By Mike Jones. Marketing Director, LAN Solutions, Micrel
The adoption of diagnostics over IP via ISO 13400 has made Ethernet widely used in today’s automobiles, allowing for faster reprogramming than the physical interface of standard Ethernet. However, challenges remain as automakers choose it as the ubiquitous in-vehicle network bus. Advanced driver assistance systems (ADAS), including camera systems, are one of the applications where the industry is looking to maximize the benefits of Ethernet.
Why should you consider Ethernet-based connectivity over analog or LVDS approaches? Especially when both the camera and central unit processing costs are higher (Figure 1). There are many key factors beyond this metric that ultimately provide lower cost and higher performance.
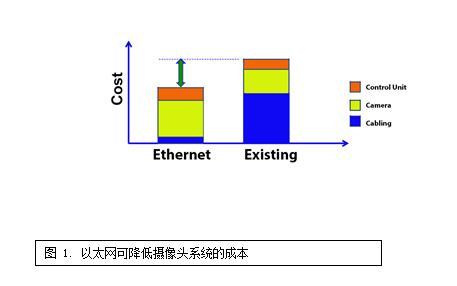
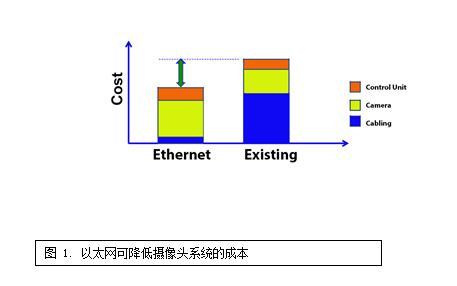
One key factor is that the ability to use low-cost unshielded twisted pair cables can significantly reduce cabling costs. In addition, Power over Ethernet (PoE) uses standards-based 100BASE-TX Ethernet, eliminating the need for additional cables. However, the real value of Ethernet goes beyond reducing the bill of materials. The ultimate goal of Ethernet is to provide a single, ubiquitous in-vehicle network with seamless, cross-domain communication - applying common data flows and physical media (cables) throughout the entire automotive domain, including chassis, powertrain, body, infotainment, and ADAS. Now, information sharing within and across domains can be supported on a single network without bridging, which can greatly reduce costs and complexity. In short, Ethernet is a network technology; whether it is for the automotive field, consumers, enterprises, or industries, this is its greatest value and the reason why it can reduce costs in any market.
In-vehicle connectivity is the most significant challenge in in-car applications, so ADAS camera design exemplifies the main challenges it faces:
1. Image quality is directly affected by the thermal noise generated by the camera. Factors such as improved thermal dissipation and lower power are critical to achieving the required performance in the absence of required space constraints.
2. Low noise is a must as electrical noise can also degrade sensor image quality. Another challenge in meeting automotive EMC emissions requirements arises when trying to use the required low-cost unshielded cables.
3. The quality and reliability requirements for the automotive market must be upheld. Automotive is a demanding environment, with different considerations for passenger vehicles, commercial vehicles, and industrial vehicles.
4. The need to deploy sensors throughout the vehicle is greater than ever, resulting in increasing space constraints for such applications. This demand is further driven by the strong demand for zero fatal accidents brought about by various ADAS applications. For example, collision avoidance, traffic lights, road signs and pedestrian recognition.
Solution: Ethernet-based ADAS
Merit has teamed up with Silicon Micro Sensors (SMS), a specialist in automotive sensors, to design a "production-ready" solution for the most demanding automotive and industrial applications. Features include: a megapixel (720p) high dynamic range (HDR) camera, a field of view from 55° to 190°, MJPEG video compression, Ethernet AVB and active Ethernet support, low-cost unshielded twisted pair, IP68/IP6k9 compliance, waterproof, scratch-proof, and fog-proof. The camera is suitable for passenger vehicles, commercial vehicles, and industrial vehicles, with applications including panoramic and rear-view, side and mirror replacement, traffic signs, blind spots, pedestrian detection, and lane departure assistance.
This solution clearly demonstrates that standard Ethernet can meet the needs of ADAS cameras. This solution uses Quiet-WIRE™ Ethernet and Auto-PoE technology and is one of a series of designs for ADAS. (Figure 2)
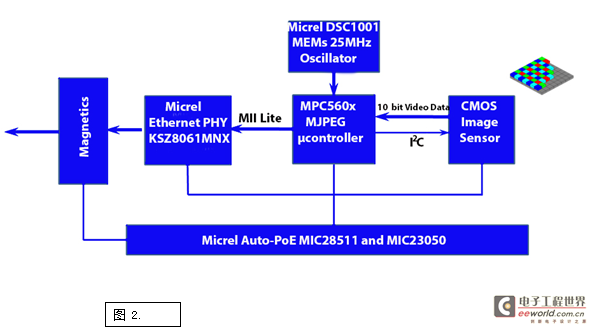
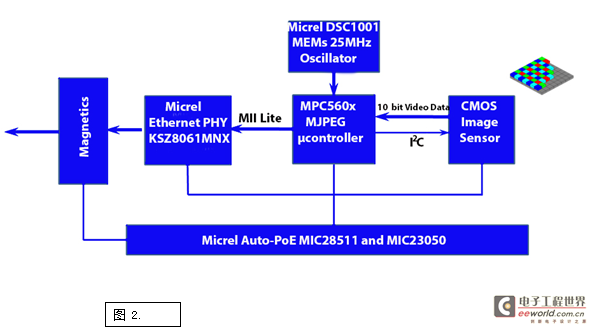
Two options are available: Aptina AR0132AT or OmniVision OV10635 image sensors. Freescale’s MPC5604 processor provides MJPEG compression based on incoming YUV digital image data and connects to the Micrel KSZ8061 Quiet-WIRE™ 100BASE-TX Ethernet PHY via a media independent interface (MII). Micrel’s DS1001 MEMS oscillator provides system timing and uses optimized automotive active Ethernet Auto-PoE for power management.
Ethernet faces challenges head on
The Ethernet physical layer offers a range of benefits that meet the needs of ADAS camera systems. One of the benefits of using a standards-based automotive Ethernet solution is that it provides a minimal standard bill of materials (BoM) that is application-independent (Figure 3). This enables economies of scale that exceed any vehicle-specific solution and enables a multi-supplier model that provides greater choice and lower costs.
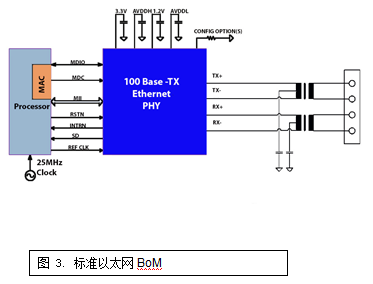
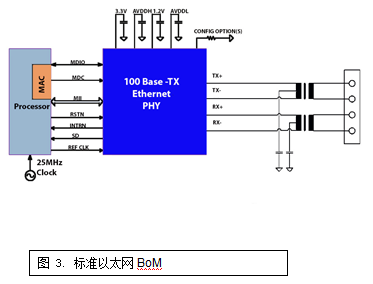
The automotive industry’s smallest PHY is provided by the Micrel KSZ8061 Quiet-WIRE™ 100BASE-TX Ethernet transceiver, which measures just 5mm x 5mm. Minimal power supply filtering must be ensured, but uniquely, the line interface between the PHY transceiver and the magnetics requires no additional passive components. This improves signal integrity while reducing cost and printed circuit board space.
Qualified automotive Ethernet magnetics have become more widely available in recent years, and standard Ethernet magnetics can also be used. Here, we used TDK's latest Ethernet magnetics, the ALT4352 series, which is a surface mount, machine-wound, and reduced-size solution with a maximum height of only 2.9mm, making it ideal for space-constrained camera modules. Machine-wound magnetics are not only lower cost, but also more accurate (relative to traditional hand winding) and provide more functional and consistent performance.
Use of Active Ethernet
100BASE-TX magnetics are just as important to achieve performance as they are to deliver power. According to the IEEE 802.3af/at “phantom powering” method, the current practice of installing additional cables to power remote sensors is no longer necessary, and power can be provided by the DC voltage provided by the center tap of the magnetics. This approach can also be further optimized when used in automotive applications and provides all the benefits without any additional system cost.
First, since the car wiring is fixed, a bridge rectifier is no longer required. Second, a redundant active Ethernet controller configuration is used (which can significantly reduce costs). Since the powered device (PD) - in this case, the camera is fixed and the power budget is known, there is no need for a relatively expensive controller to coordinate power requirements with the power supply equipment (PSE). Only a standard DC-DC regulator is required to implement the camera power management solution (Figure 4). The Micrel MIC28511 60Vin 3A synchronous buck regulator with Hyper Light Load™ technology can provide a stepped-down primary voltage to ensure high efficiency operation in low output power operations such as standby.
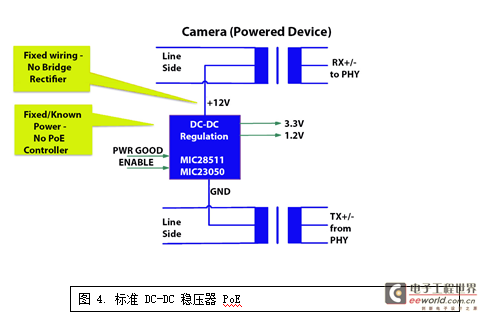
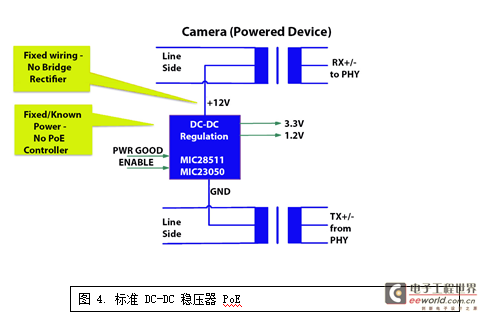
Although optimization and cost-effectiveness can be achieved, standard automotive Ethernet PoE still provides additional benefits brought by the "phantom power" method. Common-mode noise rejection is provided on the camera (PD side); noise emitted by the PSE (ECU) or extracted along the twisted pair cable will be coupled with the differential Ethernet signal as common-mode noise, thereby eliminating it. In addition, galvanic isolation between the camera (PD) and ECU (PSE) grounds prevents radiating ground loops due to different potentials; this problem has been common. Interoperability is also achieved by connecting to any other IEEE 802.3af/at PSE.
100BASE-TX Ethernet offers the lowest power PHY technology on the market today. It reduces power and cost by up to three times compared to Gigabit technology based solutions. The KSZ8061 support of IEEE 802.3az Energy Efficient Ethernet (EEE) provides an additional benefit to the camera, as the PHY can transition to a low power sleep mode when idle (e.g. when not transmitting video traffic). This can reduce power consumption by more than 50%. The KSZ8061 Ethernet PHY also offers an industry best-in-class ultra-low standby current of less than 1uA, which is ideal for all battery applications.
In addition, the KSZ8061 PHY provides a unique signal detection output socket that can be used to indicate the presence of an active link partner (Figure 5). The signal detection circuit can automatically activate and wake up the PHY standby mode. In addition, this output socket can also be used to shut down the processor and sensors for power management and provide remote standby and wake-up currents of less than 1uA for camera modules.
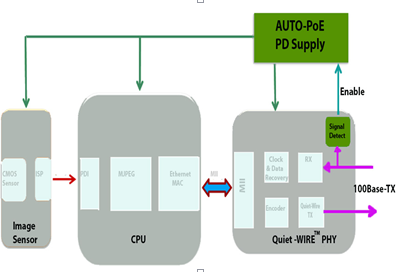
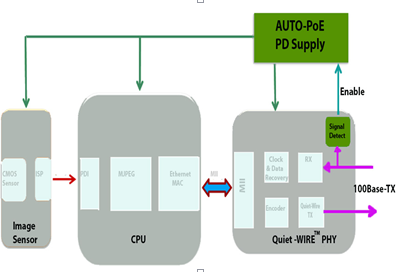
This remote shutdown solution provides important benefits:
Fully interoperable with any Ethernet vendor link partner (in ECU) Reduced standby power consumption
Alternative approaches using special waveforms/sequences often require proprietary implementations, which limits their practical applications. In the consumer space, a good example is the vendor-driven Wake-on-LAN (WoL) approach. In fact, this approach is rarely used in this space. From a standby power perspective, implementing the detection circuit on the physical layer requires less signal processing and therefore consumes less power. In this alternative example, WoL still requires the PHY and parts of the MAC layer to remain powered all the time, resulting in standby power consumption that is about a thousand times higher.
Quiet-WIRE™ technology uses the KSZ8061 Ethernet PHY, which reduces EMI line radiation compared to unshielded twisted pair and meets automotive OEM standards. Low-cost cables such as CAN or FlexRay can be deployed. Cables can also be hand-made, with each connector equipped with a maximum of 5cm of untwisted wire section without the use of a jacket, providing the lowest cost.
Active Ethernet common-mode noise suppression and isolated camera grounding reduce electrical noise to optimize camera sensor image quality. This also includes reduced thermal noise due to the KSZ8061 low-power 100BASE-TX technology. Reduced heat dissipation not only improves sensor performance, but also enables greater stability and fuel efficiency.
The Quiet-WIRE™ technology used in the camera solution not only reduces radiated emissions, but also provides better noise immunity due to its superior current injection performance. The PHY transceiver showed absolutely no errors when injected with 200mA noise current over the entire frequency range of 1MHz to 400MHz, exceeding OEM limits.
Even with Quiet-WIRE radiation filtering enabled, the enhanced PHY transceiver design in the KSZ8061 provides error-free cable range down to 130 meters. Such performance is very beneficial in industrial and commercial vehicles, where interference immunity and cable range are often longer than the maximum automotive wiring length of 15 meters.
To meet the needs of safety-critical ADAS applications such as rearview cameras, the KSZ8061 can power up and link within 20ms without processor intervention. In addition, the KSZ8061's unique transceiver signal quality indicator (SQI) can also continuously monitor the quality of the wiring harness in real time.
The camera clock timing is provided by a Micrel DSC1001 MEMS 25MHz oscillator. MEMS technology is well suited for this application due to its superior frequency temperature stability, providing up to 20 times the mean time before failure and 500 times greater shock resistance than crystal oscillators (Figure 6). All devices used in the camera design are either fully qualified or able to meet the automotive AEC-Q100 standard.
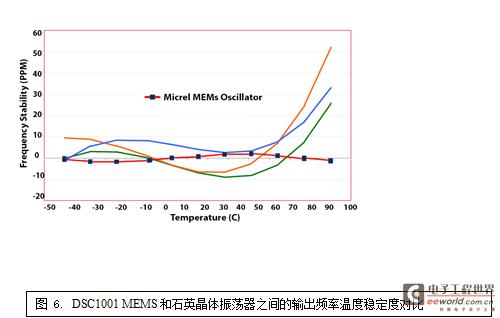
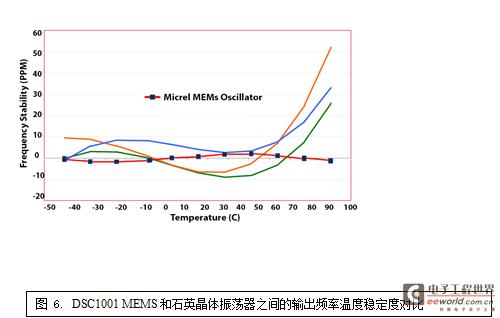
Summarize
The growth of ADAS in vehicles is driven by legislation from governments around the world that is committed to improving road safety. The US National Highway Traffic Safety Administration (NHTSA) recently mandated that all new vehicles meet new rear-view range standards starting May 1, 2018, in an effort to prevent an average of 210 deaths and 15,000 injuries each year. Europe is also planning similar initiatives to achieve its mission of zero accidents on the road.
The challenges of ADAS, especially camera sensors, are extremely demanding. They must have higher power dissipation, lowest electrical noise, and fit into extremely limited spaces, while also meeting stringent vehicle safety, quality, and reliability requirements. Standard Ethernet has proven to not only overcome these challenges, but can even provide additional benefits.
When examining these benefits, it is clear that standard Ethernet not only meets the needs of ADAS, but also solves the cost challenge. To be successfully deployed in the market, all solutions need to be both commercially and technically feasible. This is the key factor that has enabled Ethernet to successfully cross multiple markets: it can provide network performance at the lowest total cost of ownership.
The camera modules mentioned in this article can be purchased from Silicon Micro Sensors as part of a demonstration kit that includes four camera modules that can be connected via an Ethernet switch for demonstration on a computer or laptop. The Video Analyzer Advanced Development and Analysis Framework software is also available, which, in addition to object recognition, allows control, data stream storage, display, recording and playback of up to four cameras.
Mike Jones:
Mike Jones has 25 years of experience in the semiconductor industry and is responsible for the marketing of automotive and industrial products for Micrel LAN Solutions. Mr. Jones holds a Master of Science degree with first class honours in Electronic Systems Engineering from Aston University in Birmingham, UK. He has also authored numerous technical magazine articles and has been published in a number of technical and industrial publications worldwide.
Previous article:How to find the faulty node of CAN bus in one minute
Next article:How Shanghai GM finds the faulty node of CAN bus in one minute
- Popular Resources
- Popular amplifiers
Recommended Content
Latest Automotive Electronics Articles
- A new chapter in Great Wall Motors R&D: solid-state battery technology leads the future
- Naxin Micro provides full-scenario GaN driver IC solutions
- Interpreting Huawei’s new solid-state battery patent, will it challenge CATL in 2030?
- Are pure electric/plug-in hybrid vehicles going crazy? A Chinese company has launched the world's first -40℃ dischargeable hybrid battery that is not afraid of cold
- How much do you know about intelligent driving domain control: low-end and mid-end models are accelerating their introduction, with integrated driving and parking solutions accounting for the majority
- Foresight Launches Six Advanced Stereo Sensor Suite to Revolutionize Industrial and Automotive 3D Perception
- OPTIMA launches new ORANGETOP QH6 lithium battery to adapt to extreme temperature conditions
- Allegro MicroSystems Introduces Advanced Magnetic and Inductive Position Sensing Solutions
- TDK launches second generation 6-axis IMU for automotive safety applications
MoreSelected Circuit Diagrams
MorePopular Articles
- LED chemical incompatibility test to see which chemicals LEDs can be used with
- Application of ARM9 hardware coprocessor on WinCE embedded motherboard
- What are the key points for selecting rotor flowmeter?
- LM317 high power charger circuit
- A brief analysis of Embest's application and development of embedded medical devices
- Single-phase RC protection circuit
- stm32 PVD programmable voltage monitor
- Introduction and measurement of edge trigger and level trigger of 51 single chip microcomputer
- Improved design of Linux system software shell protection technology
- What to do if the ABB robot protection device stops
MoreDaily News
- Huawei's Strategic Department Director Gai Gang: The cumulative installed base of open source Euler operating system exceeds 10 million sets
- Download from the Internet--ARM Getting Started Notes
- Learn ARM development(22)
- Learn ARM development(21)
- Learn ARM development(20)
- Learn ARM development(19)
- Learn ARM development(14)
- Learn ARM development(15)
- Analysis of the application of several common contact parts in high-voltage connectors of new energy vehicles
- Wiring harness durability test and contact voltage drop test method
Guess you like
- What do you most expect humanoid robots of the future to do: replace humans, serve humans, or surpass humans?
- TMS320VC33 Digital Signal Processor Data Sheet
- Is MOV an assembly instruction? The book I am reading now is called 51 Single-Chip Microcomputer C Language Application Development Trinity Practical Explanation. . .
- How to read circuit diagrams.pdf
- [Instrument Sharing] How to use an oscilloscope to monitor the waveform of a low-frequency signal? Adjusting these three keys is enough
- How does the MK60 serial port receive a string of indefinite length?
- Microchip live broadcast at 10:30 this morning | ADAS platform trusted root, learn technology and win gifts!
- Low-cost, high-precision digital control solution for battery testing equipment
- Random errors in XINTF read and write of F28335
- STM32L431 strange assignment problem?