1 Introduction
Inverter power supplies generally use instantaneous feedback control technology to improve the dynamic response speed of inverter power supplies, reduce the harmonic content of output voltage, and improve the quality of output voltage waveform. Common inverter power supply control technologies include repetitive control, harmonic compensation control, deadbeat control, voltage instantaneous value control, and voltage instantaneous value control with current inner loop. Among them, the dual-loop control method with voltage instantaneous value loop with current inner loop has gradually become one of the development directions of high-performance inverter power supplies due to its simple implementation, superior system dynamic performance, and strong adaptability to loads . However, the traditional control method is based on the assumption that the DC side input voltage of the inverter power supply is a pulsating DC voltage, while the actual inverter power supply has the phenomenon of DC side voltage fluctuations due to grid voltage fluctuations or load mutations. DC input voltage fluctuations will cause the inverter open-loop gain to fluctuate, thereby affecting the output voltage quality. On the basis of traditional dual-loop control, the three-loop control strategy with an output voltage effective value feedback loop is added to eliminate the output voltage steady-state error caused by DC input voltage fluctuations to a certain extent, but the effective value loop has a slow response speed to output voltage changes and a complex control process.
In addition, when the sine pulse width modulation inverter power switch tube works in the hard switching state, a large number of high-order harmonics will be generated, which will increase the loss of the converter and the load, reduce the service life of the equipment, and may even cause parallel or series resonance, damage electrical equipment and interfere with the normal operation of communication lines. Soft switching technology is one of the effective methods to overcome the above defects. The use of HPWM modulation can realize ZVS soft switching technology. Without adding hardware and changing the converter topology, the parasitic parameters of existing components and switch tubes can be used to create ZVS soft switching conditions for the inverter bridge switch tube, thereby maximizing ZVS.
In view of the phenomenon that the output voltage waveform of the dual-loop control inverter power supply is distorted and the amplitude changes when the DC side voltage is disturbed, this paper proposes a three-loop control method that corrects the amplitude of the reference sinusoidal signal through the input voltage feedforward control loop to improve the output voltage quality of the inverter power supply. At the same time, with the help of the powerful computing power and rich peripherals of DSP, the digital control of the HPWM inverter power supply is realized, thereby simplifying the hardware circuit. The simulation results show that the control strategy proposed in this paper is simple and practical, which can effectively improve the dynamic performance and steady-state accuracy of the inverter power supply under DC input voltage disturbance, and reduce the total harmonics of the output voltage.
2 Inverter Power System Modeling
The main circuit structure of the single-phase full-bridge inverter power supply is shown in Figure 1. The DC input voltage Ud is converted into a pulse output voltage Ui after passing through the inverter bridge, and then a sinusoidal output voltage Uo is obtained after LC filtering.
From the average value model of the inverter bridge, it can be seen that when the triangular carrier frequency fc is much higher than the output sine wave fundamental frequency f, the average value of the inverter bridge output voltage Ui in a carrier cycle Tc can be approximately regarded as the instantaneous value Ui1 of the output voltage fundamental component, that is,
Where: Ud is the DC input voltage; UCm is the triangular carrier amplitude. Let kPWM = Ud/UCm represent the gain of the sinusoidal modulated signal passing through the inverter bridge, and the change of kPWM caused by the change of Ud is defined as the interference variable. The dual-loop control system based on the voltage instantaneous value outer loop and the capacitor current inner loop is shown in Figure 2. The voltage instantaneous value outer loop adopts PI regulation, and the capacitor current inner loop adopts P regulation. The switching frequency is 20kHz. According to the corner frequency ωn1 = ωc/10 and the damping coefficient ξ = 0.3, the output filter parameters [3] are: L = 670μH, C = 47μF. The simulation parameters of the controller are: Kv = 0.0015, Ki = 0.05, kvp = 0.098, kvi = 350, kip = 20.
Figure 2 Inverter power dual-loop control block diagram
Considering the transient response performance of the inverter power supply to the input voltage disturbance, let Uref=0,io=Uo/R, then the transfer function of the output voltage Uo to the DC voltage disturbance Δu can be obtained:
From formula (2), it can be seen that the adjustment time Ts of the system to the DC input voltage step response is 5ms. Therefore, when the inverter power supply output voltage frequency is 400Hz, the system adjustment time lasts for two sine cycles, but because the response peak is small, it will not have a significant impact on the output voltage waveform. When the inverter power supply output voltage frequency is 50Hz, the response peak appears in 1/4 of the sine cycle, causing the output voltage waveform to be distorted.
3 DC voltage feedforward control principle
From the above analysis, it can be seen that the dual-loop feedback control inverter has a certain hysteresis and steady-state error in regulating the changes in the DC input voltage. To this end, this paper proposes to use the input voltage feedforward loop to detect the DC input voltage in real time, compensate the inverter bridge gain kPWM, and offset the impact of the DC input voltage Ud fluctuation on the inverter power supply. Therefore, in the traditional dual-loop control system, the rated DC input voltage U*d is divided by the sampled DC input voltage Ud, and then multiplied by the dual-loop corrected sinusoidal signal ugm to obtain the modulation signal u′gm, which is sent to the PWM generator, as shown in Figure 3.
Figure 3 Schematic diagram of DC voltage feedforward control of inverter power supply
Substituting the modulation signal ugm(t)=U′gmsinωt into (1), we can obtain:
Among them: m′=U′gm/UCm is the modulation ratio after compensation. In order to ensure the utilization rate of DC voltage, the system needs to maintain a very high modulation index, that is, m is close to 1, that is, Ugm is close to UCm.
4 HPWM modulation principle
The hybrid pulse width modulation (HPWM) method is essentially a unipolar SPWM modulation method. It switches every half output voltage cycle during operation. That is, the switch tube of the same bridge arm works at a low frequency in the first half of the power frequency cycle, and works at a high frequency in the second half of the power frequency cycle. This overcomes the defect of the traditional unipolar control method that the switch tube of one bridge arm always works at a high frequency at the same time, thereby improving the service life of the switch tube and the system reliability.
The output voltage of the inverter power supply working in the HPWM soft switching mode has 12 working states in one switching cycle. Based on the symmetry of the working states of the positive and negative half-cycles of the output voltage, taking the positive half-cycle of the output voltage as an example, the six working modes of the single-phase full-bridge inverter power supply in one switching cycle are analyzed, as shown in Figure 4.
Figure 4 HPWM inverter power supply working mode diagram
From t0 to t1, the inverter works in mode A. Switches S1 and S4 are turned on, the circuit is in positive voltage output mode, and the filter inductor current increases linearly until S1 is turned off at t1.
From t1 to t2, the inverter works in mode B. At t1, S1 is turned off, and the filter inductor current is transferred from S1 to the C1 and C3 branches, charging C1 while discharging C3. Due to the existence of C1 and C3, S1 works in a zero voltage off state. Since this state lasts for a very short time, it can be considered that the filter inductor current is approximately unchanged and is equivalent to a constant current source. Then the voltage across C1 rises linearly, and the voltage across C3 drops linearly. At t2, the voltage of C3 drops to zero, the body diode D3 of S3 is naturally turned on, and the circuit mode B ends.
From t2 to t3, the inverter works in mode C. After D3 is turned on, S3 is turned on, so S3 is turned on with zero voltage. At this time, the current is transferred from D3 to S3, and S3 works in the synchronous rectification state. The current flows through S3, making the circuit in a zero-state freewheeling state, and the inductor current decreases linearly until it decreases to zero at t3. During this period, to ensure that S3 achieves ZVS, a dead time tdead1 is required between S1 turning off and S3 turning on, and the following requirements are met:
From t3 to t4, the inverter works in mode D. In this mode, the voltage across the filter inductor Lf is -U0, the inductor current starts to increase from zero to the negative direction, the circuit is in a zero-state energy storage state, and the current in S3 also increases from zero to the positive direction. At t4, S3 is turned off, ending the D mode.
From t4 to t5, the inverter works in mode E. This mode is similar to mode A. S3 is turned off, C3 is charged and C1 is discharged. Similarly, S3 is turned off at zero voltage. At t5, the voltage of C1 drops to zero, and the diode D1 is naturally turned on, entering the next circuit mode F.
From t5 to t6, after D1 is turned on, S1 is turned on at zero voltage. The current is transferred from D1 to S1, S1 works in the synchronous rectification state, the circuit is in the positive voltage output state feedback mode, and the inductor current decreases negatively until it decreases to zero. After that, the input voltage is output positively to the inductor energy storage, returning to the initial mode A, and starting the next switching cycle. Similarly, to ensure that S1 is turned on at zero voltage, a dead time tdead2 is required between S3 turning off and S1 turning on, and at the same time: tdead2>2CeffUd/I0. It should be noted that I1>I0 is generally the case, so tdead2>tdead1 is obtained.
5 Analysis of simulation results
The inverter power supply circuit designed in this paper was simulated and verified using Matlab/Simulink, and an experimental prototype was developed using the above principle to verify the feasibility of the scheme. The parameters are as follows: DC input voltage Ud is 400V±20%, rated output voltage Uo amplitude is 310V, output power is 1kVA, triangular modulation wave frequency is 10kHz, amplitude is 1V, modulation ratio is 0.8, THD.
Figure 10 shows the output voltage waveforms of the traditional dual-loop control inverter and the inverter studied in this paper when the output is 50Hz AC and Ud fluctuates. As can be seen from Figure 10, the traditional dual-loop control causes the output voltage waveform to be distorted due to the slow adjustment of the controller, while the output voltage waveform of the inverter studied in this paper remains good, which significantly improves the system's transient response performance to DC input voltage disturbances.
(a)
(b)
Figure 5 Output voltage waveform after DC voltage fluctuation: (a) Traditional dual-loop control; (b) Feedforward voltage control
The driving waveforms of switch tube 1 and switch tube 4 measured in the experiment are shown in Figure 6. It can be seen from the figure that the switch tube works in HPWM modulation mode.
The output voltage waveform under resistive half load is shown in Figure 7, and the output voltage waveform under resistive full load is shown in Figure 8. It can be seen from Figures 7 and 8 that when the load changes from half load to full load, the distortion of the output voltage is small, the amplitude of the output voltage does not change much, and the system has a good voltage regulation output.
Figure 7 Output voltage waveform under resistive half load
Figure 8 Output voltage waveform under resistive full load
6 Conclusion
Based on an in-depth analysis of the response performance of the traditional dual-loop control inverter to the DC input voltage disturbance, this paper proposes to use the input voltage feedforward control loop to eliminate the impact of the DC input voltage fluctuation on the inverter performance . This paper uses the powerful function of the DSP chip to realize the design of the digital HPWM inverter. The HPWM control method uses the asymmetric regular sampling method to effectively suppress the harmonic components of the system; at the same time, the four switch tubes realize soft switching control, which reduces the switching loss and improves the circuit efficiency. The simulation experimental results show that the inverter with the input voltage feedforward compensation loop has good static and dynamic performance for the DC input voltage disturbance.
Previous article:Analysis of the main methods and advantages and disadvantages of power supply heat dissipation
Next article:Manage energy consumption through load and input detection mechanisms integrated in the driver IC
Recommended ReadingLatest update time:2024-11-23 13:44
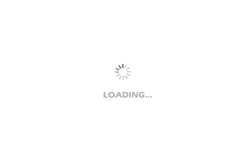
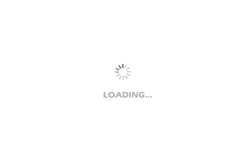
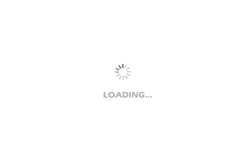
- Popular Resources
- Popular amplifiers
-
100 Examples of Microcontroller C Language Applications (with CD-ROM, 3rd Edition) (Wang Huiliang, Wang Dongfeng, Dong Guanqiang)
-
Theory and practice of small-size MOS device models for VLSI simulation
-
Power Electronics Technology 3rd Edition (Edited by He Yikang and Pan Zaiping)
-
Power electronics and motor control RTDS simulation (edited by Liu Guangchen and Tian Guizhen)
- RAQ #223: How to measure and determine soft-start timing without a soft-start equation?
- Vicor high-performance power modules enable the development of low-altitude avionics and EVTOL
- Bourns Launches Two Thick Film Resistor Series with High Power Dissipation Capabilities in Compact TO-220 and DPAK Package Designs
- Bourns Launches New High-Pulse Brake Resistor Series with Superior Energy Dissipation Capabilities
- Nexperia launches new 120 V/4 A half-bridge gate driver to further improve robustness and efficiency in industrial and automotive applications
- Vishay's New 150 V MOSFETs Offer Industry-Leading Power Loss Performance
- The first generation of SGT MOSFET series from Qiangmao: innovative trench technology, automotive-grade 60 VN channel, breakthrough in high-efficiency performance of automotive electronics
- DC/DC Power Supplies for Automotive Applications
- MathWorks and NXP Collaborate to Launch Model-Based Design Toolbox for Battery Management Systems
- Intel promotes AI with multi-dimensional efforts in technology, application, and ecology
- ChinaJoy Qualcomm Snapdragon Theme Pavilion takes you to experience the new changes in digital entertainment in the 5G era
- Infineon's latest generation IGBT technology platform enables precise control of speed and position
- Two test methods for LED lighting life
- Don't Let Lightning Induced Surges Scare You
- Application of brushless motor controller ML4425/4426
- Easy identification of LED power supply quality
- World's first integrated photovoltaic solar system completed in Israel
- Sliding window mean filter for avr microcontroller AD conversion
- What does call mean in the detailed explanation of ABB robot programming instructions?
- STMicroelectronics discloses its 2027-2028 financial model and path to achieve its 2030 goals
- 2024 China Automotive Charging and Battery Swapping Ecosystem Conference held in Taiyuan
- State-owned enterprises team up to invest in solid-state battery giant
- The evolution of electronic and electrical architecture is accelerating
- The first! National Automotive Chip Quality Inspection Center established
- BYD releases self-developed automotive chip using 4nm process, with a running score of up to 1.15 million
- GEODNET launches GEO-PULSE, a car GPS navigation device
- Should Chinese car companies develop their own high-computing chips?
- Infineon and Siemens combine embedded automotive software platform with microcontrollers to provide the necessary functions for next-generation SDVs
- Continental launches invisible biometric sensor display to monitor passengers' vital signs
- What does it mean if there is MTX-M1 E196960 on the PCB?
- Recruiting weekend part-time CAN bus lecturer
- TI Linear Chargers & Portable Medical Devices
- CC4014------8-bit shift register
- [Compilation Learning] Let's make progress together! [Download]
- Hiring embedded hardware engineers
- I would like to ask about the problem of packaging multiple sensor data into one data
- Current transformer
- CAN waveform
- PowerPCB Tutorial Condensed Version