Abstract: Thermocouples are commonly used in temperature measurement applications because of their ruggedness, reliability, and fast response time. This application note discusses the basic operation of thermocouples, including the definition and function of the reference junction (cold junction). It also provides considerations for selecting a cold junction temperature measurement device based on the specific application and presents three design examples.
Of course, thermocouples also have some defects in temperature measurement, such as poor linearity. Although they can measure a wider temperature range than RTDs and temperature sensor ICs, their linearity is greatly reduced. In addition, RTDs and temperature sensor ICs can provide higher sensitivity and accuracy, which are ideal for precise measurement systems. Thermocouple signal levels are very low and often require amplification or high-resolution data converters for processing.
If the above problems are excluded, the low price, ease of use and wide temperature range of thermocouples make them widely used.
Table 1. Commonly used thermocouple types
When two different types of metal are joined (welded) together to form two junctions, as shown in Figure 1a, the loop voltage is a function of the temperature difference between the two junctions. This phenomenon is called the Seebeck effect and is used to explain the process of converting thermal energy into electrical energy. The Seebeck effect is relative to the Peltier effect, which is used to explain the process of converting electrical energy into thermal energy. Typical applications include electrothermal coolers. As shown in Figure 1a, the measured voltage VOUT is the difference between the junction voltage at the sensing end (hot end) and the junction voltage at the reference end (cold end). Because VH and VC are generated by the temperature difference between the two junctions, VOUT is also a function of the temperature difference. The scaling factor, α, corresponds to the ratio of the voltage difference to the temperature difference and is called the Seebeck coefficient.
Figure 1a. The loop voltage is generated by the temperature difference between the two junctions of the thermocouple and is a result of the Seebeck effect.
Figure 1b. The common thermocouple configuration consists of two wires connected at one end, and the open end of each wire is connected to a copper thermostat. Figure 1b shows one of the most common thermocouple applications. This configuration introduces a third metal (intermediate metal) and two additional nodes. In this case, each open end is electrically connected to a copper wire. These wires add two additional nodes to the system. As long as the two nodes are at the same temperature, the intermediate metal (copper) will not affect the output voltage. This configuration allows the thermocouple to be used without a separate reference junction. VOUT is still a function of the difference between the hot and cold junction temperatures, which is related to the Seebeck coefficient. However, since the thermocouple measures a temperature difference, the cold junction temperature must be known in order to determine the actual temperature of the hot junction. The simplest case is when the cold junction temperature is 0°C (ice point). If TC = 0°C, then VOUT = VH. In this case, the voltage measured at the hot junction is a direct conversion of the junction temperature. The National Bureau of Standards (NBS) provides lookup tables that plot voltage characteristics versus temperature for various types of thermocouples. All data is based on a 0°C cold junction temperature. Using ice point as the reference point, the hot junction temperature can be determined by looking up VH in the appropriate table. In the early days of thermocouples, ice point was used as the standard reference point for thermocouples, but it is not practical to have an ice point reference temperature in most applications. If the cold junction temperature is not 0°C, then the cold junction temperature must be known in order to determine the actual hot junction temperature. The thermocouple output voltage must be compensated to take into account the voltage at the non-zero cold junction temperature, which is called cold junction compensation.
For devices with very high accuracy requirements, calibrated platinum RTDs can maintain high accuracy over a wide temperature range, but their cost is very high.
When the accuracy requirements are not very high, thermistors and silicon temperature sensor ICs can provide a higher cost-effectiveness. Thermistors have a wider temperature measurement range than silicon ICs, and sensor ICs have higher linearity, so the performance indicators are better. Correcting the nonlinearity of thermistors will occupy more microcontroller resources. Temperature sensor ICs have excellent linearity, but the temperature measurement range is very narrow.
In short, the cold junction temperature measurement device must be selected according to the actual needs of the system. Accuracy, temperature range, cost and linearity indicators need to be carefully considered to obtain the best cost-effectiveness.
Software linear approximation only requires the polynomial coefficients to be determined in advance and does not require storage, making it a more general solution. The disadvantage is that it takes a long time to solve multi-order polynomials. The higher the order of the polynomial, the longer the processing time, especially when the temperature range is wide. When the order of the polynomial is high, the lookup table provides a more accurate and efficient temperature measurement solution.
Before the advent of software testing solutions, analog linearization was often used to convert the measured voltage to temperature (in addition to manual lookup table retrieval). This hardware-based method uses analog circuits to correct for the nonlinearity of the thermocouple response. Its accuracy depends on the order of the correcting approximation polynomial, and this method is still used in current multimeters capable of testing thermocouple signals.
Example #1
In the circuit shown in Figure 2, a 16-bit Σ-Δ ADC converts the low-level thermocouple voltage into a 16-bit serial data output. An integrated programmable gain amplifier helps improve the ADC's resolution, which is necessary to process the small signal output of the thermocouple. The temperature sensing IC is mounted close to the thermocouple to measure the temperature near the cold junction. This method assumes that the IC temperature is approximately equal to the cold junction temperature. The cold junction temperature sensor output is digitized by channel 2 of the ADC. The 2.56V reference internal to the temperature sensor saves an external voltage reference IC. Figure 2. A local temperature sensing IC (MAX6610) determines the cold junction temperature. The temperature sensing IC is placed close to the thermocouple junction (cold junction), and the output voltages of the thermocouple and cold junction temperature sensor are converted by a 16-bit ADC (MX7705). When operating in bipolar mode, the ADC converts the positive and negative signals of the thermocouple and outputs them on channel 1. Channel 2 of the ADC converts the single-ended output voltage of the MAX6610 into a digital signal and provides it to the microcontroller. The output voltage of the temperature sensing IC is proportional to the cold junction temperature. To determine the hot junction temperature, the cold junction temperature must be determined first. The cold junction temperature is then converted to a corresponding thermoelectric voltage using a K-type thermocouple lookup table provided by NBS. This voltage is then added to the PGA gain-calibrated thermocouple reading, and the sum is converted to a temperature using the lookup table. The result is the hot junction temperature. Table 2 shows the temperature measurement results. The cold junction temperature ranged from -40°C to +85°C, and the hot junction was held at +100°C. The actual measurement results depend greatly on the accuracy of the local temperature sensing IC and the oven temperature. Table 2. The temperature measured by the circuit in Figure 2 at the cold and hot ends of different ovens.
* The "hot junction temperature" is a compensated value that is measured by the circuit.
Example #2
In the circuit shown in Figure 3, a remote temperature sensing IC measures the cold junction temperature of the circuit. Unlike a local temperature sensing IC, the IC does not need to be mounted close to the cold junction. Instead, the cold junction temperature is measured using an external diode-connected transistor. The transistor is mounted directly at the thermocouple junction. The temperature sensing IC converts the transistor's measured temperature into a digital output.
Channel 1 of the ADC converts the thermocouple voltage into a digital output. Channel 2 is not used and the input is directly grounded. An external 2.5V reference IC provides the reference voltage for the ADC.
Figure 3. The remote diode temperature sensing IC does not need to be close to the cold junction because it uses an external diode to sense the temperature. The MAX6002 provides the 2.5V reference voltage for the ADC.
Table 3 lists the temperature measurement results. The cold junction temperature range is: -40°C to +85°C, and the hot junction is held at +100°C. The actual measurement results will depend greatly on the accuracy of the remote diode temperature sensing IC and the oven temperature.
Table 3. Cold and hot junction temperature measurements of the circuit in Figure 3 in different ovens
* The "hot junction temperature" is the compensated value measured by the circuit.
Example #3
The 12-bit ADC in the circuit of Figure 4 has a temperature sensing diode that converts the ambient temperature into a voltage. The IC calculates the compensated hot junction temperature by processing the thermocouple voltage and the diode's sense voltage. The digital output is the compensated thermocouple test temperature, and the device temperature error is maintained within ±9 LSB over the 0°C to +700°C temperature range. Although this device has a wide temperature range, it cannot measure temperatures below 0°C.
Figure 4. An ADC with integrated cold junction compensation converts the thermocouple voltage into temperature without the need for external components.
Table 4 shows the measurement results of the circuit in Figure 4, with the cold junction temperature varied from 0°C to +70°C and the hot junction temperature held at +100°C.
Table 4. Cold and hot junction temperatures measured in different ovens for the circuit of Figure 4
* "Hot junction measured temperature" is a compensated value, measured by the circuit.
The selection criteria for cold end compensation devices are related to factors such as accuracy, cost, linearity, and temperature range. Platinum RTDs have the highest accuracy but are also the most expensive. Thermistors are low-priced and can operate over a wide temperature range, but their linearity is poor. Silicon temperature sensor detection ICs have a narrow operating temperature range, but have reasonable accuracy and linearity, and are relatively low in cost, which can meet the needs of most thermocouple applications.
Reference address:Thermocouple cold junction compensation
Overview
There are many types of transmitters in temperature measurement applications. Thermocouples are the most commonly used type and can be widely used in automobiles, homes and other fields. Compared with RTDs, thermistors, and temperature sensing integrated circuits (ICs), thermocouples can detect a wider temperature range and have a higher cost-effectiveness. In addition, the robustness, reliability and fast response time of thermocouples make them the first choice in various working environments.Of course, thermocouples also have some defects in temperature measurement, such as poor linearity. Although they can measure a wider temperature range than RTDs and temperature sensor ICs, their linearity is greatly reduced. In addition, RTDs and temperature sensor ICs can provide higher sensitivity and accuracy, which are ideal for precise measurement systems. Thermocouple signal levels are very low and often require amplification or high-resolution data converters for processing.
If the above problems are excluded, the low price, ease of use and wide temperature range of thermocouples make them widely used.
Thermocouple Basics
Thermocouples are differential temperature measurement devices that consist of two different metal/alloy wires, one for the positive terminal and the other for the negative terminal. Table 1 lists the four most common thermocouple types, the metals used, and the corresponding temperature measurement range. Each thermocouple has unique thermoelectric properties within its specified temperature range.Table 1. Commonly used thermocouple types
type | Positive terminal metal/alloy | Negative metal/alloy | Temperature range (°C) |
T | copper | Nickel Copper Alloy | -200 to +350 |
J | iron | Nickel Copper Alloy | 0 to +750 |
K | Nickel-chromium alloy | Nickel-based thermocouple alloys | -200 to +1250 |
E | Nickel-chromium alloy | Nickel Copper Alloy | -200 to +900 |
When two different types of metal are joined (welded) together to form two junctions, as shown in Figure 1a, the loop voltage is a function of the temperature difference between the two junctions. This phenomenon is called the Seebeck effect and is used to explain the process of converting thermal energy into electrical energy. The Seebeck effect is relative to the Peltier effect, which is used to explain the process of converting electrical energy into thermal energy. Typical applications include electrothermal coolers. As shown in Figure 1a, the measured voltage VOUT is the difference between the junction voltage at the sensing end (hot end) and the junction voltage at the reference end (cold end). Because VH and VC are generated by the temperature difference between the two junctions, VOUT is also a function of the temperature difference. The scaling factor, α, corresponds to the ratio of the voltage difference to the temperature difference and is called the Seebeck coefficient.
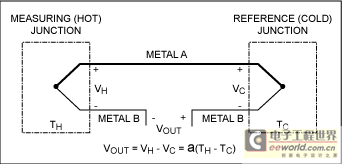
Figure 1a. The loop voltage is generated by the temperature difference between the two junctions of the thermocouple and is a result of the Seebeck effect.
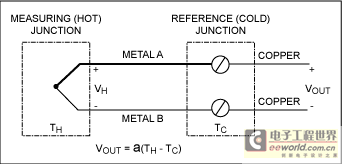
Figure 1b. The common thermocouple configuration consists of two wires connected at one end, and the open end of each wire is connected to a copper thermostat. Figure 1b shows one of the most common thermocouple applications. This configuration introduces a third metal (intermediate metal) and two additional nodes. In this case, each open end is electrically connected to a copper wire. These wires add two additional nodes to the system. As long as the two nodes are at the same temperature, the intermediate metal (copper) will not affect the output voltage. This configuration allows the thermocouple to be used without a separate reference junction. VOUT is still a function of the difference between the hot and cold junction temperatures, which is related to the Seebeck coefficient. However, since the thermocouple measures a temperature difference, the cold junction temperature must be known in order to determine the actual temperature of the hot junction. The simplest case is when the cold junction temperature is 0°C (ice point). If TC = 0°C, then VOUT = VH. In this case, the voltage measured at the hot junction is a direct conversion of the junction temperature. The National Bureau of Standards (NBS) provides lookup tables that plot voltage characteristics versus temperature for various types of thermocouples. All data is based on a 0°C cold junction temperature. Using ice point as the reference point, the hot junction temperature can be determined by looking up VH in the appropriate table. In the early days of thermocouples, ice point was used as the standard reference point for thermocouples, but it is not practical to have an ice point reference temperature in most applications. If the cold junction temperature is not 0°C, then the cold junction temperature must be known in order to determine the actual hot junction temperature. The thermocouple output voltage must be compensated to take into account the voltage at the non-zero cold junction temperature, which is called cold junction compensation.
Selecting a Cold Junction Temperature Measurement Device
As mentioned above, in order to achieve cold junction compensation, the cold junction temperature must be determined, which can be achieved by any type of temperature sensing device. Among the common temperature sensor ICs, thermistors and RTDs, different types of devices have different advantages and disadvantages and need to be selected according to the specific application.For devices with very high accuracy requirements, calibrated platinum RTDs can maintain high accuracy over a wide temperature range, but their cost is very high.
When the accuracy requirements are not very high, thermistors and silicon temperature sensor ICs can provide a higher cost-effectiveness. Thermistors have a wider temperature measurement range than silicon ICs, and sensor ICs have higher linearity, so the performance indicators are better. Correcting the nonlinearity of thermistors will occupy more microcontroller resources. Temperature sensor ICs have excellent linearity, but the temperature measurement range is very narrow.
In short, the cold junction temperature measurement device must be selected according to the actual needs of the system. Accuracy, temperature range, cost and linearity indicators need to be carefully considered to obtain the best cost-effectiveness.
Considerations
Once the cold junction compensation method is established, the compensated output voltage must be converted to the corresponding temperature. A simple method is to use the lookup table provided by NBS. Implementing the lookup table in software requires memory, but the lookup table provides a fast and accurate measurement solution for continuous repeated queries. Two other methods for converting thermocouple voltage to temperature are more complicated than the lookup table. These two methods are: 1) linear approximation using polynomial coefficients and 2) analog linearization of the thermocouple output signal.Software linear approximation only requires the polynomial coefficients to be determined in advance and does not require storage, making it a more general solution. The disadvantage is that it takes a long time to solve multi-order polynomials. The higher the order of the polynomial, the longer the processing time, especially when the temperature range is wide. When the order of the polynomial is high, the lookup table provides a more accurate and efficient temperature measurement solution.
Before the advent of software testing solutions, analog linearization was often used to convert the measured voltage to temperature (in addition to manual lookup table retrieval). This hardware-based method uses analog circuits to correct for the nonlinearity of the thermocouple response. Its accuracy depends on the order of the correcting approximation polynomial, and this method is still used in current multimeters capable of testing thermocouple signals.
Application Circuit
Three typical applications for cold junction compensation using silicon sensor ICs are discussed below. All three circuits are used to solve cold junction temperature compensation within a few degrees Celsius over a narrow temperature range (0°C to +70°C and -40°C to +85°C). The second circuit contains a remote diode temperature detector with a diode-connected transistor providing the test signal. The third circuit has built-in cold junction compensation in the analog-to-digital converter (ADC). All three circuits use K-type thermocouples (composed of nickel-chromium alloy and nickel-based thermocouple alloy) for temperature measurement.Example #1
In the circuit shown in Figure 2, a 16-bit Σ-Δ ADC converts the low-level thermocouple voltage into a 16-bit serial data output. An integrated programmable gain amplifier helps improve the ADC's resolution, which is necessary to process the small signal output of the thermocouple. The temperature sensing IC is mounted close to the thermocouple to measure the temperature near the cold junction. This method assumes that the IC temperature is approximately equal to the cold junction temperature. The cold junction temperature sensor output is digitized by channel 2 of the ADC. The 2.56V reference internal to the temperature sensor saves an external voltage reference IC. Figure 2. A local temperature sensing IC (MAX6610) determines the cold junction temperature. The temperature sensing IC is placed close to the thermocouple junction (cold junction), and the output voltages of the thermocouple and cold junction temperature sensor are converted by a 16-bit ADC (MX7705). When operating in bipolar mode, the ADC converts the positive and negative signals of the thermocouple and outputs them on channel 1. Channel 2 of the ADC converts the single-ended output voltage of the MAX6610 into a digital signal and provides it to the microcontroller. The output voltage of the temperature sensing IC is proportional to the cold junction temperature. To determine the hot junction temperature, the cold junction temperature must be determined first. The cold junction temperature is then converted to a corresponding thermoelectric voltage using a K-type thermocouple lookup table provided by NBS. This voltage is then added to the PGA gain-calibrated thermocouple reading, and the sum is converted to a temperature using the lookup table. The result is the hot junction temperature. Table 2 shows the temperature measurement results. The cold junction temperature ranged from -40°C to +85°C, and the hot junction was held at +100°C. The actual measurement results depend greatly on the accuracy of the local temperature sensing IC and the oven temperature. Table 2. The temperature measured by the circuit in Figure 2 at the cold and hot ends of different ovens.
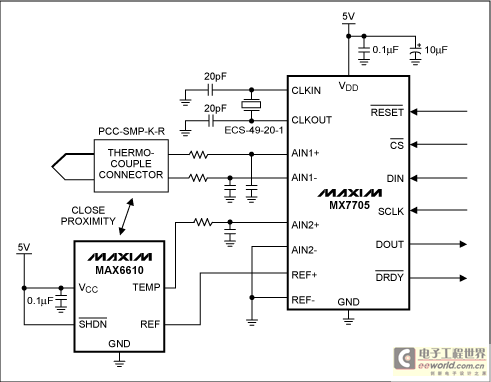
Cold junction
Temperature (°C) |
Hot end measurement
Temperature* (°C) |
|
Measurement #1 | -39.9 | +101.4 |
Measurement #2 | 0.0 | +101.5 |
Measurement #3 | +25.2 | +100.2 |
Measurement #4 | +85.0 | +99.0 |
Example #2
In the circuit shown in Figure 3, a remote temperature sensing IC measures the cold junction temperature of the circuit. Unlike a local temperature sensing IC, the IC does not need to be mounted close to the cold junction. Instead, the cold junction temperature is measured using an external diode-connected transistor. The transistor is mounted directly at the thermocouple junction. The temperature sensing IC converts the transistor's measured temperature into a digital output.
Channel 1 of the ADC converts the thermocouple voltage into a digital output. Channel 2 is not used and the input is directly grounded. An external 2.5V reference IC provides the reference voltage for the ADC.
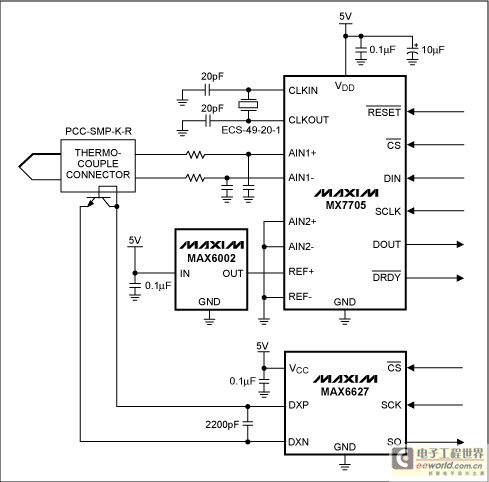
Figure 3. The remote diode temperature sensing IC does not need to be close to the cold junction because it uses an external diode to sense the temperature. The MAX6002 provides the 2.5V reference voltage for the ADC.
Table 3 lists the temperature measurement results. The cold junction temperature range is: -40°C to +85°C, and the hot junction is held at +100°C. The actual measurement results will depend greatly on the accuracy of the remote diode temperature sensing IC and the oven temperature.
Table 3. Cold and hot junction temperature measurements of the circuit in Figure 3 in different ovens
Cold junction
Temperature (°C) |
Hot end measurement
Temperature* (°C) |
|
Measurement #1 | -39.8 | +99.1 |
Measurement #2 | -0.3 | +98.4 |
Measurement #3 | +25.0 | +99.7 |
Measurement #4 | +85.1 | +101.5 |
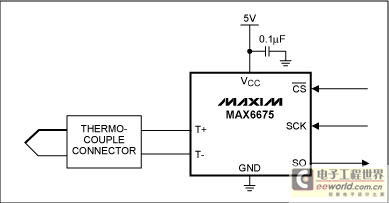
Cold junction
Temperature (°C) |
Hot end measurement
Temperature* (°C) |
|
Measurement #1 | 0.0 | +100.25 |
Measurement #2 | +25.2 | +100.25 |
Measurement #3 | +50.1 | +101.0 |
Measurement #4 | +70.0 | +101.25 |
in conclusion
Since thermocouples are differential temperature measurement devices, a reference point must be established when processing thermocouple signals. The voltage provided by the thermocouple reflects the temperature difference between the hot end and the cold end. If the cold end temperature and the hot end temperature relative to the cold end are known, the actual temperature value of the hot end can be determined.The selection criteria for cold end compensation devices are related to factors such as accuracy, cost, linearity, and temperature range. Platinum RTDs have the highest accuracy but are also the most expensive. Thermistors are low-priced and can operate over a wide temperature range, but their linearity is poor. Silicon temperature sensor detection ICs have a narrow operating temperature range, but have reasonable accuracy and linearity, and are relatively low in cost, which can meet the needs of most thermocouple applications.
Previous article:Tricks of stealing electricity using watt-hour meters and measures to prevent it
Next article:Using the 1-Wire® Link to Acquire Position Information—A Determinant
- Popular Resources
- Popular amplifiers
Recommended Content
Latest Analog Electronics Articles
- High signal-to-noise ratio MEMS microphone drives artificial intelligence interaction
- Advantages of using a differential-to-single-ended RF amplifier in a transmit signal chain design
- ON Semiconductor CEO Appears at Munich Electronica Show and Launches Treo Platform
- ON Semiconductor Launches Industry-Leading Analog and Mixed-Signal Platform
- Analog Devices ADAQ7767-1 μModule DAQ Solution for Rapid Development of Precision Data Acquisition Systems Now Available at Mouser
- Domestic high-precision, high-speed ADC chips are on the rise
- Microcontrollers that combine Hi-Fi, intelligence and USB multi-channel features – ushering in a new era of digital audio
- Using capacitive PGA, Naxin Micro launches high-precision multi-channel 24/16-bit Δ-Σ ADC
- Fully Differential Amplifier Provides High Voltage, Low Noise Signals for Precision Data Acquisition Signal Chain
MoreSelected Circuit Diagrams
MorePopular Articles
- Innolux's intelligent steer-by-wire solution makes cars smarter and safer
- 8051 MCU - Parity Check
- How to efficiently balance the sensitivity of tactile sensing interfaces
- What should I do if the servo motor shakes? What causes the servo motor to shake quickly?
- 【Brushless Motor】Analysis of three-phase BLDC motor and sharing of two popular development boards
- Midea Industrial Technology's subsidiaries Clou Electronics and Hekang New Energy jointly appeared at the Munich Battery Energy Storage Exhibition and Solar Energy Exhibition
- Guoxin Sichen | Application of ferroelectric memory PB85RS2MC in power battery management, with a capacity of 2M
- Analysis of common faults of frequency converter
- In a head-on competition with Qualcomm, what kind of cockpit products has Intel come up with?
- Dalian Rongke's all-vanadium liquid flow battery energy storage equipment industrialization project has entered the sprint stage before production
MoreDaily News
- Allegro MicroSystems Introduces Advanced Magnetic and Inductive Position Sensing Solutions at Electronica 2024
- Car key in the left hand, liveness detection radar in the right hand, UWB is imperative for cars!
- After a decade of rapid development, domestic CIS has entered the market
- Aegis Dagger Battery + Thor EM-i Super Hybrid, Geely New Energy has thrown out two "king bombs"
- A brief discussion on functional safety - fault, error, and failure
- In the smart car 2.0 cycle, these core industry chains are facing major opportunities!
- The United States and Japan are developing new batteries. CATL faces challenges? How should China's new energy battery industry respond?
- Murata launches high-precision 6-axis inertial sensor for automobiles
- Ford patents pre-charge alarm to help save costs and respond to emergencies
- New real-time microcontroller system from Texas Instruments enables smarter processing in automotive and industrial applications
Guess you like
- When BLE meets MEMS——Introduction to HID Report Descriptor
- MSP430 SPI Hardware Interface
- Understand the role and use of capacitors in one article
- The results of the GD32F350 contest (sharing experience & interaction) are as follows: Thanks to all the cool people in the contest
- Serial port printing problem after BLUENRG-1 wakes up from sleep
- 【I-Prober 520】Test Summary
- How can I wire this circuit to minimize interference?
- [RVB2601 Creative Application Development] + Stickman Player
- [Project source code] stmdb and ldmia assembly instructions
- Answer the question to win a reward: Looking for a reliable touch and gesture control solution? Come and learn about the new generation of AVR DA microcontrollers