“If you think you have it all figured out, you’re not going fast enough.” — Mario Andretti
Over the years, automobile manufacturers have been challenged by the need for more power. In the early days, cars were powered by 6V batteries until the mid-1950s, when automotive systems evolved to 12V power supplies to meet the permanent need for more power. Not only did automobile manufacturers need to anticipate new power requirements for windows, steering systems, and seats, but more power was also critical for new high-voltage engines.
Recently, OEMs have been forced to rethink how to power vehicles again, spurred by CO2 emissions compliance. While OEMs are launching electric vehicles to meet these standards, there is currently no unified approach to powering the motor and all of the vehicle’s subsystems.
This shortfall is exacerbated by the dramatic increase in power requirements. Internal combustion engine vehicles typically have power supplies between 600W and 3kW. New electrified electric vehicles, hybrids, and plug-in hybrids (xEVs) require 3kW to more than 60kW, 5–20 times more power than before.
A 5- to 20-fold increase will put tremendous pressure on the size, weight, and complexity of the vehicle power delivery network (PDN). These demands will have a negative impact on energy efficiency, reliability, and even comfort and safety, as the increased size and weight will lead to compromises in vehicle features. If automakers continue to use traditional power supply methods, there will simply not be enough space to meet all electrical needs. To meet this challenge, they need to find a lightweight and compact solution that not only mitigates the significant increase in power supply volume, but also has the flexibility to be reused across the entire product line.
In addition to the major technical challenges, OEMs are also putting pressure on themselves to commit to fully electrifying their products within the next 10 years (Figure 1), although the specifics of how to achieve this goal remain an open question. There is no clear path to standardize electrification across the entire EV market. Therefore, while OEMs may share the same goals, the PDNs they design will differ significantly.
Figure 1: By 2030, battery electric vehicles (BEVs) will account for 45% of all xEVs
Accelerating the Electrification Momentum
For many years, electric vehicles accounted for less than 1% of global vehicle production. According to the Credit Suisse Global Automotive Research Center team, this proportion will soar from 11% in 2020 to 62% in 2030, with global vehicle sales reaching 63 million. Nearly half of them (29 million) are expected to be fully electrified.
Figure 2: OEMs have set aggressive goals for electrification of their product lines. These goals are the catalyst for building a world-class xEV platform.
What’s driving the explosive growth of electric vehicles? While emissions compliance and government incentives got the ball rolling, it’s consumer desire that’s creating the massive demand that’s enabling OEMs to move electric vehicles from the niche to the mainstream. These OEMs are now making bold promises. (Figure 2)
OEMs are now electrifying some of the most popular and sought-after vehicles. The GM Hummer, Ford's new Mach E (electric Mustang), and now the flagship F150 light truck (Lightning) are electrifying. These vehicles are attracting the public's attention because of their exciting performance gains and stylish designs.
These new vehicles, with better fast-charging technology and lower maintenance and repair costs, are the catalyst for consumer demand and increased adoption of electric vehicles. Consumers see the value, so the momentum is growing.
High-stakes, high-performance electrification challenges
The number of vehicle platforms, consumer options, different powertrain architectures, and choices of battery and charging configurations all add to the complexity of vehicle electrification that powertrain designers must address.
To optimize vehicle electrification, OEMs need to increase power levels, reduce power delivery network size and weight, and provide better thermal management and reusability. Traditional approaches to designing power systems must transition from complex custom discrete designs to smaller, more flexible, easier to use, and higher density modular solutions.
Accelerating the pace of electrification
To achieve aggressive electrification goals, OEMs must rethink their power architecture approaches. In addition to finding efficient solutions, three major requirements must be met to accelerate and optimize electrification.
1. Power density: Whether designing a fast sports car, a light truck or a family car, OEMs need to provide as much power as possible within a limited space. Cars require compact and efficient power solutions.
2. Flexibility/Scalability: There are many vehicles in each car series that use the same platform, so easy power expansion is very important when modifying the power of models such as sedans, minivans and SUVs that share the same platform.
3. Reusability: To achieve full vehicle electrification, OEMs need to be able to reuse power supply designs between different models to speed up the time to market.
Power Density The size and weight of the power electronics used in various xEV platforms are directly related to vehicle performance, energy efficiency, and battery range. In order to go further and faster, OEMs are actively reducing the size and weight of their power electronics and encouraging R&D teams to reduce vehicle weight.
Figure 3: Reducing the size and weight of the power delivery network is a key factor in the next generation of xEV platforms. For example, the Vicor BCM6135 with a power of 2.5kW can fit in the palm of your hand.
A small bus converter module (BCM6135) from Vicor that is 98% efficient weighs only 68 grams and can be easily combined with EMI filtering, smaller heat sink structures and enclosures to replace a 25 kg 48V battery. This not only frees up a lot of space and payload weight, but also saves 125 to 250 Euros in weight reduction R&D costs. The high-density power module converts a 400-800V main battery to 48V in a small 61 × 35 × 7 mm package, delivering over 2kW of power with a power density exceeding 4.3kW/in3 (Figure 3)
Flexibility/Scalability OEM designers standardize as many subsystems as possible that are integrated into the vehicle to save time, money and resources. However, each subsystem is slightly different as different levels of vehicle interior require different designs. As the electrification of the vehicle progresses, power system design teams are challenged with constantly changing power delivery requirements. The flexible, scalable and modular power system design approach provided by Vicor allows designers to implement standardized solutions across a variety of powertrains such as SUVs, vans or light trucks.
For example, a van might have a power requirement of 5kW, but powering a light truck with a short bar, tow and plow, and alternator might require 10kW. Using the same platform and a little extra space, engineers can quickly add or remove pre-qualified components from the array to increase or decrease power.
In addition, the modular design can also realize a distributed power architecture through a 48V bus, providing greater flexibility. The power module can be arranged in a convenient location for local 48V/12V conversion, either behind the storage box, near the trunk, or next to each wheel. Deploying a modular solution not only provides design flexibility, but also provides a better way to optimize power supply changes and manufacturing processes.
Figure 4 The impact of modularity is best illustrated by the fact that four high-power density modules can be combined in more than 300 different ways to support different power requirements and a large number of different types of loads.
One of the most common delays in the automotive development process is the approval of electronic components used in the car. Sometimes this process can take up to two to three years to get through before a single component can get the production part approval process. R&D teams often look for ways to reuse existing components to save development and approval time, saving valuable resources.
For example, a traditional PDN based on discrete DC-DC converter designs may consist of more than 200 bulky components, whereas Vicor's advanced technology provides only a single high-density power module. For engineering teams, the time savings of certifying one module versus more than 200 individual components to achieve the same functionality is significant.
In addition, the Vicor modular approach allows engineers to implement approximately 300 power delivery combinations by using three or four different types of scalable building blocks. (Figure 4) Altogether, this design approach can save hundreds of hours of time and resources, helping OEMs stay ahead in the race to electrification.
Final push
OEMs are facing a huge challenge to not only cross the finish line of electrification, but also to design in xEV fleets that deliver long-term benefits. Adopting a modular approach to power system design can provide a competitive advantage in this important race for market share. Innovation is needed now in the form of new architectures and topologies that not only deliver the highest performance today, but can also be reused and reconfigured later.
Traditional power supply designs cannot provide this level of flexibility and ease of use. For OEMs to achieve their aggressive electrification goals, a modular approach is best used that not only delivers the highest performance at multiple critical levels, but also helps them meet the most complex xEV power needs.
YS Jun is currently the Director of APAC Automotive Business Development at Vicor. Email: YJun@vicr.com
Vicor Corporation is a leader in high-performance power modules, committed to solving our customers' toughest power challenges, helping them innovate and maximize system performance. Our easy-to-use power modules provide extreme density and efficiency to enable advanced power delivery networks from the power source to the point of load. Headquartered in Andover, Massachusetts, USA, Vicor provides unparalleled power conversion and delivery technologies to customers around the world.
Previous article:New ultra-low-loss diode for light-duty vehicle generators
Next article:Can autonomous driving learn? Zhiji Auto IM AD, the evolving intelligent driving
Recommended ReadingLatest update time:2024-11-15 16:27
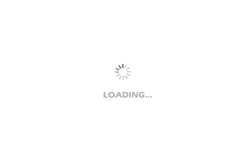
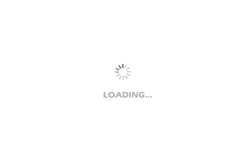
- Popular Resources
- Popular amplifiers
- A new chapter in Great Wall Motors R&D: solid-state battery technology leads the future
- Naxin Micro provides full-scenario GaN driver IC solutions
- Interpreting Huawei’s new solid-state battery patent, will it challenge CATL in 2030?
- Are pure electric/plug-in hybrid vehicles going crazy? A Chinese company has launched the world's first -40℃ dischargeable hybrid battery that is not afraid of cold
- How much do you know about intelligent driving domain control: low-end and mid-end models are accelerating their introduction, with integrated driving and parking solutions accounting for the majority
- Foresight Launches Six Advanced Stereo Sensor Suite to Revolutionize Industrial and Automotive 3D Perception
- OPTIMA launches new ORANGETOP QH6 lithium battery to adapt to extreme temperature conditions
- Allegro MicroSystems Introduces Advanced Magnetic and Inductive Position Sensing Solutions
- TDK launches second generation 6-axis IMU for automotive safety applications
- LED chemical incompatibility test to see which chemicals LEDs can be used with
- Application of ARM9 hardware coprocessor on WinCE embedded motherboard
- What are the key points for selecting rotor flowmeter?
- LM317 high power charger circuit
- A brief analysis of Embest's application and development of embedded medical devices
- Single-phase RC protection circuit
- stm32 PVD programmable voltage monitor
- Introduction and measurement of edge trigger and level trigger of 51 single chip microcomputer
- Improved design of Linux system software shell protection technology
- What to do if the ABB robot protection device stops
- Huawei's Strategic Department Director Gai Gang: The cumulative installed base of open source Euler operating system exceeds 10 million sets
- Download from the Internet--ARM Getting Started Notes
- Learn ARM development(22)
- Learn ARM development(21)
- Learn ARM development(20)
- Learn ARM development(19)
- Learn ARM development(14)
- Learn ARM development(15)
- Analysis of the application of several common contact parts in high-voltage connectors of new energy vehicles
- Wiring harness durability test and contact voltage drop test method
- 【National Technology N32G430】2 FFT application and DWT counter use
- LSM6DSOX unboxing and experience "Port not open & not supported" problem solution
- Write the makefile step by step
- NUCLEO_G431RB Review - SPI Operation of SSD1306, OLED
- FPGA/CPLD popular data download collection
- 2022 Digi-Key Innovation Design Competition + Unboxing
- EEWORLD University Hall----Radiation Hardness Assurance (RHA) Process of TI Space Products
- How do I input an external clock signal into CC2530?
- Playing with Zynq Serial 29——[ex51] Making the boot file BOOT.bin of the naked running program
- SPI transmission