The hearing aid market is growing due to an aging population and a significant increase in hearing loss, but their conspicuous form factor and short battery life have turned off many people. As hearing loss becomes more common, people will seek smaller, more effective, and higher quality hearing aids. The front end of the hearing aid signal chain is the microphone, which detects speech and other ambient noise. Therefore, improving audio capture can improve the performance of the entire signal chain and reduce power consumption.
A microphone is a transducer that converts an acoustic signal into an electrical signal for processing by the hearing aid audio signal chain. There are many technologies for this acoustic-electrical conversion, but condenser microphones are the smallest and most accurate of the bunch. The diaphragm in a condenser microphone moves in response to the acoustic signal, and this movement causes a change in capacitance, which in turn generates an electrical signal.
The electret condenser microphone (ECM) is the most widely used technology in hearing aids. ECMs use a variable capacitor with one plate made of a material that has a permanent electrical charge. ECMs are well known in the hearing aid industry today, but the technology behind these devices has not changed much since the 1960s. Their performance, repeatability, and stability over temperature and other environmental conditions are not very good. Hearing aids and other applications where high performance and consistency are important have created an opportunity for the development of new microphone technologies. New technologies should improve on these shortcomings, allowing manufacturers to produce higher quality, more reliable devices.
Microelectromechanical systems (MEMS) technology is the backbone of the condenser microphone revolution. MEMS microphones take advantage of the great advances in silicon technology over the past few decades, including ultra-small manufacturing structures, excellent stability and repeatability, and low power consumption, all of which have become uncompromising requirements of the silicon industry. Until now, the power consumption and noise levels of MEMS microphones have been too high to be suitable for use in hearing aids, but new devices that meet these two key requirements have emerged and are setting off the next wave of innovation in hearing aid microphones.
How MEMS Microphones Work
Like ECMs, MEMS microphones are capacitive microphones. MEMS microphones consist of a flexibly suspended membrane that is free to move above a fixed backplate, all fabricated on a single silicon wafer. This structure forms a variable capacitor, with a fixed charge applied between the membrane and the backplate. Incoming sound pressure waves pass through holes in the backplate, causing the membrane to move in an amount proportional to the amplitude of the compression and rarefaction waves. This movement changes the distance between the membrane and the backplate, which in turn changes the capacitance, as shown in Figure 1. With the charge constant, this capacitance change is converted into an electrical signal.
Figure 1. The capacitance of a MEMS microphone varies with the amplitude of the sound wave.
The process of manufacturing microphone sensor elements on silicon wafers is similar to the manufacturing process of other integrated circuits (ICs). Unlike ECM manufacturing technology, silicon manufacturing processes are very precise and highly repeatable. Not only will all MEMS microphone elements manufactured on a wafer have the same performance, but each element on different wafers will also have the same performance over the multi-year life cycle of the product.
Silicon manufacturing is a series of deposition and etching processes in a tightly controlled environment that produces a collection of metal and polysilicon shapes to form a MEMS microphone. The geometries involved in producing MEMS microphones are on the micrometer (μm) scale. The holes in the backplate through which the sound waves pass can be less than 10 μm in diameter, and the film thickness can be around 1 μm. The gap between the film and the backplate is only a few microns. Figure 2 shows an SEM image of a typical MEMS microphone sensor element, viewed from the top (film). Figure 3 shows a cross-section of the middle of the microphone element. In this design, sound waves enter the microphone through a cavity at the bottom of the element and pass through the backplate holes to excite the film.
Figure 2. SEM image of a MEMS microphone.
Figure 3. Cross section of a MEMS microphone.
Because the geometry is tightly controlled during the manufacturing process, the measured performance of different microphones is highly repeatable. Another advantage of using MEMS technology to build microphones is that the membrane is extremely small and therefore has very low mass, making MEMS microphones less susceptible to vibrations than ECMs, which have a much larger membrane mass.
Development, reproducibility and stability
MEMS microphones have been developed to a high level and have become the default choice for many audio capture applications that require small size and high performance, but most commercial-grade microphones are not suitable for the hearing aid industry, which requires much smaller devices, lower power consumption, better noise performance, and higher reliability, environmental stability, and device-to-device repeatability. MEMS microphone technology is now able to meet all of the above requirements: ultra-small packaging, very low power consumption, and very low equivalent input noise.
The tight control measures of the silicon manufacturing process make the stability and device-to-device performance variation of MEMS microphones significantly better than that of ECMs. Figure 4 shows the normalized frequency response of several MEMS microphones of the same model, and Figure 5 shows the normalized frequency response of different ECMs. The frequency response of each MEMS microphone is almost identical, while the frequency response of the ECM shows considerable device-to-device variation, especially at high and low frequencies.
Figure 4. Frequency responses of several MEMS microphones.
Figure 5. Frequency responses of three ECM microphones.
MEMS microphones also exhibit excellent stability over a wide temperature range. Figure 6 shows the change in sensitivity as the ambient temperature changes from -40°C to +85°C. The black line shows that the sensitivity changes by less than 0.5 dB over the temperature range of the MEMS microphone, while the ECM shows a maximum change of 8 dB.
Figure 6. Sensitivity to vibration vs. temperature: MEMS and ECM
Compared to ECM, the power supply rejection performance of MEMS microphone design is significantly improved, with a typical power supply rejection ratio (PSRR) better than -50 dB. On ECM, the output signal and bias voltage (power supply) share a pin, and any ripple on the power supply will appear directly on the output signal. The excellent PSRR of MEMS microphones provides a degree of freedom for audio circuit design that ECM cannot match. The number of components and system cost are reduced.
In tiny, battery-powered applications like hearing aids, every milliwatt of power consumption counts. When the hearing aid is operating, the microphone cannot save power by cycling its power. Therefore, the operating power consumption of the microphone is extremely important. A typical ECM microphone used in a hearing aid consumes 35 μA when powered by a typical zinc-air battery voltage (0.9 V-1.4 V). At the same voltage, a MEMS microphone used in a hearing aid can consume half the power, allowing the hearing aid to last longer on a single battery charge.
The latest generation of MEMS microphones has the excellent noise and power performance required by the hearing aid industry. Analog Devices has leveraged more than 20 years of experience in MEMS technology to create high performance microphones for the hearing aid market. The equivalent input noise (EIN) specification of a typical omnidirectional MEMS microphone is 27.5 dB SPL (A-weighted, 8 kHz bandwidth), which is suitable for hearing aid applications. The 1/3 octave EIN noise performance is typically used to specify hearing aid microphones and is very good at low frequencies, as shown in Figure 7. This high noise performance is achieved with only 17 μA of power consumption (at a typical hearing aid battery voltage). The microphone is available in a tiny package with a total volume of less than 7.5 mm3, as shown in Figure 8.
Figure 7. 1/3-octave noise of a MEMS microphone.
Figure 8. Omnidirectional MEMS microphone for hearing aids a) Bottom view; b) Top view; c) Top view of package for easy hand soldering
in conclusion
New high-performance, low-power MEMS microphones are proving to be the next generation of microphone technology for hearing aids. MEMS microphones are competitive with many hearing aid ECMs in performance and exceed ECM technology in many areas, such as repeatability, stability, size, manufacturability, and power consumption. MEMS microphones are the future of hearing aids, and the future is already here.
Previous article:Wireless coupling test using CPL antenna as W-Fi device
Next article:The "Secret" of RF Receiver Chip Structure
Recommended ReadingLatest update time:2024-11-16 08:36
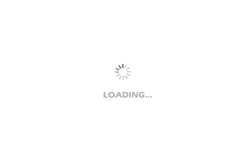
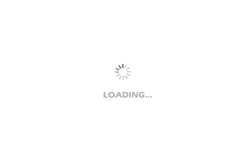
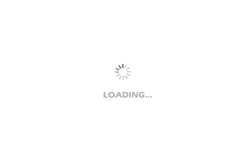
- MathWorks and NXP Collaborate to Launch Model-Based Design Toolbox for Battery Management Systems
- STMicroelectronics' advanced galvanically isolated gate driver STGAP3S provides flexible protection for IGBTs and SiC MOSFETs
- New diaphragm-free solid-state lithium battery technology is launched: the distance between the positive and negative electrodes is less than 0.000001 meters
- [“Source” Observe the Autumn Series] Application and testing of the next generation of semiconductor gallium oxide device photodetectors
- 采用自主设计封装,绝缘电阻显著提高!ROHM开发出更高电压xEV系统的SiC肖特基势垒二极管
- Will GaN replace SiC? PI's disruptive 1700V InnoMux2 is here to demonstrate
- From Isolation to the Third and a Half Generation: Understanding Naxinwei's Gate Driver IC in One Article
- The appeal of 48 V technology: importance, benefits and key factors in system-level applications
- Important breakthrough in recycling of used lithium-ion batteries
- Innolux's intelligent steer-by-wire solution makes cars smarter and safer
- 8051 MCU - Parity Check
- How to efficiently balance the sensitivity of tactile sensing interfaces
- What should I do if the servo motor shakes? What causes the servo motor to shake quickly?
- 【Brushless Motor】Analysis of three-phase BLDC motor and sharing of two popular development boards
- Midea Industrial Technology's subsidiaries Clou Electronics and Hekang New Energy jointly appeared at the Munich Battery Energy Storage Exhibition and Solar Energy Exhibition
- Guoxin Sichen | Application of ferroelectric memory PB85RS2MC in power battery management, with a capacity of 2M
- Analysis of common faults of frequency converter
- In a head-on competition with Qualcomm, what kind of cockpit products has Intel come up with?
- Dalian Rongke's all-vanadium liquid flow battery energy storage equipment industrialization project has entered the sprint stage before production
- Allegro MicroSystems Introduces Advanced Magnetic and Inductive Position Sensing Solutions at Electronica 2024
- Car key in the left hand, liveness detection radar in the right hand, UWB is imperative for cars!
- After a decade of rapid development, domestic CIS has entered the market
- Aegis Dagger Battery + Thor EM-i Super Hybrid, Geely New Energy has thrown out two "king bombs"
- A brief discussion on functional safety - fault, error, and failure
- In the smart car 2.0 cycle, these core industry chains are facing major opportunities!
- The United States and Japan are developing new batteries. CATL faces challenges? How should China's new energy battery industry respond?
- Murata launches high-precision 6-axis inertial sensor for automobiles
- Ford patents pre-charge alarm to help save costs and respond to emergencies
- New real-time microcontroller system from Texas Instruments enables smarter processing in automotive and industrial applications
- [Zhongke Bluexun AB32VG1 RISC-V board "run into" RTT evaluation] ADC
- dxp
- How to timestamp ZigBee mac layer data
- Unboxing
- Tmall Genie controls ESP8266 to light up LED lights
- I am a novice learning ESP8266 infrared remote control. I have searched around for micropython and it seems that there is no library related to infrared transceiver. Does anyone know...
- Recommended high voltage mosfet models
- Single-cell lithium battery fuel gauge
- CS5090 5V USB input charges 2 lithium batteries, with path management application, which can realize the function of "charging and discharging at the same time".
- Free review: National Technology low power series, N32L43x is now available for testing