With the comprehensive improvement of high brightness light emitting diodes (HB-LED) in terms of light output, energy efficiency and cost, combined with many advantages such as compactness, low voltage operation and environmental protection, LED lighting (also known as solid-state lighting (SSL)) is setting off a lighting revolution. Under the trend of energy saving and environmental protection, LED lighting has naturally become the target of many regulatory agencies. For example, the 1.1 version of the solid-state lighting standard of the "Energy Star" project of the US Department of Energy has been effective since February 2009. China's China National Institute of Standardization is also taking the lead and working with relevant agencies to prepare to release the Chinese version of the LED lighting energy efficiency standard in 2010.
As for the new version of the solid-state lighting standard of "Energy Star", an important feature of this standard is that it requires a minimum power factor of 0.7 for a variety of residential lighting products, some of which are typical products such as portable table lamps, cabinet lights and outdoor corridor lights. The power of these LED lighting applications is generally between 1 and 12 W, which is a low-power application. The most suitable power supply topology for this type of low-power application is the isolated flyback topology. Unfortunately, the existing standard design techniques used to design these power supplies usually result in a power factor (PF) of only 0.5 to 0.6. This article will analyze the reasons for the low power factor of existing designs, explore the technology and solutions for improving the power factor, introduce the relevant design process and share some test data, showing how this reference design can easily meet the power factor requirements of the "Energy Star" solid-state lighting specification for residential LED lighting applications.
Design Background
A typical offline flyback power converter uses a full-wave bridge rectifier and a large capacitor in front of the switching regulator. This configuration is chosen because the line power decreases every 2 line cycles until it reaches zero and then rises to the next peak. The large capacitor acts as an energy storage element to fill the missing power and provide a more constant input to the switching regulator to maintain power flow to the load. This configuration has a low power utilization or power factor of the input line waveform. The line current is consumed in large, narrow pulses close to the peak of the voltage waveform, introducing interfering high-frequency harmonics.
There are many passive power factor correction (PFC) solutions in the industry, which usually use more additional components. One of the solutions is the valley-fill rectifier, in which the combination of electrolytic capacitors and diodes increases the line frequency conduction angle, thereby improving the power factor. In fact, this process uses high line voltage to charge the series capacitors with low current, and then discharges the capacitors to the switching regulator with a larger current at a lower voltage. Typical applications use 2 capacitors and 3 diodes, while to further enhance the power factor performance, 3 capacitors and 6 diodes are used.
Figure 1: Typical valley-fill circuit.
Although the valley-fill rectifier improves the utilization of the line current, it does not provide a constant input to the switching regulator. The power delivered to the load will have a large ripple, up to twice the line power frequency. It should be noted that four diodes are still required to rectify the line power, bringing the number of diodes used in this solution to seven or ten. These diodes and multiple electrolytic capacitors increase the solution cost, reduce reliability, and occupy considerable board area.
Another solution is to use an active PFC stage before the flyback converter, such as the NCP1607B. This solution provides excellent power factor with typical performance above 0.98, but increases the number of components, reduces efficiency and increases complexity. It is most suitable for power levels much higher than the power level of this application.
Solution
High power factor usually requires a sinusoidal line current with a very small phase difference between the line current and voltage. The first step in modifying the design is to get a very low capacitance before the switching stage, resulting in a more sinusoidal input current. This causes the rectified voltage to follow the line voltage, resulting in a more ideal sinusoidal input current. The flyback converter input voltage then follows the rectified sinusoidal voltage waveform at twice the line frequency. If the input current remains the same waveform, the power factor is high. The energy delivered to the load is the product of the voltage and current, a sine-squared waveform. Due to this sinusoidal energy transfer, the load will see a ripple at twice the line frequency, similar in nature to the ripple seen in valley-fill circuits.
As mentioned above, the input current must be maintained at a nearly sinusoidal waveform to achieve high power factor. The key to high power factor is to not allow the control loop to correct for output ripple by maintaining the feedback input at a constant level related to the line frequency. One option is to significantly increase the output capacitance, thereby reducing the amount of 120 Hz ripple, which may be required for some applications. LEDs for general lighting applications are more tolerant of ripple if the frequency is above the range of visible light perception. A more compact and inexpensive solution is to filter the feedback signal back to the PWM converter to establish a nearly constant level. This level fixes the maximum current in the power switch. The power switch current is determined by the applied instantaneous input voltage divided by the transformer primary inductance multiplied by the length of time the power switch is on. [page]
ON Semiconductor’s NCP1014LEDGTGEVB evaluation board is optimized to drive 1 to 8 high-power, high-brightness LEDs, such as Cree XLAMP® XR−E/XP−E, Luxeon™ Rebel, Seoul Semiconductor Z−POWER®, or OSRAM Golden Dragon™. The design is based on the NCP1014, a compact fixed-frequency pulse-width modulation (PWM) converter that integrates a high-voltage power switch with internal current limiting. Because the NCP1014 operates at a fixed frequency, the current cannot rise above a certain point; this point is determined by the input voltage and the primary inductance before the end of the switching cycle or on-time. Due to the on-time limitation, the input current will follow the waveform of the input voltage, providing a higher power factor. The relevant circuit diagram is shown in Figure 2.
Figure 2: NCP1014LEDGTGEVB circuit diagram.
Design Process
Higher switching frequencies can reduce transformer size, but at the same time increase switching losses. The 100 kHz version of the NCP1014 was chosen as a balance for this reference design. The efficiency of this monolithic converter is expected to be about 75%, so to provide 8 W of output power, an input power of 10.6 W is expected. The input operating voltage range is 90 to 265 Vac. The NCP1014 includes ON Semiconductor's dynamic self-supply (DSS) circuit, which simplifies startup by reducing component count. Thermal considerations of this integrated controller determine the maximum output power. Copper area on the board dissipates heat and cools it down. When the converter is operating, the bias winding on the flyback transformer turns off the DSS, reducing the power consumption of the converter. Lower operating temperatures allow more power to be delivered to the load.
1) Electromagnetic Interference (EMI) Filters
Switching regulators consume pulsed current from the input source. Requirements for harmonic content limit the high-frequency components of the power supply input current. Usually the filter consists of capacitors and inductors to attenuate undesirable signals. The capacitors connected to the input line conduct with a current that is 90° out of phase with the input voltage. This shifted current reduces the power factor by shifting the phase between the input voltage and current, so a balance needs to be struck between the need for filtering and maintaining a high power factor.
Based on the properties of electromagnetic interference and the complex characteristics of the filter components, capacitors C1 and C2 were initially selected as 100 nF capacitors. The differential inductor L1 was selected to provide an LC filter frequency of approximately 1/10 of the switching frequency. The inductor values used are:
In the actual design, a 2.7 mH inductor was chosen, which is a standard inductor value. Based on this starting point, the filter was adjusted empirically to meet the conducted interference limits. Capacitor C2 was increased to 220 nF to provide interference limit margin. Resistor R1 limits the inrush current and provides a fusible element in the event of a fault. Depending on the application environment, a fuse may be required to meet safety requirements. Note that the inrush current is smaller with a smaller total primary capacitance.
2) Primary clamp
Diode D5, capacitor C3, and resistor R2 form a clamping network that controls the voltage spike caused by the flyback transformer leakage inductance. D5 should be a fast recovery device rated to handle the peak input voltage and the output voltage reflected on the transformer primary. The MURA160 fast recovery diode with a 600 V current rating of 1 A is a suitable choice for D5. Capacitor C3 must absorb the leakage energy with only a minimal increase in voltage, and a capacitor of 1.5 nF is sufficient for this type of low power application. Resistor R3 must dissipate the leakage energy, but not necessarily at the expense of efficiency. This resistor was chosen empirically as 47 kΩ. Note that the rated voltage of this resistor and capacitor C3 is 125.5 V.
3) Bias Supply
Diode D6 rectifies the supply from the bias winding. The MMBD914 diode rated for 100 V at 200 mA is a suitable choice for D6. The primary bias is filtered by capacitor C4, resistor R3, and capacitor C5. C5 was chosen to be 2.2 µF, C4 to be 0.1 µF, and R3 to be 1.5 kΩ.
4) Output Rectifier
The output rectifier must withstand peak currents much higher than the 630 mA average output current. The maximum output voltage is 22 V, and the rectifier peak voltage is 93.2 V. The output rectifier selected is the 3 A, 200 V, 35 nS MURS320, which provides low forward voltage drop and fast switching time. The 2,000 µF capacitor limits the output ripple current to 25%, or 144 mA peak-to-peak.
5) Current Control
A constant current output is maintained by monitoring the voltage drop across a sense resistor, RSENSE, in series with the output. Resistor R11 connects the sense resistor to the base-emitter junction of a general-purpose PNP transistor, Q1. When the voltage drop across the sense resistor is approximately 0.6 V, the current through R11 biases Q1, turning it on. Q1 determines the current through the LED of optocoupler U2, which is limited by resistor R4. The transistor of optocoupler U2 provides feedback current to the NCP1014, controlling the output current.
Setting the output current Iout = 630 mA requires the sense resistor RSENSE = 0.85 Ω. The sense resistor consists of four parallel components R6, R7, R8 and R9. The resistance of R6 and R7 is selected to be 1.8 Ω, the resistance of R8 is selected to be 10 Ω, and R9 is left open, resulting in a total sense resistance of about 0.83 Ω.
6) Power Factor Control
Maintaining a high power factor in this circuit relies on a slow feedback response time that allows only a slight change in feedback level within a given input supply half cycle. For this current mode control device, the maximum peak current remains almost constant within the half cycle. This improves the power factor compared to a conventional feedback system. Capacitor C6 provides a slow loop response and suppresses the current from the internal 18 kΩ pull-up resistor of the NCP1014 and the feedback optocoupler transistor. From experience, capacitor C6 is determined to be in the range of 22 µF to 47 µF.
7) Transformer
The minimum input voltage required for this LED driver is 90 Vac, and the corresponding peak value is 126 Vac. Under the conditions of output power Po=8 W, efficiency (η)=0.75 and Vin=126 V, the calculated peak current Ipk=0.339 A. Using the switching frequency (fSW) value of 100 kHz, the primary inductance (Ip) is calculated to be 1858 µH. [page]
This power level is suitable for choosing an E16 core with a window area (Ac) of 0.2 cm2. The maximum flux density is set to 3 kG, and the number of primary turns (T) can be calculated to be 105. The output voltage is limited to 22 V for protection under open load events. In order to provide some output voltage margin and reduce the duty cycle, the output voltage value is increased by 50% to 33 V. The minimum number of secondary turns (Ns) will be about 20 turns.
The NCP1014 requires a minimum voltage of 8.1 V to keep the DSS function from being activated when the converter is operating. The minimum LED voltage is designed to be 12.5 V and the number of primary bias winding turns (Nb) is approximately 13 turns.
8) Open circuit protection
The Zener diode provides open circuit load protection. The open circuit voltage is determined by the sum of the diode D8 voltage, the resistor R4 voltage drop and the optocoupler LED voltage. The selected Zener diode D8 has a rated voltage of 18 V.
9) Leakage resistor and filter
Resistor R10 and capacitor C10 provide a small discharge path and filter the output noise.
10) Analog Dimming
This reference design includes an optional control section to implement analog current regulated dimming. For this purpose, components such as resistors R12, R14, R15, diode D9, transistor Q2 can be added and connected to potentiometer R13. The resistor R12 selected for this design has a resistance of 1 kΩ, the dimming potentiometer R13 is 10 kΩ, R14 is 820 Ω, and R15 is 1 kΩ.
11) Capacitor Life
One of the considerations for LED lighting is that the driver and LED should have comparable operating life. While there are many factors that affect power supply reliability, electrolytic capacitors are critical to the overall reliability of any electronic circuit. It is necessary to analyze the capacitors in this application and select the appropriate electrolytic capacitors to provide a long operating life. The usable life of an electrolytic capacitor is greatly affected by the ambient temperature and internal temperature rise. The capacitor selected for this reference design is Panasonic's ECA-1EM102, which is rated at 1000 µF, 25 V, 850 mA, 2,000 hours, and 85°C. Assuming an ambient temperature of 50°C, the usable life of this capacitor is over 120,000 hours.
Test results
The relevant test data is measured by the NCP1014LEDGTGEVB evaluation board under the conditions of 4 LEDs and an operating current of about 630 mA, unless otherwise stated. Figures 3 and 4 are the energy efficiency measurement data under different conditions. Figure 5 shows the power factor under different line voltage conditions. It should be noted that when the input voltage is in the range of 90 Vac to 135 Vac, the power factor is higher than 0.8, which is much higher than the power factor requirement of "Energy Star" LED residential lighting applications.
Summary:
The "Energy Star" standard provides quantitative requirements for solid-state lighting, which exposes LED drivers to some new requirements, such as power factor correction. This requires novel solutions to meet these requirements without increasing circuit complexity and cost. This article, combined with the optimized NCP1014LEDGTGEVB evaluation board, introduces the design background, solutions and design process of ON Semiconductor's offline 8 W LED driver reference design, and shares the relevant energy efficiency and power factor test results, showing that this reference design provides higher energy efficiency and meets the power factor requirements of the "Energy Star" solid-state lighting standard, which is very suitable for this type of low-power LED lighting application.
Previous article:Design of street lighting power saving control system with remote monitoring
Next article:AC-DC power supply architecture and LED backlight solutions for medium and large size LCD TVs
Recommended ReadingLatest update time:2024-11-16 16:19
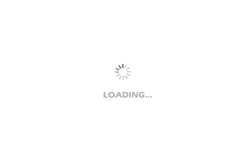
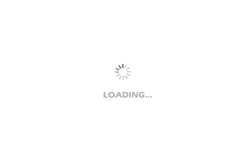
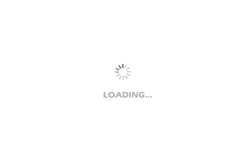
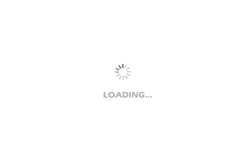
- Popular Resources
- Popular amplifiers
-
MCU C language programming and Proteus simulation technology (Xu Aijun)
-
100 Examples of Microcontroller C Language Applications (with CD-ROM, 3rd Edition) (Wang Huiliang, Wang Dongfeng, Dong Guanqiang)
-
Research on three-phase all-solid-state high-efficiency LED tunnel lighting system based on chip drive_Li Jian
-
Follow me Season 2 Episode 1 All Code + Library
- MathWorks and NXP Collaborate to Launch Model-Based Design Toolbox for Battery Management Systems
- STMicroelectronics' advanced galvanically isolated gate driver STGAP3S provides flexible protection for IGBTs and SiC MOSFETs
- New diaphragm-free solid-state lithium battery technology is launched: the distance between the positive and negative electrodes is less than 0.000001 meters
- [“Source” Observe the Autumn Series] Application and testing of the next generation of semiconductor gallium oxide device photodetectors
- 采用自主设计封装,绝缘电阻显著提高!ROHM开发出更高电压xEV系统的SiC肖特基势垒二极管
- Will GaN replace SiC? PI's disruptive 1700V InnoMux2 is here to demonstrate
- From Isolation to the Third and a Half Generation: Understanding Naxinwei's Gate Driver IC in One Article
- The appeal of 48 V technology: importance, benefits and key factors in system-level applications
- Important breakthrough in recycling of used lithium-ion batteries
- Innolux's intelligent steer-by-wire solution makes cars smarter and safer
- 8051 MCU - Parity Check
- How to efficiently balance the sensitivity of tactile sensing interfaces
- What should I do if the servo motor shakes? What causes the servo motor to shake quickly?
- 【Brushless Motor】Analysis of three-phase BLDC motor and sharing of two popular development boards
- Midea Industrial Technology's subsidiaries Clou Electronics and Hekang New Energy jointly appeared at the Munich Battery Energy Storage Exhibition and Solar Energy Exhibition
- Guoxin Sichen | Application of ferroelectric memory PB85RS2MC in power battery management, with a capacity of 2M
- Analysis of common faults of frequency converter
- In a head-on competition with Qualcomm, what kind of cockpit products has Intel come up with?
- Dalian Rongke's all-vanadium liquid flow battery energy storage equipment industrialization project has entered the sprint stage before production
- Allegro MicroSystems Introduces Advanced Magnetic and Inductive Position Sensing Solutions at Electronica 2024
- Car key in the left hand, liveness detection radar in the right hand, UWB is imperative for cars!
- After a decade of rapid development, domestic CIS has entered the market
- Aegis Dagger Battery + Thor EM-i Super Hybrid, Geely New Energy has thrown out two "king bombs"
- A brief discussion on functional safety - fault, error, and failure
- In the smart car 2.0 cycle, these core industry chains are facing major opportunities!
- The United States and Japan are developing new batteries. CATL faces challenges? How should China's new energy battery industry respond?
- Murata launches high-precision 6-axis inertial sensor for automobiles
- Ford patents pre-charge alarm to help save costs and respond to emergencies
- New real-time microcontroller system from Texas Instruments enables smarter processing in automotive and industrial applications