1 Introduction
Programmable
Controller
(
PLC
) is a new type of industrial automatic control device developed based on microprocessor, integrating
modern technologies such as
computer
technology, automatic control technology and
communication
technology. It has powerful functions such as logic control, timing, counting, data processing, networking and communication. At the same time, due to the high reliability and great application flexibility of PLC, it has become inevitable to use it to replace the traditional relay contact control system. A large number of equipment using traditional relay-contact control systems have been transformed and updated to become PLC-controlled
automation
systems, and have the characteristics of low transformation cost, short cycle and high reliability. This article introduces the design and application of PLC control system for double-sided single-station hydraulic transmission modular machine tools.
2 Movement and control requirements of modular machine tools
Combined machine tools refer to machine tools that can perform multiple or multiple processing at the same time. The processing actions of modular machine tools are often arranged according to predetermined steps, similar to simple program control, which is exactly what PLC is best at.
The double-sided single-station hydraulic transmission combined machine tool uses three motors for driving. M1 and M2 are the left and right power head motors, and M3 is the cooling pump motor. The corresponding control AC contactors are km1, km2, and km3 respectively. SA1 is the left power head separate adjustment
switch
, and SA2 is the right power head separate adjustment switch. Through them, the left and right power heads can be adjusted separately. SA3 is the cooling pump motor working selection switch. The working cycle of the left and right power heads of the machine tool is shown in Figure 1, and the electromagnet action sequence table is shown in Table 1.
Figure 1 Working cycle diagram of the power head
As shown in Figure 1 and Table 1, when the combined machine tool is in the automatic cycle state, after pressing the start button, the left and right power head motors m1 and m2 rotate at the same time, and the "fast forward" button is pressed, the solenoid valves yv1 and yv3 are energized, the left and right power heads feed quickly and leave the original position, and the travel switches sq1, sq2, sq5, and sq6 are reset first, and the travel sq3 and sq4 are reset later. When sq3 and sq4 are reset, during the power head feeding process, the fast forward is automatically changed to the working forward by the respective travel valves, and the travel switch sq is pressed at the same time, and the cooling pump motor m3 works to supply coolant. When the left power head is processed, sq7 will be pressed down and pressed against the dead stop iron, and the oil pressure in its oil circuit will increase to make kp1 act. When the right power head is processed, sq8 will be pressed down to make kp2 act, yv2 and yv4 will be energized, and yv1 and yv3 will also lose power, and the left and right power heads will fast retreat. When the left power head resets sq, the cooling pump motor will stop. When the left and right power heads are quickly retreated to their original positions, first press sq3 and sq4, then press sq1, sq2, sq5, and sq6 to cut off the power head motors m1 and m2, and at the same time, yv2 and yv4 are cut off, the power head stops, and the machine tool cycle ends. During the processing, the left and right power heads can be quickly retreated to their original positions at any time.
3 Hardware Design of PLC Control System
The control system of the double-sided single-station hydraulic transmission combination machine tool should first meet the basic requirements of the above-mentioned working cycle, and then select the programmable controller according to the number of travel switches required for the working cycle and control, plus the number of working points required for the buttons, pressure
relays
, and thermal relay contacts. The PLC input and output wiring diagram is shown in Figure 2.
Figure 2 PLC input/output wiring diagram for double-sided single-station combination machine tool
The PLC has 21 input signals (4 buttons, 9 travel switches, 3 thermal relay break contacts, 2 pressure relay contacts, and 3 conversion switches), which requires 21 input points. In practical applications, in order to save the number of PLC points, the input signal wiring can be appropriately changed. For example, SQ8 and KP2 are connected in series as an input signal of the PLC, which can reduce one input point. At this time, the number of PLC input points is reduced from 21 points to 13 points, which can reduce the cost of the equipment. However, since some contacts are input in series or parallel, the reliability of the input device and the reliability of the entire control system may be reduced.
The output control object of the programmable controller is mainly the actuator in the control circuit, such as contactors, solenoid valves, etc. The actuators in the double-sided single-station hydraulic transmission combination machine tool include AC contactors KM1, KM2, KM3, solenoid valves YV1, YV2, YV3, and YV4, which require 7 output points. According to their working voltage, the output port wiring diagram of the PLC can be designed. Since the types and levels of the voltages applied to the contactor and the solenoid valve coil are different, two sets of output channels of the PLC must be occupied, and a relay output type PLC must be selected. Through a comprehensive analysis of the input and output circuits of the machine tool PLC control system, the Japanese Mitsubishi FX2N?32MR programmable controller is selected to implement the control of the machine tool, which can basically meet the above overall requirements.
4 Programming of PLC Control System
The PLC control program is completed by ladder diagram programming. According to the control requirements, the PLC control ladder diagram of the double-sided single-station hydraulic transmission modular machine tool cycle operation is designed as shown in Figure 3. In the figure, when the modular machine tool is in the automatic cycle position, x013 and x014 are connected, the start button sb2 is pressed, y000 and y001 are connected, the km1 and km2 coils are energized and self-locked, and the left and right power head motors start to rotate. Press the button sb3, y004 and y006 are connected, yv1 and yv3 are energized, and the left and right power heads are quickly fed and leave the original position. During the power head feeding process, the fast feed is automatically changed to the working feed by the respective stroke valves. At the same time, sq is pressed, y002 is connected, the km3 coil is energized, and the cooling pump motor m3 starts. When the left power head is finished, press sq7 and press against the dead stop iron. The oil pressure rises to make kp1 act and y005 connect. When the right power head is finished, press sq8 and make kp2 act, y007 connects, yv2 and yv4 will be energized, and yv1 and yv3 will lose power at the same time, and the left and right power heads will retreat quickly. When the left power head resets sq, y002 will lose power, km3 will lose power, and the cooling pump motor will stop. When the left and right power heads retreat quickly to the original position, press each travel switch to make y000 and y001 lose power, km1 and km2 coils lose power, and m1 and m2 stop. At the same time, yv2 and yv4 lose power, the power head stops, and the machine tool cycle ends. If sb4 is pressed and x003 is connected, the left and right power heads can be retreated quickly to the original position and stopped at any time. In addition, the machine tool is also designed with overload and short circuit protection.
Figure 3 PLC control ladder diagram of modular machine tool
5 Conclusion
Applying PLC technology to double-sided single-station hydraulic transmission modular machine tools can give full play to the advantages of PLC such as high reliability, convenient debugging and flexible use. It can greatly shorten the product development cycle, reduce design costs, improve success
rate
and product reliability, and increase production efficiency.
Previous article:Design and implementation of intelligent lighting control system based on photoelectric sensor
Next article:Design of accelerated life test system for electromagnetic relay
Recommended ReadingLatest update time:2024-11-16 17:48
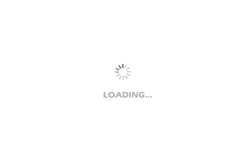
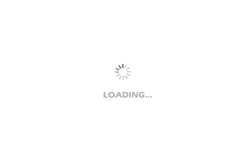
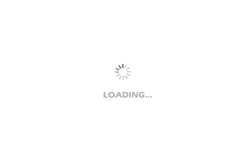
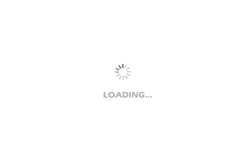
- Popular Resources
- Popular amplifiers
- MathWorks and NXP Collaborate to Launch Model-Based Design Toolbox for Battery Management Systems
- STMicroelectronics' advanced galvanically isolated gate driver STGAP3S provides flexible protection for IGBTs and SiC MOSFETs
- New diaphragm-free solid-state lithium battery technology is launched: the distance between the positive and negative electrodes is less than 0.000001 meters
- [“Source” Observe the Autumn Series] Application and testing of the next generation of semiconductor gallium oxide device photodetectors
- 采用自主设计封装,绝缘电阻显著提高!ROHM开发出更高电压xEV系统的SiC肖特基势垒二极管
- Will GaN replace SiC? PI's disruptive 1700V InnoMux2 is here to demonstrate
- From Isolation to the Third and a Half Generation: Understanding Naxinwei's Gate Driver IC in One Article
- The appeal of 48 V technology: importance, benefits and key factors in system-level applications
- Important breakthrough in recycling of used lithium-ion batteries
- Innolux's intelligent steer-by-wire solution makes cars smarter and safer
- 8051 MCU - Parity Check
- How to efficiently balance the sensitivity of tactile sensing interfaces
- What should I do if the servo motor shakes? What causes the servo motor to shake quickly?
- 【Brushless Motor】Analysis of three-phase BLDC motor and sharing of two popular development boards
- Midea Industrial Technology's subsidiaries Clou Electronics and Hekang New Energy jointly appeared at the Munich Battery Energy Storage Exhibition and Solar Energy Exhibition
- Guoxin Sichen | Application of ferroelectric memory PB85RS2MC in power battery management, with a capacity of 2M
- Analysis of common faults of frequency converter
- In a head-on competition with Qualcomm, what kind of cockpit products has Intel come up with?
- Dalian Rongke's all-vanadium liquid flow battery energy storage equipment industrialization project has entered the sprint stage before production
- Allegro MicroSystems Introduces Advanced Magnetic and Inductive Position Sensing Solutions at Electronica 2024
- Car key in the left hand, liveness detection radar in the right hand, UWB is imperative for cars!
- After a decade of rapid development, domestic CIS has entered the market
- Aegis Dagger Battery + Thor EM-i Super Hybrid, Geely New Energy has thrown out two "king bombs"
- A brief discussion on functional safety - fault, error, and failure
- In the smart car 2.0 cycle, these core industry chains are facing major opportunities!
- The United States and Japan are developing new batteries. CATL faces challenges? How should China's new energy battery industry respond?
- Murata launches high-precision 6-axis inertial sensor for automobiles
- Ford patents pre-charge alarm to help save costs and respond to emergencies
- New real-time microcontroller system from Texas Instruments enables smarter processing in automotive and industrial applications
- Qorvo CEO Bob Bruggeworth Elected Chairman of the Semiconductor Industry Association
- Introduction to RF Gain Blocks for Radio Range and Reliability
- How to choose pliers, terminals, wires, and heat shrink tubing for DuPont cables?
- Talk about the "obstacles" on the road to power supply upgrade
- How to do switch detection in TWS headset design
- FAQ|Littelfuse Live: How to improve the safety and reliability of smart building electronic equipment in the era of the Internet of Things
- Simple use of window function in Matlab
- I want a vhdl written eeprom read and write function, power failure data will not be lost
- How to measure the output ripple of a single-phase inverter with an oscilloscope
- No color difference splicing screen