Thermocouples are widely used in industry because of their high measurement accuracy, economical price, easy availability and wide temperature measurement range. It consists of two different metal or metal alloy wires welded together (usually called the hot end). The output voltage of the thermocouple is the voltage difference between the two wire ends (the other end is usually called the cold end), which must be maintained at a known temperature. Thermocouple voltage is a combination of the Seebeck (around 1921), Peltier (around 1834) and Thompson (around 1851) effects.
The terms hot junction and cold junction come from the history of applications. In fact, depending on the specific application, the cold junction temperature may be higher than the hot junction. In this case, the thermocouple outputs a voltage with opposite polarity. Therefore, the thermocouple measures the difference between the hot and cold junction temperatures, not the absolute temperature of the cold junction.
The output voltages for thermocouples made of different metals or alloys have been standardized in a table. Standard metal pairs are represented by capital letters, for example, K for a nickel-cadmium thermocouple, and the data listed in the table assume a cold junction temperature of 0°C.
To obtain the absolute temperature of the hot junction, the cold junction temperature must be measured and the thermocouple output adjusted accordingly. This technique is called cold junction compensation. In the mid-1800s, when thermocouples first came into use, absolute temperature measurements required keeping the cold junction at the temperature of an equilibrium mixture of ice and distilled water to establish a true 0°C reference point.
Thermocouple temperature sensors require special cables and connectors made of the same material as the thermocouple wire. Therefore, commercial thermocouples are available in a variety of packages, sizes, and types, and also come with a complete selection of cables, connectors, and accessories2,3.
The cold junction isotherm is located at the input of the thermocouple signal processing module, which is usually mounted on a base plate made of high thermal conductivity material. The thermal conductivity of copper is 381W/m°K (the same magnitude of change per degree, whether in Celsius or Kelvin). The input connection must be electrically isolated, but thermally conductive to the base plate. Ideally, the entire signal processing module should be kept in the same temperature environment.
The signal processing circuit consists of a low-voltage DC amplifier (thermocouple signal range is µV/°C), a temperature sensor, a cold-junction compensation circuit, an internal reference ADC, a thermocouple open-circuit detector, an alarm indicator, and a digital output interface. All of these functions are integrated into a small IC, such as the MAX6674 and MAX6675, which only requires external connections to the thermocouple and power supply. The serial port output represents the temperature of the thermocouple detection point.
The MAX6674/MAX6675 internal thermocouple-to-digital converter circuit is ratiometric to nickel-cadmium (Type K) thermocouples. The MAX6674 measures 0 to +128°C with a resolution of 0.125°C; the MAX6675 measures 0 to 1024°C with a resolution of 0.25°C. Both ICs interface to a microcontroller or similar local intelligent circuit through an SPI™-compatible interface. If the sensing point is far from the controller, the thermocouple signal should be digitized near the sensing point.
Like other low voltage circuits, thermocouple signal processing circuits are very sensitive to EMI. Thermocouple leads are often exposed to EMI (the level of interference noise picked up by the leads is proportional to the lead length). EMI increases the uncertainty of the received signal and reduces the accuracy of the temperature measurement. For this environment, the use of special thermocouple connection cables is expensive, and if other cables are selected, it is difficult to determine the test temperature in the actual environment.
In order to minimize the noise, a control circuit can be used near the detection point, a remote control circuit can be added near the detection point to provide local intelligent management, and complex signal filtering and cable shielding can be introduced. Figure 1 provides a better design solution to digitize the thermocouple output near the detection point.
Figure 1. Providing power at the far end of a 3000-foot cable.
The MAX6674/MAX6675 quantize the thermocouple output close to the sensing point to minimize EMI.
The SPI interface of the MAX6674/MAX6675 is driven by a local pulse timing generator (IC2 and IC3). IC2 and IC3 force the MAX6674/MAX6675 to generate asynchronous serial output data at 4800 baud and four characters per second. The character structure is: 1 start bit, 11 data bits, and 1 stop bit (MAX6675 uses 13 data bits). For the MAX6674, the 11 data bits include 10 bits of direct binary numbers representing temperature data (MSB first) and 1 thermocouple open circuit alarm bit. The MAX6675 provides 12 bits of data and 1 alarm.
A stable crystal oscillator ensures accurate data transmission baud rate. To ensure correct circuit operation, the thermocouple sensing point must be electrically isolated from the circuit, and the MAX6674/MAX6675 must be maintained within the -20°C to +85°C operating temperature range at all times.
The circuit is connected to a remote power supply and data receiver via a twisted pair cable, which powers the circuit and transmits data to the data receiver. The temperature measurement is implemented by the internal 10-bit ADC of the MAX6674/MAX6675, and the data is sent serially to the cable. The temperature data shown in Figure 2 is generated by the MAX6674 and quantized through 3000 feet of twisted pair cable. These data show that the thermocouple is in good working condition and the measured temperature is 21.875°C.
Figure 2. The serial data word received at the data receiver A and B in Figure 1.
The data represents a temperature of 21.875°C measured by the thermocouple at the other end of the cable.
For additional information, refer to the MAX6674/MAX6675 data sheet, thermocouple data sheets1, sensor data sheets from temperature sensor and accessory manufacturers2,3, and technical standards that specify thermocouples4,5,6.
Previous article:Principle and application circuit of pulse circuit composed of photoelectric coupler
Next article:Low Power High Slew Rate CMOS Analog Buffer
Recommended ReadingLatest update time:2024-11-17 06:01
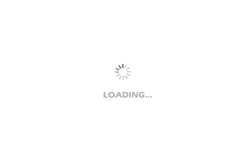
- High signal-to-noise ratio MEMS microphone drives artificial intelligence interaction
- Advantages of using a differential-to-single-ended RF amplifier in a transmit signal chain design
- ON Semiconductor CEO Appears at Munich Electronica Show and Launches Treo Platform
- ON Semiconductor Launches Industry-Leading Analog and Mixed-Signal Platform
- Analog Devices ADAQ7767-1 μModule DAQ Solution for Rapid Development of Precision Data Acquisition Systems Now Available at Mouser
- Domestic high-precision, high-speed ADC chips are on the rise
- Microcontrollers that combine Hi-Fi, intelligence and USB multi-channel features – ushering in a new era of digital audio
- Using capacitive PGA, Naxin Micro launches high-precision multi-channel 24/16-bit Δ-Σ ADC
- Fully Differential Amplifier Provides High Voltage, Low Noise Signals for Precision Data Acquisition Signal Chain
- Innolux's intelligent steer-by-wire solution makes cars smarter and safer
- 8051 MCU - Parity Check
- How to efficiently balance the sensitivity of tactile sensing interfaces
- What should I do if the servo motor shakes? What causes the servo motor to shake quickly?
- 【Brushless Motor】Analysis of three-phase BLDC motor and sharing of two popular development boards
- Midea Industrial Technology's subsidiaries Clou Electronics and Hekang New Energy jointly appeared at the Munich Battery Energy Storage Exhibition and Solar Energy Exhibition
- Guoxin Sichen | Application of ferroelectric memory PB85RS2MC in power battery management, with a capacity of 2M
- Analysis of common faults of frequency converter
- In a head-on competition with Qualcomm, what kind of cockpit products has Intel come up with?
- Dalian Rongke's all-vanadium liquid flow battery energy storage equipment industrialization project has entered the sprint stage before production
- Allegro MicroSystems Introduces Advanced Magnetic and Inductive Position Sensing Solutions at Electronica 2024
- Car key in the left hand, liveness detection radar in the right hand, UWB is imperative for cars!
- After a decade of rapid development, domestic CIS has entered the market
- Aegis Dagger Battery + Thor EM-i Super Hybrid, Geely New Energy has thrown out two "king bombs"
- A brief discussion on functional safety - fault, error, and failure
- In the smart car 2.0 cycle, these core industry chains are facing major opportunities!
- Rambus Launches Industry's First HBM 4 Controller IP: What Are the Technical Details Behind It?
- The United States and Japan are developing new batteries. CATL faces challenges? How should China's new energy battery industry respond?
- Murata launches high-precision 6-axis inertial sensor for automobiles
- Ford patents pre-charge alarm to help save costs and respond to emergencies
- Power consumption evaluation of GD32L233CCT6 in different power management modes
- Differential Equal Length
- IAP Function Design of MSP43F149 Series MCU
- C2000 floating point calculation notes - differences between CPU and CLA and error handling techniques
- TMS320F28335GPIO Example - Light up the LED
- Building an assisted driving system algorithm based on FPGA platform
- Why does my MSP430F5529 clock initialization use the high-speed XT1 mode, and XT1HFOFFG is always high?
- Practice together in 2021 + publish more papers and patents
- Share your experience in learning msp430 series microcontrollers
- Free Sample Application | Littelfuse Data Center Solutions Zone