 to 300 mm, a 16-bit counter provided by the software can cover the required measurement range. If the CPLD resources are relatively tight, you can also use the VerilogHDL language to design a counter with a suitable number of bits (such as a 12-bit counter) to achieve the effect of reasonable use of resources.
(3) If the CPLD does not receive the echo signal within a reasonable time, the echo valid flag is 0, the data in the latch is invalid, and the CPU does not read it. When the CPLD receives the echo signal, it is also necessary to perform a width detection on the received echo signal. Only when the echo width is within a reasonable range is it considered valid. The echo width detection is to avoid inaccurate readings caused by poor probe coupling.
(4) When the CPLD detects a valid echo, it latches the time taken from transmission to reception, the leading and trailing edges of the echo, and other related information. The echo valid flag is set to 1, and the CPU reads the required information. It is worth noting that in the data acquisition of the ultrasonic thickness gauge echo, only the leading and trailing edges of the echo are detected, and the midpoint is calculated based on the symmetry, without spending more resources to calculate its peak value. This makes the instrument simpler in structure, smaller in size, and lower in power consumption. This program continuously collects 256 data and accumulates the average thickness, then converts the hexadecimal to decimal, and displays the decimal thickness value.
5 Conclusion
The application of low-power CPLD in ultrasonic thickness gauges can reduce the production cost of products, improve the reliability of the system, reduce the physical size of the design, and improve flexibility. In addition, while meeting the measurement accuracy, it greatly reduces the overall static power consumption of the instrument. Conclusion of this system:
(1) The probe and thickness measurement of this system are not limited by the shape and thickness of the workpiece, and have high sensitivity.
(2) The performance indicators of this system meet the following values:
detection sensitivity margin>=46 dB;
vertical linear error<=5%;
horizontal linear error<=1%;
attenuation accuracy±0.6 for every 12 dB;
resolution>=22 dB;
dynamic range>=32 dB;
thickness measurement accuracy0.05 mm.
Previous article:Cirrus CS485xx Series Digital Audio DSP Processing Solutions
Next article:Design of LCD display driver IP based on NiosII in SOPC
Recommended ReadingLatest update time:2024-11-16 17:58
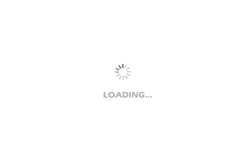
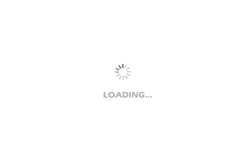
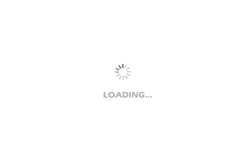
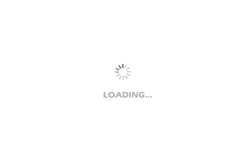
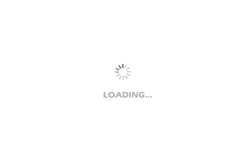
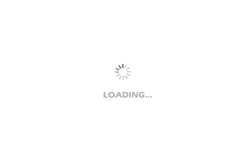
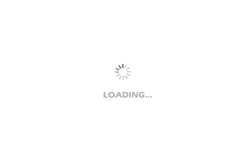
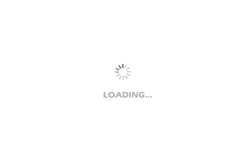
- Popular Resources
- Popular amplifiers
-
Learn CPLD and Verilog HDL programming technology from scratch_Let beginners easily learn CPLD system design technology through practical methods
-
Practical Electronic Components and Circuit Basics (4th Edition)_Explanation of basic circuit principles, introduction to electronic components, design of various circuits and practical circuit analysis
-
Computer Vision Applications in Autonomous Vehicles: Methods, Challenges, and Future Directions
-
FPGA Principle and Structure (Zhao Qian)
- Huawei's Strategic Department Director Gai Gang: The cumulative installed base of open source Euler operating system exceeds 10 million sets
- Analysis of the application of several common contact parts in high-voltage connectors of new energy vehicles
- Wiring harness durability test and contact voltage drop test method
- Sn-doped CuO nanostructure-based ethanol gas sensor for real-time drunk driving detection in vehicles
- Design considerations for automotive battery wiring harness
- Do you know all the various motors commonly used in automotive electronics?
- What are the functions of the Internet of Vehicles? What are the uses and benefits of the Internet of Vehicles?
- Power Inverter - A critical safety system for electric vehicles
- Analysis of the information security mechanism of AUTOSAR, the automotive embedded software framework
Professor at Beihang University, dedicated to promoting microcontrollers and embedded systems for over 20 years.
- Innolux's intelligent steer-by-wire solution makes cars smarter and safer
- 8051 MCU - Parity Check
- How to efficiently balance the sensitivity of tactile sensing interfaces
- What should I do if the servo motor shakes? What causes the servo motor to shake quickly?
- 【Brushless Motor】Analysis of three-phase BLDC motor and sharing of two popular development boards
- Midea Industrial Technology's subsidiaries Clou Electronics and Hekang New Energy jointly appeared at the Munich Battery Energy Storage Exhibition and Solar Energy Exhibition
- Guoxin Sichen | Application of ferroelectric memory PB85RS2MC in power battery management, with a capacity of 2M
- Analysis of common faults of frequency converter
- In a head-on competition with Qualcomm, what kind of cockpit products has Intel come up with?
- Dalian Rongke's all-vanadium liquid flow battery energy storage equipment industrialization project has entered the sprint stage before production
- Allegro MicroSystems Introduces Advanced Magnetic and Inductive Position Sensing Solutions at Electronica 2024
- Car key in the left hand, liveness detection radar in the right hand, UWB is imperative for cars!
- After a decade of rapid development, domestic CIS has entered the market
- Aegis Dagger Battery + Thor EM-i Super Hybrid, Geely New Energy has thrown out two "king bombs"
- A brief discussion on functional safety - fault, error, and failure
- In the smart car 2.0 cycle, these core industry chains are facing major opportunities!
- The United States and Japan are developing new batteries. CATL faces challenges? How should China's new energy battery industry respond?
- Murata launches high-precision 6-axis inertial sensor for automobiles
- Ford patents pre-charge alarm to help save costs and respond to emergencies
- New real-time microcontroller system from Texas Instruments enables smarter processing in automotive and industrial applications
- Playing with Zynq Serial 31——[ex53] EMIO control based on Zynq PS
- Great! Tektronix oscilloscopes have been completely upgraded, come and unlock them! If you don't read it, you will miss out on 100 million!
- TMS320C6000 Basic Learning (3)——CCS v5 Software Development Environment Construction
- Microcontrollers: The Basics
- Improvement of RC series-parallel frequency-selective network oscillator in El experimental box
- Texas Instruments helps you solve the three most common problems in high-speed amplifier design!
- LNA [Low Noise Amplifier Practical Application Case]——[qorvo-TQL9092]
- 【Home Smart Dashboard】 Development and Construction of ESP-IDF under Linux
- Solutions to security issues in RF systems and Wi-Fi networks
- [ESP32-S2-Kaluga-1 Review] 2. LCD display pictures