Requirements for the control device of the six-sided press
The six-sided top press is a key equipment for synthetic diamond synthesis. It has the characteristics of multiple specifications and high degree of automation. In the past, it was controlled by relay-contactor mode. Its logical relationship is cumbersome and a large number of relays are used (more than 40), so the swelling rate is high. The failure of the relay action often causes the pressing block to be smashed or even damages the top hammer, which increases the consumption of raw and auxiliary materials and affects the normal operation of the equipment. In addition, the six-sided top press also has certain requirements for the positioning accuracy and synchronization performance of the six pressure cylinders. The past relay-contactor control method has the problems of slow response speed, slow action, sticky armature, poor contact, etc., which makes the positioning and synchronization performance of the six cylinders worse and increases the chance of damage to the hard and gold top hammers. Therefore, the six-sided top press has the following requirements for the control device:
1. High reliability
2. Six-cylinder positioning and synchronization control should be good
In view of the above two basic requirements, combined with the process characteristics of the six-sided top press, we use PLC to control the press to work according to the following procedures (as shown in the right figure):
PLC Model Selection
The focus of PLC model selection is nothing more than the following aspects: 1. Determine the control scale, that is, the number of I/O points; 2. Price; 3. Whether the after-sales service is guaranteed. After sufficient research and considering the convenience of future maintenance, we finally decided to use the SR-21PLC produced by the Sino-foreign joint venture Wuxi Huaguang Electronics Co., Ltd. This is a small PLC with relatively high performance and price. The maximum number of I/O points is 168 points, the maximum capacity is 1.7K~3.7K instruction words, modular structure, flexible configuration, and a variety of I/O modules and special function modules. This PLC has rich instructions, data processing functions, and can be connected to the host computer to form an industrial local network. The peripheral equipment that matches it can basically meet user requirements, with a printer interface, EPROM writer, and can be connected to a tape recorder.
Control device configuration
Based on the configuration principles established by the press process characteristics, the basic requirements for the control device and the cost of the entire device, we decided to use a PLC with 80 I/O points. In order to facilitate future operation, a programmer and printer interface unit were also configured.
Circuit Design
We connect the six definition numbers 122~127 to the proximity switch input signal, which are used as monitoring for whether the right, front and upper three-cylinder pistons are offside when moving forward in the empty stroke and whether the six cylinders (including the left, right and lower three-cylinder pistons) are running at the same time (i.e. synchronous action) when filling. The rest of the I/O is connected to buttons, travel switches, external time relays, contactors, 220V AC solenoid valves, indicator lights and other electrical components. In the actual installation process, in order to prevent electromagnetic interference, all input lines are strictly separated from strong current wires; the proximity switch input signal line uses twisted pair wires; an isolation transformer is installed on the PLC power supply side; and RC absorbers are connected to both ends of all solenoid valves and contactor coils. Considering the cost and the PLC's interference suppressor from the power supply.
Software design and application of data processing functions
1. Software design:
For the sake of convenience and space saving, we only list the automatic engineering flow chart here.
The segmented working procedure is basically the same as the automatic working procedure, except that the pressure will not be automatically released immediately after the pressure maintenance is completed. The operator needs to press the supercharger pressure relief (i.e. segmented pressure relief) button to release the pressure, and then the procedure ends. The adjustment procedure is mainly used to manually adjust the position of the six-cylinder piston.
2. Application of data processing functions
Due to space limitations, we will only illustrate here the use of SR-21 data processing instructions to prevent multiple buttons from being operated simultaneously during six-cylinder synchronous monitoring and adjustment, and will explain them one by one below.
(1) Synchronous monitoring program module
The left figure is a block diagram of the synchronous monitoring program module. The delay in the block diagram is set according to the speed of the six-cylinder piston movement response in the specific equipment. A short time requires that the six-cylinder pistons basically start moving at the same time when filling, and a long time allows the six-cylinder pistons to not start moving at the same time at the moment of filling. Due to the adjustment of the hydraulic system, the length of the high-pressure oil circuit, the friction resistance of the piston, the size of the flow rate and other factors that may affect the speed of each cylinder piston response, there will always be a phenomenon of slow movement of the piston movement of a few cylinders. When this phenomenon is more serious, it may cause the six top hammers to be not on the center line when the six cylinders are over-pressurized, resulting in a fault. The purpose of synchronous monitoring is to send out an asynchronous alarm signal when the sluggish phenomenon is more serious, and stop the six-cylinder piston movement at the same time, so that the operator can make corresponding treatment in time.
(2) Synchronous monitoring ladder diagram
The ladder diagram is shown in the figure, which is a specific application of the above flowchart. It is worth mentioning that in the ladder diagram, 772, 773, and 774 are used as the result of compare. When the six-cylinder pistons are synchronized, the comparison result is equal to the constant 63 (BCD number), and the flag relay 773 is established. Otherwise, 772 and 774 are separated, and an out-of-sync alarm is triggered.
(3) Adjust the anti-misoperation program flowchart
See the following diagram for this part of the block diagram. It should be noted that this is only the procedure for manual adjustment of the pistons of the upper, front, right and lower cylinders. Some other adjustment actions belong to different groups and have similar principles. This anti-misoperation procedure can effectively prevent the operator from pressing a certain button and preventing other groups of buttons from being pressed by mistake and causing equipment failure.
(4) Ladder diagram to prevent misoperation
Conclusion
Practice has proved that the application of PLC in the transformation of six-sided top press is fruitful. The data processing function adopted enables the designed monitoring and anti-misoperation procedures to meet the expected requirements. PLC can be used in harsh working environments without having to consider the impact of voltage fluctuations, electromagnetic interference, ambient temperature and humidity on it too much. The entire control device can operate stably and reliably.
Previous article:Application of MP920 servo system in automobile flexible welding production line
Next article:Application of NA200 PLC in ultrafiltration water purifier
Recommended ReadingLatest update time:2024-11-17 13:56
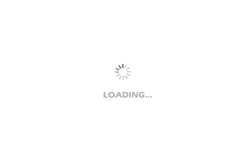
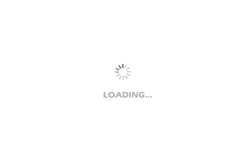
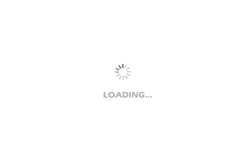
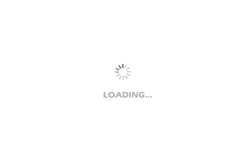
- Popular Resources
- Popular amplifiers
- Molex leverages SAP solutions to drive smart supply chain collaboration
- Pickering Launches New Future-Proof PXIe Single-Slot Controller for High-Performance Test and Measurement Applications
- CGD and Qorvo to jointly revolutionize motor control solutions
- Advanced gameplay, Harting takes your PCB board connection to a new level!
- Nidec Intelligent Motion is the first to launch an electric clutch ECU for two-wheeled vehicles
- Bosch and Tsinghua University renew cooperation agreement on artificial intelligence research to jointly promote the development of artificial intelligence in the industrial field
- GigaDevice unveils new MCU products, deeply unlocking industrial application scenarios with diversified products and solutions
- Advantech: Investing in Edge AI Innovation to Drive an Intelligent Future
- CGD and QORVO will revolutionize motor control solutions
- Innolux's intelligent steer-by-wire solution makes cars smarter and safer
- 8051 MCU - Parity Check
- How to efficiently balance the sensitivity of tactile sensing interfaces
- What should I do if the servo motor shakes? What causes the servo motor to shake quickly?
- 【Brushless Motor】Analysis of three-phase BLDC motor and sharing of two popular development boards
- Midea Industrial Technology's subsidiaries Clou Electronics and Hekang New Energy jointly appeared at the Munich Battery Energy Storage Exhibition and Solar Energy Exhibition
- Guoxin Sichen | Application of ferroelectric memory PB85RS2MC in power battery management, with a capacity of 2M
- Analysis of common faults of frequency converter
- In a head-on competition with Qualcomm, what kind of cockpit products has Intel come up with?
- Dalian Rongke's all-vanadium liquid flow battery energy storage equipment industrialization project has entered the sprint stage before production
- New breakthrough! Ultra-fast memory accelerates Intel Xeon 6-core processors
- New breakthrough! Ultra-fast memory accelerates Intel Xeon 6-core processors
- Consolidating vRAN sites onto a single server helps operators reduce total cost of ownership
- Consolidating vRAN sites onto a single server helps operators reduce total cost of ownership
- Allegro MicroSystems Introduces Advanced Magnetic and Inductive Position Sensing Solutions at Electronica 2024
- Car key in the left hand, liveness detection radar in the right hand, UWB is imperative for cars!
- After a decade of rapid development, domestic CIS has entered the market
- Aegis Dagger Battery + Thor EM-i Super Hybrid, Geely New Energy has thrown out two "king bombs"
- A brief discussion on functional safety - fault, error, and failure
- In the smart car 2.0 cycle, these core industry chains are facing major opportunities!
- Talk about the upper and lower tubes of the buck circuit_DC-DC BUCK bootstrap circuit
- Machine interface and boot design based on MCU+DSP embedded platform
- High voltage PWM three-terminal switching power supply
- Real-time solution to single chip microcomputer delay
- CB5654 Development Board Review 2
- [Raspberry Pi Pico Review] 3. My first project
- Problems with op amp sampling in oximeters
- EasyARM-RT1052 Review Summary
- If you have original works, I will give you rewards, up to 500 yuan in cash rewards
- Submit your idea, experience MPS products or evaluation boards for free, and win a backpack, Bluetooth wireless headset, and 10,000 yuan in cash!