Our flight had just begun to descend when a gentleman sitting next to me turned to talk to me about engineering—he had seen me reading an engineering journal. The gentleman next to me said that he was a member of the Institute of Electrical and Electronics Engineers (IEEE) and that his original ambition was to be a member of a standards committee. I asked him what standard he was working on—it was related to power plant safety. We ended the conversation until the plane stopped in front of the terminal and went our separate ways. During the discussion, I talked about the importance of standards and told him from my industry perspective how surprised I was that it took until 2000 for us to have an IEEE standard to define the specifications and test methods for analog-to-digital converters (ADCs).
This is noteworthy because analog-to-digital conversion has been known since at least the 1920s, but commercial ADCs did not appear until the 1960s [1]. For decades, ADC manufacturers defined the specifications for these devices and tested them independently. Naturally, some "standards" for how to test were developed, but there were still no standard guidelines issued by a physical standards body.
The first real ADC standardization effort began in 1980, culminating in the release of IEEE1057 [2], which later became IEEE1241 [3]. IEEE1241 is specifically targeted at ADC devices themselves, as opposed to a complete data acquisition or recording system. IEEE1241-2000 was the first standard truly developed for ADC component manufacturers; it was updated in 2010.
Figure 1. An ideal ADC transfer function has evenly spaced transfer points
(just one least significant bit LSB wide).
A major task in evaluating an ADC is determining its transfer function. Ideally, a converter would have a transfer function similar to that shown in Figure 1. Figure 1 shows the transfer function of a three-bit converter. In an ideal converter, each code width is exactly the same, and a straight line can be drawn through the middle of each code "plateau." In reality, this is not always the case—because actual transfer functions differ from the ideal, determining the transition points and code widths is critical to ADC testing and characterization.
To find the true transfer function, the IEEE standard suggests several possible test procedures and methods. One method uses a complex servo-loop system that requires a digital-to-analog converter (DAC) with higher resolution than the ADC being tested. Another method uses a sine wave oscillator, but with a total harmonic distortion and noise (THD+N) that is at least 20 dB higher than the expected signal-to-noise-and-distortion ratio (SINAD) of the ADC being tested. For example, an ideal 16-bit ADC has a 98 dB signal-to-noise ratio (SNR) and no distortion (it is ideal after all)—then the SINAD is 98 dB. Testing this ADC requires an oscillator with a THD+N of more than –118 dB. When you look at high-resolution ADCs, if the sine wave generator alone cannot do the job, it may require filtering to obtain a spectrally pure signal.
Finding such high-resolution DACs or pure-spectrum oscillators and building the required complex test equipment is something that most ADC manufacturers are willing to do and generally have the ability to do. Some of these instruments are very expensive, but if your business is to manufacture ADCs, then these investments are worth it. But for individuals who are engaged in ADC system design, how can they complete the evaluation and testing of ADCs?
Many people turn to evaluation boards and tool kits provided by the manufacturer for testing. With these systems, it is easy to connect the ADC under test to a computer via a USB cable and then use software to acquire data and finally analyze it.
Some people want to use the evaluation kit to get the same results as shown in the ADC data sheet specifications, but this is not always possible, especially when using high-resolution converters because the required sine wave generator may not be available. Although using the evaluation board and its software, you can often get some meaningful results, but you should be careful.
Evaluation hardware and analysis software generally operate in a mode termed "block mode." In this mode, a fixed number of samples are collected and sent to the software, which then analyzes that block or record of data. Most IEEE standard tests are defined so that they work with these blocks of data.
The question is, do the tests outlined in IEEE1241 really help you evaluate the suitability of an ADC for your system? If you believe it does, then what do you gain beyond what you see in the device data sheet? Many people believe that in addition to seeing the actual device in operation, the evaluation board also describes the reference design and layout that can provide guidance for using it in an actual system.
Still, for some people, IEEE1241 testing is not what they need. Depending on the type of ADC, some people like to use the evaluation board and software as a digital oscilloscope or chart recorder, continuously streaming data, as opposed to transmitting data block by block. Some customers I have worked with strive to understand long-term stability or drift performance, sometimes requiring data to be logged to a hard drive for hours or even days. Although these applications are more regulated by IEEE1057, there is no standard that discusses long-term drift or stability testing.
Most manufacturers' evaluation boards and software will not support this type of application or testing. Should ADC component manufacturers enable their evaluation boards and software to generate data streaming and block acquisitions and turn on other features to perform tests that are not specified in the ADC-related standards?
Standards are definitely relevant to ADC manufacturers. But as a circuit designer using these ADCs, the same standards used by ADC manufacturers may not be of much use to you. What standards do you think of when evaluating ADCs? I will share them with readers in a subsequent article.
Previous article:PGI releases PGI Accelerator compiler with OpenACC support
Next article:Aliasing Frequency Calculator
Recommended ReadingLatest update time:2024-11-16 16:37
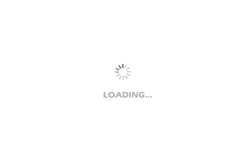
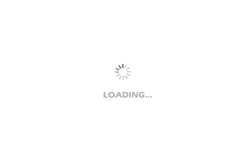
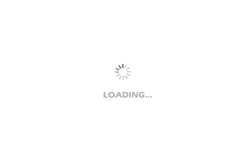
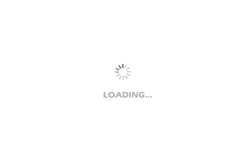
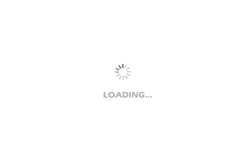
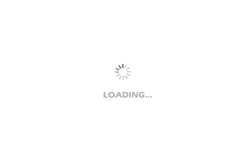
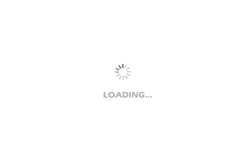
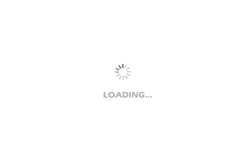
- High signal-to-noise ratio MEMS microphone drives artificial intelligence interaction
- Advantages of using a differential-to-single-ended RF amplifier in a transmit signal chain design
- ON Semiconductor CEO Appears at Munich Electronica Show and Launches Treo Platform
- ON Semiconductor Launches Industry-Leading Analog and Mixed-Signal Platform
- Analog Devices ADAQ7767-1 μModule DAQ Solution for Rapid Development of Precision Data Acquisition Systems Now Available at Mouser
- Domestic high-precision, high-speed ADC chips are on the rise
- Microcontrollers that combine Hi-Fi, intelligence and USB multi-channel features – ushering in a new era of digital audio
- Using capacitive PGA, Naxin Micro launches high-precision multi-channel 24/16-bit Δ-Σ ADC
- Fully Differential Amplifier Provides High Voltage, Low Noise Signals for Precision Data Acquisition Signal Chain
- Innolux's intelligent steer-by-wire solution makes cars smarter and safer
- 8051 MCU - Parity Check
- How to efficiently balance the sensitivity of tactile sensing interfaces
- What should I do if the servo motor shakes? What causes the servo motor to shake quickly?
- 【Brushless Motor】Analysis of three-phase BLDC motor and sharing of two popular development boards
- Midea Industrial Technology's subsidiaries Clou Electronics and Hekang New Energy jointly appeared at the Munich Battery Energy Storage Exhibition and Solar Energy Exhibition
- Guoxin Sichen | Application of ferroelectric memory PB85RS2MC in power battery management, with a capacity of 2M
- Analysis of common faults of frequency converter
- In a head-on competition with Qualcomm, what kind of cockpit products has Intel come up with?
- Dalian Rongke's all-vanadium liquid flow battery energy storage equipment industrialization project has entered the sprint stage before production
- Allegro MicroSystems Introduces Advanced Magnetic and Inductive Position Sensing Solutions at Electronica 2024
- Car key in the left hand, liveness detection radar in the right hand, UWB is imperative for cars!
- After a decade of rapid development, domestic CIS has entered the market
- Aegis Dagger Battery + Thor EM-i Super Hybrid, Geely New Energy has thrown out two "king bombs"
- A brief discussion on functional safety - fault, error, and failure
- In the smart car 2.0 cycle, these core industry chains are facing major opportunities!
- The United States and Japan are developing new batteries. CATL faces challenges? How should China's new energy battery industry respond?
- Murata launches high-precision 6-axis inertial sensor for automobiles
- Ford patents pre-charge alarm to help save costs and respond to emergencies
- New real-time microcontroller system from Texas Instruments enables smarter processing in automotive and industrial applications
- MSP430 interrupt mechanism
- The internal matching drive amplifier is actually an internal two-stage process as shown below:
- Using a microphone to measure light? It turns out there is such a cool operation!
- CC2540 Power Settings
- How do I convert the differential signal from the fiber optic transceiver into a video signal (CVBS)?
- I'd like to ask for your advice, is there any cheap solution to remotely control LED advertising screens via the internet?
- Meet at the MPS Core Cloud Exhibition Hall, challenge yourself with wisdom and courage, and win exclusive gifts!
- 【Silicon Labs Development Kit Review】+PG22 Hardware Resources
- "Play Board" + Shared Bicycle Control Panel-Hardware Modification
- MSP430fr6989 serial port DMA sending experimental routine