1 Introduction
Automatic escalators are widely used in large shopping malls, supermarkets, airports, subways, hotels and other places. Most escalators work at rated operating conditions when there are large passenger flows, and still run at rated speeds when there are no passengers. They have the disadvantages of high energy consumption, severe mechanical wear, and short service life. The energy-saving control system that combines PLC with frequency conversion control has become the development direction of automatic escalator control technology.
The escalator with energy-saving effect has the following characteristics:
(1) When no one is riding the escalator, the escalator automatically and smoothly transitions to energy-saving operation and runs at 1/5 of the rated speed (the escalator can be automatically stopped when no one is riding the escalator);
(2) When someone takes the escalator, the escalator automatically and smoothly transitions to the rated speed;
(3) Since the speed is very low during energy-saving operation, the wear of the mechanical parts is greatly reduced, which relatively extends the service life of the escalator;
(4) The use of frequency conversion technology greatly reduces the impact on the power grid when the escalator starts.
At present, most energy-saving escalators have a single form and function, and can only realize simple fast-slow cycle or fast-stop cycle. The highlight of this system design is that the fast-slow cycle and the fast-slow stop cycle can be freely selected through the program. The system also integrates functions such as up and down step loss, anti-drive chain break, anti-reverse and fault protection output, and can monitor the escalator operation status through the status of the internal auxiliary relay of the program, which is very convenient for on-site debugging.
2. Automatic escalator variable frequency energy-saving control method
2.1 Frequency conversion non-self-start (fast and slow cycle)
2.1.1 Functional Description
By adding a frequency converter to control the speed of the escalator, when there are passengers on the escalator, the escalator runs at a high speed (such as the rated speed) to increase the passenger flow. When the passenger detection device does not detect any passengers passing through for a period of time, the escalator begins to decelerate and run at a low speed (such as 0.2m/s, the parameters can be set). At this time, it is always in standby operation, which is non-self-starting energy saving.
2.1.2 Operation Status Description
Frequency conversion control, low speed when no one is around, high speed when someone is around. The high speed operation time is recorded as TQ, which can be set through the PLC program. The specific time depends on the lifting height and speed of the elevator.
2.1.3 Operation steps
(1) When the escalator is powered on and stops waiting, and then starts running in a certain direction (such as upward), the escalator starts running at a low speed to save energy and enters the waiting state.
(2) The passenger detection device in the lower machine room detects whether someone passes by. When someone passes by, the high-speed operation time counter (recorded as TC) inside the controller is reset to zero, and the escalator begins to slowly accelerate to high-speed operation.
(3) The high-speed running time counter (referred to as TC) starts counting.
(4) When there is no one riding the escalator for a period of time, that is, TC ≥ TQ, the escalator starts to slow down and enter the low-speed standby state, and the operation is repeated in this cycle.
Figure 1 is a timing diagram of the fast and slow cycle control of an escalator.
Figure 1. Time sequence diagram of escalator fast and slow cycle control
2.1.4 Function Implementation
The passenger detection device installed at the entrance of the escalator detects whether there is anyone riding the escalator.
2.2 Frequency conversion self-start (fast and slow stop cycle)
2.2.1 Functional Description
By adding a frequency converter to control the speed of the escalator, when there are passengers on the escalator, the escalator runs at a high speed (such as rated speed) to increase passenger flow. When the passenger detection device does not detect any passengers passing by for a period of time, the escalator begins to decelerate and run at a low speed (such as 0.2m/s, the parameter can be set). When the passenger detection device does not detect any passengers taking the escalator for a period of time, the escalator begins to stop and wait, which is self-starting and energy saving.
2.2.2 Operation Status Description
Frequency conversion control, the elevator stops when no one is on the elevator for a long time, and runs at high speed when someone is on the elevator. The high-speed running time is recorded as TQ, and the low-speed running time is TS. The two parameters can be set through the PLC program. The specific time depends on the lifting height and speed of the elevator.
2.2.3 Operation steps
(1) When the escalator is powered on and stops waiting, and then starts running in a certain direction (such as upward), the escalator enters the upward stop waiting state.
(2) The photoelectric detection device in the lower machine room detects whether someone passes by. When someone passes by, the high-speed operation time counter (referred to as TC) inside the controller is reset to zero, and the escalator begins to slowly accelerate to high-speed operation.
(3) The high-speed running time counter (TC) starts timing.
(4) When there is no one riding the escalator for a period of time, that is, TC ≥ TQ, the escalator begins to decelerate and enters a low-speed operation state.
(5) The low-speed operation time counter (referred to as TSC) starts timing. When TSC < TS, if someone enters at this time, TC is reset and the timing starts again. The escalator accelerates to the high-speed operation state and then enters the high-speed operation state.
(6) When no one takes the escalator for a period of time, that is, TSC ≥ TS, the escalator stops running and enters a waiting state, and the operation repeats in this cycle.
Figure 2 is a timing diagram of the fast, slow, stop and cycle control of an escalator.
Figure 2. Time sequence diagram of escalator fast, slow, stop and cycle control
2.2.4 Function Implementation
The passenger detection device installed at the entrance of the escalator detects whether there are people riding the escalator. However, in order to ensure the safety of passengers, according to the requirements of GB16899-1997 "Safety Specifications for the Manufacture and Installation of Escalators and Moving Walkways": Self-starting escalators should start running before the user walks to the intersection line of the comb teeth, so the passenger detection device should meet the following requirements:
(1) Requirements that the detection device should meet
The light beam should be set at least 1.3m before the intersection of the comb teeth;
The outer edge of the contact pad should be set at least 1.8m before the intersection of the comb teeth, and the length of the contact pad along the running direction should be at least 0.85m. It should respond before the load applied to any point of 25mm2 on its surface reaches 150N.
(1) In actual design, you can choose
· Photoelectric diffuser installed at the entrance and exit of the handrail;
·Light beam installed at the entrance of the cover;
·It is realized by the self-starting device of the foot pad installed under the cover.
The photoelectric diffuse reflection device is selected when designing this system, which can ensure that every passenger coming from different directions can be effectively detected, thereby realizing the self-starting function.
3 System Design
3.1 Control system composition
Figure 3 Control system block diagram
As shown in Figure 3, the system is mainly composed of the following parts: power supply, PLC, frequency converter, etc. PLC is the core of the control system. PLC determines the output of high-speed operation command according to whether the input photoelectric signal is effective. Frequency converter controls the running speed of the escalator according to the high-speed running command of PLC, and completes the fast and slow and fast and slow stop cycle operation of the escalator.
3.2 Hardware Selection
Taking the escalator variable frequency non-self-start (fast and slow cycle) as an example, the escalator control system actually requires 11 input points and 7 output points. The PLC main controller uses Omron CPM1A-20CDR-A-V1 PLC. This type of PLC is equipped with the corresponding programming software CX-Programmer for programming and monitoring. Not only can the PLC be programmed through a handheld programmer, but it can also be programmed on a personal PC. During the operation of the escalator, the elevator operation status can be monitored through the status of the internal auxiliary relay of the program, and on-site debugging is very convenient.
The inverter adopts Inovance's MD320 inverter. The MD series inverter has complete input and output interfaces, and a full range of independent air ducts and radiators can be installed inside or outside the cabinet. It can provide solutions close to IP54 protection requirements, and its system design is especially suitable for constant torque loads.
4 System Design
4.1 Frequency conversion control main circuit
Figure 4 Frequency conversion control main circuit
Figure 4 shows that the main circuit is mainly composed of main circuit breaker ZK, phase sequence protection relay JXW, safety contactor JAQ, operation contactor JYX, main motor MT, etc.
4.2 PLC input and output port allocation
The input and output port allocation is shown in the attached table.
Appendix Input and Output Port Allocation Table
4.3 Operation Control Loop
Figure 5 shows the operation control loop.
Figure 5 Operation control loop
The operation control of the escalator is completed by PLC and frequency converter. The following takes frequency conversion non-self-start (fast and slow cycle) as an example to introduce the working principle of escalator energy-saving operation.
The inverter monitors the output signal of the PLC in real time to determine the next operation of the escalator. For example (1) Direction control of the escalator: When the terminal DI1 of the inverter receives the signal from the PLC, the output is forward and the escalator realizes upward operation; conversely, when the terminal DI2 is valid, the output is reverse and the escalator realizes downward operation. (2) Control of high-speed operation: The inverter has pre-set speed frequencies for multiple speed controls. When the escalator is running in energy-saving low-speed standby mode, only the running contactor (JYX) is energized. When the PLC detects the photoelectric signal, it outputs a high-speed operation command signal. At this time, the high-speed operation contactor (VN) is energized, and the inverter terminal DI3 is valid. The escalator immediately and smoothly accelerates to the set frequency and runs at high speed.
4.4 Typical control program design
The following focuses on the two subroutines in the program: operating mode and energy-saving time control.
4.4.1 Selection of frequency conversion non-self-start (fast and slow cycle) and self-start (fast and slow stop cycle) mode
The selection of methods is shown in Figure 6.
Figure 6 Fast-slow cycle and fast-slow stop cycle subroutines
Simply modify the combination of SET and RSET in the program to switch between two different operating modes.
Fast and slow cycle, set to SET 212.00 and RSET 212.01.
Fast and slow stop cycles are set to SET 212.00 and SET 212.01.
4.4.2 Control of energy-saving time
Figure 7 Energy saving time subroutine
The express operation holding time can be set by the above-mentioned counter, so as to meet the use of escalators with different lifting heights and speeds (see Figure 7).
4.5 Test data
In order to verify the energy-saving effect of this system, we selected a site for testing. The power of the on-site traction motor is 7.5kW, and the power consumption of the escalator with variable frequency energy-saving control and ordinary Y-△ control is compared. The escalator is tested for 4 hours each when it is used by passengers and when it is running without load. In actual testing, the energy-saving escalator consumes 25.3kWh when running at full load, while the ordinary Y-△ control escalator consumes 26kWh; when running without load, it consumes 1.8kWh, while the ordinary Y-△ control escalator consumes 8.4kWh. From this example, it can be seen that the escalator with variable frequency energy-saving control saves 22% energy than the ordinary Y-△ control escalator.
If the escalator is stopped when no one is on it, it can save about 30% of energy compared with before the transformation. In actual use, the longer the escalator slows down or stops, the more obvious the energy saving effect.
5 Conclusion
This design has been widely used in energy-saving renovation of escalators, and more than 300 units have been installed in major cities such as Wuhan and Shanghai. Practice has proved that the escalator energy-saving system based on PLC and inverter control is reliable and stable, and it effectively saves users' usage costs.
Previous article:Connect any industrial network to PLC using the NI platform
Next article:Control design of universal milling machine based on touch screen and PLC
Recommended ReadingLatest update time:2024-11-16 21:54
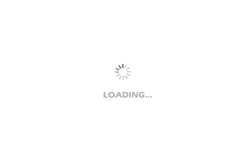
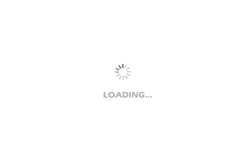
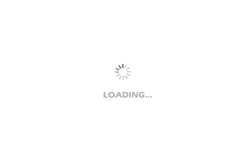
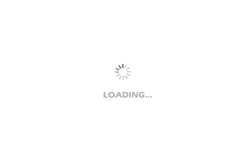
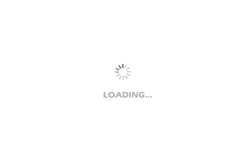
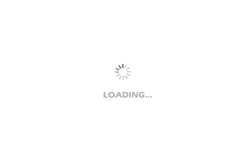
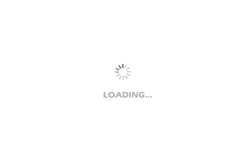
- Popular Resources
- Popular amplifiers
- Molex leverages SAP solutions to drive smart supply chain collaboration
- Pickering Launches New Future-Proof PXIe Single-Slot Controller for High-Performance Test and Measurement Applications
- CGD and Qorvo to jointly revolutionize motor control solutions
- Advanced gameplay, Harting takes your PCB board connection to a new level!
- Nidec Intelligent Motion is the first to launch an electric clutch ECU for two-wheeled vehicles
- Bosch and Tsinghua University renew cooperation agreement on artificial intelligence research to jointly promote the development of artificial intelligence in the industrial field
- GigaDevice unveils new MCU products, deeply unlocking industrial application scenarios with diversified products and solutions
- Advantech: Investing in Edge AI Innovation to Drive an Intelligent Future
- CGD and QORVO will revolutionize motor control solutions
- Innolux's intelligent steer-by-wire solution makes cars smarter and safer
- 8051 MCU - Parity Check
- How to efficiently balance the sensitivity of tactile sensing interfaces
- What should I do if the servo motor shakes? What causes the servo motor to shake quickly?
- 【Brushless Motor】Analysis of three-phase BLDC motor and sharing of two popular development boards
- Midea Industrial Technology's subsidiaries Clou Electronics and Hekang New Energy jointly appeared at the Munich Battery Energy Storage Exhibition and Solar Energy Exhibition
- Guoxin Sichen | Application of ferroelectric memory PB85RS2MC in power battery management, with a capacity of 2M
- Analysis of common faults of frequency converter
- In a head-on competition with Qualcomm, what kind of cockpit products has Intel come up with?
- Dalian Rongke's all-vanadium liquid flow battery energy storage equipment industrialization project has entered the sprint stage before production
- Allegro MicroSystems Introduces Advanced Magnetic and Inductive Position Sensing Solutions at Electronica 2024
- Car key in the left hand, liveness detection radar in the right hand, UWB is imperative for cars!
- After a decade of rapid development, domestic CIS has entered the market
- Aegis Dagger Battery + Thor EM-i Super Hybrid, Geely New Energy has thrown out two "king bombs"
- A brief discussion on functional safety - fault, error, and failure
- In the smart car 2.0 cycle, these core industry chains are facing major opportunities!
- The United States and Japan are developing new batteries. CATL faces challenges? How should China's new energy battery industry respond?
- Murata launches high-precision 6-axis inertial sensor for automobiles
- Ford patents pre-charge alarm to help save costs and respond to emergencies
- New real-time microcontroller system from Texas Instruments enables smarter processing in automotive and industrial applications
- Problems with using transistors as followers
- Did EE change its logo?
- What is the difference between single-ended audio and differential audio? One is mono and the other is stereo?
- Comprehensive explanation of infrared remote control codec
- e8 emulator connection keeps disconnecting
- 【Qinheng Trial】ch554 lights up lcd1602
- How is 5G charged?
- 【NXP Rapid IoT Review】+ 5. Comprehensive application of sensors
- WiFi 6 and "CHIP" will strongly promote the popularization of the Internet of Things. What do you think?
- OMRON H3Y-2 0-10s TIMER