Experimental study on clutch diaphragm spring parameter test system based on virtual instrument
This paper introduces the basic principle and composition of the microcomputer test system for diaphragm spring performance parameters based on virtual instrument, and expounds the design method and function of its hardware system and software system.
Keywords: virtual instrument; diaphragm spring; parameter test?
Application of VI in Parameter Testing of Clutch Diaphragm Sprin g
2.Jinan Shidai Shijin Instrument Co,Ltd. Jinan 250022, China)
Keywords: virtual instrument; diaphragm spring; parameter testing
The overall structure of the test system is a portal structure. A hydraulic system is installed on the workbench to achieve automatic control (Figure 1). The test system hardware mainly consists of a workbench, a crossbeam and a column to form its loading frame. The loading frame is supported on the box assembly. The loading cylinder is fixed in the box under the workbench, and its piston rod passes through the workbench. The lower pressure head is fixed on the piston rod of the loading cylinder, and its range of motion is adjusted by the travel switch. The upper oil cylinder is fixed on the adjustment screw, and the adjustment screw is fixed on the crossbeam by two nuts. The upper pressure head is connected to the adjustment screw through the oil cylinder and the force sensor. The adjustment screw can be adjusted up and down according to the space required by different types of springs. The displacement sensor A fixed on the lower part of the oil cylinder is used to measure the overall deformation of the spring when it is axially stressed. The three displacement sensors B1~B3 on the workbench are used to measure the deformation of the large end of the spring. The force sensor is used to measure the load applied to the diaphragm spring. The five sensor signals are transmitted to the data acquisition card after being processed by the signal conditioning circuit. After being processed by Labview (virtual instrument software), two important characteristic curves of the diaphragm spring are obtained: the load characteristic curve and the separation characteristic curve. According to actual needs, the characteristic points of the clutch cover assembly parameters are given on the system operation interface so that engineering and technical personnel can judge the working performance of the clutch.
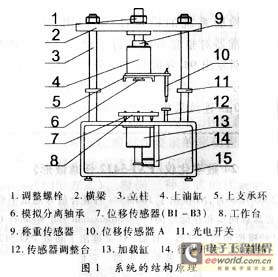
The software uses high-speed disk streaming technology during the design process to facilitate the playback and analysis of data afterwards. In addition, if various data analyses are performed during the data acquisition process, a lot of CPU time will be occupied, resulting in errors in data acquisition. The data must be saved at high speed. The block diagram program shown in Figure 2 is the data acquisition module of this system. First, use the Oper/Create /ReplaceFile.vi module to create a data stream file, then use the AI Config.vi module to configure the DAQ device, use the AI Start Config.vi module to start the DAQ, use a While loop and the AI Read Config.vi module to read the data from the DAQ cache continuously, and then the AI Write Config.vi module writes the data to the disk. After data collection is completed, use the AI Config.vi module to read the data for analysis and processing, and finally use AIClear.vi to end the execution of the entire system and release resources.
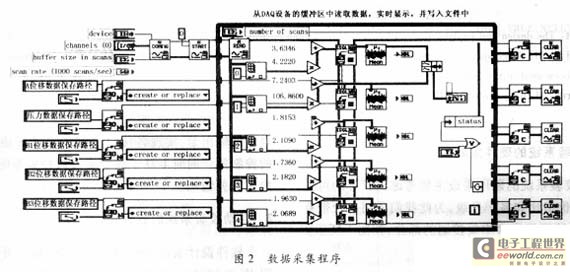
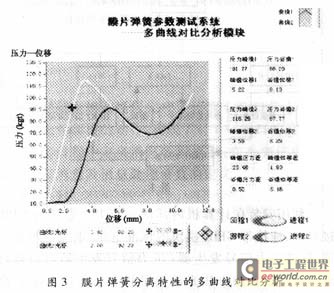
Previous article:Embedded Digital Storage Oscilloscope
Next article:Long-term analysis of bridge operation status based on LabVIEW
- Popular Resources
- Popular amplifiers
- High signal-to-noise ratio MEMS microphone drives artificial intelligence interaction
- Advantages of using a differential-to-single-ended RF amplifier in a transmit signal chain design
- ON Semiconductor CEO Appears at Munich Electronica Show and Launches Treo Platform
- ON Semiconductor Launches Industry-Leading Analog and Mixed-Signal Platform
- Analog Devices ADAQ7767-1 μModule DAQ Solution for Rapid Development of Precision Data Acquisition Systems Now Available at Mouser
- Domestic high-precision, high-speed ADC chips are on the rise
- Microcontrollers that combine Hi-Fi, intelligence and USB multi-channel features – ushering in a new era of digital audio
- Using capacitive PGA, Naxin Micro launches high-precision multi-channel 24/16-bit Δ-Σ ADC
- Fully Differential Amplifier Provides High Voltage, Low Noise Signals for Precision Data Acquisition Signal Chain
- Innolux's intelligent steer-by-wire solution makes cars smarter and safer
- 8051 MCU - Parity Check
- How to efficiently balance the sensitivity of tactile sensing interfaces
- What should I do if the servo motor shakes? What causes the servo motor to shake quickly?
- 【Brushless Motor】Analysis of three-phase BLDC motor and sharing of two popular development boards
- Midea Industrial Technology's subsidiaries Clou Electronics and Hekang New Energy jointly appeared at the Munich Battery Energy Storage Exhibition and Solar Energy Exhibition
- Guoxin Sichen | Application of ferroelectric memory PB85RS2MC in power battery management, with a capacity of 2M
- Analysis of common faults of frequency converter
- In a head-on competition with Qualcomm, what kind of cockpit products has Intel come up with?
- Dalian Rongke's all-vanadium liquid flow battery energy storage equipment industrialization project has entered the sprint stage before production
- Allegro MicroSystems Introduces Advanced Magnetic and Inductive Position Sensing Solutions at Electronica 2024
- Car key in the left hand, liveness detection radar in the right hand, UWB is imperative for cars!
- After a decade of rapid development, domestic CIS has entered the market
- Aegis Dagger Battery + Thor EM-i Super Hybrid, Geely New Energy has thrown out two "king bombs"
- A brief discussion on functional safety - fault, error, and failure
- In the smart car 2.0 cycle, these core industry chains are facing major opportunities!
- The United States and Japan are developing new batteries. CATL faces challenges? How should China's new energy battery industry respond?
- Murata launches high-precision 6-axis inertial sensor for automobiles
- Ford patents pre-charge alarm to help save costs and respond to emergencies
- New real-time microcontroller system from Texas Instruments enables smarter processing in automotive and industrial applications
- RF Ground - RF is not what you think "ground" is
- Nuvoton 003 Series Platform MS51 Replacement Update N76E003 Guide V1.0
- I, I, I have a question about relays and analog switches...
- Smart TFT with LUA script, making Tetris is so easy
- Last day! Apply for GD32VF series development board and new ATMEGA4809 for free, grab the last train and get on it!
- "Thank you for being here, thank you for the gift" - Thanksgiving Day Grab the Building & Give Thank You Gift Event
- Electronic component failure analysis and typical cases
- Hongmeng Development Board Neptune (VI) - Source Code Compilation 3
- When TEA1062 is on a call, the receiver is very quiet and no sound comes out of the MIC
- For CLC and CRC filtering, it is best to have high-frequency capacitors at both ends of the resistor and inductor. Could you please tell me how to configure the high-frequency capacitors?