Groundwater is an important component of water resources and a major part of strategic resources. It plays a very important role in ensuring the lives of urban and rural residents, supporting economic and social development, and maintaining ecological balance [1]. Groundwater level observation is a basic water conservancy work and plays an important role in groundwater research and engineering construction [2]. The dynamic change information of groundwater level provides an important reference for groundwater exploitation, local ecological maintenance, and engineering construction. In view of the fact that the groundwater level meets the needs of real-time collection and real-time monitoring, this paper presents a remote monitoring system design for groundwater dynamic water level monitoring.
1 System Design
1.1 System Design Requirements
The function of the collector is to collect the water level or water depth information in the deep well and send the data to the host computer system through wireless communication. In order to save human resources, the collector needs to run for a long time without maintenance. The collection system requires easy installation and maintenance, no wiring, etc., which requires minimizing the construction links, improving work efficiency and reducing costs. Therefore, the following design requirements are proposed:
(1) Reliable communication;
(2) Low power consumption, battery powered;
(3) Low installation cost;
(4) Easy to maintain.
1.2 Current situation analysis
The acquisition modules currently available on the market have high static power consumption, generally ranging from 200 mW to 600 mW. The lower computer is large in size and requires external batteries and solar panels, which are prone to theft and vandalism. The installation is complex and the installation cost is high when used in areas without power supply. It is not suitable for special occasions with harsh conditions. The integrated wireless RTU is also large in size and cannot be advanced for secondary development into special products. The inability to provide low-voltage power supply also limits its application in this system.
1.3 System Solution
GSM network communication has the advantages of high speed, reliability, wide coverage, etc., and it is easy to realize remote data communication. SMS is a short message service provided by mobile operators, which is based on GSM network communication. SMS supports point-to-point and point-to-multipoint message transmission of GSM devices, and can transmit a text message and a text message of 140 B. In the case that the target device is not online or fails, the short message will be temporarily stored in the operator's server. This method can achieve a higher degree of reliability. The host system can be a personal mobile device or a dedicated monitoring device that supports SMS.
GPRS is a high-speed data service based on the GSM network with low charges, but data packet loss and disconnection often occur when the network is busy. Since groundwater changes relatively slowly, the real-time requirements of the system are not high, so the use of SMS for wireless data communication is sufficient to meet the requirements, and the charges for this system are also low.
In order to facilitate the replacement and maintenance of the collector, a universal No. 5 alkaline battery is used for power supply. The hardware adopts the selective separation of power supply for each functional module, and the software adopts the method of timed collection and timed upload to greatly reduce power consumption and determine the feasibility of long-term battery power supply, thereby eliminating the process and cost of wiring and installing solar cells. The collector is integrated with the GSM communication module, which reduces the size and can be built into the wellhead to be tested for easy installation and later maintenance.
2 Hardware Design
2.1 Hardware Structure
The data collector (lower computer) consists of a microprocessor, battery pack, power management, GPRS module, pressure sensor, clock calendar, signal conditioning and A/D converter, as shown in Figure 1.
2.2 Module Design
(1) Main controller: The ATmega88V microcontroller is used as the microcontroller of the data collector. It has built-in 1 KB SRAM and 512 B EEPROM memory, eliminating the need for external memory and a wide operating voltage range of 1.8 V to 5.5 V. In order to save power, the microcontroller operates at a system clock frequency of 32.768 kHz.
(2) Clock and calendar module: The MAX690 chip is used as the clock and calendar module. It is powered by an independent 3 V button battery and communicates with the CPU in real time. The CPU queries the time to determine the working status of the collector.
(3) Pressure sensor: A domestically produced KY type pressure sensor with an integrated voltage transmitter is used. The operating voltage is 10.5 V to 15 V, the output signal is 1 V to 5 V, and the range is 0 m to 100 m.
(4) A/D converter: AD7921, a 12-bit A/D converter with SPI serial interface is used. The voltage reference chip AD780 provides 2.5 V supply voltage and reference voltage.
(5) Signal conditioning: The general dual op amp LM2904 is used to condition the sensor output signal and the battery voltage signal and send them to the A/D converter. The power supply voltage of LM2904 is provided by LT1613 (12 V), and the 1 V to 5 V signal of the pressure transmitter is conditioned. First, the front stage is a follower, and the output of the op amp is divided by a potentiometer to obtain a 0.5 V to 2.5 V signal. The second signal is the battery voltage signal. Similarly, the possible maximum value of the battery group voltage VCC (7 V) is adjusted to be less than the full-scale voltage of the A/D conversion (2.5 V). The two signals are sent to the A/D converter for digital quantization.
(6) Power management: Four No. 5 batteries are connected in series, and two of them are used to power the microcontroller. IRFU220 and IRFU9530 form two push-pull outputs, and the GPIO of the microcontroller selectively powers the measurement part (including pressure sensor, A/D converter, signal conditioning circuit) and GSM module. After the push-pull output, an LT1086 is used to provide 3.6 V power for the GSM module after voltage regulation, and the LT1613 boost circuit chip provides 12 V power for the sensor/transmitter and analog signal conditioning circuit.
(7) GSM module: The GR64 module from Wavecom is used. The interface with the microcontroller is an asynchronous serial interface. During programming, AT commands are used to set up the module, conduct conversations, package data, and send information.
2.3 Measurement error analysis
3 Software Design
3.1 Brief description of the working process
After the device is turned on, the MCU will execute the initialization program of each functional module, then read the current date and time from the clock calendar chip, and then determine whether this moment exceeds the set measurement moment. If it exceeds the measurement moment, it will enter the measurement state. At this time, the MCU will turn on the power supply to the measurement circuit, and after a delay waiting for the sensor to stabilize, it will continuously collect 100 data and store them in RAM. After the collection, the power supply of the measurement circuit will be turned off, and the final retained data will be obtained through the median filtering method, and then the data will be saved in the EEPROM on the MCU chip. When the program determines that the current time exceeds the upload moment, it will turn on the GSM module, wait for the GSM module to access the network, first receive the power supply, and then package the data to be sent according to the AT command, and send it to the destination device in the form of a text message. If the data transmission timeout, the MCU will store the stranded data packet in the EEPROM inside the MCU and wait for the next upload. Finally, turn off the GSM module and return to the query state of the cycle time.
The frequency of data collection is twice a day. When the measurement time comes, the CPU enables the boost circuit to power the pressure sensor and signal conditioning circuit, starts the A/D converter, collects the pressure sensor data and battery voltage data, turns off the power supply circuit, processes the data, and saves the measurement results in the EEPROM inside the microcontroller. The data upload time can be modified by command. In order to save power consumption on the data bus, the time reading is not real-time, and the timer interrupt service program is used to read it once per minute. The uploaded data is always the data measured the previous day.
During the entire process of program running, the watchdog counter inside the microcontroller is always enabled to monitor the normal operation of the collector. If the system freezes or the program execution is chaotic, the watchdog timer will reset the microcontroller.
3.2 Program Flowchart
The program flow chart is shown in Figure 2
3.3 Protocol Design
The AT command set is a universal interface command for mobile platforms and device terminals issued by ETSI (European Telecommunications Standards Institute), which includes the control of SMS [7]. The data transmitted by the collector to the host system includes function code, date and time, and collected data. Each byte of data is in ASCII code. The protocol consists of two parts:
(1) The format of the message uploaded by the data collector (excluding AT commands) is: DT (data description)_upload time_measurement date_time 1_water depth (unit: m)_time 2_water depth (unit: m)#(end). The text form of a data example is as follows:
T_2008/11/09/16:00_2008/11/08_02:00_23.40_14:00_23.10_16:00#. The data is uploaded at 16:00 on November 9, 2008. On November 8, 2008, the water depth was 23.40m at 2:00 and 23.10m at 14:00.
(2) The format of the command message sent by the host system to the collector (excluding AT commands): ST (setting instructions)_Set date and time_Time 1_Water depth (unit: m)_Time 2_Water depth (unit: m)_Upload time#(end), expressed in text form as:
ST_2008/11/08/09:00_05:00_20:00_14:00#. The content of this data is that the time is set to 9:00 on November 8, 2008, the two collection times are set to 5:00 and 20:00, and the upload time is set to 14:00.
After sending this SMS, the destination address of the collector's next SMS will be automatically adjusted to this address.
4 Actual Test
4.1 Data Transmission
In the data transmission test, the program was adjusted to upload data every half an hour, and the information set for the collector was randomly sent in the middle. The set upload time was ignored. Table 1 lists part of the 450 short messages received.
In the table, data No. 346 and No. 347 indicate that at 2008/11/09/14:00, the GSM module had a network access timeout and the information was not sent successfully. At 14:30, the data that had failed to be sent was successfully resent.
During the 450 data transmission tests, the network access timeout rate was 0.67% and the data loss rate was 0. After 50 settings, the setting failure rate was 8%, but after the timeout was extended and the test was performed 100 times, the setting failure rate dropped to 2%.
4.2 Energy consumption test
(1) Static waiting: The microcontroller consumes less than 20 μA when operating at a 32.768 kHz clock. The measurement circuit and GPRS module are powered off. When the power push-pull output is low, the leakage current of the MOS tube is less than 10 μA. The clock calendar chip can basically work continuously for more than 8 years with independent power supply and will not be included in the power consumption analysis. The total energy consumption for one day is 720 μAh when running 24 hours a day.
(2) Measurement: The LT1613 consumes 1 mA of its own operating current, the sensor consumes 10 mA (12 V) when operating, and the measured current drawn from the battery pack is 25 mA when powered by 5 V. The voltage reference consumes 1 mA, and the A/D converter consumes 3 mA when operating. The entire measurement process takes less than 300 ms, and each measurement consumes a total of 2.4 μAh of power.
(3) Data upload: The current of the GSM module is 500 mA when sending data, 20 mA when receiving data, and 2.5 mA when static. During the independent test of the GSM module, a data upload process takes less than 20 s and consumes approximately 200 μAh of power.
In summary, the process of measuring twice a day and uploading once consumes a total of 0.925 mAh of power. If the power consumption is 800 mAh, the alkaline battery can work continuously for more than 800 days. However, due to the battery shelf life and the self-discharge of the battery itself, plus the internal resistance when the power is low, it can guarantee normal operation for at least one year.
The power consumption of this acquisition terminal in normal operation all day is 0.925 μAh. It can maintain continuous normal operation for more than one year with 4 AA alkaline batteries. The measurement error is less than 0.16%. The communication protocol interface with the host system is simple and reliable. It can better meet the needs of the lower computer system of the groundwater dynamic monitoring system.
Previous article:Research on fuzzy control method of hydraulic system of excavator
Next article:Research on PID Parameter Self-tuning Method Based on CMAC Neural Network
Recommended ReadingLatest update time:2024-11-17 03:51
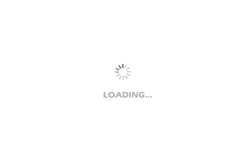
- Molex leverages SAP solutions to drive smart supply chain collaboration
- Pickering Launches New Future-Proof PXIe Single-Slot Controller for High-Performance Test and Measurement Applications
- CGD and Qorvo to jointly revolutionize motor control solutions
- Advanced gameplay, Harting takes your PCB board connection to a new level!
- Nidec Intelligent Motion is the first to launch an electric clutch ECU for two-wheeled vehicles
- Bosch and Tsinghua University renew cooperation agreement on artificial intelligence research to jointly promote the development of artificial intelligence in the industrial field
- GigaDevice unveils new MCU products, deeply unlocking industrial application scenarios with diversified products and solutions
- Advantech: Investing in Edge AI Innovation to Drive an Intelligent Future
- CGD and QORVO will revolutionize motor control solutions
- Innolux's intelligent steer-by-wire solution makes cars smarter and safer
- 8051 MCU - Parity Check
- How to efficiently balance the sensitivity of tactile sensing interfaces
- What should I do if the servo motor shakes? What causes the servo motor to shake quickly?
- 【Brushless Motor】Analysis of three-phase BLDC motor and sharing of two popular development boards
- Midea Industrial Technology's subsidiaries Clou Electronics and Hekang New Energy jointly appeared at the Munich Battery Energy Storage Exhibition and Solar Energy Exhibition
- Guoxin Sichen | Application of ferroelectric memory PB85RS2MC in power battery management, with a capacity of 2M
- Analysis of common faults of frequency converter
- In a head-on competition with Qualcomm, what kind of cockpit products has Intel come up with?
- Dalian Rongke's all-vanadium liquid flow battery energy storage equipment industrialization project has entered the sprint stage before production
- Allegro MicroSystems Introduces Advanced Magnetic and Inductive Position Sensing Solutions at Electronica 2024
- Car key in the left hand, liveness detection radar in the right hand, UWB is imperative for cars!
- After a decade of rapid development, domestic CIS has entered the market
- Aegis Dagger Battery + Thor EM-i Super Hybrid, Geely New Energy has thrown out two "king bombs"
- A brief discussion on functional safety - fault, error, and failure
- In the smart car 2.0 cycle, these core industry chains are facing major opportunities!
- Rambus Launches Industry's First HBM 4 Controller IP: What Are the Technical Details Behind It?
- The United States and Japan are developing new batteries. CATL faces challenges? How should China's new energy battery industry respond?
- Murata launches high-precision 6-axis inertial sensor for automobiles
- Ford patents pre-charge alarm to help save costs and respond to emergencies
- LLC formula derivation, loop compensation transfer function derivation calculation and simulation
- EEWORLD University Hall ---- Introduction to Deep Learning
- [FreeRTOS check-in station 4 opens] Inter-task communication, closing time is August 23
- [Technical Discussion] How to troubleshoot electromagnetic interference in wireless communications?
- Urgent recruitment
- STM32 replacement note: It is easy to replace domestic chips!
- Micron ships 232-layer NAND, expanding the boundaries of 3D NAND technology——Win gifts by passing levels now!
- The Present and Future of Finger Vein Recognition Technology (Electronics Industry Procurement)
- Inventory of major domestic MCU manufacturers
- Fluorescent lamp remote control dimming controller