By Toru Inoue, Executive Vice President and Director of Component Business Unit at Murata
After joining Murata in 1980, Toru Inoue was appointed as the head of the Accounting and Control Department, where he worked with the Industrial Engineering Department in addition to accounting. From 1990, he worked at factories in the UK and the US and at Murata's North American headquarters before returning to Japan in 1998. He then moved from the Accounting and Control Department to the Production Department. Working at the Yokaichi Plant, from Murata Ogaki to the Corporate Planning Department and other departments, he was appointed Vice President in 2009. Inoue became Director of the Parts Business Unit in July 2013.
As every device becomes more and more digital, EMI (Electromagnetic Interference) has become a major concern in the electronics industry.
Murata's EMI filter division has two main pillars of business: noise suppression components and inductors. The latter are used to stabilize signals and power supplies.
With the advancement of communication technologies such as PCs and smartphones, these products are expected to generate increasing demand.
In the high-growth potential markets of home electronics and automotive electronics, demand for Murata's products is growing rapidly due to the increasing introduction of multifunctional devices supported by communication technologies.
Providing components suitable for high-current circuits and improving reliability are major challenges facing Murata.
We need to leverage our traditional expertise in communications and consumer product applications while meeting customer needs.
We have established a successful partnership with a supplier of metal magnetic materials, which are required for the production of power line components. Murata EMI Filter Division is now ready to explore new markets and pave the way for the next stage of growth.
The emergence of PCs and mobile phones has led to a dramatic increase in demand. The demand for noise suppression components and inductors has been growing steadily. Size reduction is our specialty and one of the most important requirements of the market.
With the development of digitalization, the demand for compactness, high current and high Q of EMI filter segment products is growing
EMI suppression technology has recently become a focus of attention as the digitalization of devices continues to advance. Murata has been committed to providing inductors and noise suppression components that are relatively compact and for lower power lines. Looking back at our history, we provided noise suppression components for radios and TVs, as well as inductors for smoothing power supply voltages. Then, the emergence of PCs and mobile phones led to a sharp increase in demand. In the mobile phone market, customers mainly need inductors for RF applications. But we also see demand for power line inductors. Not only do PC manufacturers have an increasingly high demand for components that process general-purpose signals, the growing wireless communication between PCs and external devices is now also causing demand for RF circuit products. In the growing field of these products, the demand for noise suppression components and inductors has steadily increased. Size reduction is our specialty and it is one of the most important requirements.
One of Murata's strengths is that we produce three types of components using different processes: wire-wound, thin-film, and monolithic. This diversity allows us to make flexible proposals to our customers based on their needs. For example, customers who emphasize cost-effectiveness can choose monolithic products, while manufacturers who focus on performance can adopt wire-wound technology.
Murata is re-entering the power products market with reliable components and products for high-current circuits
The future of Murata's EMI filter division depends on whether we can successfully develop the market segments of home electronics and automotive electronics. The key words here are "high current and high reliability". In the current market, non-power components account for 60% of the overall demand, and components for high-current power lines account for 40%. However, we expect that in four to five years' time, the latter's share will increase to around 50%.
The fact is that we have used high-current power cords in the past. But in the late 1980s, we faced increasing competition, and since then we have focused our resources on other areas. At the same time, Murata has expanded its market share by leveraging its superior miniaturization technology. As a result, the company is now trying to re-enter the high-current power component market.
Product Size
Reducing component size is one of Murata’s traditional strengths. Murata’s noise suppression components and inductors are manufactured using three processes (wire winding, thin film, and monolithic), each with its own unique characteristics. The wire winding process can achieve the highest Q (quality factor) levels, but the scope for reducing size is limited. Current wire wound products have become smaller and smaller, but they are still a bit larger than components produced using thin film and monolithic technologies. But their size has been reduced to 0302 (0.8 x 0.6mm). Our line winding equipment also has an advantage: it was developed through a joint research program that combined Murata’s production technology with expertise in machine manufacturing.
On the other hand, the size of thin film and monolithic products has been reduced to 01005 (0.4 x 0.2mm). Thin film products have relatively high Q values, but not as good as wire wound products. If the thin film process is further developed in the future to achieve Q values comparable to those provided by the wire winding process, the inductor size may change significantly.
The challenge is to build close relationships with our customers that involve us in their product development activities from the beginning.
Strengthening alliance with Toko, a promising metal magnetic material producer
Murata formed an alliance with electronic component manufacturer Toko in February 2013 and started joint development. Murata's new partner is strong in providing highly reliable inductors and coil transformers for high-current applications. The highlight of these products from Toko is the use of "metal alloy" (a metal powder-based magnetic material), which makes it possible to provide low DC resistance at high inductance, thereby maintaining high performance in high-current circuits. We aim to use this technology and related processes to increase our sales in the high-current power line product market.
Murata has traditionally reduced costs by automating its production processes. The aim was to make its products cost-competitive even when produced in Japan, a market with high labor costs. In contrast, Toko started early in overseas production in order to reduce costs. It now produces all its products outside of Japan. Despite the differences in the nature of our production networks, we hope that both companies will be able to combine their expertise to create new products. With an eye on the newly formed joint development team, Murata hopes to establish an even closer relationship with Toko. To this end, both parties will further strengthen their cooperation.
Metal-based materials provide us with business opportunities
Suppose we don’t have metal materials available. Even then, we can achieve a certain degree of properties using ferrite-based materials. However, the advantage of metal-based materials is that they make it possible to create components that are smaller and can accommodate high currents. If we had not partnered with Toko and had developed metal materials from scratch, it would have taken at least three years to develop similar materials. In the meantime, we would not have any revenue. Assuming that new metal-based products take several more years to be popularized in the market after launch, we would have fallen behind our competitors. In other words, the partnership with Toko provided us with an opportunity five years ago.
Components made of metal magnetic materials have been used in the power circuits of smartphones for a year and a half. These components have higher performance than ferrite components. That is why they have been rapidly gaining popularity as soon as they were launched on the market, especially in smartphones. By combining Toko's metal technology with Murata's sales network, we expect to significantly increase sales of these components. We can also achieve synergies in production. Our leadership position may continue for a few more years, but in the meantime, we also need to prepare by anticipating the needs that will be born in the market.
The challenges we face include internal collaboration and information sharing with other departments, as well as proposing solutions to our clients.
Challenge: Build closer relationships with customers, as well as collaborate and share information with other departments
We do this with the goal of building close relationships with our customers, allowing us to propose solutions to them from the earliest stages of their product development. Murata offers a wide range of electronic components and has a broad customer base. All of our product divisions have access to a wide range of information. Therefore, if they can share with each other, we will have a stronger combined strength. In particular, the product division that provides modules is closer to customers than the division that produces traditional components.
We are looking to develop ways to get business-level information not only from customers but also internally that is closer to the final product.
Solution Proposal: A New Way for Sales Engineers to Sell
The EMI Filter Division has many opportunities to provide solutions to customers because it has traditionally supplied many components that need to be matched to the circuits into which they will be integrated. It is the sales engineer's responsibility to make recommendations and obtain information from customers. If we are to succeed in new markets such as energy, healthcare, and in-vehicle equipment, we must be more proactive than ever in discovering customer needs. As part of these efforts, we will further upgrade our electromagnetic anechoic chambers in Japan and abroad to help identify customer needs more accurately.
Previous article:Combined with Texas Instruments' new products, we review various technologies for reducing EMI in power chips
Next article:Core and Semiconductor's on-chip passive electromagnetic field simulation suite passes Samsung process certification
Recommended ReadingLatest update time:2024-11-23 03:07
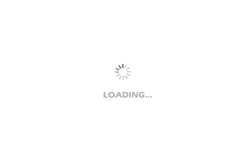
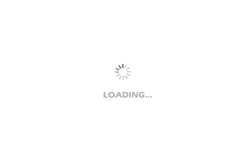
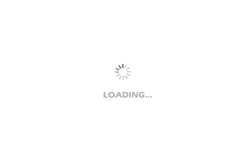
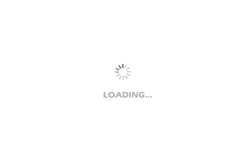
- Popular Resources
- Popular amplifiers
-
Study on the Behavioral Model of Silicon Carbide MOSFET Power Module and EMI Prediction of Low-Voltage Auxiliary Power Supply
-
Cable radiated EMI modeling considering mutual coupling effects_Junpeng Ji
-
Design of broadband hybrid active EMI filter for switching power supply_Liao Yuehong
-
Switching power supply conducted EMI simulation and filter circuit design_Jiang Yunfu
- USB Type-C® and USB Power Delivery: Designed for extended power range and battery-powered systems
- ROHM develops the second generation of MUS-IC™ series audio DAC chips suitable for high-resolution audio playback
- ADALM2000 Experiment: Transformer-Coupled Amplifier
- High signal-to-noise ratio MEMS microphone drives artificial intelligence interaction
- Advantages of using a differential-to-single-ended RF amplifier in a transmit signal chain design
- ON Semiconductor CEO Appears at Munich Electronica Show and Launches Treo Platform
- ON Semiconductor Launches Industry-Leading Analog and Mixed-Signal Platform
- Analog Devices ADAQ7767-1 μModule DAQ Solution for Rapid Development of Precision Data Acquisition Systems Now Available at Mouser
- Domestic high-precision, high-speed ADC chips are on the rise
- Intel promotes AI with multi-dimensional efforts in technology, application, and ecology
- ChinaJoy Qualcomm Snapdragon Theme Pavilion takes you to experience the new changes in digital entertainment in the 5G era
- Infineon's latest generation IGBT technology platform enables precise control of speed and position
- Two test methods for LED lighting life
- Don't Let Lightning Induced Surges Scare You
- Application of brushless motor controller ML4425/4426
- Easy identification of LED power supply quality
- World's first integrated photovoltaic solar system completed in Israel
- Sliding window mean filter for avr microcontroller AD conversion
- What does call mean in the detailed explanation of ABB robot programming instructions?
- STMicroelectronics discloses its 2027-2028 financial model and path to achieve its 2030 goals
- 2024 China Automotive Charging and Battery Swapping Ecosystem Conference held in Taiyuan
- State-owned enterprises team up to invest in solid-state battery giant
- The evolution of electronic and electrical architecture is accelerating
- The first! National Automotive Chip Quality Inspection Center established
- BYD releases self-developed automotive chip using 4nm process, with a running score of up to 1.15 million
- GEODNET launches GEO-PULSE, a car GPS navigation device
- Should Chinese car companies develop their own high-computing chips?
- Infineon and Siemens combine embedded automotive software platform with microcontrollers to provide the necessary functions for next-generation SDVs
- Continental launches invisible biometric sensor display to monitor passengers' vital signs
- Code efficiency in TMS320F28377S Flash and RAM
- [Xianji HPM6750EVKMINI Review] 3# HPM6750 Control of RW007 Module
- [For sale] USB color screen tester Ruideng UM25C is available for sale! ! !
- Application of single-stage power factor correction in miniaturized design of AC-PDP switching power supply
- Question about transistor base emitter saturation voltage
- Problems with switching tube oscillation and inversion
- Can this be done at the input end of the optocoupler?
- KiCad 5.1.6 released
- [Jiangxiang Technology] Today I won a bottle of 2499 Jiangxiang Technology
- Today at 10:00 AM, live broadcast with prizes: Arrow Electronics & ADI join hands to design flyback isolated power supply without optocoupler