Organic Light-Emitting Diode (OLED) is considered to be the next generation of flat panel display emerging application technology due to its excellent characteristics such as self-luminescence, no need for backlight, high contrast, thin thickness, wide viewing angle, fast response speed, can be used for flexible panels, wide operating temperature range, simple structure and process, etc. Therefore, many manufacturers around the world are investing in research and development. According to our understanding and estimation, there are 38 mobile phones using OLED products in the current mobile phone market in my country [10 monochrome OLEDs, 15 regional color, 8 256 color, 3 full color] (see Table 1). According to what I have learned, there are already 7 OLED mobile phones being developed by domestic mobile phone design companies. In addition, there are SKD/CKD products and international brand products.
It is estimated that by the end of the year, there will be 50 OLED mobile phones in the Chinese mobile phone market, which will dominate the Chinese mobile phone market (see Table 2). At the same time, the data in Table 3 shows that OLED is expected to compete with STN-LCD and TFT-LCD technology in the future. So far, I would like to introduce the relevant knowledge of OLED to you.
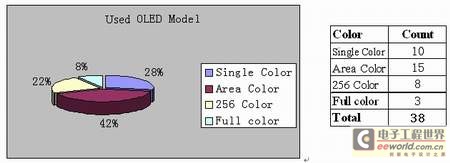
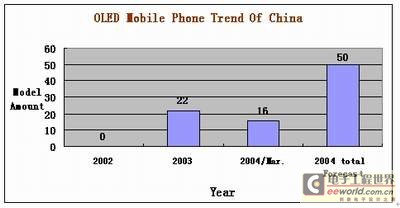
1. Development History of OLED
According to the material, it can be roughly divided into two types: small molecule type and polymer type. The small molecule type uses dyes and pigments as materials, called OLED, which was published by CW Tang (Dr. Deng Qingyun, born in Hong Kong, graduated from the Department of Chemistry of National Taiwan University) of Eastman Kodak Co. in 1987. The polymer type uses conjugated polymers as materials, called PLED (Polymer Light-emitting Diode) or LEP (Light-emitting Polymer Device), which was proposed by Cambridge University in 1990. In 1992, Cambridge established CDT (Cambrige Display Technology) to commercialize PLED.
2. The light-emitting principle of OLED
The light-emitting principle of OLED is similar to that of LED. It uses external bias to make holes and electrons start from the positive and negative electrodes respectively, and meet in the organic light-emitting layer to produce light. The anode is an ITO conductive film, and the cathode contains metals such as Mg, Al, and Li. Its basic structure is shown in (Figure 4). The color of OLED light depends on the material of the organic light-emitting layer, so manufacturers can get the desired color by changing the material of the light-emitting layer. It can also be understood that the main principle of light emission is that light is generated by the combination of electrons and holes. Depending on the different materials, the energy levels of electrons and holes are also different, which in turn produces light of different wavelengths (i.e. different colors).
3. OLED/Polymer OLED
OLED is a self-luminous material and does not require a backlight. It has a wide viewing angle, uniform image quality, fast response speed, is easy to colorize, can be illuminated with a simple driving circuit, has a simple process, can be made into a flexible panel, and meets the principle of being thin, light and short. Its application scope belongs to small and medium-sized panels. However, due to the high driving voltage of OLED, the energy efficiency is poor. PLED does not need to go through a thin film process and expensive vacuum devices, and the component structure has only two layers, which is relatively simple, so the investment cost is much lower than OLED. However, since PLED is not as good as OLED in color performance, each color attenuation constant is different, and color deviation must be compensated. At the same time, the bandwidth is large, and the luminous color is not easy to adjust, so the product life is also relatively short. At present, the main application scope of PLED is large-size panels. From the perspective of product market segmentation, the market niche of OLED will develop towards high-priced and high-value-added products, while PLED will develop towards large-volume and low-priced products.
4. Passive OLED and Active OLED
OLED can be divided into two types according to the driving method: passive driving (Passive Matrix; PMOLED) and active driving (Active Matrix; AMOLED). The driving method of OLED is current driving. The passive method has a simpler structure, and the driving current determines the grayscale. The resolution and image quality of small-sized products are quite good, but if it is to be developed into large-sized application products, it may increase power consumption and reduce life. The best corresponding is to use active driving method, because the active current rectification is better than the passive method, and it is not easy to cause leakage. At the same time, when using low-temperature polysilicon (Poly-si) TFT technology, the current can generate small TFTs with low impedance, which meets the needs of large-size and large-screen OLED displays.
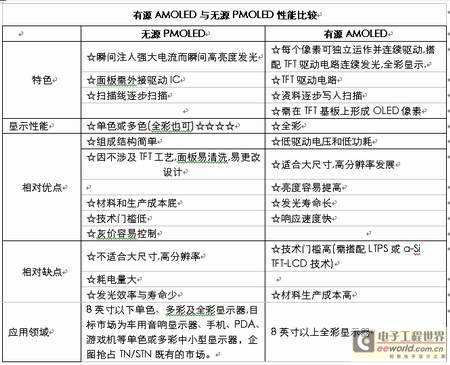
5. OLED colorization method
OLED can be divided into three types based on the colorization method: 1. "RGB three-color luminous structure", 2. "Color conversion structure [white light + color filter]", and 3. "Color filter film [blue light + color conversion layer]". Since the three-color luminous structure uses independent luminous materials RGB (red, green and blue) to arrange the three colors, it has the characteristics of good luminous efficiency and does not need to add a color filter or a color conversion layer film. It is currently the most commonly used method by manufacturers; but since the three-color method process uses a shadow mask evaporation method, the color fineness is poor. The color conversion method uses blue luminous materials to emit light, and a thin film is added in the middle when emitting light, so the luminous efficiency is not as good as the three-color luminous method. The color filter uses white light luminous materials to emit light, and a layer of color filter is added in the middle, so the luminous efficiency is also not as good as the three-color luminous method. Currently, there are not many manufacturers with white light technology.
6. Comparison between OLED and LCD technology
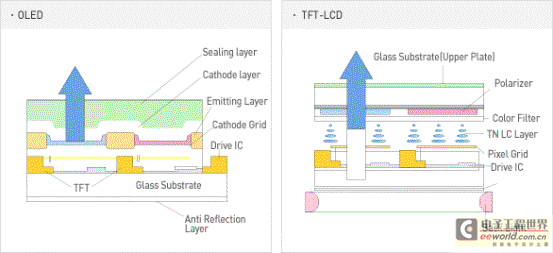
7. Comparison of product characteristics of OLED, TFT, and CSTN used in mobile phones?
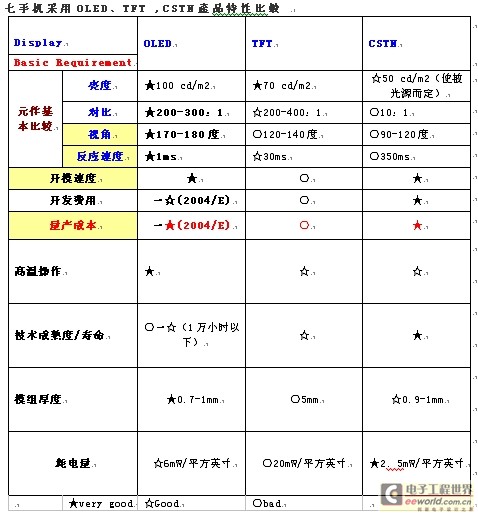
8. OLED Process
ITO panel [Array manufacturing process] → ITO panel (forming organic film) → OLED module packaging test → OLED finished product
Because OLED has a simple structure, the production process is not as complicated as the TFT-LCD manufacturing process. The production process includes organic materials, ITO panels (array manufacturing process), ITO panels (forming organic modules), and OLED module packaging and testing. In the array manufacturing process, the cleanliness of the ITO panel is one of the key factors for OLED quality. The panel cleaning method has become a trade secret of various manufacturers. The molecular structure of OLED will affect the integrity of the film. If the film is not flat, it will cause uneven light emission. The selection of appropriate organic materials will naturally become the research and development and future competitive niche of manufacturers. In addition, during the film formation process, the compound generation reaction will produce by-product impurities, which will affect the light emission efficiency and product life. Therefore, moderate purification in the manufacturing process is necessary. Furthermore, the materials of OLED devices are easily affected by moisture and oxygen, which can cause the devices to deteriorate and affect their service life. Therefore, moisture in the air must be removed during the packaging process after coating. The success or failure of the packaging technology directly affects the success or failure of the device. Packaging technology can be said to be a very important part of the entire manufacturing process. The best packaging method has not yet appeared. Although the OLED production process is relatively simple, there are still different difficulties to be overcome at each manufacturing process stage. Therefore, OLED currently has no standard mass production technology, and manufacturers still have a lot of room for development in manufacturing technology.
Summarize
OLED is most commonly used in secondary displays. Currently, about 20% of secondary displays use OLED. In the next two years, full-color OLED will be used for main and secondary displays. The most commonly used OLED will be OLED displays with a resolution of 96*64/96*96 pixels. These products with relatively low resolutions use passive matrix [passive] OLED technology, which has low manufacturing costs and low power consumption. The upper limit of passive matrix OLED technology is 128 rows. When it exceeds 128 rows, active matrix [Active] OLED technology is required. This is because the current load and power consumption of the cathode bus are limited when the passive matrix is addressed.
Although OLED full-color technology is not yet mature, with the increasing investment of global manufacturers in research and development, OLED technology will become more and more mature, and LCD, which is currently popular in mobile phones and portable products, will gradually give up a considerable part of the market to OLED.
-
OLED: Organic Light-Emitting Diode
-
IT indium tin oxid [Indium tin oxide]
-
Passive Matrix: PMOLED [Passive Matrix is also called passive drive OLED]
-
Active Matrix; AMOLED [Active Matrix is also called Active Drive OLED]
-
LTPS: Low Temperature Poly Silicon
-
SKD: Semi Knock-down
- CKD: complete knock-down
Previous article:OLED light-emitting principle
Next article:Performance and Application of TVS Transient Interference Suppressor
- Popular Resources
- Popular amplifiers
- High signal-to-noise ratio MEMS microphone drives artificial intelligence interaction
- Advantages of using a differential-to-single-ended RF amplifier in a transmit signal chain design
- ON Semiconductor CEO Appears at Munich Electronica Show and Launches Treo Platform
- ON Semiconductor Launches Industry-Leading Analog and Mixed-Signal Platform
- Analog Devices ADAQ7767-1 μModule DAQ Solution for Rapid Development of Precision Data Acquisition Systems Now Available at Mouser
- Domestic high-precision, high-speed ADC chips are on the rise
- Microcontrollers that combine Hi-Fi, intelligence and USB multi-channel features – ushering in a new era of digital audio
- Using capacitive PGA, Naxin Micro launches high-precision multi-channel 24/16-bit Δ-Σ ADC
- Fully Differential Amplifier Provides High Voltage, Low Noise Signals for Precision Data Acquisition Signal Chain
- Innolux's intelligent steer-by-wire solution makes cars smarter and safer
- 8051 MCU - Parity Check
- How to efficiently balance the sensitivity of tactile sensing interfaces
- What should I do if the servo motor shakes? What causes the servo motor to shake quickly?
- 【Brushless Motor】Analysis of three-phase BLDC motor and sharing of two popular development boards
- Midea Industrial Technology's subsidiaries Clou Electronics and Hekang New Energy jointly appeared at the Munich Battery Energy Storage Exhibition and Solar Energy Exhibition
- Guoxin Sichen | Application of ferroelectric memory PB85RS2MC in power battery management, with a capacity of 2M
- Analysis of common faults of frequency converter
- In a head-on competition with Qualcomm, what kind of cockpit products has Intel come up with?
- Dalian Rongke's all-vanadium liquid flow battery energy storage equipment industrialization project has entered the sprint stage before production
- Allegro MicroSystems Introduces Advanced Magnetic and Inductive Position Sensing Solutions at Electronica 2024
- Car key in the left hand, liveness detection radar in the right hand, UWB is imperative for cars!
- After a decade of rapid development, domestic CIS has entered the market
- Aegis Dagger Battery + Thor EM-i Super Hybrid, Geely New Energy has thrown out two "king bombs"
- A brief discussion on functional safety - fault, error, and failure
- In the smart car 2.0 cycle, these core industry chains are facing major opportunities!
- The United States and Japan are developing new batteries. CATL faces challenges? How should China's new energy battery industry respond?
- Murata launches high-precision 6-axis inertial sensor for automobiles
- Ford patents pre-charge alarm to help save costs and respond to emergencies
- New real-time microcontroller system from Texas Instruments enables smarter processing in automotive and industrial applications
- How does the uart.write function output three bytes of 0XFF 0XFF 0XFF (HEX data, not string data)?
- Chinese programmers VS American programmers, so vivid...
- The last version of Python2, Python 2.7.18, was released
- Unboxing the Renesas CPK-RA2L1 development board and preparing for evaluation
- DSP5402 development board schematic diagram
- Please tell me the setting function of deep sleep
- Driver transplantation of pedometer bracelet based on F103 and X-NUCLEO-IKS01A3
- [Jihai APM32E103VET6S Development Board] Review 1. Unboxing
- Using LM339 to generate triangle wave
- Are there any homemade downloaders such as st-link and j-link?