DSP chip, also known as digital signal processor , is a microprocessor that is particularly suitable for digital signal processing operations. Its host application is to implement various digital signal processing algorithms in real time and quickly. According to the requirements of digital signal processing, DSP chips generally have the following main features:
(1) One multiplication and one addition can be completed in one instruction cycle;
(2) The program and data spaces are separated, and instructions and data can be accessed simultaneously;
(3) The chip has fast RAM, which can usually be accessed simultaneously in two blocks through independent data buses;
(4) Hardware support for low-overhead or no-overhead loops and jumps;
(5) Fast interrupt processing and hardware I/O support;
(6) Having multiple hardware address generators operating in a single cycle;
(7) Multiple operations can be performed in parallel; (8) Pipeline operations are supported so that operations such as instruction fetch, decoding, and execution can be performed in an overlapping manner.
When we design DSP application systems, DSP chip selection is a very important link. Only after the DSP chip is selected in the DSP system hardware design can its peripheral circuits and other circuits of the system be further designed. Therefore, the selection of DSP chips should be determined according to the actual needs of the application system, so as to meet the use requirements and not waste resources, thereby achieving the purpose of minimizing costs.
The DSP real-time system design and development process is shown in Figure 1.
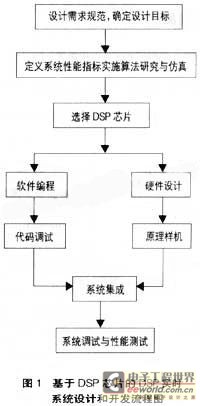
Major DSP chip manufacturers and their products
Texas Instruments
As we all know, Texas Instruments (TI) is the world's most famous DSP chip manufacturer, and its products are also the most widely used. The TMS320 series DSP chips produced by TI are widely used in various fields. In 1982, TI successfully launched its first generation DSP chip TMS32010, which was a milestone in the history of DSP application. Since then, DSP chips have been truly widely used. Due to the characteristics of low price, easy to use, and powerful functions, the TMS320 series DSP chips have gradually become the most influential and successful DSP series processors.
At present, TI has three main series of products on the market:
(1) TMS320C2000 series for digital control and motion control, mainly including TMS320C24x/F24x, TMS320LC240x/LF240x, TMS320C24xA/LF240xA, TMS320C28xx, etc.
(2) TMS320C5000 series for low-power, handheld devices, and wireless terminal applications, mainly including TMS320C54x, TMS320C54xx, TMS320C55x, etc.
(3) The TMS320C6000 series, which is aimed at high-performance, multi-functional and complex applications, mainly includes TMS320C62xx, TMS320C64xx, TMS320C67xx, etc.
Analog Devices
ADI also has a certain share in the DSP chip market and has successively launched a series of DSP chips with their own characteristics. Its fixed-point DSP chips include ADSP2101/2103/2105, ADSP2111/2115, ADSP2126/2162/2164, ADSP2127/2181, ADSP-BF532 and Blackfin series; its floating-point DSP chips include ADSP21000/21020, ADSP21060/21062, as well as Tigershark TS101 and TS201S.
Motorola
Motorola launched its DSP chips relatively late. In 1986, the company launched the fixed-point DSP processor MC56001; in 1990, it launched the floating-point DSP chip MC96002 that is compatible with the IEEE floating-point format.
There are also products such as DSP53611, 16-bit DSP56800, 24-bit DSP563XX and MSC8101.
JEOL
Agere's two series of embedded DSP cores, SC1000 and SC2000, are mainly aimed at telecommunications infrastructure, mobile communications, multimedia servers and other emerging applications.
[page]
DSP chip selection parameters
Depending on the application and design goals, the emphasis of selecting DSP chips is also different. Its main parameters include the following aspects: (1) Operation speed: First, we need to determine the algorithm for digital signal processing. After the algorithm is determined, its operation amount and completion time are roughly determined. According to the operation amount and time requirements, the lower limit of the DSP chip operation speed can be estimated. When selecting a DSP chip, the main criteria for measuring the operation speed of each chip are:
MIPS (Millions of Instructions Per Second), millions of instructions per second, the general DSP is 20~100MIPS, and the TMS320B2XX using very long instruction words is 2400MIPS. It must be pointed out that this is a measure of the computing speed of fixed-point DSP chips. It should be noted that the indicator provided by the manufacturer generally refers to the peak indicator, so a certain margin should be left when designing the system.
MOPS (Millions of Operations Per Second) refers to one million operations per second. The question about this indicator is what is an operation. Usually, operations include address calculation, DMA access data transmission, I/O operations, etc. in addition to CPU operations. Generally speaking, the higher the MOPS, the faster the multiplication-accumulation and operation speed. MOPS can comprehensively describe the performance of the DSP chip.
MFLOPS (Million Floating Point Operations Per Second), million floating point operations per second, is an important indicator for measuring floating point DSP chips. For example, when the main frequency of TMS320C31 is 40MHz, the processing capacity is 40MFLOPS, and when the instruction cycle of TMS320C6701 is 6ns, the single-precision operation can reach 1GFLOPS. Floating point operations include floating point multiplication, addition, subtraction, storage and other operations. It should be noted that the indicator provided by the manufacturer generally refers to the peak indicator, so when designing the system, it should be noted that a certain margin should be left.
MBPS (Million Bit Per Second) is a measure of the data throughput of a bus or I/O port, that is, the bandwidth of a bus or I/O. For example, for TMS320C6XXX, 200MHz clock, 32bit bus, the bus data throughput is 800Mbyte/s or 6400MBPS.
ACS (Multiply-Accumulates Per Second), for example, TMS320C6XXX's multiplication acceleration reaches 300MMACS~600MMACS.
The instruction cycle, that is, the time required to execute an instruction, is usually measured in ns (nanoseconds). For example, the instruction cycle of TMS320LC549-80 when the main frequency is 80MHz is 12.5ns.
MAC time, the time it takes to perform a multiplication and addition operation: Most DSP chips can complete a MAC operation in one instruction cycle.
FFT/FIR execution time refers to the time it takes to run an N-point FFT or N-point FIR program. Since FFT operation/FIR operation is a typical algorithm for digital signal processing, this indicator can be used as a comprehensive indicator to measure chip performance.
Table 1 is a comparison of some DSP chips based on some of the above parameters.
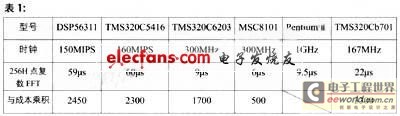
(2) Calculation accuracy: Generally speaking, the calculation accuracy of floating-point DSP chips is higher than that of fixed-point DSP chips, but power consumption and price also increase accordingly. Generally, the word length of fixed-point DSP chips is 16 bits, 24 bits or 32 bits, while the word length of floating-point chips is 32 bits. The accumulator is generally 32 bits or 40 bits. The characteristics of fixed-point DSP are high main frequency, fast speed, low cost and low power consumption. It is mainly used in control, communication, voice/image, consumer electronics and other fields with low computational complexity. For problems that can usually be solved with fixed-point devices, try to use fixed-point devices as much as possible because they are economical, fast, low cost and low power consumption. However, when programming, you should pay attention to the dynamic range of the signal and add calibration operations to the code to limit the dynamic range of the signal. Although we can improve the calculation accuracy by improving the algorithm, doing so will increase the complexity and amount of calculation of the program accordingly. The speed of floating-point DSP is generally lower than that of fixed-point DSP, and its cost and power consumption are higher than those of fixed-point DSP. However, because it uses floating-point data format, its processing accuracy and dynamic range are much higher than those of fixed-point DSP, which is suitable for applications with high computational complexity and high precision requirements. Even for general applications, when programming floating-point DSP, there is no need to consider data overflow and insufficient precision, so programming is more convenient and easier than fixed-point DSP. Therefore, the computational precision requirement is a compromise issue, and an optimal combination point needs to be determined based on experience.
(3) Choice of word length: Generally, floating-point DSP chips use 32-bit data words, while most fixed-point DSP chips use 16-bit data words. However, Motorola's fixed-point chips use 24-bit data words to achieve a compromise between fixed-point and floating-point accuracy. Word length is an important factor affecting cost. It affects the size of the chip, the number of pins, and the size of the memory. When designing, the smallest data word should be selected as much as possible while meeting performance indicators.
(4) Arrangement of on-chip hardware resources such as memory: including memory size, amount of on-chip memory, bus addressing space, etc. The size of on-chip memory determines the chip's operating speed and cost. For example, TI's DSP chips of the same series have different hardware resources such as memory configurations of different types of chips. The requirements for on-chip resources of the DSP chip can be roughly determined by careful analysis of the algorithm program and application goals. Several important considerations are the amount of on-chip RAM and ROM, whether external memory can be expanded, whether the bus interface/interrupt/serial port is sufficient, whether it has A/D conversion, etc.
(5) Development and debugging tools: Complete and convenient development tools and related support software are essential conditions for developing large and complex DSP systems, and play an important role in shortening the product development cycle. Development tools include software and hardware. Software development tools mainly include: C compiler, assembler, linker, program library, software simulator, etc. After determining the DSP algorithm, the written program code is simulated and run through the software simulator to determine the necessary performance indicators. Hardware development tools include online hardware simulators and system development boards. Online hardware simulators are usually JTAG peripheral scanning interface boards that can debug the designed hardware online; before the hardware system is completed, the designed DSP software can be run in real time on development boards with different functions to improve development efficiency. Even in some small-volume products, the development board is directly used as the final product.
(6) Power consumption and power management: Generally speaking, personal digital products, portable devices, and outdoor equipment have special requirements for power consumption, so this is also an issue that should be considered. It usually includes the selection of power supply voltage and power management functions. The power supply voltage is generally relatively low, and the low-voltage power supply of the chip is usually 3.3V, 2.5V, 1.8V, 0.9V, etc. At the same clock frequency, their power consumption will be much lower than that of chips with a 5V power supply voltage. After strengthening the management of the power supply, sleep and wait modes are usually used to save power consumption. For example, TI provides detailed application notes whose functions change with the instruction type and processor configuration.
(7) Price and manufacturer's after-sales service factors: The price includes the price of the DSP chip and the price of the development tools. If an expensive DSP chip is used, its application range will certainly be limited even if its performance is high. However, low-priced chips must have fewer functions, less on-chip memory, and poorer performance, which brings certain difficulties to programming. Therefore, it is necessary to determine a moderately priced DSP chip based on the actual system application. It is also necessary to fully consider factors such as the after-sales service provided by the manufacturer. Good after-sales technical support is also an important resource in the development process.
(8) Other factors: including DSP chip packaging form, environmental requirements, delivery cycle, life cycle, etc.
DSP Application Selection Examples
DSP chip selection for DSP system development for digital control and motion control
The main applications for digital control and motion control include disk drive control, engine control, laser printer control, inkjet printer control, motor control, power system control, robot control, high-precision servo system control, CNC machine tools, etc. Of course, these are mainly applications designed for digital motion control systems. In the control of these systems, not only peripheral circuits specifically used for digital control systems are required, but also the chips must have the general characteristics of digital signal processors.
For example, in the DSP control system for controlling brushless DC motors, two types of control are required during the operation of brushless DC motors. One is speed control, that is, controlling the current provided to the stator coil; the other is phase change control, which changes the stator conduction phase when the rotor reaches the specified position to achieve a change in the stator magnetic field. This control actually implements the mechanism of physical brushes. Therefore, this motor needs a position feedback mechanism, such as Hall elements, photoelectric encoders, or back-electromotive force zero-crossing detection using the trapezoidal back-electromotive force characteristics. Motor speed control also calculates the rotor speed based on the position feedback signal, and then uses control methods such as PI or PID to adjust the PWM duty cycle in real time to achieve stator current regulation. Therefore, the control chip has to perform more calculations. Of course, there are also special brushless DC motor control chips; but generally speaking, in most applications, in addition to motor control, there are always other things such as control and communication that need to be done. Therefore, it is also a good choice to choose a chip with PWM and strong mathematical operation functions.
Motorola's digital signal processor DSP568xx series integrates the fast computing functions of general digital signal processors and the rich peripheral features of microcontrollers, making this series particularly suitable for applications that require strong data processing capabilities and more control functions. The control of brushless DC motors is one of the typical applications of this series of DSPs.
In addition, in the field of digital motion control, TI's TMS320C24x series, TMS320Lx240xx series, and especially TMS320LF2407A have been widely used in control. As a general-purpose programmable microprocessor specially optimized for digital control systems, TMS320LF2407A not only has the characteristics of low power consumption and code confidentiality, but also integrates extremely strong digital signal processing capabilities, and integrates the input, output, A/D conversion, event capture and other peripherals required for digital control systems. Its clock frequency is 40MHz, and the instruction cycle is less than 50ns. It adopts improved Harvard structure and pipeline technology, and can execute several instructions in one instruction cycle.
From the perspective of running speed and accuracy, the above two chips are almost the same, but the debugging development environment (CCS) of TMS320LF2407A is more mature and has more reference materials, which will undoubtedly shorten the development cycle. DSP chip selection for low power consumption, handheld devices, and wireless terminal applications
Compared with other series, the main feature of C54X, C54XX, and C55X is low power consumption, so they are most suitable for personal and portable Internet access and wireless communication applications, such as mobile phones, PDAs, GPS, etc. The processing speed is between 80 and 400 MIPS. C54XX and C55XX generally only have peripherals such as McBSP synchronous serial port, HPI parallel interface, timer, DMA, etc. It is worth noting that C55XX provides an EMIF external memory expansion interface, which can directly use SDRAM, while C54XX cannot use it directly.
Future DSP Development Trends
For a long time, wireless applications will continue to be the driving engine of the programmable DSP market. DSP technology will continue to be the main means of accessing narrowband, broadband or wireless Internet. It is also the key technology of the emerging packet (IP) telephone market. DSP will continue to be the technological driving force of the entire semiconductor industry.
In terms of product applications, currently important DSP application products include mobile phones, modems, HDDs and other personal computers and communication products. However, there are signs that the digital revolution has promoted the widespread application of high-performance DSPs, such as digital cameras, VoIP phones and handheld electronic devices. China's development in consumer electronics is even more eye-catching. Many consumer electronics products require lower-cost and easier-to-use DSP products, such as audio equipment, DVRs, set-top boxes, etc. Overall, DSP applications in the communication field and digital audio and video products will become more and more popular.
Previous article:FPGA Implementation of 2D Lifting Wavelet Transform of Images
Next article:Analysis of DDR2 Interface Design Based on Cyclone III FPGA
Recommended ReadingLatest update time:2024-11-16 20:23
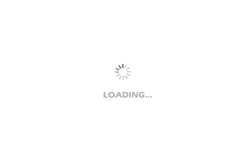
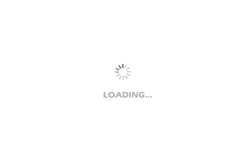
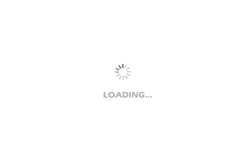
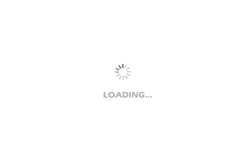
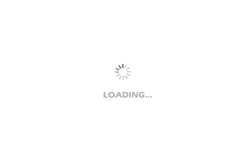
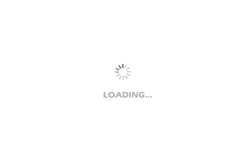
- Popular Resources
- Popular amplifiers
- Huawei's Strategic Department Director Gai Gang: The cumulative installed base of open source Euler operating system exceeds 10 million sets
- Analysis of the application of several common contact parts in high-voltage connectors of new energy vehicles
- Wiring harness durability test and contact voltage drop test method
- Sn-doped CuO nanostructure-based ethanol gas sensor for real-time drunk driving detection in vehicles
- Design considerations for automotive battery wiring harness
- Do you know all the various motors commonly used in automotive electronics?
- What are the functions of the Internet of Vehicles? What are the uses and benefits of the Internet of Vehicles?
- Power Inverter - A critical safety system for electric vehicles
- Analysis of the information security mechanism of AUTOSAR, the automotive embedded software framework
Professor at Beihang University, dedicated to promoting microcontrollers and embedded systems for over 20 years.
- Innolux's intelligent steer-by-wire solution makes cars smarter and safer
- 8051 MCU - Parity Check
- How to efficiently balance the sensitivity of tactile sensing interfaces
- What should I do if the servo motor shakes? What causes the servo motor to shake quickly?
- 【Brushless Motor】Analysis of three-phase BLDC motor and sharing of two popular development boards
- Midea Industrial Technology's subsidiaries Clou Electronics and Hekang New Energy jointly appeared at the Munich Battery Energy Storage Exhibition and Solar Energy Exhibition
- Guoxin Sichen | Application of ferroelectric memory PB85RS2MC in power battery management, with a capacity of 2M
- Analysis of common faults of frequency converter
- In a head-on competition with Qualcomm, what kind of cockpit products has Intel come up with?
- Dalian Rongke's all-vanadium liquid flow battery energy storage equipment industrialization project has entered the sprint stage before production
- Allegro MicroSystems Introduces Advanced Magnetic and Inductive Position Sensing Solutions at Electronica 2024
- Car key in the left hand, liveness detection radar in the right hand, UWB is imperative for cars!
- After a decade of rapid development, domestic CIS has entered the market
- Aegis Dagger Battery + Thor EM-i Super Hybrid, Geely New Energy has thrown out two "king bombs"
- A brief discussion on functional safety - fault, error, and failure
- In the smart car 2.0 cycle, these core industry chains are facing major opportunities!
- The United States and Japan are developing new batteries. CATL faces challenges? How should China's new energy battery industry respond?
- Murata launches high-precision 6-axis inertial sensor for automobiles
- Ford patents pre-charge alarm to help save costs and respond to emergencies
- New real-time microcontroller system from Texas Instruments enables smarter processing in automotive and industrial applications
- micropython update: 2020.12
- [Sipeed LicheeRV 86 Panel Review] The board is not responding
- Use stm32l452 to drive hts221 and stts751 routine
- [National Technology N32WB452 Review] + Basic Function Usage
- Will demand for SiC FETs increase in the future?
- Problems with pressure maintenance of testing machine
- Testing a battery-powered product with a 26K resistor between the battery pads (no battery is soldered at this time!),...
- When TMS320F28377D runs CLA, it shows that Cla1Task2 does not contain frame information
- Application and precautions of Hall elements
- Which one is better to use, the Type-C interface or the MicroUSB interface for mobile phone data cables?