1. Comparison of several CNC DC regulated power supply design schemes
1.1 Circuit principles of several design schemes
Solution 1: Use analog discrete components and pure hardware to realize functions. Through power transformer, rectifier filter circuit and voltage regulator circuit, the voltage regulator can output ±5 V, ±12 V, ±15 V stably and can output 0~30 V voltage, as shown in Figure 1. However, due to the large dispersion of analog discrete components and the large influence between resistors and capacitors, the designed indicators are not high and do not meet the design requirements. In addition, there are many devices used, the connection is complex, the flexibility is poor, the power consumption is also large, and there are many solder joints and lines, which affects the stability and accuracy of the finished product.
Figure 1 Circuit principle of solution 1
Solution 2: This solution adopts the traditional adjustment tube solution. Its main feature is to use a set of dual counters to complete the control function of the system. The output of the binary counter is converted by D/A to control the reference voltage of the error amplification to control the output step. The decimal counter drives the digital tube to display the output voltage value after decoding. In order for the system to work properly, the dual counters must work synchronously.
Figure 2 Circuit principle of solution 2
Solution 3: This solution is different from Solution 1 in that it uses a set of decimal counters to decode and display the voltage on the one hand, and its output is used as the address input of the EPROM on the other hand. The output of the EPROM is converted by D/A to control the error amplification synchronization problem. However, since the control data is burned into the EPROM, the flexibility of system design is reduced.
Figure 3 Circuit principle of solution 3
Solution 4: This solution uses the 51 series single-chip microcomputer as the control unit of the whole machine. By changing the input digital quantity to change the output voltage value, the output voltage of the switch-controlled power supply changes, and the output voltage is indirectly changed. In order to enable the system to detect the actual output voltage value, the analog-to-digital conversion is performed through ADC0809, and the voltage is indirectly sampled in real time by the single-chip microcomputer, and then the data is processed. The single-chip microcomputer is used to program the output of the digital signal, and the analog quantity is output through the D/A converter (DA0830), and then the output voltage is controlled by the switch power supply circuit to achieve the purpose of voltage stabilization. The single-chip microcomputer system also takes into account the real-time monitoring of the constant voltage source. After the output voltage is converted from current to voltage, the analog quantity is converted into data quantity in real time through the A/D conversion chip. After the single-chip microcomputer analyzes and processes it, the voltage is more stable through the feedback link in the form of data, forming a stable voltage-controlled voltage source. In addition, the PWM-controlled switching power supply has the advantages of high integration, high cost performance, simplest peripheral circuit, best performance index, and can form a high-efficiency isolated switching power supply without industrial frequency transformer. Moreover, the cost is comparable to that of a linear regulated power supply of the same power, while the power efficiency is significantly improved and the size and weight are greatly reduced. [page]
Figure 4 Circuit principle of scheme 4
2. Comparison and demonstration of the schemes
(1) Output module
Solution 1: Use a linear voltage regulator to increase/decrease the output by changing its reference voltage. In this way, the influence of the ripple after rectification and filtering on the output ground cannot be ignored. This output can only be measured with a multimeter. In Solution 2 and Solution 3, an operational amplifier is used as the front-end operational amplifier. Since the operational amplifier has a large power supply voltage rejection ratio, the ripple voltage at the output end can be reduced. In Solution 1, the large capacitor connected in parallel at the output end of the linear voltage regulator to suppress the ripple reduces the response speed of the system, so that the output voltage is difficult to track the fast-changing input. The output voltage waveform in Solution 4 is the same as the D/A conversion output waveform. It can not only output DC level, but also generate a variety of waveform outputs as long as the quantized data of the waveform is generated in advance, so that the system has a signal source with a certain driving capability.
(2) CNC module
Solution 1 uses pure hardware to control the output of voltage. The most basic circuit principle analysis requires the calculation of the load size and the selection of the voltage regulator. Solution 2 and Solution 3 use medium and small-scale devices to implement the numerical control part of the system. Many chips are used, resulting in complicated internal circuit interface signals, many interrelationships in the middle, and poor anti-interference ability. For example, once the dual counters in Solution 1 count out of sync, the displayed voltage will be inconsistent with the output voltage. In Solution 4, the AT89C51 microcontroller is used to complete the functions of the entire numerical control part. At the same time, as an intelligent programmable device, AT89C51 is convenient for the expansion of system functions.
Figure 5 Scheme 5 CNC module
(3) Control module
In this system, a PWM regulation circuit with D/A conversion function, a chopper circuit, a current regulator and an adjustable voltage regulator (LM317) are used to control the output reference voltage. A/D conversion sampling is used to make the output more accurate, with small ripple, expandable current, and easy circuit protection.
(4) Display module
The display output in Scheme 2 and Scheme 3 directly decodes and displays the quantized value of the voltage. The displayed value is the input of the D/A conversion. Due to the error introduced by the D/A conversion and the power drive circuit, there may be a large deviation between the displayed value and the actual output value of the power supply. Scheme 4 uses an A/D conversion circuit to sample the output voltage, analyze and process it through the single-chip microcomputer, and make the voltage more stable through the data feedback link, so that the deviation between the displayed value and the actual output is minimized. Scheme 4 uses a 4-bit digital voltmeter to directly sample the output voltage and display the actual output voltage value. Once the system works abnormally and the deviation between the preset value and the output value is too large, the user can process it according to the information. The query time of the keyboard/display is also used to improve the CPU utilization.
3. Conclusion
As mentioned earlier, although Scheme 3 has many advantages over the previous two, Schemes 1 and 2 are not unfeasible for meeting the design requirements, and they even have advantages in some aspects. One of the important considerations for adopting Scheme 4 is that the system uses a single-chip microcomputer, which makes further functional expansion more convenient.
Previous article:Design of wireless sensor telemetry system
Next article:Design of wireless access point based on Bluetooth
Recommended ReadingLatest update time:2024-11-15 15:04
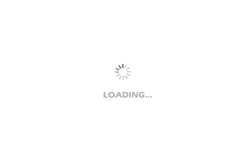
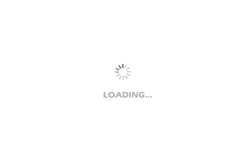
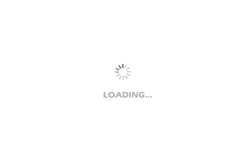
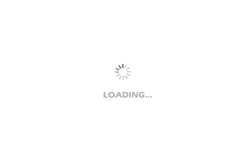
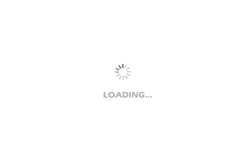
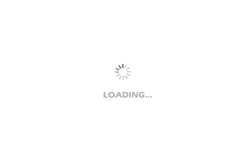
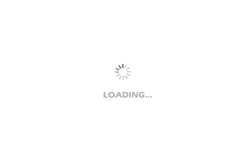
- Popular Resources
- Popular amplifiers
- Learn ARM development(16)
- Learn ARM development(17)
- Learn ARM development(18)
- Embedded system debugging simulation tool
- A small question that has been bothering me recently has finally been solved~~
- Learn ARM development (1)
- Learn ARM development (2)
- Learn ARM development (4)
- Learn ARM development (6)
Professor at Beihang University, dedicated to promoting microcontrollers and embedded systems for over 20 years.
- LED chemical incompatibility test to see which chemicals LEDs can be used with
- Application of ARM9 hardware coprocessor on WinCE embedded motherboard
- What are the key points for selecting rotor flowmeter?
- LM317 high power charger circuit
- A brief analysis of Embest's application and development of embedded medical devices
- Single-phase RC protection circuit
- stm32 PVD programmable voltage monitor
- Introduction and measurement of edge trigger and level trigger of 51 single chip microcomputer
- Improved design of Linux system software shell protection technology
- What to do if the ABB robot protection device stops
- Analysis of the application of several common contact parts in high-voltage connectors of new energy vehicles
- Wiring harness durability test and contact voltage drop test method
- From probes to power supplies, Tektronix is leading the way in comprehensive innovation in power electronics testing
- From probes to power supplies, Tektronix is leading the way in comprehensive innovation in power electronics testing
- Sn-doped CuO nanostructure-based ethanol gas sensor for real-time drunk driving detection in vehicles
- Design considerations for automotive battery wiring harness
- Do you know all the various motors commonly used in automotive electronics?
- What are the functions of the Internet of Vehicles? What are the uses and benefits of the Internet of Vehicles?
- Power Inverter - A critical safety system for electric vehicles
- Analysis of the information security mechanism of AUTOSAR, the automotive embedded software framework
- AD 20.2.5.213
- Use Solve
- [Raspberry Pi 4B Review] + Building a file server
- Capacitor connected between GS
- RS485 MODBUS RTU Communication Protocol
- [Online Live Broadcast] E-sports veterans say | As preparations for the e-sports competitions are underway, RIGOL will meet you in the air
- PPT materials
- Arduino's new product Nicla Vision
- The STM8S003F3P6 chip is very interesting
- 【Wireless closed-loop feedback system for desktop robotic arms】