As a new type of semiconductor light source, LED has been increasingly valued by the industry. LED lights and backlight sources have been widely used in many fields. This article will introduce some characteristics of LED semiconductor light sources and the purpose and key points of thermal management, "Thermal Ohm's Law", heat flow transmission and node temperature detection and analysis methods, and preliminary experimental results of the comparison of the application of thermal conductive graphite and aluminum heat sinks for readers' reference
.
Unlike incandescent lamps, traditional fluorescent lamps and halogen lamps, LED semiconductor light sources are made of semiconductor materials and consist of a PN junction. Hole-electron pairs recombine to generate light and work in the forward direction of the PN junction. The P region is the positive (anode) electrode and the N region is the negative (cathode) electrode. LED semiconductor light sources are small in size, high in luminous efficiency, short in response time and energy-saving. In addition, they have characteristics that traditional light sources do not have:
1. Similar characteristics to general PN junction devices (such as diodes):
forward voltage must exceed a certain threshold to have current; both
forward voltage and forward current have negative temperature coefficients and decrease with increasing temperature;
in reverse, there is no current and it does not work.
2. Like all semiconductor devices, its operating temperature is subject to the following factors:
the junction temperature must be kept below the rated value of 95 oC ~ 125 oC (depending on the light-emitting device), otherwise it will cause failure;
if there is a plastic lens on the surface, it will also be limited by the melting point temperature of the lens material;
the brightness of the LED is related to the forward current, and after the junction temperature exceeds a certain value, the forward current decreases and the brightness decreases.
Usually, there are two possible failure modes of LED: light degradation and total failure. Light degradation occurs when the emitted light drops to 50% of its initial value. In addition to total failure caused by exceeding the maximum allowable junction temperature, total failure also occurs due to internal open circuits, including: between the chip and the lead frame, between the chip and the bonding wire, and between the bonding wire and the lead frame. One of the reasons for failure is that the LDE resin glass lens is overheated, softened, and then cooled. The stress generated causes an internal open circuit.
It is very important for users to understand these characteristics, especially their thermal characteristics. This reminds me of the scene when transistors replaced electron tubes in electronic circuits. Due to the sensitivity of transistors as semiconductor devices to temperature, at the beginning of their application, some engineers and technicians who were familiar with the application of electron tubes in the past believed that although transistors had many advantages, their reliability was not as good as electron tubes. However, the power of new things is unstoppable. With the advancement of application technology, the use of temperature compensation and negative feedback to suppress temperature drift and stabilize the operating point has made transistors and semiconductor integrated circuit technology the core technology of today's electronic information technology. In the field of light source technology, the application technology of LED will also go through the process of how to make the best use of its strengths and avoid its weaknesses.
Thermal
management design and "Thermal Ohm's Law"
The purpose of thermal management design is
to ensure that the device works under appropriate conditions to achieve high reliability;
prevent driving under overstress conditions to extend the working life of the LED;
work at the maximum possible current to improve the light output performance.
The key points of thermal management are: to keep the operating temperature of the LED within a reasonable range through heat conduction and heat dissipation. Usually, the heat of the LED is conducted to the heat sink by heat conduction, and then the heat "buried" in the heat sink is dissipated. This "conduction" and "dissipation" are very important and indispensable, and heat dissipation depends not only on conduction but also on convection and radiation.
When conducting thermal management analysis, the commonly used basic law is the heat flow law, the so-called "thermal Ohm's law".
When analyzing current transmission, Ohm established the well-known Ohm's law, namely: U=R*I, where R is the resistance, I is the current, and U is the potential difference across the resistor R. In the case of heat transfer, there is a law similar in form: △T=Rth*Po, which is also called "thermal Ohm's law" by some users (in fact, this law has nothing to do with Ohm).
Here Rth represents thermal resistance, which characterizes the resistance to heat transfer. The unit is oC/W;
Po is heat flow, that is, the amount of heat transferred per unit time Po=Q (heat)/t (time), and the dimension is the same as power.
△T represents the temperature difference between two points in the heat transfer process, that is, the temperature difference on the thermal resistance between these two points.
When testing electronic circuits, we often use a multimeter to detect the potential and potential difference of the relevant nodes, that is, the voltage. When testing heat transfer, point thermometers, thermocouples and infrared thermal imagers can be used to detect the temperature and temperature difference of the relevant nodes on the heat transfer path. In
Ohm's law, the current in the series circuit is equal everywhere, but this is not the case for heat transfer. At some points, the heat transfer will be blocked due to excessive thermal resistance, causing heat accumulation.
The following can be detected and estimated using "Thermal Ohm's Law":
Similar to establishing an equivalent circuit in circuit analysis, an equivalent heat flow path diagram can also be established during heat flow analysis.
Detect and estimate the LED junction temperature Tj;
determine the heat dissipation effect and thermal resistance between related nodes;
evaluate the quality of LED working conditions when using heat sinks of different materials.
There are several important temperature nodes in heat flow analysis:
the junction temperature Tj of the chip PN junction should be less than the rated value specified by the product to make it work within a safe range.
The solder point temperature Ts is the temperature at the LED lead end and the base plate pad.
The interface temperature Ta between the heat sink and the external environment
should be able to dissipate the heat generated by the heat source LED, so that the junction temperature Tj is maintained at a reasonable and safe value, in order to obtain the maximum forward current If allowed by the device and obtain the highest luminous effect.
Analysis Examples
The three examples to be introduced here are: the establishment of a heat flow diagram, the calculation of the junction temperature Tj of a certain SMT packaging structure (SMD type) LED, and the preliminary experiment on the influence of different bulk materials on LED performance.
1. Equivalent heat flow diagram
Figure 1 and Figure 2 are the internal structure diagram and static equivalent heat path of SMT package (i.e. SMD type) LED respectively.
Figure 1 Internal structure of SMD LED
The arrows in the figure indicate the heat transfer path.
Figure 2 Static equivalent thermal circuit diagram of SMD LED
In this static equivalent thermal circuit, the internal thermal resistance is composed of 4 parts in series, that is, internal thermal resistance = chip thermal resistance + chip bonding (attachment) thermal resistance + lead frame thermal resistance + solder joint thermal resistance. The external thermal resistance is determined by specific application conditions. For example, if the LED is assembled on a PCB board, its external thermal resistance = pad thermal resistance + PCB thermal resistance.
Po is the heat flow, Tj is the junction temperature, Ts is the solder joint temperature, and Ta is the ambient interface temperature.
2. Junction temperature detection and estimation:
For a certain (LAE67B) SMT package structure LED, the solder joint temperature Ts = 70 oC was measured with a spot thermometer.
At the same time, the external forward voltage U was measured to be 2.1V and the forward current was 50mA. The thermal resistance of LAE67B is 130 oC /W, and assuming that all electrical power is converted into heat flow, the calculation is based on "Thermal Ohm's Law":
Tj=130130 oC /W *50mA*2.1V+70 oC
=83.7 oC.
The actual junction temperature Tj is less than the maximum allowable junction temperature of 125oC, so it is safe to work.
3. Preliminary experiment on the effect of different heat sink materials on LED performance
From the above analysis, it can be seen that temperature has a great influence on the luminous performance, life and reliability of LED. The influence of heat dissipation effect on the performance of LED is a very wide-ranging research topic. This example is only a preliminary experiment.
In the experiment, for the same LED, aluminum and thermally conductive graphite heat sinks were used for heat dissipation, and the same forward voltage was applied to record the forward current value, solder point temperature and illumination value. The experimental results show that; because the thermal resistance of thermally conductive graphite material is much smaller than that of aluminum, the temperature Ta at the graphite heat sink rises quickly at a lower current after the LED is lit. After a period of equilibrium, it is slightly higher than the temperature at the aluminum plate heat sink. The former is also slightly brighter. When it is turned on for a long time and works at a larger current, the difference gradually becomes obvious.
Conclusion
This article introduces the importance, purpose requirements, design management points, detection and analysis methods and case analysis of thermal management design for LEDs. The overall failure and light loss of LED lamps are related to temperature. The influencing factors include: the ambient temperature of the LED; the heat conduction channel between the LED junction and the outside; the energy released by the chip, etc. Although the key point of thermal management design and implementation is to "conduct" and "dissipate" the heat of LED to reduce the thermal resistance of each part. But it still involves many aspects:
prevent external heat from being transferred to the LED junction point to increase the temperature of Ta (such as separating the drive circuit and the LED circuit board);
LED pad design and assembly process, to consider the factors of thermoelectric compatibility;
the most important is: the selection and assembly of heat sink (device) (including assembly position and orientation), also including the selection of new thermal conductive materials and heat sink;
due to limited space, no more details. The thermal resistance of the package and the thermal resistance of the external heat sink are closely related to the thermal conductivity of the materials used and the assembly technology. These are the hot topics that the author and colleagues in the industry are concerned about, and we look forward to making new progress in this field.
Previous article:PI releases new reference design based on single-stage LinkSwitch-PH LED driver IC series - DER-278
Next article:Experts answer the top ten LED questions
Recommended ReadingLatest update time:2024-11-16 15:57
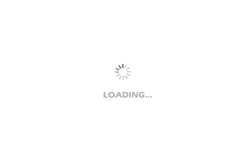
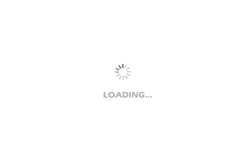
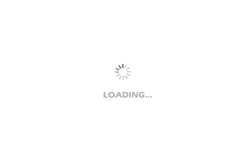
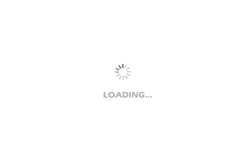
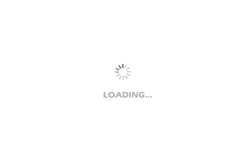
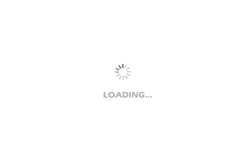
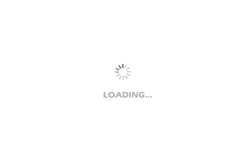
- Popular Resources
- Popular amplifiers
- MathWorks and NXP Collaborate to Launch Model-Based Design Toolbox for Battery Management Systems
- STMicroelectronics' advanced galvanically isolated gate driver STGAP3S provides flexible protection for IGBTs and SiC MOSFETs
- New diaphragm-free solid-state lithium battery technology is launched: the distance between the positive and negative electrodes is less than 0.000001 meters
- [“Source” Observe the Autumn Series] Application and testing of the next generation of semiconductor gallium oxide device photodetectors
- 采用自主设计封装,绝缘电阻显著提高!ROHM开发出更高电压xEV系统的SiC肖特基势垒二极管
- Will GaN replace SiC? PI's disruptive 1700V InnoMux2 is here to demonstrate
- From Isolation to the Third and a Half Generation: Understanding Naxinwei's Gate Driver IC in One Article
- The appeal of 48 V technology: importance, benefits and key factors in system-level applications
- Important breakthrough in recycling of used lithium-ion batteries
- Innolux's intelligent steer-by-wire solution makes cars smarter and safer
- 8051 MCU - Parity Check
- How to efficiently balance the sensitivity of tactile sensing interfaces
- What should I do if the servo motor shakes? What causes the servo motor to shake quickly?
- 【Brushless Motor】Analysis of three-phase BLDC motor and sharing of two popular development boards
- Midea Industrial Technology's subsidiaries Clou Electronics and Hekang New Energy jointly appeared at the Munich Battery Energy Storage Exhibition and Solar Energy Exhibition
- Guoxin Sichen | Application of ferroelectric memory PB85RS2MC in power battery management, with a capacity of 2M
- Analysis of common faults of frequency converter
- In a head-on competition with Qualcomm, what kind of cockpit products has Intel come up with?
- Dalian Rongke's all-vanadium liquid flow battery energy storage equipment industrialization project has entered the sprint stage before production
- Allegro MicroSystems Introduces Advanced Magnetic and Inductive Position Sensing Solutions at Electronica 2024
- Car key in the left hand, liveness detection radar in the right hand, UWB is imperative for cars!
- After a decade of rapid development, domestic CIS has entered the market
- Aegis Dagger Battery + Thor EM-i Super Hybrid, Geely New Energy has thrown out two "king bombs"
- A brief discussion on functional safety - fault, error, and failure
- In the smart car 2.0 cycle, these core industry chains are facing major opportunities!
- The United States and Japan are developing new batteries. CATL faces challenges? How should China's new energy battery industry respond?
- Murata launches high-precision 6-axis inertial sensor for automobiles
- Ford patents pre-charge alarm to help save costs and respond to emergencies
- New real-time microcontroller system from Texas Instruments enables smarter processing in automotive and industrial applications
- Keil compiles ADuC7029 and reports an error
- Technical Article: Optimizing 48V Mild Hybrid Electric Vehicle Motor Drive Design
- DIY an STLink V2.1
- Playing with Zynq Serial 18——[ex01] Trying out the first project based on Zynq PL
- Hangshun chip-HK32F103 xCxDxE data sheet
- How to lay digital and analog floors?
- The entire process of R&D and production of a chip
- pyWatch with BLE functionality and micropython
- Use the microcontroller DAC to output analog voltage and control the output voltage of the DC-DC circuit so that Vout=2*Vset. Please help me design the circuit
- Summary of DSP2000 serial port programming operation