Grating types and structures
A grating is a photoelectric device composed of many equally spaced light-transmitting slits and opaque lines that are evenly arranged alternately. According to the working principle, gratings can be divided into physical gratings and metrological gratings. Physical gratings are based on the diffraction phenomenon of gratings and are often used for spectral analysis and light wavelength measurements; metrological gratings are devices that use the moiré fringe phenomenon of gratings for measurement and are often used for precise displacement measurement.
According to the purpose and structural form, metrological gratings can be divided into long gratings for measuring linear displacement and circular gratings for measuring angular displacement. In practical applications, metrological gratings are divided into transmission gratings and reflection gratings. Transmission gratings are formed by uniformly engraving parallel and equally spaced stripes on transparent optical glass, while reflection gratings are formed by engraving equally spaced stripes on an opaque metal carrier. This section mainly discusses transmission metrological gratings.
The structure of the transmission grating is shown in Figure 12.1.1, where a is the width of the lines (opaque), b is the width of the gaps (transparent), and W = a+b is called the grating pitch. Generally, a=b, and a:b=1.1:0.9 can also be made. The line density of commonly used transmission gratings is generally 10, 25, 50, 100, or 250 lines per millimeter, and the line density is determined by the measurement accuracy.
Figure 12.1.1 Transmission grating
Working principle of grating digital sensor
Grating digital sensor usually consists of light source 5 (condenser 4), metering grating, photoelectric device 3 and measuring circuit, as shown in Figure 12.1.2. The metering grating consists of scale grating 1 (main grating) and indicator grating 2, so the metering grating is also called grating pair, which determines the measurement accuracy of the whole system. Generally, the main grating and indicator grating have the same line density, but the main grating is much longer than the indicator grating. During measurement, the main grating is connected to the object to be measured and moves with it, while the indicator grating is fixed, so the effective length of the main grating determines the measurement range of the sensor.
Figure 12.1.2 Grating digital sensor
1. Moiré fringes
Place the main grating and the scale grating on top of each other, keeping a small gap between them and making a small angle θ between the lines of the two gratings, as shown in Figure 12.1.3. When there is light, due to the light blocking effect (for gratings with a line density of ≤50 lines/mm) or the diffraction of light (for gratings with a line density of ≥100 lines/mm), alternating light and dark fringes are formed in a direction roughly perpendicular to the grating lines. At the overlap of the lines of the two gratings, light passes through the gap to form a bright band; at the offset of the two grating lines, a dark band is formed; these alternating light and dark fringes are called moiré fringes.
The relationship between
the spacing of the moiré fringes
and the grating pitch
W
and the angle
θ
(in rad)
between the two grating lines
is
(12.1.1)
(12.1.2)
K
is called the magnification factor.
Moiré fringes have the following important characteristics:
(1) The movement of the moiré fringes corresponds to the movement of the grating.
When the indicator grating is stationary, the angle θ between the main grating and the indicator grating is always maintained, and the main grating is relatively moved in the direction perpendicular to the grating, the moiré fringes will move in the direction of the grating grating; when the grating moves in the opposite direction, the moiré fringes also move in the opposite direction. For every grating pitch W that the main grating moves, the moiré fringes also move a spacing S accordingly. Therefore, by measuring the movement of the moiré fringes, the size and direction of the grating movement can be measured, which is much easier than measuring the grating directly.
(2) Moiré fringes have a displacement magnification effect.
When the main grating moves a grating pitch
W
in the direction perpendicular to the grating
, the moiré fringes move a fringe pitch
. When the angle
θ
between
the two grating gratings
is small, it can be seen from formula (12.1.1) that
when
W
is constant,
the smaller
θ
is, the larger B is, which is equivalent to magnifying the grating pitch
W
by 1/θ times. For example, for a grating with 50 lines/mm,
W
= 0.02mm. If
, then the spacing of the moiré fringes
, K = 573, is equivalent to magnifying the grating pitch by 573 times. Therefore, the magnification of the moiré fringes is quite large, and high-sensitivity displacement measurement can be achieved.
(3) Moiré fringes have an error averaging effect.
Moiré fringes are formed by many lines of the grating, and have an averaging effect on the line errors. They can largely eliminate the influence of local and short-period errors caused by the line errors, and can achieve a higher measurement accuracy than the line accuracy of the grating itself. Therefore, the metrological grating is particularly suitable for small displacement and high-precision displacement measurement.
(4) The spacing S of the moiré fringes changes with the angle θ of the grating lines
. Since the angle θ of the grating lines can be adjusted, the spacing of the moiré fringes can be adjusted according to the size of θ as needed, which brings convenience to practical applications.
When the relative movement direction of the two gratings remains unchanged, changing the direction of θ will change the movement direction of the moiré fringes.
2. Photoelectric conversion
The relative displacement of the main grating and the indicator grating produces moiré fringes. In order to measure the displacement of the moiré fringes, the optical signal must be converted into an electrical signal through a photoelectric device (such as a silicon photocell).
Place a photoelectric device at an appropriate position of the grating. When the two gratings move relative to each other, the light intensity on the photoelectric device moves with the moiré fringes, and the light intensity changes to a sine curve, as shown in Figure 12.1.4. At position a, the two grating lines overlap, the transmitted light intensity is the largest, and the electrical signal output by the photoelectric device is also the largest; at position c, the light intensity decreases because half of the light is blocked; at position d, the light is completely blocked and becomes completely black, with the lowest light intensity; if the grating continues to move, the light intensity transmitted to the photoelectric device gradually increases. The light intensity change on the photoelectric device is approximately a sine curve. When the grating moves one grating distance W, the light intensity changes by one cycle. The output voltage of the photoelectric device can be expressed by the formula
(12.1.3)
where
——the DC component in the output signal;
——the amplitude of the AC component in the output signal;
x——the relative displacement of the two gratings.
Figure 12.1.4 Relationship between grating displacement and light intensity output signal
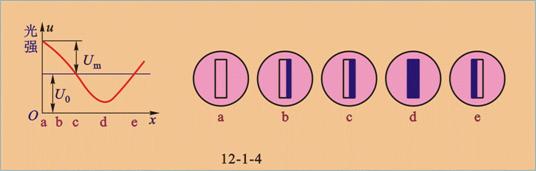
The sine signal is converted into a square wave pulse signal through a shaping circuit, and a square wave pulse is output after each cycle. In this way, the total number of pulses N corresponds to the number of grating pitches moved by the grating, so the displacement of the grating is
(12.1.4)
Direction identification and subdivision circuit
1. Direction identification circuit
Whether measuring linear displacement or angular displacement, it is necessary to be able to determine the direction of movement based on the output signal of the sensor, that is, to determine whether it is moving forward or backward, and whether it is rotating clockwise or counterclockwise.
However, the output of only one photoelectric element cannot determine the direction of movement of the grating, because when observing at one point, no matter which direction the main grating moves, the moiré fringes will alternate between light and dark. In order to identify the direction,
two photoelectric elements are usually placed at positions 1/4 of the moiré fringe spacing to obtain two signals with a phase difference of 90°, and then sent to the direction identification circuit shown in Figure 12.1.5 for processing.
Figure 12.1.5 Direction recognition circuit
Assume that when the main grating moves to the left, the moiré fringes move upward, and the two photoelectric elements output voltage signals U1 and U2 respectively, as shown in Figure 12.1.6 (a). After amplification and shaping, two square
wave signals
with a phase difference of
and
are obtained
.
After inversion
,
, and
after passing through the differential circuit, two groups of electrical pulses
,
, are obtained, which are input to the AND gates
and ,
respectively
. For AND gate Y1, since
is always low
when it is
at a high level, the pulse is blocked and the output of Y1 is zero; for AND gate Y2,
when it is at a high level,
it is also high, so the pulse is allowed to pass, and the addition and subtraction control trigger is triggered to set it to 1, and the reversible counter counts the pulses output by the AND gate Y`. Similarly, when the scale grating moves to the right, the output signal waveform is shown in Figure 12.1.6 (b), and the AND gate Y2 is blocked, and the Y1 output pulse signal sets the trigger to 0, and the reversible counter counts the pulses output by the AND gate Y2. Each time the main grating moves one grating pitch, the direction identification circuit outputs only one pulse. The number of pulses counted by the counter represents the displacement of the grating.
2. Subdivision circuit
The measurement resolution of the grating digital sensor is equal to one grating pitch. However, in precision detection, it is often necessary to measure a displacement smaller than the grating pitch. In order to improve the resolution, two methods can be used: 1) Increase the line density to reduce the grating pitch, but this method is limited by the grating line process. 2) Use subdivision technology to make the grating output evenly distributed n pulses each time it moves one grating pitch, thereby obtaining a division value smaller than the grating pitch, and improving the resolution to
.
There are many methods of subdivision, such as direct subdivision, bridge subdivision, phase-locked subdivision, modulated signal subdivision, software subdivision, etc. The following introduces the commonly used direct subdivision methods.
Figure 12.1.6 Waveforms at various points in the direction-finding circuit when the grating moves
Direct subdivision is also called position subdivision. The commonly used subdivision number is 4, so it is also called four-fold frequency subdivision. Figure 12.1.7 shows a four-fold frequency subdivision circuit and its waveform. On the basis of the above-mentioned direction identification circuit, the two sinusoidal signals with a phase difference of 90° are shaped and inverted respectively, and four square wave signals with phases of 0° (S), 90° (C), 180° (
), and 270° (
) can be obtained. After passing through the RC differential circuit, when the grating moves one grating pitch, 4 evenly distributed counting pulses can be obtained, and then sent to the reversible counter for addition or subtraction counting, which can increase the resolution by 4 times.
Figure 12.1.7 Four-times subdivision circuit and waveform
The advantage of the four-fold frequency subdivision is that the circuit is simple and there is no strict requirement for the waveform of the moiré fringe signal. Its disadvantage is that the subdivision number is not high. The subdivision number can be effectively increased by using bridge subdivision, modulation signal subdivision, phase-locked subdivision, etc. For the subdivision circuit, please refer to other materials.
Application of Grating Digital Sensor
Grating digital sensors have high measurement accuracy, high resolution, large measurement range, good dynamic characteristics, are suitable for non-contact dynamic measurement, are easy to realize automatic control, and are widely used in CNC machine tools and precision measuring equipment. However, when gratings are used in industrial sites, they have high requirements for the working environment, cannot withstand large shocks and vibrations, require sealing to prevent pollution from dust, oil, iron filings, etc., and have high costs.
Figure 12.1.8 shows the block diagram of the position detection and position closed-loop control system of grating digital sensors for CNC machine tools. The position command Pc generated by the control system controls the movement of the workbench. During the movement of the workbench, the grating digital sensor continuously detects the actual position of the workbench
and provides feedback (compared with the position command Pc) to form a position deviation Pe (Pe =
-Pc). When
=Pc, P = 0, indicating that the workbench has reached the command position, the servo motor stops, and the workbench stops accurately at the command position.
Figure
12.1.8
Block diagram of position control of CNC machine tools
1 - lead screw 2 - worktable 3 - grating reading head
Previous article:Grating types and structures
Next article:Operation method of reversing valve
- Popular Resources
- Popular amplifiers
- High signal-to-noise ratio MEMS microphone drives artificial intelligence interaction
- Advantages of using a differential-to-single-ended RF amplifier in a transmit signal chain design
- ON Semiconductor CEO Appears at Munich Electronica Show and Launches Treo Platform
- ON Semiconductor Launches Industry-Leading Analog and Mixed-Signal Platform
- Analog Devices ADAQ7767-1 μModule DAQ Solution for Rapid Development of Precision Data Acquisition Systems Now Available at Mouser
- Domestic high-precision, high-speed ADC chips are on the rise
- Microcontrollers that combine Hi-Fi, intelligence and USB multi-channel features – ushering in a new era of digital audio
- Using capacitive PGA, Naxin Micro launches high-precision multi-channel 24/16-bit Δ-Σ ADC
- Fully Differential Amplifier Provides High Voltage, Low Noise Signals for Precision Data Acquisition Signal Chain
- Innolux's intelligent steer-by-wire solution makes cars smarter and safer
- 8051 MCU - Parity Check
- How to efficiently balance the sensitivity of tactile sensing interfaces
- What should I do if the servo motor shakes? What causes the servo motor to shake quickly?
- 【Brushless Motor】Analysis of three-phase BLDC motor and sharing of two popular development boards
- Midea Industrial Technology's subsidiaries Clou Electronics and Hekang New Energy jointly appeared at the Munich Battery Energy Storage Exhibition and Solar Energy Exhibition
- Guoxin Sichen | Application of ferroelectric memory PB85RS2MC in power battery management, with a capacity of 2M
- Analysis of common faults of frequency converter
- In a head-on competition with Qualcomm, what kind of cockpit products has Intel come up with?
- Dalian Rongke's all-vanadium liquid flow battery energy storage equipment industrialization project has entered the sprint stage before production
- Allegro MicroSystems Introduces Advanced Magnetic and Inductive Position Sensing Solutions at Electronica 2024
- Car key in the left hand, liveness detection radar in the right hand, UWB is imperative for cars!
- After a decade of rapid development, domestic CIS has entered the market
- Aegis Dagger Battery + Thor EM-i Super Hybrid, Geely New Energy has thrown out two "king bombs"
- A brief discussion on functional safety - fault, error, and failure
- In the smart car 2.0 cycle, these core industry chains are facing major opportunities!
- The United States and Japan are developing new batteries. CATL faces challenges? How should China's new energy battery industry respond?
- Murata launches high-precision 6-axis inertial sensor for automobiles
- Ford patents pre-charge alarm to help save costs and respond to emergencies
- New real-time microcontroller system from Texas Instruments enables smarter processing in automotive and industrial applications
- Several interesting GIF animations
- EEWORLD University Hall----Live Replay: Application of TI Precision ADC in Transmitter
- 【TI recommended course】#What is I2C design tool? #
- BQ40Z50-R2 security mode introduction and password modification method
- [NUCLEO-L552ZE Review] Expansion board ws2812 power supply correction
- Don't stop me, I want to do mpy development!
- TPS23861 48V power supply has a small probability of burning out.
- Free resource download | Five trends driving change in power management
- My Journey of MCU Development (Part 2)
- 【Development and application based on NUCLEO-F746ZG motor】13. Parameter configuration - USART3 configuration