DC stands for "direct current", which is a unidirectional current flowing through a conductor from point A to point B in a circuit. The most basic definition of DC-DC conversion is to convert a DC voltage into another DC voltage (even if it is the same voltage) through a zero output impedance and noise-free circuit.
Working principle and composition of DC-DC
A switching regulator has an on/off power switch built into it (mostly a vertical metal oxide semiconductor, or VMOS, but can also be a bipolar device). The on/off cycle of the power switch determines the energy that is accumulated and then delivered to the load. Whereas linear regulators use the voltage drop across a resistor to regulate the voltage, they are very inefficient. Relatively speaking, a switching regulator dissipates almost no power! The secret is in the power switch. When the switch is open, the voltage across the switch is high, but the current is zero. When the switch is closed, the current through the switch is high, but the voltage is zero!. Since the voltage and current of the inductor are 90 degrees out of phase (and there is no DC drop), the switching regulator is very efficient.
The basic working principle of the DC/DC converter is: the switch tube works in the switch state under the control of the control circuit. When the switch tube is turned on, the voltage forms a loop through the switch tube, the energy storage inductor and the capacitor. The charging current not only establishes a DC voltage at both ends of the capacitor, but also generates a positive left and a negative right electromotive force on the energy storage inductor. During the cut-off period of the switch tube, since the current in the energy storage inductor cannot change suddenly, the inductor generates a positive right and a negative left pulse voltage through self-inductance. Therefore, the positive voltage at the right end of the inductor → filter capacitor → freewheeling diode → left end of the inductor forms a discharge loop, and the discharge current continues to establish a DC voltage at both ends of the capacitor. The DC voltage obtained at both ends of the capacitor supplies power to the load.
What parts does a DC-DC converter generally consist of?
A switching DC-DC converter is generally composed of a control chip switch tube (K), an inductor coil (L), a diode (D), and a capacitor (C).
The linear DC-DC converter is mainly composed of a linear regulator, a transistor, a Zener diode, and a bias resistor.
Principle and Application of DC-DC Converter
When the last joule of energy in your battery is gone, power consumption and efficiency really take on new meanings. Take a typical mobile phone, for example. Even when you are not using the phone to make a call, power is consumed by tasks such as lighting up the LCD screen and displaying the time and the network operator being used. If it is a more advanced phone, you can also play your favorite MP3 music or browse video data. However, every time you add a function to the phone, you actually add a burden on the battery. For most mobile phone designers, the key to how long your phone can last before the next charge is whether it can extend the use of available power. This means that power needs to be carefully conserved and budgeted among various functional modules to maximize battery life and use.
To achieve true efficiency, it does not only mean how high the efficiency of the DC-DC converter can be at a certain operating point specified by the load, but how long this high efficiency can be maintained over the entire load range of the DC-DC converter. Generally speaking, most DC-DC converters specify the maximum efficiency figure that can be achieved, and people also choose a suitable converter without hesitation by choosing a very large figure (such as 95%). However, to really make full use of this efficiency, it is also necessary to crank the converter to the operating point where maximum power conversion can be achieved. If it is not turned to this point, 95% efficiency cannot be achieved. And because of this problem, sometimes even 60% efficiency cannot be achieved depending on the load applied.

Figure 1 Typical efficiency curve
Figure 1 shows that while 95% efficiency can be achieved at point A, 60% or even lower efficiency can be achieved at point B. This difference in operating point or load scale is very important for portable consumer products because most of these electronic devices have multiple functions (such as playing music, taking pictures, or making phone calls), each of which requires a different operating point or different effective load on the DC-DC regulator. For those functions that are not invoked by the user, the power load on the DC-DC source will be very light, and the 95% efficiency will drop sharply to 50% or even lower, as it is at point B in Figure 1.
Take smartphones, for example. In smartphones, it is important to know how long it will take for the DC-DC converter that powers the AP (application processor) IO or core voltage to drain the battery. Assume that your phone battery can last for a maximum of 2-3 days in normal use (i.e., mainly voice calls). During this time (48-72 hours), only a small portion of the power is usually used for entertainment activities, such as taking and browsing photos or playing MP3 music. It means that the phone does not need the AP to do much during the rest of the time; it may just be used to refresh the DDR memory when the AP is in standby or sleep mode. Therefore, if the AP is often in these modes, the load it brings to the converter will be at the light load end of the scale, that is, point B. This means that the power of the AP regulator will always run at 50% or even lower efficiency, making it the single largest drain on the battery. It can be seen that it is not enough to just select a DC-DC regulator with a high efficiency specification. It is also necessary to ensure that the regulator can provide high efficiency throughout the load range, especially at light load and full load.

Figure 2 Improving efficiency at light loads
Innovative solutions are needed to address this problem. Take, for example, a new DC-DC buck converter from Freescale that provides high efficiency at light loads. The MC34726/7 series is a synchronous buck converter that can deliver up to 300mA or 600mA while achieving 90% efficiency. The converter's efficiency is shown in Figure 2, which maintains high efficiency over the entire load range, peaking near the maximum load. For light loads (point B), efficiency is also maintained above 80%. The device uses a dedicated adjustable Z-factor mode (Z-Mode) switching architecture to achieve smooth transitions between PWM and PFM without sacrificing transient response, bias current, or efficiency. As a result, the Z-Mode architecture greatly improves performance during load current transitions, providing better transient response while still maintaining a low bias current of 65μA at light loads in the "sleep" Z-Mode.

Figure 3 Typical application diagram
The device accepts an input voltage range of 2.7 to 5.5V and can provide an output voltage of 0.8 to 3.3V at a continuous load current of 300mA/600mA. In addition, its high switching frequency of 2MHz or 4MHz also makes it very suitable for space-constrained portable devices such as mobile phones, PDAs, DSCs, PNDs, GPS, PMPs and other portable instruments. Figure 3 shows a typical application of the device.
Technical parameters of DC-DC converter chip
Input, Output and Efficiency
The input voltage of the DC-DC converter is required to be within a specific range. If the input voltage is too low, it cannot provide enough energy. If the input voltage is too high, the chip cannot withstand it. The working efficiency of LDO decreases as the input voltage increases, while the efficiency of DC-DC chip has little to do with the input voltage, which is one of the biggest advantages of DC-DC.
Output current capability is the most important parameter of a DC-DC converter with built-in FET. ON's DC-DC device NCP3102 can output up to 10A of current, which can meet your demanding requirements for power supply.
Efficiency is defined as output power divided by input power, and higher efficiency means efficient power management. ON's DC-DC device NCP1595 has an efficiency of up to 95%.
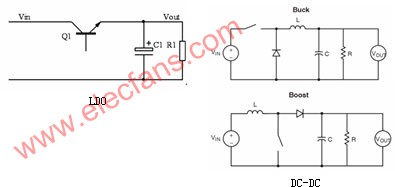
Soft Start
When the hard start circuit just starts working, there is no energy stored in the output capacitor, so the voltage is very low. When the feedback loop of the circuit detects the low voltage value, it will use the widest PWM to increase the output voltage as quickly as possible. However, this process is prone to current overshoot and damage to circuit components because the feedback loop reacts very quickly.
The advantages of applying soft start technology are:
The output voltage rise speed is slowed down and the startup current is controlled, thus protecting the load;
Greatly reduces the requirement for the transient output power of the front-stage power supply;
Most of the ON devices support soft-start technology.

Power on and off sequence control
Establishing and maintaining a suitable power supply environment is critical to the normal operation of the system, especially in the design of processors such as FPGA, DSP, ARM, etc. In order to avoid problems such as latch-up, inrush current or I/O contention, up to 4 to 5 or more power supplies may be required to power on and off in a specified order and slope. In addition, many applications also require that the power-on sequence and slow power-on slope be adjustable to adapt to various situations.
NCP3120/3221/3122/3123 integrate power-on and power-off control functions and also support cascade operation.

Voltage mode control and current mode control
There are two methods for controlling the feedback loop and voltage regulation characteristics of a switching DC-DC converter: voltage mode control and current mode control.
In voltage-mode control, the converter's duty cycle is proportional to the error between the actual output voltage and the ideal output voltage; in current-mode control, the duty cycle is proportional to the error between the rated output voltage and the converter's control current function (the control current can be the switch current in a non-isolated topology or the transformer primary current in an isolated topology).
Voltage mode control only responds to changes in the output (load) voltage. This means that in order for the converter to respond to changes in the load current or input line voltage, it must "wait" for a corresponding change in the load voltage. This waiting delay affects the converter's voltage regulation characteristics.
If the load current change can be responded to within a single switching cycle, the "waiting" problem and the corresponding load regulation compensation associated with voltage mode control can be eliminated, which can be achieved with current mode control. Current mode control controls the output current on a pulse-by-pulse basis. In other words, current mode control has superior input transient response and output transient response than voltage mode control.

Switching Mode and Frequency
The higher the operating frequency of the DC-DC converter means that the external circuit is smaller, which can provide higher power density. To a certain extent, the output ripple will also become smaller.
PWM (pulse width modulation): The control frequency is constant and the pulse width is variable. This modulation method is the most widely used.
PFM (pulse frequency modulation): The on-time of the reference oscillator is fixed, while the frequency is variable. This modulation method is more commonly used when the load is relatively light.
ON's DC-DC devices NCP1526, NCP1522B, and NCP1523B operate at frequencies up to 3000KHz.
Previous article:When RF meets analog and digital signals – EMI testing
Next article:Learning simulation bit by bit: some problems with DC-DC converters
Recommended ReadingLatest update time:2024-11-16 16:31
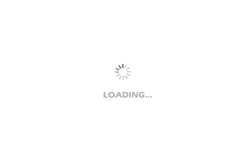
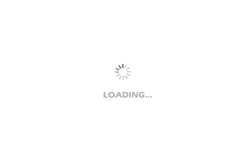
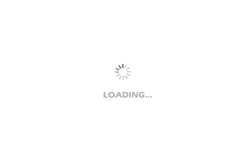
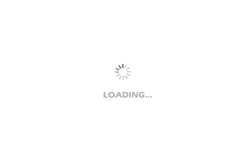
- Popular Resources
- Popular amplifiers
-
New Energy Vehicle Detection and Diagnosis Experiment (Edited by Mao Caiyun, Zhou Xien, and Long Jiwen)
-
Virtualization Technology Practice Guide - High-efficiency and low-cost solutions for small and medium-sized enterprises (Wang Chunhai)
-
Design of an adaptive constant on-time buck DC-DC converter with high efficiency and low power consumption
-
Research on design technology of high-efficiency step-up DC-DC converter with wide load range
- High signal-to-noise ratio MEMS microphone drives artificial intelligence interaction
- Advantages of using a differential-to-single-ended RF amplifier in a transmit signal chain design
- ON Semiconductor CEO Appears at Munich Electronica Show and Launches Treo Platform
- ON Semiconductor Launches Industry-Leading Analog and Mixed-Signal Platform
- Analog Devices ADAQ7767-1 μModule DAQ Solution for Rapid Development of Precision Data Acquisition Systems Now Available at Mouser
- Domestic high-precision, high-speed ADC chips are on the rise
- Microcontrollers that combine Hi-Fi, intelligence and USB multi-channel features – ushering in a new era of digital audio
- Using capacitive PGA, Naxin Micro launches high-precision multi-channel 24/16-bit Δ-Σ ADC
- Fully Differential Amplifier Provides High Voltage, Low Noise Signals for Precision Data Acquisition Signal Chain
- Innolux's intelligent steer-by-wire solution makes cars smarter and safer
- 8051 MCU - Parity Check
- How to efficiently balance the sensitivity of tactile sensing interfaces
- What should I do if the servo motor shakes? What causes the servo motor to shake quickly?
- 【Brushless Motor】Analysis of three-phase BLDC motor and sharing of two popular development boards
- Midea Industrial Technology's subsidiaries Clou Electronics and Hekang New Energy jointly appeared at the Munich Battery Energy Storage Exhibition and Solar Energy Exhibition
- Guoxin Sichen | Application of ferroelectric memory PB85RS2MC in power battery management, with a capacity of 2M
- Analysis of common faults of frequency converter
- In a head-on competition with Qualcomm, what kind of cockpit products has Intel come up with?
- Dalian Rongke's all-vanadium liquid flow battery energy storage equipment industrialization project has entered the sprint stage before production
- Allegro MicroSystems Introduces Advanced Magnetic and Inductive Position Sensing Solutions at Electronica 2024
- Car key in the left hand, liveness detection radar in the right hand, UWB is imperative for cars!
- After a decade of rapid development, domestic CIS has entered the market
- Aegis Dagger Battery + Thor EM-i Super Hybrid, Geely New Energy has thrown out two "king bombs"
- A brief discussion on functional safety - fault, error, and failure
- In the smart car 2.0 cycle, these core industry chains are facing major opportunities!
- The United States and Japan are developing new batteries. CATL faces challenges? How should China's new energy battery industry respond?
- Murata launches high-precision 6-axis inertial sensor for automobiles
- Ford patents pre-charge alarm to help save costs and respond to emergencies
- New real-time microcontroller system from Texas Instruments enables smarter processing in automotive and industrial applications
- FPGA_100 Days Journey_DA Design
- How will 6 GHz and Matter change the smart home?
- Let’s discuss 5G millimeter wave technology and base station solutions.
- TE Connectivity enables electric vehicles with sensing and connectivity solutions
- Improving bandwidth to create a future-proof CATV solution
- Probably the simplest and cheapest DIY thermometer and hygrometer
- Class A amplifier made by imitating Spark 230C circuit
- ON Semiconductor and Avnet IoT Innovation Design Competition Development Board Unboxing Photos
- DCDC circuit SEPIC
- [Evaluation of EC-01F-Kit, the NB-IoT development board of Anxinke] 06. Connecting to Alibaba Cloud based on STM32+EC-01F MQTT