1 Sensor Network Architecture
The architecture of a typical sensor network includes distributed sensor nodes, gateway nodes, the Internet, and user interfaces. In a sensor network, nodes are arranged in the monitored area. Each sensor network is equipped with a gateway connected to a transmission network. The gateway transmits the measured data from the sensor area to a base station that provides remote connection and data processing through the transmission network, and the base station is connected to a remote database through the Internet. Finally, the collected data is analyzed and mined and provided to the end user through an interface.
The main structure of this system is that each CC2430 module is connected to multiple DS18820 temperature sensors. The temperature sensors are arranged in the grain warehouse according to a certain pattern and connected to the current CC2430 module through a single bus. These CC2430 modules are networked using wireless sensor network technology, and the data is sent to the local warehouse data concentrator, and the data concentrator is connected to the local monitoring host through a bridge, as shown in Figure 1. Finally, the remote terminal user is connected to the local monitoring system through the Internet to realize remote networked grain warehouse quantity monitoring, as shown in Figure 2.
2 Sensor layout model
The schematic diagram of the monitoring point layout of the flat warehouse grain pile temperature data information collection system is shown in Figure 3. The temperature sensors in the warehouse are set to arrange 3 groups of temperature sensors on each side of the east, south, west and north walls, with a spacing of 1 m between each group; the spacing from the wall to the inside on the east, south, west and north sides is 0.25 m, 0.25 m, 0.5 m, 1.0 m, 1.0 m, etc.
The elevation diagram of the monitoring points of the flat warehouse grain pile temperature data information collection system is shown in Figure 4. The grain pile temperature monitoring points are arranged from the grain surface downward and from the warehouse bottom upward. According to the 6m grain loading height, 8 temperature sensors are set for each single bus cable. The sensor spacing from the grain surface downward and from the warehouse bottom upward is 0.30 m, 0.70 m, 1.0 m, and 1.0 m. The data information of the three grain pile temperature monitoring points on the east, south, west, and north sides of the warehouse in the same plane is sorted by averaging to improve the reliability and accuracy of the monitoring data information.
3 DS18B20 single bus temperature sensor
The DS18820 digital thermometer provides 9-bit (binary) temperature readings, indicating that the device's temperature information is sent to or from the DS18820 via a single-wire interface, so only one wire (and ground wire) is required from the host CPU to the DS18820. The power supply for the DS18820 can be provided by the data line itself, without the need for an external power supply. Because each DS18820 has been given a unique serial number when it leaves the factory, any number of DS18820s can be stored on the same single-wire bus, which allows temperature-sensitive devices to be placed in many different places. The measurement range of the DS18820 is from -55°C to +125°C, with an increment of 0.5°C, and the temperature can be converted into digital within 1 s (typical value). The interface circuit of the DS18820 and CC2430 is shown in Figure 5.
The temperature reading process of multiple DS18820s is as follows: reset → send 55HMATCHROM command → send 64-bit address → send 44H start conversion command → delay → reset → send 55HMATCHROM command → send 64-bit address → send 0BE read memory command → continuously read 2 bytes of data (i.e. temperature) → reset → read the temperature of the next device.
4 CC2430 module
4.1 Main features of CC2430 chip
The CC2430 chip uses the architecture of the previous CC2420 chip, integrating the ZigBee radio frequency (RF) front end, memory and microcontroller on a single chip. It uses an 8-bit MCU (8051), has 128 KB of programmable flash memory and 8 KB of RAM, and also includes an analog-to-digital converter (ADC), several timers, AES128 coprocessor, watchdog timer, sleep mode timer with 32 kHz crystal oscillator, power on reset circuit, brown out detection circuit, and 21 programmable I/O pins. The CC2430 chip is produced using 0.18 μm CMOS technology; in receive and transmit modes, the current consumption is less than 27 mA or 25 mA respectively. The CC2430's sleep mode and ultra-short time to switch to active mode are particularly suitable for applications that require very long battery life.
The main features of the CC2430 chip are as follows: high-performance and low-power 8051 microcontroller core; integrated 2.4GHz RF radio transceiver that complies with the IEEE 802.15.4 standard; excellent wireless receiving sensitivity and strong anti-interference; only 0.9μA current consumption in sleep mode, and an external interrupt or RTC can wake up the system; less than 0.6μA current consumption in standby mode, and an external interrupt can wake up the system; hardware support for CSMA/CA function; a wide voltage range (2.0~3.6 V); digital RSSI/LQI support and powerful DMA function; with battery monitoring and temperature sensing functions; integrated 14-bit analog-to-digital conversion ADC; integrated AES security coprocessor; with 2 powerful USARTs that support several groups of protocols, as well as 1 MAC timer that complies with the IEEE802.15.4 specification, 1 conventional 16-bit timer and 2 8-bit timers; powerful and flexible development tools.
4.2 CC2430 module design
The CC2430 chip requires very few peripheral components to realize the signal transmission and reception functions. The circuit uses an unbalanced antenna, and connecting an unbalanced transformer can make the antenna performance better. The unbalanced transformer in the circuit is composed of capacitor C112 and inductors L102, L100, L101 and a PCB microwave transmission line. The entire structure meets the requirements of RF input/output matching resistance (50 Ω). The internal T/R switching circuit completes the switching between LNA and PA. A 32 MHz crystal oscillator circuit is formed by a 32 MHz quartz resonator (X100) and two capacitors (C108 and C109). A 32.768 kHz crystal oscillator circuit is formed by a 32.768 kHz quartz resonator (Y100) and two capacitors (C110 and C111). The voltage regulator supplies power to all pins and internal power supplies that require 1.8 V. Capacitors C115, C100, C101, C104, C102, C113, C103, C107, C106, and C105 are decoupling capacitors used for power supply filtering to improve the stability of chip operation. R101 and R102 provide precise bias resistance for the current, as shown in Figure 6.
5 Software Design
5.1 Host computer software design
In this system, the upper management software adopts a three-layer C/S mode to process the data sent by the sensor network in real time to form the data representation that users ultimately care about. After authorization, terminal users in the local area network can read the real-time data on the monitoring host to achieve remote monitoring. The monitoring application software also tracks and manages each node in the sensor network. For abnormal situations monitored, the upper management software uses sound, light, text messages, and telephone real-time alarm methods. It can display parameter lists, real-time curves (corresponding to specific values and adjusting coordinates at will), real-time data, converted data, cumulative data, history, alarm screens, reports, and other displays. The statistical function can be specifically designed according to user needs.
5.2 Lower computer software design
In the network, each node has a fixed address. The sensor node connected to the monitoring host is a special node, which uses a serial interface to communicate with the monitoring host. The data transmission adopts the master-slave mode. The node connected to the monitoring host is the master station, which controls the communication timing within the network; other nodes are slave stations and can be addressed by the master station. The master node mainly completes the collection of data from each slave node and performs preprocessing; the slave node mainly completes the collection of raw data from various sensors, as shown in Figure 7.
6 Conclusion
The wireless temperature sensor network is based on the low-cost, low-power wireless single-chip CC2430, and uses the DS18820 temperature sensor to obtain data. It has the characteristics of simple circuit structure, stable and reliable operation, high detection accuracy, and flexible and convenient wireless data communication. It is particularly suitable for industrial field environments, monitoring closed spaces, and other special occasions that require multi-point monitoring. The application of this network has greatly improved the management level of central grain reserves, reduced management costs, and improved the safety of grain depots.
Previous article:Design of fuzzy control system for temperature and humidity in environmental laboratory
Next article:Remote temperature and humidity measurement and control system for flue-cured tobacco room based on Labview
Recommended ReadingLatest update time:2024-11-16 18:02
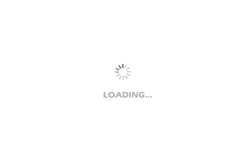
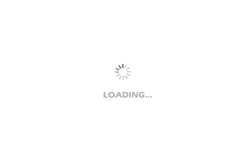
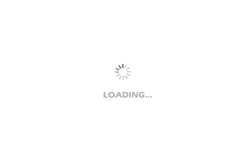
- Popular Resources
- Popular amplifiers
-
MCU C language programming and Proteus simulation technology (Xu Aijun)
-
100 Examples of Microcontroller C Language Applications (with CD-ROM, 3rd Edition) (Wang Huiliang, Wang Dongfeng, Dong Guanqiang)
-
Single-chip microcomputer technology and application - electronic circuit design, simulation and production (edited by Zhou Runjing)
-
Principles and Applications of Single Chip Microcomputers and C51 Programming (3rd Edition) (Xie Weicheng, Yang Jiaguo)
- Molex leverages SAP solutions to drive smart supply chain collaboration
- Pickering Launches New Future-Proof PXIe Single-Slot Controller for High-Performance Test and Measurement Applications
- CGD and Qorvo to jointly revolutionize motor control solutions
- Advanced gameplay, Harting takes your PCB board connection to a new level!
- Nidec Intelligent Motion is the first to launch an electric clutch ECU for two-wheeled vehicles
- Bosch and Tsinghua University renew cooperation agreement on artificial intelligence research to jointly promote the development of artificial intelligence in the industrial field
- GigaDevice unveils new MCU products, deeply unlocking industrial application scenarios with diversified products and solutions
- Advantech: Investing in Edge AI Innovation to Drive an Intelligent Future
- CGD and QORVO will revolutionize motor control solutions
- Innolux's intelligent steer-by-wire solution makes cars smarter and safer
- 8051 MCU - Parity Check
- How to efficiently balance the sensitivity of tactile sensing interfaces
- What should I do if the servo motor shakes? What causes the servo motor to shake quickly?
- 【Brushless Motor】Analysis of three-phase BLDC motor and sharing of two popular development boards
- Midea Industrial Technology's subsidiaries Clou Electronics and Hekang New Energy jointly appeared at the Munich Battery Energy Storage Exhibition and Solar Energy Exhibition
- Guoxin Sichen | Application of ferroelectric memory PB85RS2MC in power battery management, with a capacity of 2M
- Analysis of common faults of frequency converter
- In a head-on competition with Qualcomm, what kind of cockpit products has Intel come up with?
- Dalian Rongke's all-vanadium liquid flow battery energy storage equipment industrialization project has entered the sprint stage before production
- Allegro MicroSystems Introduces Advanced Magnetic and Inductive Position Sensing Solutions at Electronica 2024
- Car key in the left hand, liveness detection radar in the right hand, UWB is imperative for cars!
- After a decade of rapid development, domestic CIS has entered the market
- Aegis Dagger Battery + Thor EM-i Super Hybrid, Geely New Energy has thrown out two "king bombs"
- A brief discussion on functional safety - fault, error, and failure
- In the smart car 2.0 cycle, these core industry chains are facing major opportunities!
- The United States and Japan are developing new batteries. CATL faces challenges? How should China's new energy battery industry respond?
- Murata launches high-precision 6-axis inertial sensor for automobiles
- Ford patents pre-charge alarm to help save costs and respond to emergencies
- New real-time microcontroller system from Texas Instruments enables smarter processing in automotive and industrial applications
- Basic knowledge of interrupts and interrupt directions of MCU core
- What exactly is “Passive Internet of Things”?
- Know some DSP memory management
- [Analysis of the topic of the college electronic competition] - 2016 Jiangsu Province TI Cup F "Bit Synchronous Clock Extraction Circuit"
- Problems found when connecting stm32f103vet6 to ferroelectric FM28V020
- Compiled PLATFORM
- Looking to buy a Milink MIZ702N development board
- can communication
- CC2541 serial port printing information problem
- Share a picture of domestic alternative power IC