1 Overview
Universal memory IC card is made of universal memory chip package. It has been widely used in various fields because of its simple structure and function, low production cost and convenient use. At present, most universal memory chips used in IC cards are E2PROM. The commonly used protocols are mainly two-wire serial connection protocol (I2C) and three-wire serial link protocol. Among them, the more commonly used are AT24 series chips produced by ATMEL. Take AT24C01 in this series as an example. It has a storage capacity of 1k, is suitable for low voltage/standard voltage operation of 2V~5V, and has the advantages of low power consumption and high reliability. Although AT89C2051 is a low-end model of ATMEL's 89 series microcontroller, it has 2k FLASH ROM (reprogrammable flash memory), 128×8-bit internal RAM and full static operation mode, and also has low power consumption and strong functions. Taking AT24C2051 as an example, the working principle and basic circuit connection of the universal memory IC card are introduced below. The circuit is simple, flexible to use, and can reliably read and write universal memory IC cards.
2 Hardware Features
2.1 Characteristics of AT24 Series Memory
AT24 series memory chips are manufactured using CMOS technology and have a built-in high-voltage pump, which can work under single voltage supply conditions. Its standard package is an 8-pin DIP package, and the functions of each pin are as follows:
SCL: Serial clock. At the rising edge of this pin, the system inputs data to each EEPROM device and outputs it at the falling edge.
SDA: Serial Data. This pin is open drain driven and can transmit data in both directions.
A0, A1, A2: Device/page addressing. Device address input terminals. In AT24C01/02, this pin is hard-wired.
Vcc: Generally input +5V operating voltage.
Figure 1 is a contact diagram of an IC card that complies with the ISO7816-2 standard. For the AT24 series universal memory IC card, only four contacts are usually used. The internal configuration of the AT24C01 is 128 8-bit bytes, and a 7-bit address is required for random word addressing.
2.2 Bus Status and Timing
The SCL and SDA buses of A24C01 can be pulled up to a high level through a resistor, and the data on SDA can only be changed periodically when SCL is at a low level. When SCL is at a high level, the change of SDA indicates the "start" and "stop" states. At this time, all addresses and data words are input and output from the EEPROM in 8-bit serial code.
Start state: When SCL is high, SDA changes from high to low. This command must be executed before other commands.
Stop state: When SCL is high, SDA changes from low to high. This command terminates all communications.
Confirmation: After receiving the data, the devices on the same bus confirm it by setting SDA to a low level.
2.3 Device Addressing
The AT24 series EEPROM requires an 8-bit device address immediately after the start state to perform read and write operations. The upper 4 bits of the device address code are 1, 0, 1, 0. For AT24C01/02, the three bits after the upper 4 bits of the address code are the device address code, corresponding to their hard-wired pins. The lowest bit should be the read and write selection bit, which can trigger a read operation when set to 0.
The specific format is as follows:
1 | 0 | 1 | 0 | A2 | A1 | A0 | R/W |
2.4 AT89C2051 chip
AT89C2051 is compatible with MCS-51 products. It has 2k FLASH ROM, 128 bytes ROM, 15 I/O pins, two 16-bit timers/counters, a five-vector two-level interrupt structure, a full-duplex serial port, a precision analog comparator, and an on-chip oscillator circuit and clock circuit. Its P1 and P3 ports are bidirectional I/O ports, of which P1.2~P1.7, P3.0~P3.5 and P3.7 have internal pull-up resistors. When AT89C2051 is used as an input terminal, "1" will be written to the pin first to turn off the internal MOS tube so that the pin is in a suspended state, thereby obtaining a high-impedance input. [page]
FIG. 2 is a basic circuit connection diagram of a general-purpose memory IC card.
3 Read and write operation software
When the system uses a 6MHz crystal oscillator, the defined I/O lines and device addresses are as follows:
SCL BIT P1.7
SDA BIT P1.6
DEVICEAD_W DATA 10100000B ; Write card device address
DEVICEAD_R DATA 10100001B ; Card reader device address
3.1 Start Condition (START_IC)
In the start condition, when SCL is high, SDA changes from high to low. The procedure is as follows:
START_IC: CLR SCL; SDA is allowed to change only when SCL is low
NOP; add a null instruction delay to ensure signal reliability
NOP
SETB SDA
NOP
NOP
SETB SCL
NOP
NOP
CLR SDA
NOP
NOP
CLR SCL
NOP
RET
3.2 Stop Condition (STOP_C)
In the stop condition, when SCL is high, SDA changes from low to high. The procedure is as follows:
STOP_IC:CLR SCL
NOP
NOP
CLR SDA
NOP
NOP
SETB SCL
NOP
NOP
SETB SDA
NOP
NOP
CLR SCL
NOP
NOP
CLR SDA
RET
3.3 Acknowledgement signal (ACK_IC)
When the receiver responds, the SDA level is pulled low after each byte is received. The procedure is as follows:
ACK_IC:CLR SCL
NOP
NOP
CLR SDA
NOP
NOP
SEIB SCL
NOP
NOP
CLR SCL[page]
NOP
SETB SDA
NOP
RET
3.4 Write one byte of data to the IC card (WR_BYTE)
In the following program, parameter A represents the source data and R5 represents the number of bytes.
WR_BYTE: MOV R5, #08; one byte of 8-bit data
CLR SCL
NOP
NOP
WR_BYTE1: RLC A; left shift with carry, A.8->C
MOV SDA, C; Change the data on SDA when SCL is low
NOP
SETB SCL; pull up SCL to send data out
NOP
NOP
CLR SCL
NOP
NOP
DJNZ R5, WR_BYTE1; send 8 bits of data in A in sequence
SETB SDA
SETB SCL
JB SDA, $; Waiting for IC card confirmation signal
CLR SCL
NOP
RET
The main function of this subroutine is to sequentially shift the 8-bit data of one byte in A to the left according to the defined timing and transmit it through the pin. When one byte is sent, wait for the confirmation signal sent back by the IC card.
3.5 Read one byte from IC card (RD+BYTE)
The source program to read one byte from the IC card is as follows:
RD_BYTE: MOV R5, #08
SETB SDA; device SDA is in read state
CLR A ; Clear the A register
RD_BTYE1: MOV C, SDA; read one bit of data to the carry bit
RLC A; Left shift data to A.0
SETB SCL
NOP
NOP
CLR SCL
NOP
NOP
DJNZ R5, RD_BYTE1; read out 8 bits of data into A in sequence
RET ; No response signal
This program can be used to store the read data in A. It should be noted that the device that reads the data does not respond by confirming the status, but generates a stop status afterwards. [page]
3.6 Byte write mode write data (WRITE_BYTE)
The parameters in the following program are: R6= =destination address, A= =data; the data is as follows:
WRITE_BYTE: PUSH ACC; save the data in A
LCALL START_IC ; send start signal
MOV A, #DEVICEAD_W; write device address
LCAL WR_BYTE
MOV A, R6 ; write byte address
LCALL WR_BYTE
POP ACC; Restore data in A
LCALL WR_BYTE ;Write data
LCALL STOP_IC
RET
After receiving 8 bits of data, the EEPROM will send back a confirmation signal through SDA, and the transmitting device must terminate the write operation with a stop state. At this time, the EEPROM will enter a write cycle of the internal fixed memory and prohibit all inputs during this period, and will not respond to the communication until the write operation is completed. The write cycle can be customized, with a maximum of 10ms.
3.7 Write data in page write mode (WRITE_PAGE)
The parameters in the following program are P0= = source pointer, R6= = destination address, R7= = page length.
WRITE_PAGE: LCALL START_IC
MOV A, #DEVICEAD_W
LCALL WR_BYTE
MOV A, R6
LCALL WR_BYTE
WRITE_PAGE1: MOV A, @R0
LCALL WR_BYTE
INC R0
DJNZ R7, WRITE_PAGE1
LCALL STOP_IC
RET
AT24C01/02 can use the above program to write 8-byte pages. Its operation is similar to writing bytes. The difference is that it does not need to stop after the first byte is sent. After receiving the confirmation signal, it sends 7 bytes of data code and finally stops the page write sequence. The page of AT24C04/08/16 is 16 bytes.
3.8 Immediate Address Read Mode (READ_BYTEC)
The procedure for reading one byte of data in immediate address read mode is as follows: READ_BYTEC: LCALL START_IC
MOV A, #DEVICEAD_R
LCALL WR_BYTE
LCALL RD_BYTE ;Read the default address data
LCALL STOP_IC ;Send stop status response
RET
After the program is executed, its internal data word address pointer will remain at the last address accessed by the last read or write operation, and will increment by 1 and remain valid during the chip power-on period. Only when the address is at the end of the page will the next access scroll to the first address of the page.
3.9 Random Address Read Mode (READ_BYTER)
In the following program, R6 = = source address, the program is as follows:
READ_BYTER: LCALL START_IC
MOV A, #DEVICEAD_W ; Execute a null byte write sequence
LCALL WR_BYTE ; load data address
MOV A, R6
LCALL WR_BYTE
LCALL START_IC
MOV A, #DEVICEAD_R; immediate address read
LCALL WR_BYTE
LCALL DR_BYTE
LCALL STOP_IC
RET
The read mode requires a byte write sequence to load the data address. After the device and data address are written and acknowledged, another start condition is generated and the address of the read device is sent, stimulating an immediate address read.
3.10 Sequential Address Read (READ_BYTES)
In the following program: R0 = = destination pointer; R7 = = data length, the program is as follows:
READ+BYTES:LCALL START_IC
MOV A, #DEVICEAD_R
LCALL WR_BYTE
READ_BYTES2: LCALL RD_BYTE
MOV @R0, A; store data to the destination address
INC R0
DJNZ R7, READ_BYTES1
LCALL STOP_IC ;Stop after reading or writing the specified length
RET
READ_BYTES1: LCALL ACK_IC; send confirmation signal SJMP after receiving data READ_BYTES2
The sequential read is triggered by an immediate address read or a random address read, and responds with a confirmation signal after receiving a byte of data. When the reading device responds with a stop state, the operation is terminated.
4 Conclusion
The system has a simple structure and high reliability in actual operation. It also has certain scalability and can be directly connected to the computer through the serial port of the microcontroller after level conversion for data communication. In addition, it can also be connected to other pins or card holder contacts as needed. If the circuit and program are properly improved, encryption cards and CPU cards can also be read and written.
Previous article:Development of a wide range and high precision optical fiber temperature sensor based on single chip microcomputer
Next article:Design Method of Realizing Digital Phase Converter Using Single Chip Microcomputer
Recommended ReadingLatest update time:2024-11-16 19:52
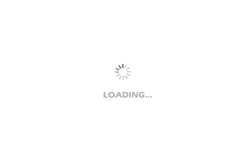
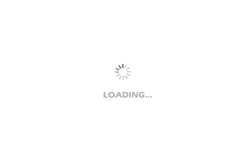
- Popular Resources
- Popular amplifiers
Professor at Beihang University, dedicated to promoting microcontrollers and embedded systems for over 20 years.
- Innolux's intelligent steer-by-wire solution makes cars smarter and safer
- 8051 MCU - Parity Check
- How to efficiently balance the sensitivity of tactile sensing interfaces
- What should I do if the servo motor shakes? What causes the servo motor to shake quickly?
- 【Brushless Motor】Analysis of three-phase BLDC motor and sharing of two popular development boards
- Midea Industrial Technology's subsidiaries Clou Electronics and Hekang New Energy jointly appeared at the Munich Battery Energy Storage Exhibition and Solar Energy Exhibition
- Guoxin Sichen | Application of ferroelectric memory PB85RS2MC in power battery management, with a capacity of 2M
- Analysis of common faults of frequency converter
- In a head-on competition with Qualcomm, what kind of cockpit products has Intel come up with?
- Dalian Rongke's all-vanadium liquid flow battery energy storage equipment industrialization project has entered the sprint stage before production
- Allegro MicroSystems Introduces Advanced Magnetic and Inductive Position Sensing Solutions at Electronica 2024
- Car key in the left hand, liveness detection radar in the right hand, UWB is imperative for cars!
- After a decade of rapid development, domestic CIS has entered the market
- Aegis Dagger Battery + Thor EM-i Super Hybrid, Geely New Energy has thrown out two "king bombs"
- A brief discussion on functional safety - fault, error, and failure
- In the smart car 2.0 cycle, these core industry chains are facing major opportunities!
- The United States and Japan are developing new batteries. CATL faces challenges? How should China's new energy battery industry respond?
- Murata launches high-precision 6-axis inertial sensor for automobiles
- Ford patents pre-charge alarm to help save costs and respond to emergencies
- New real-time microcontroller system from Texas Instruments enables smarter processing in automotive and industrial applications
- How to deal with unused pins of STM32L151 low power consumption
- What is the principle of this temperature measuring water cup? Doesn't it need to replace the battery?
- Why can byte addresses overlap with bit addresses?
- Creative Cube
- 10 ways to dissipate heat from PCB!!!
- LOTO Lesson 3: Frequency Response Curve Plotting --- 3 groups of RC low-pass filter tests with different parameters
- Three major programming languages for the development of the Internet of Things
- [Shanghai Hangxin ACM32F070 development board + touch function evaluation board evaluation] Transplant RT-Thread Nano
- Since it is so similar to inductors, why can you only use ferrite beads in your circuit?
- Device tree interrupt node