1 Overall design of spray dust suppression control system
The overall structure of the coal mine spray dust suppression control system based on power carrier communication is shown in Figure 1. The system consists of several spray dust suppression controllers and actuator solenoid valves. Each controller controls two solenoid valves, and the controllers communicate with each other through power carriers. The controllers are installed on the coal mining face support in sequence. When the coal mining machine is running, the infrared positioning device installed on the coal mining machine transmits a positioning signal. The controller that receives the coal mining signal acts as the main controller to control the actions of other controllers, and the solenoid valve completes the spray dust suppression task.
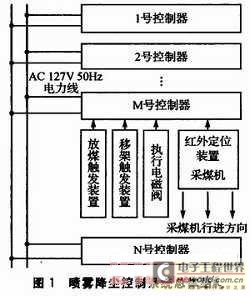
2 Hardware design of spray dust suppression control system
2.1 Spray dust suppression controller hardware structure
As shown in Figure 2, the spray dust suppression controller includes a power module, a power line carrier communication module, a spray time setting module, a controller address setting module, a rack moving and coal placing signal receiving module, a coal mining machine dust source tracking infrared positioning signal receiving module, LED lighting, and a solenoid valve drive control module. The power module supplies power to the microcontroller, solenoid valve, and high-power LED. The communication module is responsible for sending the control signal of the main controller to other controllers through the power line carrier. The positioning signal receiving module on the controller is responsible for receiving signals from the coal mining machine, the bracket, and the coal placing handle, and taking corresponding actions to open the solenoid valve to implement the spray operation.
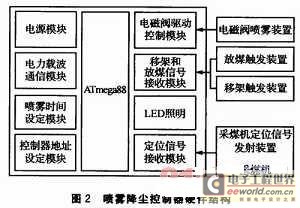
2.2 Spray dust suppression controller hardware circuit
The hardware circuit diagram of the spray dust suppression controller is shown in Figure 3. The controller uses the AVR series high-performance, low-power 8-bit AVR microcontroller ATmega88. It has an advanced RISC structure and 8 KB system-programmable Flash, with a data throughput of up to 1 MIPS/MHz, which can alleviate the contradiction between system power consumption and processing speed; the operating temperature range is relatively wide (-40 to 85°C, which fully meets the requirements of the underground environment; the controller circuit has address setting and spray mode setting modules.
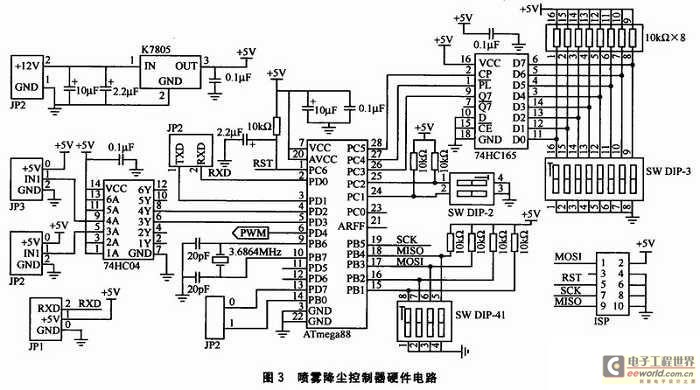
The hardware circuit of the power carrier communication module is shown in Figure 4. The carrier signal modem BWP08 is used. It is a single-phase power line carrier modem, which adopts a 5-12 V wide voltage design and an adjustable carrier baud rate of 100-600 bps. There are a variety of interface options, including UART, SPI and other interfaces, which can be easily connected to the microcontroller for data communication. The module adopts spread spectrum coding, has strong anti-interference ability, reliable data transmission, and a communication distance of within 200 m. The control signal is sent from the serial port of the microcontroller to the modem, and the modulated signal is amplified by power and then output coupled to the power line; the carrier signal on the power line is input coupled, filtered, amplified, and then demodulated by the modem and sent to the serial port of the microcontroller.
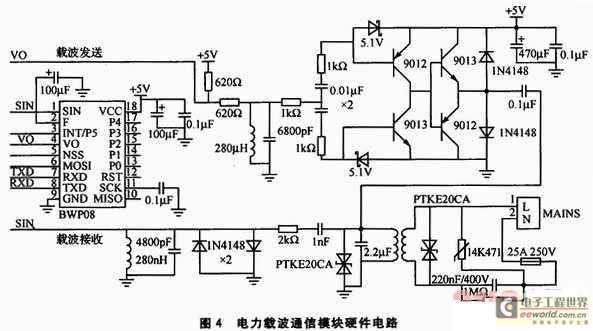
The infrared positioning signal transmitting circuit is shown in Figure 5. When the coal mining machine is running, the infrared positioning device installed on the coal mining machine transmits the infrared positioning signal. After receiving the signal, the receiving part of the controller can determine the position of the coal mining machine. The controller that receives the signal from the coal mining machine serves as the main controller to control the controller located downwind of the coal mining working face to implement the spray dust reduction operation. Infrared
The positioning circuit uses Silicon Labs' C8051F330 microcontroller, infrared emitting diode and integrated receiving head, which has low power consumption, stable operation and good signal directionality.
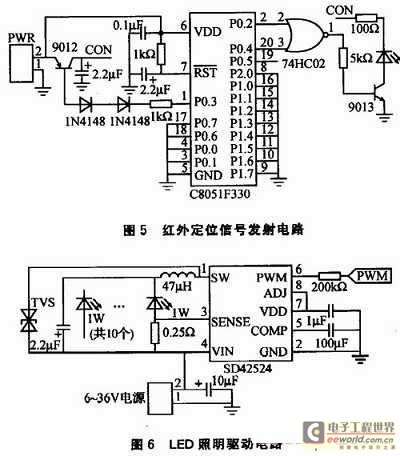
The lighting conditions in the mine are related to the safe production of the coal mine. LED lamps are energy-saving, flameproof and intrinsically safe, and have obvious advantages over traditional lighting methods in mines. The lighting circuit selects a 1 W high-power LED and adopts a step-down constant current drive circuit. The driver chip SD42524 has high efficiency, which can reach more than 96%. When the input/output voltage changes, the output current change in the full voltage range is controlled within ±1%; it has a built-in temperature protection circuit, current limiting circuit, and PWM dimming circuit. SD42524 adopts current mode control, which can provide fast transient response, and the loop stability design is simple. The LED lighting drive circuit is shown in Figure 6.
The hydraulic support moving frame and coal placing trigger circuit adopts infrared sensing control design. When the support is moved and the coal placing handle is used, the pyroelectric infrared sensor can detect the infrared radiation emitted by the human body, convert it into an electrical signal, and send it to the window comparator after amplification. If the signal amplitude exceeds the upper and lower limits of the window comparator, the system outputs a high-level signal, otherwise it outputs a low-level signal, and the controller takes corresponding actions after receiving the signal. The pyroelectric infrared sensor uses BISS0001, which is a high-performance sensor signal processing integrated circuit, which is equipped with a small number of external components to form a passive pyroelectric infrared switch.
The power module uses a low-power switching regulator, and the LM2576-12 and LM2576-ADJ in the LM2576 series are selected. This series is a 3 A current output step-down switching integrated voltage regulator circuit produced by National Semiconductor Corporation of the United States. It contains a fixed frequency oscillator and a reference voltage regulator; it has a complete protection circuit (including current limiting and thermal shutdown circuits, etc.). Using this device, only a few peripheral devices are needed to form an efficient voltage regulator circuit; it has reliable working performance, high working efficiency and strong output current driving capability, which can provide a strong guarantee for the stable and reliable operation of the MCU.
3. Software design of spray dust suppression control system
After the system is powered on and starts working, it enters the interrupt waiting state. When it receives a coal mining machine signal or a rack moving or coal placing signal, an interrupt is generated and the interrupt processing program is entered. The controllers installed on the bracket work in groups of three. When one controller receives a coal mining machine signal, the two controllers located downwind also start working. The controller first reads its own address. When it receives the address sent by other controllers on the power line, it compares it with its own address. If they are the same, the solenoid valve sprays. The program flow is shown in Figure 7.
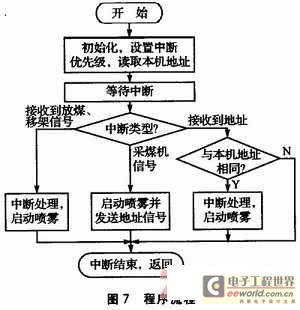
Conclusion
This design is an automatic spray dust control system based on power line carrier communication. The system has simple wiring, good dust reduction effect, and is suitable for coal mining working faces; at the same time, the LED lighting function greatly improves the underground lighting environment.
Previous article:Application of Passau60 industrial computer in train control center system
Next article:MAX6369–MAX6374 Pin-Programmable Watchdog Timers
- Popular Resources
- Popular amplifiers
- High signal-to-noise ratio MEMS microphone drives artificial intelligence interaction
- Advantages of using a differential-to-single-ended RF amplifier in a transmit signal chain design
- ON Semiconductor CEO Appears at Munich Electronica Show and Launches Treo Platform
- ON Semiconductor Launches Industry-Leading Analog and Mixed-Signal Platform
- Analog Devices ADAQ7767-1 μModule DAQ Solution for Rapid Development of Precision Data Acquisition Systems Now Available at Mouser
- Domestic high-precision, high-speed ADC chips are on the rise
- Microcontrollers that combine Hi-Fi, intelligence and USB multi-channel features – ushering in a new era of digital audio
- Using capacitive PGA, Naxin Micro launches high-precision multi-channel 24/16-bit Δ-Σ ADC
- Fully Differential Amplifier Provides High Voltage, Low Noise Signals for Precision Data Acquisition Signal Chain
- Innolux's intelligent steer-by-wire solution makes cars smarter and safer
- 8051 MCU - Parity Check
- How to efficiently balance the sensitivity of tactile sensing interfaces
- What should I do if the servo motor shakes? What causes the servo motor to shake quickly?
- 【Brushless Motor】Analysis of three-phase BLDC motor and sharing of two popular development boards
- Midea Industrial Technology's subsidiaries Clou Electronics and Hekang New Energy jointly appeared at the Munich Battery Energy Storage Exhibition and Solar Energy Exhibition
- Guoxin Sichen | Application of ferroelectric memory PB85RS2MC in power battery management, with a capacity of 2M
- Analysis of common faults of frequency converter
- In a head-on competition with Qualcomm, what kind of cockpit products has Intel come up with?
- Dalian Rongke's all-vanadium liquid flow battery energy storage equipment industrialization project has entered the sprint stage before production
- Allegro MicroSystems Introduces Advanced Magnetic and Inductive Position Sensing Solutions at Electronica 2024
- Car key in the left hand, liveness detection radar in the right hand, UWB is imperative for cars!
- After a decade of rapid development, domestic CIS has entered the market
- Aegis Dagger Battery + Thor EM-i Super Hybrid, Geely New Energy has thrown out two "king bombs"
- A brief discussion on functional safety - fault, error, and failure
- In the smart car 2.0 cycle, these core industry chains are facing major opportunities!
- The United States and Japan are developing new batteries. CATL faces challenges? How should China's new energy battery industry respond?
- Murata launches high-precision 6-axis inertial sensor for automobiles
- Ford patents pre-charge alarm to help save costs and respond to emergencies
- New real-time microcontroller system from Texas Instruments enables smarter processing in automotive and industrial applications
- I need help with a fully digital phase-locked loop Verilog code and modelsim simulation
- EEWORLD University Hall----Sharing of FOC ceiling fan application cases based on Lingdong MM32SPIN series MCU
- Solving for the transfer characteristic curve of an op amp
- What does the typical transmission distance of an infrared receiver mean?
- GD32307E-START power on + led control
- Common options for compiling c6x
- [Limited time sale] PICkit 3 In-Circuit Debugger is now available for 11.11 yuan with free shipping!
- [Silicon Labs BG22-EK4108A Bluetooth Development Evaluation] Evaluation 3: Try Keil/IAR Development
- Overview of TI's 28335 chip
- 【STM32WB55 Review】+First Impressions