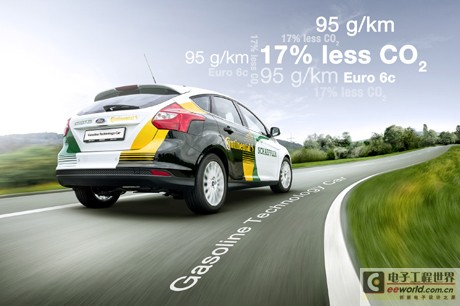
大陆(Continental)、舍弗勒(Schaeffler)利用第35届日内瓦汽车讨论会的机会,展示了合作研发的汽油技术汽车GTC。GTC项目显示微混技术广泛应用在汽车上,燃油消耗量会出现显著下降;与搭载三缸1.0升汽油发动机的高效能福特福克斯EcoBoost车型相比,采用微混技术可以额外减少17%的二氧化碳排放量。
To achieve the goal of mild hybridization, engineers from Continental and Schaeffler have brought out their core technologies and integrated and systemized them into the GTC model. The research and development results of the GTC are the extension of the potential of a previous mild hybrid model, and the engine equipped in the earlier car was nominated for the World Engine Award in 2012 and 2013 for its efficiency and performance. Thanks to the interaction between the various components and various advanced technologies in the GTC model, drivers can personally experience the vehicle's excellent fuel economy and excellent controllability. The two automotive suppliers emphasized that the GTC is made up of a large number of cutting-edge technologies, but the final effect is greater than the simple sum of the components. In other words, it is a one plus one equals three effect.
The two partners in the project optimized various parts of the GTC model's powertrain, replacing the relevant components of the reference model with appropriately adjusted Continental injectors and engine control units, and a large number of innovative components and technologies were also applied to the vehicle. The core of all the components is the Continental 48-volt Eco Drive energy-saving system as a mild hybrid device, and the Schaeffler electronic clutch as a power transmission device, as well as the related thermal management module. In addition, some measurement methods were supplemented to reduce friction losses in the engine and electrically heated catalytic converter. By using these components and intelligent management strategies, the GTC prototype not only improved fuel economy by 17%, but also helped exhaust emissions meet the Euro 6c standard limits that will be implemented in 2017.
The 1.0-liter three-cylinder engine in the GTC model uses an improved precision ignition timing optimization control strategy, but in order to further improve the vehicle's drivability and allow additional hybrid power to be added to the power system, the vehicle is equipped with an independent secondary drive unit - the 48-volt Eco Drive energy-saving system. The electric motor in this system uses an integrated decoupling tensioner, and the electric traction motor/generator is connected to the internal combustion engine using a modified belt drive. The DC-to-DC converter helps to freely convert the current and voltage between the vehicle's 12 volts and the lithium-ion battery's 48 volts. In mild hybrid drive mode, the engine can provide additional power with electric energy at low speeds, while in supercharged vehicles, the turbo intervention at low speeds is often delayed, resulting in a response lag; the high-efficiency 48-volt energy recovery system is the basic element for providing driving power with electric energy. In the new European driving cycle, the total amount of kinetic energy that the GTC can recover is close to twice the amount of electricity required by the vehicle's electrical system.
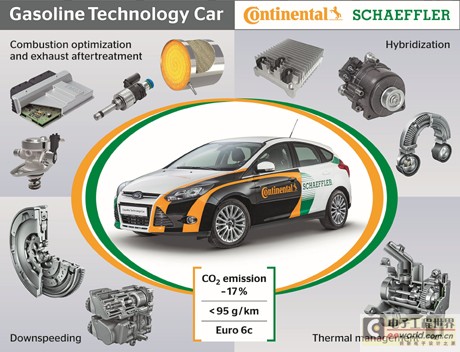
The GTC prototype is equipped with a six-speed manual transmission. The driving strategy of coasting in neutral is also a good way to save energy. The Schaeffler electronic clutch makes this control method possible. The device automatically separates the engine and the transmission system when the vehicle is coasting, so engine braking will no longer occur, and more kinetic energy can be used to recover. The recovered energy in turn helps to improve the efficiency of other devices. For example, the electrically heated catalytic converter uses the energy recovered from the previous driving cycle to quickly reach the operating temperature from the cold start temperature.
In addition, Schaeffler uses a separate cooling structure with a rotary slide valve to help GTC achieve graded heat management. The engine can be temporarily separated from the cooling cycle as needed, so as to obtain the required temperature in the shortest possible time or maintain a certain temperature value for as long as possible. The rapid heating strategy ultimately helps to reduce engine friction losses. The above technology improves driving efficiency. As a far-sighted control strategy, it is also a good choice to shut down the cooling system in a timely manner in conditions such as downhill where energy can be recovered.
The emergence of mild hybrid components increases the complexity of the power system. The Continental standardized engine control unit used by the GTC is used to simplify the system and improve the vehicle's controllability. The engine control unit is at the forefront of technology, and its open automotive system architecture is very flexible, supporting various partition schemes and electronic topologies related to hybridization and electrification.
When the driver, the optimized components and the vehicle characteristics are in harmony, the car can achieve the highest performance value when it is matched with a manual transmission. For this reason, the downshift point selected by the engine control unit is crucial; the appropriate shift point ensures that the additional electric drive torque does not have any negative impact on driving performance and can improve fuel economy during driving.
Previous article:Honeywell's new technology solves two "chronic problems" of turbocharging
Next article:New dual-carbon battery charges 20 times faster than lithium batteries
- Popular Resources
- Popular amplifiers
- A new chapter in Great Wall Motors R&D: solid-state battery technology leads the future
- Naxin Micro provides full-scenario GaN driver IC solutions
- Interpreting Huawei’s new solid-state battery patent, will it challenge CATL in 2030?
- Are pure electric/plug-in hybrid vehicles going crazy? A Chinese company has launched the world's first -40℃ dischargeable hybrid battery that is not afraid of cold
- How much do you know about intelligent driving domain control: low-end and mid-end models are accelerating their introduction, with integrated driving and parking solutions accounting for the majority
- Foresight Launches Six Advanced Stereo Sensor Suite to Revolutionize Industrial and Automotive 3D Perception
- OPTIMA launches new ORANGETOP QH6 lithium battery to adapt to extreme temperature conditions
- Allegro MicroSystems Introduces Advanced Magnetic and Inductive Position Sensing Solutions
- TDK launches second generation 6-axis IMU for automotive safety applications
- LED chemical incompatibility test to see which chemicals LEDs can be used with
- Application of ARM9 hardware coprocessor on WinCE embedded motherboard
- What are the key points for selecting rotor flowmeter?
- LM317 high power charger circuit
- A brief analysis of Embest's application and development of embedded medical devices
- Single-phase RC protection circuit
- stm32 PVD programmable voltage monitor
- Introduction and measurement of edge trigger and level trigger of 51 single chip microcomputer
- Improved design of Linux system software shell protection technology
- What to do if the ABB robot protection device stops
- Download from the Internet--ARM Getting Started Notes
- Learn ARM development(22)
- Learn ARM development(21)
- Learn ARM development(20)
- Learn ARM development(19)
- Learn ARM development(14)
- Learn ARM development(15)
- Analysis of the application of several common contact parts in high-voltage connectors of new energy vehicles
- Wiring harness durability test and contact voltage drop test method
- From probes to power supplies, Tektronix is leading the way in comprehensive innovation in power electronics testing
- [Review of the RTT of the Bluesight AB32VG1 RISC-V board] + LED and button control
- Application of wireless pressure transmitter in the field of Internet of Things!
- Made an integrated offline robotic arm controller
- Sensor detection circuit advice
- Today's live broadcast: Keysight Technologies' high-speed bus PCIe5.0 technology development and testing sharing
- I want to know the specific communication process between the external 24C02 EEPROM and the microcontroller. Which forum friend can tell me? Thank you.
- Failed to run Verilog with Cypress PSoC
- ARM programming mode and 7 modes
- #Idle Market# 4G module
- How to learn drivers, Linux kernel and various common peripherals