1 Overview
ST72141 is a single-chip microcomputer specially designed by ST Company for synchronous motor control. It is especially suitable for the control of 3-phase brushless DC motors. Brushless DC motors can be used in products such as industrial controls, automotive electronics, refrigerators, air conditioners, compressors and fans. The advantages of brushless DC motors are high efficiency, low operating noise, small size, good reliability and long life.
ST72141 is a member of the ST7 microcontroller family. It includes A/D conversion and SPI interface, has on-chip peripherals specifically for brushless DC motor control, and can choose between sensor mode and sensorless mode.
The motor control circuit on the ST7 chip can be regarded as a pulse width modulation multiplexer. It has 6 outputs and 1 back electromotive force zero point detection circuit used when controlling brushless DC motors without sensors.
The motor control peripheral of ST72141 has 4 main parts:
◇ Detection circuit for the end of demagnetization and zero point of back electromotive force;
◇ Delay management circuit;
◇ PWM management circuit (requires PWM signal to drive the motor);
◇ Channel management circuit.
A typical application of ST72141 in a brushless DC motor is shown in Figure 1. 2 Basic principles of brushless DC motor
A brushless DC motor contains two coaxial magnetic armatures: the outer armature, which is the fixed stator, and the inner armature, which is the movable rotor. The stator is the guiding part of the motor; the rotor is the inductive part of the motor. The rotor of the brushless DC motor's internal armature is a permanent magnet. This armature is powered by a constant current source. The stator can have multiple phases (here, 3 phases are taken as an example). The motor is a synchronous motor. The brushless permanent magnet DC motor is a synchronous motor, and the magnetic field rotation speed of the stator is the same as the mechanical rotation speed of the rotor.
Back EMF is the basis for driving a brushless DC motor in sensorless mode using the ST72141. The back electromotive force is proportional to the rotation speed of the rotor, the magnetic flux flowing through the rotor and the number of rotors in the corresponding windings.
The torque generated by the winding is proportional to the current and magnetic flux.
ST72141 provides 2 control modes: voltage mode and current mode. In current mode, the torque can be directly adjusted proportionally; in voltage mode, the speed can be adjusted and the torque limit threshold (i.e., the current threshold) can be set.
3 ST72141 for brushless DC motor control
Figure 2 is a schematic diagram of motor control using 6 steps.
The motor control in ST72141 is based on the standard three half-bridge 6-step control principle.
T1, T3, and T5 are the upper-end transistors of the motor A, B, and C winding phases.
T2, T4, and T6 are the lower-end transistors of the A, B, and C winding phases of the motor.
At step size 1, phase A is forward biased, so the current in this winding is positive; phase B is reverse biased, so the current in this phase winding is negative. At this time, no power is applied to the C-phase winding.
In brushless mode, using ST72141 to control the motor, you can read the phase winding back electromotive force without applied power (here, starting with winding phase C as the step size 1). By reading this back EMF, the actual position of the rotor can be determined. As shown in Figure 3, the efficiency is optimal when the back electromotive force and the current of the phase winding are in the same direction.
ST72141 can have 2 different driving modes: voltage mode and current mode. In current mode, the magnitude of the torque is changed by changing the reference current of the motor (because the torque is proportional to the current). The current control is adjusted through PWM. In voltage mode, the speed is changed by changing the reference voltage of the motor. This mode does not directly control the current, but sets the highest limit of the current, that is, the maximum value of the torque that can be reached. Voltage control is also achieved by changing the PWM period.
Adjustment of the motor speed is achieved using a closed loop. There are 2 speed adjustment loops inside ST72141. The first loop is the adjustment loop for efficiency during automatic reversal. This loop makes the back electromotive force and the current signal of the phase winding in the same direction. The second loop is the speed adjustment loop, which can maintain the motor at the set speed.
ST72141 processes motor control based on three events: back electromotive force zero-crossing event (Z event), commutation (C event), and winding demagnetization end (D event), as shown in Figure 4.
The end of demagnetization and the zero-crossing point of back electromotive force are physical events, but the commutation event is calculated through ST72141, that is, the delay time between the zero-crossing event and the next commutation is calculated. If the speed is increased, the zero-crossing event will occur earlier and the delay must be reduced to bring the back EMF and phase winding currents in the same direction.
The motor control peripheral of the ST72141 always handles these 3 events in the same order: the Z event generates the C event after a calculated delay, and then waits for the D event. When the motor starts, it enters the automatic commutation mode after detecting certain continuous Z events. In ST72141, the detection of Z event (zero crossing point) and D event (end of demagnetization) are handled by the same peripheral part. These signals are input through the three pins of MCIA, MCIB and MCIC of ST72141. The principle of zero-crossing event (Z event) detection is shown in Figure 5.
Figure 5 shows the two states of motor control. In the left part of Figure 5, winding C has been demagnetized. After approximately 20 μs , the window for reading the back EMF opens. When T1 is turned off, current flows through the freewheeling diode, and point A is ground. Assume that the back electromotive force of the A-phase winding is Ea, the back electromotive force of the B-phase winding is Eb, and the back electromotive force of the C-phase winding is Ec. When Ec crosses the zero point, Ea=-Eb, so there is zero potential at N. This means that the required back electromotive force information can be obtained without a virtual ground. The back electromotive force zero-crossing event is obtained through the output comparator. In sensorless mode, a PWM signal of a certain frequency is added to T1. The voltage of C is clamped by the clamping diode at +5V/0.6V (what needs to be paid attention to is the zero crossing point). The analysis here also applies to motor windings with delta connections.
One input of the comparator is the voltage signal of the C-phase winding, and the other input is a threshold voltage (0.2, 0.6, 1.2 and 2.5V selectable through software). ST72141 waits for the back electromotive force of the C-phase winding to reach the selected threshold voltage. The PWM signal is applied to T1, and when T1 is turned off, the voltage of the C-phase winding is ground. Therefore, the ST72141 only needs to read the back EMF to detect the point in time when this threshold is reached.
The method of detecting the demagnetization end event is the same as the zero-crossing event, and uses the same peripherals. The motor control processes these three events in a fixed order. After a delay after the Z event, a C event is generated, and then it waits for a D event. After commutation, accelerated phase winding demagnetization begins. To avoid premature detection of end-of-demagnetization events, there is a 20 μs filtering time after commutation, as shown in Figure 6. In order to avoid detecting the end of degaussing event too late, the detection of the end of degaussing uses the same comparator, but the sampling frequency is 800kHz.
In the sensorless mode, the output sampling frequency of the comparator is the PWM signal during the zero-crossing event and is 800kHz during the demagnetization end event detection.
4 Examples of starting and controlling motors
Here we take the starting of a motor with 2 pole pairs as an example. After the motor starts, the target speed is 1400r/min. Before starting the motor, the position must be pre-fixed. When first started, the back EMF signal is too weak to be read. In the process before reading the back electromotive force signal, the current must provide > (load torque + friction torque + torque of the inertial load of the motor). Therefore, during startup, the PWM duty cycle of ST72141 timer A must be higher than the value required under normal operation.
After a certain step size, in order to detect the zero-crossing event, a special method is needed to start the motor, called synchronous (forced commutation) mode, or the process of the motor accelerating according to the accelerometer. After a certain step size, continuously increasing step time and current are applied to the motor to accelerate the motor and detect a zero-crossing event. After detecting a specified number of consecutive Z events during motor acceleration, adjustments will be made to make the motor run at high efficiency, that is, the motor will enter automatic commutation mode. If the motor cannot enter the automatic commutation mode after the accelerometer is taken, the motor will stop. Figure 7 shows the starting process of the motor in closed-loop mode.
The starting process in open loop mode is the same, except that the current or voltage can be changed by the user after the motor enters automatic commutation mode. In closed-loop mode, the current or voltage limit is imposed by the user and fixed until the motor enters speed adjustment. After entering speed adjustment, the current is no longer controlled by the user (ST72141 automatically adjusts). In closed-loop control mode, no matter which control mode (current or voltage), the speed adjustment loop starts. The motor is controlled by the microcontroller and runs at a fixed speed determined by the speedometer.
Previous article:Using ST72141 to realize the control of brushless DC motor
Next article:EM78P447S microcontroller and its application in DC motor infrared remote control system
Recommended ReadingLatest update time:2024-11-16 16:49
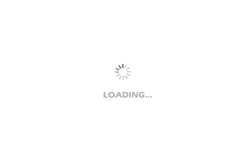
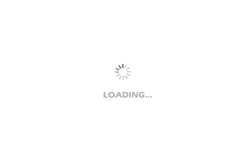
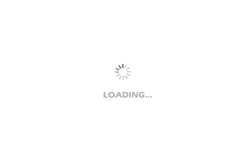
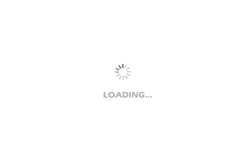
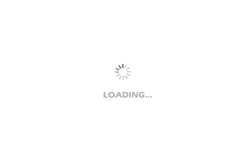
- Popular Resources
- Popular amplifiers
-
Analysis and Implementation of MAC Protocol for Wireless Sensor Networks (by Yang Zhijun, Xie Xianjie, and Ding Hongwei)
-
Introduction to Internet of Things Engineering 2nd Edition (Gongyi Wu)
-
西门子S7-12001500 PLC SCL语言编程从入门到精通 (北岛李工)
-
Modern Motor Control Technology (Wang Chengyuan, Xia Jiakuan, Sun Yibiao)
- Molex leverages SAP solutions to drive smart supply chain collaboration
- Pickering Launches New Future-Proof PXIe Single-Slot Controller for High-Performance Test and Measurement Applications
- CGD and Qorvo to jointly revolutionize motor control solutions
- Advanced gameplay, Harting takes your PCB board connection to a new level!
- Nidec Intelligent Motion is the first to launch an electric clutch ECU for two-wheeled vehicles
- Bosch and Tsinghua University renew cooperation agreement on artificial intelligence research to jointly promote the development of artificial intelligence in the industrial field
- GigaDevice unveils new MCU products, deeply unlocking industrial application scenarios with diversified products and solutions
- Advantech: Investing in Edge AI Innovation to Drive an Intelligent Future
- CGD and QORVO will revolutionize motor control solutions
- Innolux's intelligent steer-by-wire solution makes cars smarter and safer
- 8051 MCU - Parity Check
- How to efficiently balance the sensitivity of tactile sensing interfaces
- What should I do if the servo motor shakes? What causes the servo motor to shake quickly?
- 【Brushless Motor】Analysis of three-phase BLDC motor and sharing of two popular development boards
- Midea Industrial Technology's subsidiaries Clou Electronics and Hekang New Energy jointly appeared at the Munich Battery Energy Storage Exhibition and Solar Energy Exhibition
- Guoxin Sichen | Application of ferroelectric memory PB85RS2MC in power battery management, with a capacity of 2M
- Analysis of common faults of frequency converter
- In a head-on competition with Qualcomm, what kind of cockpit products has Intel come up with?
- Dalian Rongke's all-vanadium liquid flow battery energy storage equipment industrialization project has entered the sprint stage before production
- Allegro MicroSystems Introduces Advanced Magnetic and Inductive Position Sensing Solutions at Electronica 2024
- Car key in the left hand, liveness detection radar in the right hand, UWB is imperative for cars!
- After a decade of rapid development, domestic CIS has entered the market
- Aegis Dagger Battery + Thor EM-i Super Hybrid, Geely New Energy has thrown out two "king bombs"
- A brief discussion on functional safety - fault, error, and failure
- In the smart car 2.0 cycle, these core industry chains are facing major opportunities!
- The United States and Japan are developing new batteries. CATL faces challenges? How should China's new energy battery industry respond?
- Murata launches high-precision 6-axis inertial sensor for automobiles
- Ford patents pre-charge alarm to help save costs and respond to emergencies
- New real-time microcontroller system from Texas Instruments enables smarter processing in automotive and industrial applications
- [GD32E503 Evaluation] mig29_Step2 Measure the physical characteristics of DAC and ADC
- Pressure sensor power supply application solution
- RISC-V Manual (Chinese, a guide to the open source instruction set)
- Award Ceremony: Watch the live broadcast to learn more about the principle, operation, and waterproof structure design of ST's latest MEMS barometer
- [Project source code] Design and implementation of multi-channel DDS signal generator based on FPGA
- MSP430F248TPMR Texas TI ultra-low power microcontroller package LQFP
- Introduction to RF Front-end Technology
- Causes of voltage drop and measures to achieve the lowest possible voltage drop
- WS2410 high performance and low power consumption 2.4G SOC chip
- Does anyone know what circuit this is and what function it has?