The figure below is the relationship curve between forward voltage drop (VF) and forward current (IF). From the curve, we can see that when the forward voltage exceeds a certain threshold (about 2V), which is usually called the on-voltage, it can be approximately considered that IF is proportional to VF. The table shows the electrical characteristics of the current main ultra-bright LEDs. From the table, we can see that the highest IF of the current ultra-bright LEDs can reach 1A, while VF is usually 2 to 4V.
Since the light characteristics of LEDs are usually described as a function of current rather than a function of voltage, the relationship curve between luminous flux (φV) and IF, therefore, constant current source driving can better control the brightness. In addition, the forward voltage drop of LEDs varies in a relatively large range (up to 1V or more), and from the VF-IF curve in the figure above, it can be seen that a small change in VF will cause a large change in IF, thereby causing a large change in brightness. Therefore, the use of a constant voltage source driving cannot guarantee the consistency of LED brightness, and affects the reliability, life and light decay of the LED. Therefore, ultra-bright LEDs are usually driven by a constant current source.
The figure below is the relationship curve between LED temperature and luminous flux (φV). It can be seen from the figure that luminous flux is inversely proportional to temperature. The luminous flux at 85℃ is half of that at 25℃, and the light output at -40℃ is 1.8 times that at 25℃. Temperature changes also have a certain impact on the wavelength of LFD. Therefore, good heat dissipation is the guarantee for LED to maintain constant brightness. See the relationship curve between LED temperature and luminous flux.
General LED drive circuit introduction
Due to the limitation of LED power level, it is usually necessary to drive multiple LEDs at the same time to meet the brightness requirements. Therefore, a special drive circuit is needed to light up the LED. The following briefly introduces the LED conceptual drive circuit.
Current limiting circuit
The resistor current limiting drive circuit is the simplest drive circuit, and the current limiting resistor is calculated according to the following formula.
Where: Vin is the input voltage of the circuit:
VF is the forward current of IED;
VF is the voltage drop of the LED when the forward current is IF;
VD is the voltage drop of the anti-reverse diode (optional);
y is the number of LEDs in each string;
x is the number of parallel LED strings.
From the above figure, the linear mathematical model of LED can be obtained as follows:
Where: Vo is the turn-on voltage drop of a single LED;
Rs is the linearized equivalent series resistance of a single LED.
The calculation of the current limiting resistor in the above formula can be written as: When the resistor is selected, the relationship between IF and VF of the resistor current limiting circuit is: From the above formula, it can be seen that the resistor current limiting circuit is simple, but when the input voltage fluctuates, the current through the LED will also change, so the regulation performance is poor. In addition, since the power loss of the resistor R is xRIF, the efficiency is low.
Introduction to Linear Regulators
The core of the linear regulator is to use the power transistor or MOSFET working in the linear region as a dynamically adjustable resistor to control the load. There are two types of linear regulators: parallel type and series type.
Figure a below shows a parallel linear regulator, also known as a shunt regulator (only one LED is drawn in the figure, but in fact the load can be multiple LEDs connected in series, the same below). It is connected in parallel with the LED. When the input voltage increases or the LED decreases, the current through the shunt regulator will increase, which will increase the voltage drop on the current limiting resistor to keep the current through the LED constant.
Since the shunt regulator requires a series resistor, it is not efficient and has difficulty in achieving constant regulation over a wide input voltage range.
The following figure b shows a series regulator. When the input voltage increases, the dynamic resistance is increased to keep the voltage (current) on the LED constant.
Since power transistors or MOSFETs have a saturation conduction voltage, the minimum input voltage must be greater than the sum of the saturation voltage and the load voltage for the circuit to work correctly.
Switching Regulator Introduction
The above driving technology is not only limited by the input voltage range, but also has low efficiency. When used for driving low-power ordinary LEDs, the loss is not obvious because the current is only a few mA. When used for driving high-brightness LEDs with a current of several hundred mA or even higher, the loss of the power circuit becomes a more serious problem. The switching power supply is the most efficient in energy conversion at present, which can reach more than 90%. Power converters such as Buek, Boost and Buck-Boost can all be used to drive LEDs, but for
In order to meet the constant current drive of LED, the output current is detected instead of the output voltage for feedback control. The following figure (a) shows the LED drive circuit using Buck converter. Unlike the traditional Buek converter, the switch tube S is moved behind the inductor L, so that the source of S is grounded, which facilitates the drive of S. The LED is connected in series with L, and the freewheeling diode D is connected in anti-parallel with the series circuit. The drive circuit is not only simple but also does not require an output filter capacitor, reducing the cost. However, Buck converter is a step-down converter and is not suitable for occasions with low input voltage or multiple LEDs in series.
Figure (b) above shows an LED drive circuit using a Boost converter, which uses inductive energy storage to pump the output voltage to a desired value higher than the input voltage, thereby achieving LED drive at a low input voltage. The advantage is that the output of such a driver IC can be used in parallel, effectively increasing the power of a single LED.
Figure (c) above is an LED drive circuit using a Buck-Boost converter. Similar to the Buek circuit, the source of S in this circuit can be directly grounded, which facilitates the drive of S. Although Boost and Buck-Boosl converters have one more capacitor than Buck converters, they can both increase the absolute value of the output voltage. Therefore, they are more commonly used when the input voltage is low and multiple LEDs need to be driven.
Introduction to PWM dimming knowledge
In mobile phones and other consumer electronics , white LEDs are increasingly being used as backlight sources for displays. Recently, many product designers want the brightness of white LEDs to be able to change in different applications. This means that the driver for white LEDs should be able to support the LED brightness adjustment function. There are currently three main dimming technologies: PWM dimming, analog dimming, and digital dimming. Many drivers on the market can support one or more of these dimming technologies.
The respective characteristics of these three dimming technologies will be introduced, and product designers can choose the corresponding technology according to specific requirements.
PWM Dimming (Pulse Width Modulation) dimming method - This is a dimming technology that uses simple digital pulses to repeatedly switch the white light LED driver. The user's system only needs to provide different wide and narrow digital pulses to simply change the output current and thus adjust the brightness of the white light LED. The advantages of PWM dimming are that it can provide high-quality white light, simple application, and high efficiency! For example, in the system of a mobile phone, a dedicated PWM interface can simply generate a pulse signal with any duty cycle, which is connected to the EN interface of the driver through a resistor. Most manufacturers' drivers support PWM dimming.
However, PWM dimming has its disadvantages. The main disadvantage is that PWM dimming can easily cause the white light LED driver circuit to produce audible noise (or microphonic noise). How is this noise generated? Usually white light LED drivers are switching power supply devices (buck, boost, charge pump, etc.), and their switching frequency is around 1MHz. Therefore, in typical applications of the driver, no audible noise is generated. However, when the driver performs PWM
When dimming, if the frequency of the PWM signal happens to fall between 200Hz and 20kHz, the inductor and output capacitor around the white light LED driver will generate audible noise. Therefore, it is necessary to avoid using low frequencies below 20kHz when designing.
We all know that a low-frequency switching signal acting on an ordinary wirewinding coil will cause mechanical vibrations between the coils in the inductor. The frequency of the mechanical vibrations falls exactly on the above frequency, and the noise emitted by the inductor can be heard by the human ear. The inductor generates part of the noise, and the other part comes from the output capacitor. Now more and more mobile phone designers use ceramic capacitors as the output capacitors of the driver. Ceramic capacitors have piezoelectric properties, which means that when a low-frequency voltage ripple signal acts on the output capacitor, the capacitor will emit a squeaking buzzing sound. When the PWM signal is low, the white light LED driver stops working, and the output capacitor discharges through the white light LED and the resistor at the lower end. Therefore, when PWM dimming is performed, the output capacitor inevitably generates a large ripple. In short, in order to avoid audible noise during PWM dimming, the white light LED driver should be able to provide a dimming frequency that exceeds the audible range of the human ear!
Compared with PWM dimming, if the resistance value of RS can be changed, the current flowing through the white light LED can also be changed, thereby changing the brightness of the LED. We call this technology analog dimming.
The biggest advantage of analog dimming is that it avoids the noise generated by dimming. When using analog dimming technology, the forward voltage drop of the LED will decrease as the LED current decreases, which reduces the energy consumption of the white light LED. However, unlike PWM dimming technology, the white light LED driver is always in working mode during analog dimming, and the driver's power conversion efficiency drops rapidly as the output current decreases. Therefore, the use of analog dimming technology often increases the energy consumption of the entire system.
Another disadvantage of analog dimming technology is the quality of light emission. Since it directly changes the current of white light LED, the quality of white light of white light LED also changes! In addition to PWM dimming and analog dimming, some manufacturers' drivers currently support digital dimming. White light LED drivers with digital dimming technology will have corresponding digital interfaces. The digital interface can be SMB, I2C, or a single-wire digital interface. System designers only need to give the driver a string of digital signals according to the specific communication protocol to change the brightness of the white light LED.
LED driver design tips
LED series-parallel drive reference design
LEDs cannot be made the same due to their VF characteristics. Some VF values will also change with temperature and current, so they are generally not suitable for parallel design. However, in some cases, multiple LEDs have to be connected in parallel to solve the cost problem of driving multiple LEDs. These designs can be used as a reference for everyone.
Please note that VF values need to be divided into different grades. LEDs with the same VF value should be used on the same product as much as possible. The product can ensure that the error current is within 1mA and the LED works in a relative constant current state.
The integrated transistors in the figure below can keep the current of each LED channel consistent. These transistors have the same β value produced under the same temperature environment and the same process conditions, which can ensure that the current of each channel is basically the same. The constant current part can be designed like this under conditions where the requirements are not very high. A stable voltage or a stable PWM volt value drives the bias of the transistor after voltage stabilization to achieve basic constant current.
The figure below uses a high-precision IC as a constant current reference source. R can set the IC output current. Once the R resistance value is determined, it can be replaced by a fixed resistor. The use of multi-transistor integrated devices can reduce the number of ICs used, thereby reducing the cost of design products.
Linear high-power LED constant current output can be used in parallel. In product design, we often cannot find driver ICs with larger currents. Generally, more than 2A is rare, and ICs with a nominal current of 2A may not be used to the limit. The reason for the process cost of ICs greater than 1A is that MOS tubes are external, and the circuits of external MOS tubes are complex and the reliability is reduced. Parallel use is an effective design method.
The figure below uses the DD312 parallel reference design to directly drive three 6W LEDs. The PWM control signal needs to be properly isolated to avoid mutual interference and drive capability issues. The EN enable voltage must meet the requirements of the specification, and the voltage should not be too high to damage the EN pin. Generally, the IC withstand voltage refers to the load and power supply. If the excitation voltage is not specified, please do not design it to be greater than 5V.
Like this, the LED constant current driver IC can also be designed in parallel for detection at one end of the LED. In fact, the IC works alone and finally flows in parallel. The DC-DC method works at a higher frequency. It should be noted that when laying out the PCB, cross design should be avoided. The respective filter and bypass capacitors should be close to the IC, and the load current will finally be summed.
Of course, you can design 2 in parallel, 3 in parallel, or more in parallel, but you should try it more often!
LED driver design reference case and selection guide High-power LED temperature protection reference design
The best temperature protection Curie point temperature should be 80-90℃. The highest ambient temperature is 40℃ in summer and 50℃ in summer sunlight exposure. 50℃ is the highest ambient temperature. Generally, the junction temperature of high-power LEDs can be tolerated at 120℃. The thermal resistance from the chip to the aluminum substrate is generally recommended to be 10-15℃ in the specification, so the LED substrate must be guaranteed to be 120-15=105℃. The temperature difference is retained and the middle value of 50--105℃ is 77.5℃. Generally, the operating temperature of electronic components is reliable at 85℃, and 77℃ is in line with this principle.
It is recommended to start protection at 77℃, reduce the current significantly before 85℃, and completely complete the product temperature protection function at 90℃. An ideal circuit can be designed by selecting a thermistor with a Curie point of around 85℃.
Previous article:LED packaging structure
Next article:LED Display Basics
Recommended ReadingLatest update time:2024-11-16 23:30
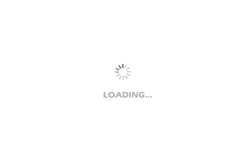
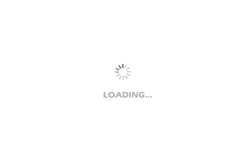
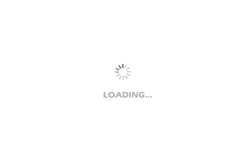
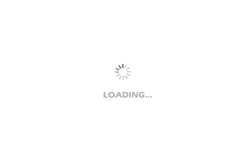
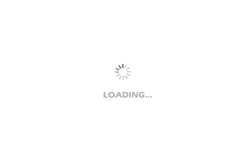
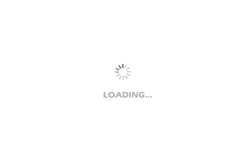
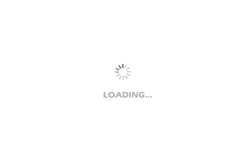
- MathWorks and NXP Collaborate to Launch Model-Based Design Toolbox for Battery Management Systems
- STMicroelectronics' advanced galvanically isolated gate driver STGAP3S provides flexible protection for IGBTs and SiC MOSFETs
- New diaphragm-free solid-state lithium battery technology is launched: the distance between the positive and negative electrodes is less than 0.000001 meters
- [“Source” Observe the Autumn Series] Application and testing of the next generation of semiconductor gallium oxide device photodetectors
- 采用自主设计封装,绝缘电阻显著提高!ROHM开发出更高电压xEV系统的SiC肖特基势垒二极管
- Will GaN replace SiC? PI's disruptive 1700V InnoMux2 is here to demonstrate
- From Isolation to the Third and a Half Generation: Understanding Naxinwei's Gate Driver IC in One Article
- The appeal of 48 V technology: importance, benefits and key factors in system-level applications
- Important breakthrough in recycling of used lithium-ion batteries
- Innolux's intelligent steer-by-wire solution makes cars smarter and safer
- 8051 MCU - Parity Check
- How to efficiently balance the sensitivity of tactile sensing interfaces
- What should I do if the servo motor shakes? What causes the servo motor to shake quickly?
- 【Brushless Motor】Analysis of three-phase BLDC motor and sharing of two popular development boards
- Midea Industrial Technology's subsidiaries Clou Electronics and Hekang New Energy jointly appeared at the Munich Battery Energy Storage Exhibition and Solar Energy Exhibition
- Guoxin Sichen | Application of ferroelectric memory PB85RS2MC in power battery management, with a capacity of 2M
- Analysis of common faults of frequency converter
- In a head-on competition with Qualcomm, what kind of cockpit products has Intel come up with?
- Dalian Rongke's all-vanadium liquid flow battery energy storage equipment industrialization project has entered the sprint stage before production
- Allegro MicroSystems Introduces Advanced Magnetic and Inductive Position Sensing Solutions at Electronica 2024
- Car key in the left hand, liveness detection radar in the right hand, UWB is imperative for cars!
- After a decade of rapid development, domestic CIS has entered the market
- Aegis Dagger Battery + Thor EM-i Super Hybrid, Geely New Energy has thrown out two "king bombs"
- A brief discussion on functional safety - fault, error, and failure
- In the smart car 2.0 cycle, these core industry chains are facing major opportunities!
- The United States and Japan are developing new batteries. CATL faces challenges? How should China's new energy battery industry respond?
- Murata launches high-precision 6-axis inertial sensor for automobiles
- Ford patents pre-charge alarm to help save costs and respond to emergencies
- New real-time microcontroller system from Texas Instruments enables smarter processing in automotive and industrial applications
- ZTE's 7nm chip mass production still needs time to catch up with high-end chip track
- Comparison of Three Synchronous Designs in FPGA
- Looking for package SOT128-1
- 【Qinheng RISC-V core CH582】Timer PWM drive servo
- Selection and use of bypass capacitors
- CircuitPython Holiday Wreath
- Application and advantages of mica capacitors
- First Battlefield
- Infrared remote control LED dot matrix
- [Chuanglong TL570x-EVM] Install Prossessor SDK and create a development environment