2.1.6 Thyristor trigger circuit
The dust removal control system controls the power supply by changing the trigger angle of the thyristor. The increase or decrease of the trigger angle is changed by the trigger pulse, as shown in Figure 8. The trigger pulse circuit is mainly composed of a pulse amplifier and a transformer. When the PLC generates a zero-crossing interrupt, it starts the timer T0 (T0 is the initial value, corresponding to the conduction angle). T0 overflow will cause an interrupt. At this time, the PLC outputs a trigger pulse to control the conduction of the transistor. The primary side of the pulse transformer will generate a trigger pulse that is added to the G and K poles of the thyristor respectively. When the transistor is cut off, the trigger pulse will be blocked.
Figure 8 SCR trigger circuit
2.1.7 Data Acquisition Circuit
The analog quantities that need to be detected mainly include the average value of the primary voltage and current, the average value of the secondary voltage and current, and the peak value of the secondary current. The values of these analog quantities are generally large.
On-site sampling is required before entering the control system.
Sampling of primary voltage: The primary voltage is stepped down through a small transformer.
Sampling of primary current: conversion by current transformer connected in series in the primary circuit.
Sampling of secondary voltage: voltage division of anode high voltage circuit in transformer rectifier.
Sampling of secondary current: A sampling resistor is connected in parallel to the ground end of the anode-secondary circuit in the transformer-rectifier and then converted.
Figure 9 Secondary voltage acquisition circuit
The following is an explanation using the secondary voltage as an example. The sampling circuit is shown in FIG9 . The secondary voltage collected on site is divided, passed through a proportional adjustment circuit composed of a sliding rheostat VR4, and finally detected by a Hall voltage sensor.
2.2 Software Design
2.2.1 Main flow chart of the program
As shown in Figure 10, after the control system is powered on, the system is initialized first. If the reset button is pressed, it will restart. If the start button is pressed, the parameter setting stage will be carried out. The CPU will process the collected parameters. If sparks appear, it will enter the spark processing subroutine. If a parameter exceeds the limit, it will enter the alarm and fault processing subroutine. Finally, the system will rescan the data and start a new cycle.
Figure 10 Main flow chart of the program
2.2.2 Touch screen configuration
The configuration of the touch screen is mainly the configuration of the screen. Designing a friendly and convenient touch screen interface can not only increase the convenience of operation, but also reduce the error rate of operation, so that the machine and equipment can play the maximum function. The screen includes the main screen, parameter setting, display screen, trend curve and help. The detailed pictures of the display screen and parameter setting screen are omitted.
In the parameter setting screen, click the input field on the screen, and a numeric keyboard will appear for input. The KTP touch screen can ensure that when a fault occurs, an alarm will be displayed on the current page for immediate processing. There are two types of alarms: errors and warnings. Warnings do not require confirmation and do not cause direct harm to the equipment; errors require operational confirmation and are harmful to the equipment. The equipment will trip and shut down. Warnings include primary voltage overlimit, primary current overlimit, secondary voltage overlimit, etc. Errors include secondary overcurrent fault, secondary overvoltage fault, oil temperature overlimit fault, biased excitation, etc.
3. Implementation of remote control
With the help of modern network interconnection technology, the controllers of each electric field of the dust collector can exchange data with the host computer monitoring software through Ethernet. The host computer can realize remote start, stop, boost, buck control and parameter adjustment of the dust removal equipment. The operating parameters and operating status of each device of the electrostatic precipitator can also be intuitively displayed on the host computer screen, so that managers can realize remote control as if they were on site.
The upper computer monitoring software uses Siemens' WinCC configuration software, which has operation screen, monitoring screen, control screen, alarm screen, real-time trend curve, historical trend curve, and can print reports.
The communication between WinCC and S7-1200 CPU is realized through Ethernet and can only be realized through OPC. S7-1200 CPU only needs to set the IP address. The host computer establishes PC Starion through SIMATIC NET software to communicate with S7-1200 CPU. S7-1200 CPU has an integrated PROFINET port that supports Ethernet and TCP/IP-based communication standards. The remote control of the three-field dust collector is shown in Figure 11.
Figure 11 Schematic diagram of three-field remote control
4 Conclusion
The system not only has good automatic voltage regulation and remote control capabilities, but also simplifies on-site operations through PLC and touch screen, improves the flexibility of control programs and human-machine interfaces, and is easy to maintain. Although the initial investment in the equipment is high, the operating cost is acceptable in the long run.
Previous article:High-voltage electrostatic dust removal control system solution based on PLC and touch screen
Next article:Application of Advantech touch-screen industrial tablet computer in remote monitoring system
Recommended ReadingLatest update time:2024-11-16 14:44
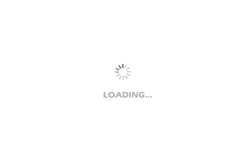
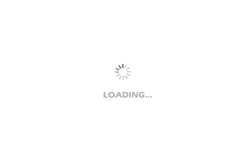
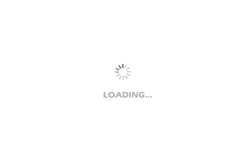
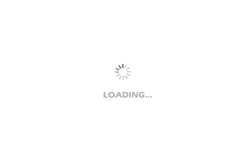
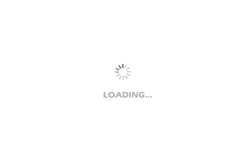
- Popular Resources
- Popular amplifiers
- High signal-to-noise ratio MEMS microphone drives artificial intelligence interaction
- Advantages of using a differential-to-single-ended RF amplifier in a transmit signal chain design
- ON Semiconductor CEO Appears at Munich Electronica Show and Launches Treo Platform
- ON Semiconductor Launches Industry-Leading Analog and Mixed-Signal Platform
- Analog Devices ADAQ7767-1 μModule DAQ Solution for Rapid Development of Precision Data Acquisition Systems Now Available at Mouser
- Domestic high-precision, high-speed ADC chips are on the rise
- Microcontrollers that combine Hi-Fi, intelligence and USB multi-channel features – ushering in a new era of digital audio
- Using capacitive PGA, Naxin Micro launches high-precision multi-channel 24/16-bit Δ-Σ ADC
- Fully Differential Amplifier Provides High Voltage, Low Noise Signals for Precision Data Acquisition Signal Chain
- Innolux's intelligent steer-by-wire solution makes cars smarter and safer
- 8051 MCU - Parity Check
- How to efficiently balance the sensitivity of tactile sensing interfaces
- What should I do if the servo motor shakes? What causes the servo motor to shake quickly?
- 【Brushless Motor】Analysis of three-phase BLDC motor and sharing of two popular development boards
- Midea Industrial Technology's subsidiaries Clou Electronics and Hekang New Energy jointly appeared at the Munich Battery Energy Storage Exhibition and Solar Energy Exhibition
- Guoxin Sichen | Application of ferroelectric memory PB85RS2MC in power battery management, with a capacity of 2M
- Analysis of common faults of frequency converter
- In a head-on competition with Qualcomm, what kind of cockpit products has Intel come up with?
- Dalian Rongke's all-vanadium liquid flow battery energy storage equipment industrialization project has entered the sprint stage before production
- Allegro MicroSystems Introduces Advanced Magnetic and Inductive Position Sensing Solutions at Electronica 2024
- Car key in the left hand, liveness detection radar in the right hand, UWB is imperative for cars!
- After a decade of rapid development, domestic CIS has entered the market
- Aegis Dagger Battery + Thor EM-i Super Hybrid, Geely New Energy has thrown out two "king bombs"
- A brief discussion on functional safety - fault, error, and failure
- In the smart car 2.0 cycle, these core industry chains are facing major opportunities!
- The United States and Japan are developing new batteries. CATL faces challenges? How should China's new energy battery industry respond?
- Murata launches high-precision 6-axis inertial sensor for automobiles
- Ford patents pre-charge alarm to help save costs and respond to emergencies
- New real-time microcontroller system from Texas Instruments enables smarter processing in automotive and industrial applications
- Apply for a trial of a new Tektronix oscilloscope and win a custom T-shirt!
- TI invites you to fill out the questionnaire to win gifts | Personally customize your 2019 industrial application solution
- In what situations is serpentine routing suitable for high-speed applications? What are its disadvantages?
- C6747's emifa access to asynchronous external storage
- How to use arrays in C language for microcontrollers
- Implementation of booting Linux from TF card on i.MX6UL
- Can you help me transfer the Ambarella A2S HD camera PCB + schematic diagram to PDF?
- In-depth analysis of T-BOX system solution: wireless connection unit
- Water level measurement voice alarm device
- Application of wireless pressure transmitter in the field of Internet of Things!