1. Background: Chip factory expansion
According to Jingyuan Company's prediction, (1) if LED LCD TVs account for 10% of the LCD TV market share, the current production capacity of LED chip factories around the world will be in short supply (this prediction has now been confirmed); (2) the lighting market is even larger. If 100% of the incandescent lamps in the world are replaced by LED lamps , the demand for LED chips in LED lighting will be 100 times that of LED LCD TVs. Even if 10% of incandescent lamps are replaced by LED lamps, the demand for LED chips will be 10 times that of LED LCD TVs. A more optimistic estimate is that in the next 1 to 2 years, LED will enter the lighting market in a big way.
Therefore, on the one hand, various LED chip companies are expanding production, and on the other hand, other funds are also pouring into the LED chip industry. For example, Samsung in South Korea has purchased a large amount of MOCVD epitaxial equipment.
The bottleneck is that the expansion speed of epitaxial equipment factories is limited (it is reported that the world's two largest MOCVD manufacturers expect to double their production capacity by the end of this year), and the expansion speed of sapphire substrate factories is limited (currently, there are only a handful of qualified sapphire substrate manufacturers). The expansion speed of epitaxial equipment factories and sapphire substrate factories is far from the speed of the increase in demand for LED chips for LED lighting. The supply of other chip equipment and raw materials will be tight.
How to expand the production capacity of equipment factories and raw material factories in the next few years to meet the demand for LED chips in LED lighting?
2. A mitigation method: LED chips driven by high current
One of the ways to alleviate the problem is to develop and produce within 1 to 2 years LED chips that can be driven by large currents, so that the luminous flux emitted by one chip is equivalent to the luminous flux of several traditional LED chips.
The advantages of high current driven LED chips are as follows:
(1) It is equivalent to reducing the price of LED chips to a fraction of the original chips, which is more conducive to the promotion of LED lighting.
(2) It is equivalent to increasing the existing production capacity several times without increasing the extremely expensive equipment investment, reducing the risk.
(3) It improves the production capacity of the newly expanded equipment.
In order to understand this mitigation method more intuitively, two definitions of chip capacity are introduced:
(A) “Chip production capacity”.
(B) "lm capacity", that is, the capacity of a chip factory is calculated by the number of lm, because the lighting fixtures are required to be calculated by the number of lm (or lux) rather than the number of chips used in the fixtures, which is somewhat like the capacity of a power plant is calculated by the amount of electricity generated.
For example, the "chip capacity" of a chip factory is: 100 kk of 45mil chips per month.
If each chip emits 100 lm of light when driven at 350mA after packaging, the "lm production capacity" of the factory can be said to be 10 kkk lm. However, if each chip emits 300 lm of light when driven at a higher current after packaging, the "lm production capacity" of the factory can be said to be 30 kkk lm. However, according to the 100 lm LED chip driven at 350mA, in order to achieve the "lm production capacity" of 30 kkk lm, the "chip production capacity" required is: 300 kk of 45mil chips driven at 350mA per month.
For the example above, this is equivalent to:
(1) The cost per lm of luminous flux of high-current driven chips was reduced to 1/3 of the original;
(2) The "lm production capacity" of chip manufacturers increased by 3 times, but the "chip production capacity" of chip manufacturers did not increase. Therefore, there was no huge increase in equipment investment, saving the huge investment in expanding the "chip production capacity" to 200 kk per month;
(3) It also saved the raw material costs of epitaxial growth and chip process of 350mA driven chips with a monthly output of 200 kk.
This not only eases the pressure on equipment manufacturers, but also eases the demand for raw materials (including sapphire substrates).
If it can be driven with a higher current (for example, a current on the order of several amperes), the advantage will be even greater.
The news that Samsung of South Korea purchased a large number of epitaxial equipment has been quoted many times, but what has not attracted widespread attention is that Samsung is cooperating with others to develop high-current drive LED chips and has already made patent layouts at the epitaxial level. By then, not only will the "chip production capacity" of Samsung's epitaxial equipment be astonishingly large, but its "lm production capacity" will be even more astonishing - several times the "lm production capacity" of 350mA driven LED chips. Manufacturers without high-current drive chip technology will find it even more difficult to match them.
3. Development of high current driven LED chips
It was revealed that Cree's 1.5A current-driven chip is undergoing aging testing, and so far, it has only decayed by 7% after 6,000 hours.
We know that LED chips that can be driven with high current must meet the following conditions at the (A) epitaxial level, (B) chip level, and (C) packaging level:
(A) Epitaxial layer: The key issue is to solve the problem of chip quantum efficiency droop when driven by high current. Some companies are developing methods to solve efficiency droop. For example, the University of Virginia in the United States has made public the results of experiments: using a magnesium-doped InGaN barrier layer instead of an undoped GaN barrier layer, the maximum external quantum efficiency is obtained at a current density of 900A/cm2 (equivalent to using a 9A current to drive a 1mm2 chip). In comparison, the current density of the common high-power 1mm2 LED chips on the market is only 35A/cm2. Recently, the university made public their research and development results on non-polarized LEDs driven by high current (see Figure 1).
![]() |
![]() |
Figure 1
Moreover, the University of Virginia also found that for current flowing laterally in P-GaN, that is, for LED chips with a lateral structure, current congestion will cause additional quantum efficiency decline.
(B) Chip level (see "China Semiconductor Lighting Industry Development Yearbook (2008)"): The following conditions must be met: an effective method to introduce high current into the LED chip, uniform current distribution, no current congestion, and excellent heat dissipation performance of the chip.
3D vertical structure LED chips are more likely to meet the above conditions. The electrodes of a 3D vertical structure LED chip are shown in the figure below:
In the figure above, there are 4 strip electrodes, and therefore, 4 current introduction points, that is, the current flows from the N metal through the 4 current introduction points into the 4 strip electrodes, and then into the LED film, and the current introduced from each current introduction point is equal to 1/4 of the total current. Therefore, the current density near the current introduction point is small, and it is not easy to generate current congestion near the current introduction point. For larger currents, multiple strip electrodes can be used without too much light blocking.
The 3D vertical structure of LED chips has advantages in introducing large currents into the chip.
(C) Packaging level: The heat generated by large current must be effectively dissipated.
In short, in order to advance the progress of LED lighting as quickly as possible and meet the demand for LED chips in LED lighting, on the one hand, we must consider the expansion speed of chip equipment factories and raw material factories, and on the other hand, we must increase the production capacity of LED chips with as little investment as possible. The use of high-current driven chips can better meet these two needs, and 3D vertical structured LED chips are more suitable for high-current drive!
Previous article:Characteristics of LED LCD TV
Next article:Wafer bonding and inspection to reduce the cost of high brightness LEDs
Recommended ReadingLatest update time:2024-11-16 19:55
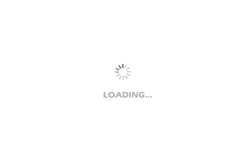
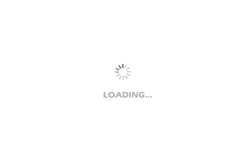
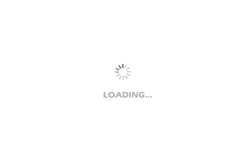
- MathWorks and NXP Collaborate to Launch Model-Based Design Toolbox for Battery Management Systems
- STMicroelectronics' advanced galvanically isolated gate driver STGAP3S provides flexible protection for IGBTs and SiC MOSFETs
- New diaphragm-free solid-state lithium battery technology is launched: the distance between the positive and negative electrodes is less than 0.000001 meters
- [“Source” Observe the Autumn Series] Application and testing of the next generation of semiconductor gallium oxide device photodetectors
- 采用自主设计封装,绝缘电阻显著提高!ROHM开发出更高电压xEV系统的SiC肖特基势垒二极管
- Will GaN replace SiC? PI's disruptive 1700V InnoMux2 is here to demonstrate
- From Isolation to the Third and a Half Generation: Understanding Naxinwei's Gate Driver IC in One Article
- The appeal of 48 V technology: importance, benefits and key factors in system-level applications
- Important breakthrough in recycling of used lithium-ion batteries
- Innolux's intelligent steer-by-wire solution makes cars smarter and safer
- 8051 MCU - Parity Check
- How to efficiently balance the sensitivity of tactile sensing interfaces
- What should I do if the servo motor shakes? What causes the servo motor to shake quickly?
- 【Brushless Motor】Analysis of three-phase BLDC motor and sharing of two popular development boards
- Midea Industrial Technology's subsidiaries Clou Electronics and Hekang New Energy jointly appeared at the Munich Battery Energy Storage Exhibition and Solar Energy Exhibition
- Guoxin Sichen | Application of ferroelectric memory PB85RS2MC in power battery management, with a capacity of 2M
- Analysis of common faults of frequency converter
- In a head-on competition with Qualcomm, what kind of cockpit products has Intel come up with?
- Dalian Rongke's all-vanadium liquid flow battery energy storage equipment industrialization project has entered the sprint stage before production
- Allegro MicroSystems Introduces Advanced Magnetic and Inductive Position Sensing Solutions at Electronica 2024
- Car key in the left hand, liveness detection radar in the right hand, UWB is imperative for cars!
- After a decade of rapid development, domestic CIS has entered the market
- Aegis Dagger Battery + Thor EM-i Super Hybrid, Geely New Energy has thrown out two "king bombs"
- A brief discussion on functional safety - fault, error, and failure
- In the smart car 2.0 cycle, these core industry chains are facing major opportunities!
- The United States and Japan are developing new batteries. CATL faces challenges? How should China's new energy battery industry respond?
- Murata launches high-precision 6-axis inertial sensor for automobiles
- Ford patents pre-charge alarm to help save costs and respond to emergencies
- New real-time microcontroller system from Texas Instruments enables smarter processing in automotive and industrial applications
- The role of capacitors in op amp circuits
- Repairing PCB without drawings, this article is enough
- [Fudan Micro FM33LC046N] PACK package also limits the MDK version?
- Can stm32f407 be used as a USB host to receive serial port data?
- uLisp, a Lisp language for embedded systems
- SensorTile.box firmware upgrade first experience
- EPLAN P8 Advanced Tutorial (Chinese)
- [ESP32-Audio-Kit Audio Development Board Review] Part 3 play_mp3_control
- PCB manufacturing experience summary (2)
- [Telink B91 Universal Development Kit] Questions about the functions of TX and RX on the burning tool