introduce
Many industrial applications, such as semiconductor wafer inspection systems, organic light-emitting diode flat panel display production and inspection, require extremely high motion performance, maintaining sub-nanometer static jitter and tracking errors in slow, uniform nano-motion. Linear servo drives have been used to meet these needs. This type of drive provides amazing performance and can achieve the linearity required by these applications. However, linear servo drives are inefficient, have high heat losses, and are large and bulky. The new generation of 450mm semiconductors is much larger than the current 300mm semiconductors, and such systems require drives with higher capabilities, higher voltages and currents. This requires linear drives to be very large and have limited energy, which limits the performance and throughput of this system, increases system cost, and reduces system reliability.
NanoPWM is a linearization of switching PWM drives based on a unique patented technology.
PWMBoost developed by ACS in the past five years can meet the needs of such positioning systems. NanoPWM drives provide better positioning and following performance, and overcome the shortcomings of linear drives. NanoPWM is very compact, has higher efficiency and reliability, can provide higher energy, current and power, and is more economical.
Types of servo drives
There are two main types of servo drives: linear drives and switching PWM drives.
Figure 1 depicts a block diagram of a linear drive. The drive works like a variable resistor, adjusting the current based on the current demand and load impedance. The supply voltage is split between the motor and the drive. When the motor is required to provide high torque at low speed, the current is high, the voltage applied to the motor is low, and the voltage applied to the drive is high. At this time, the losses in the drive are high.
Figure 1 Schematic description of a linear actuator
Figure 2 depicts the block diagram of the switching PWM drive. The driver operates as an on-off switch. The motor operates as an integrated circuit with an average current. The average current is a linear function of the switch duty cycle. At any given moment, the switch is either off (no current flows through the switch) or on (low voltage is applied to the switch). Therefore, the switching losses are very low.
Figure 2 - Schematic description of a PWM driver
.
Table 1. Summary of the advantages and disadvantages of various types of drives
Table 1 - Advantages and disadvantages of various drivers
need
Table 3 - Semiconductor Wafer Blueprint
Semiconductor wafer inspection systems require sub-nanometer standstill errors and nanometer tracking errors. Today, most systems are designed to handle 300mm diameter wafers. The next generation of wafers will have a diameter of 450mm. This requires the same or better position control performance, and due to the larger size and weight, we need larger motors and drives to maintain and increase the throughput of the system. Such systems require drives that have the advantages of linear drives and PWM drives. NanoPWMTM is such a drive. It is very efficient, can achieve high voltage operation, and provide high current. It is compact and has lower cost.
Figures 4 and 5 introduce the main features of NaonPWM.
lowEM noise: low electromagnetic noise
good performance: good performance
High efficiency: High efficiency
Compact size: compact structure
Very reliable: Very reliable
Affordable price: acceptable price
Regular performance: General performance
High EM noise: High electromagnetic noise
Complex design: Complex design
Poor reliability: Poor reliability
Low efficiency: Low efficiency
Expensive: Expensive
Figure 4-NanoPWM combines the advantages of linear drivers and PWM drivers
Figure 5 - Size comparison of linear and PWM drivers of the same power
Performance Comparison
The test system includes a linear stage driven by a non-intimate linear motor, a crossed ball bearing mechanism and a magnascale laser analog SIN-COS encoder with a basic resolution of 0.4 mico-meter. The motion control system includes an ACS MC4U control module and three different drives
• NanoPWM
• Standard PWM standard PWM driver
• Standalone linear drive
In each test, the driver and algorithm were tuned to achieve optimal performance and similar bandwidth.
As described in Table 2, the drivers have the same characteristics
Table 2 – Main performance indicators of the drive
The following performance indicators were tested:
Stillness jitter
Low speed following error
Static Error—NanoPWM vs Linear Driver
The test results are in Table 6 and summarized in Table 3
Table 6 – NanoPWM (red) vs. linear driver (yellow) static jitter
Table 3 - NanoPWM (red) vs. Linear Driver (yellow) Static Jitter
The static jitter is significantly reduced when using NanoPWM drivers than when using linear drivers (4.5 times smaller: 0.8nm Vr 3.6nm)
Low speed following error - NanoPWM vs linear drive.
The following error was measured at a speed of 1 mm/s. The test results are shown in Figure 7 and summarized in Table 4.
Figure 7. Following error of NanoPWM driver (red) vs. linear driver (yellow)
NanoPWM Linear Drivers
Table 4 - NanoPWM (red) VS Linear Actuator (yellow) Following Error
The following error is significantly reduced when using the NanoPWM driver, resulting in a smoother motion trajectory, which is very important during wafer inspection.
Static Error - NanoPWM vs. Standard PWM Drivers
The test results are shown in Figure 8 and summarized in Table 5.
Figure 8 - NanoPWM (red) vs PWM (yellow) static jitter
Table 5 - NanoPWM (red) VS PWM drive (yellow) static jitter
The static error of using NanoPWM driver is two orders of magnitude smaller than that of using standard PWM driver. Flat panel display processing system is relatively large, and the requirements for motor voltage and current exceed the allowable capacity of currently commercialized linear motors. Organic LED display requires higher precision, tracking accuracy and static jitter, which must be within the error range of several nanometers. NanoPWM provides a solution to such needs.
Summarize
This article introduces a new type of linear switching servo drive - NanoPWM, which has all the advantages of linear drives and PWM drives. The motion performance obtained by using NanoPWM drives exceeds that of currently commercialized linear servo drives. This drive is smaller, more reliable and cheaper.
This drive can meet the needs of higher motion performance and is suitable for semiconductor wafer inspection and flat panel display manufacturing systems.
Previous article:Design of practical signal source based on DDS technology (Part 2)
Next article:Integrated Power Management Unit Simplifies FPGA-Based Systems
Recommended ReadingLatest update time:2024-11-16 03:29
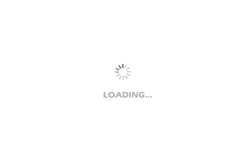
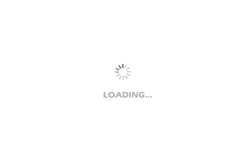
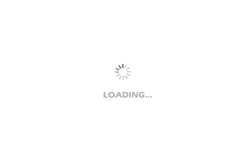
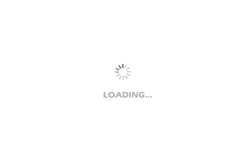
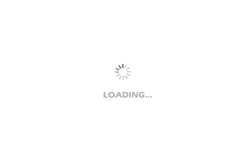
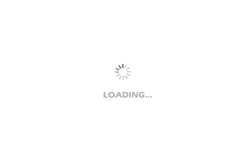
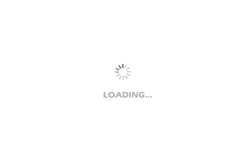
- Popular Resources
- Popular amplifiers
-
Siemens Motion Control Technology and Engineering Applications (Tongxue, edited by Wu Xiaojun)
-
Modern Product Design Guide
-
Modern arc welding power supply and its control
-
Small AC Servo Motor Control Circuit Design (by Masaru Ishijima; translated by Xue Liang and Zhu Jianjun, by Masaru Ishijima, Xue Liang, and Zhu Jianjun)
- MathWorks and NXP Collaborate to Launch Model-Based Design Toolbox for Battery Management Systems
- STMicroelectronics' advanced galvanically isolated gate driver STGAP3S provides flexible protection for IGBTs and SiC MOSFETs
- New diaphragm-free solid-state lithium battery technology is launched: the distance between the positive and negative electrodes is less than 0.000001 meters
- [“Source” Observe the Autumn Series] Application and testing of the next generation of semiconductor gallium oxide device photodetectors
- 采用自主设计封装,绝缘电阻显著提高!ROHM开发出更高电压xEV系统的SiC肖特基势垒二极管
- Will GaN replace SiC? PI's disruptive 1700V InnoMux2 is here to demonstrate
- From Isolation to the Third and a Half Generation: Understanding Naxinwei's Gate Driver IC in One Article
- The appeal of 48 V technology: importance, benefits and key factors in system-level applications
- Important breakthrough in recycling of used lithium-ion batteries
- LED chemical incompatibility test to see which chemicals LEDs can be used with
- Application of ARM9 hardware coprocessor on WinCE embedded motherboard
- What are the key points for selecting rotor flowmeter?
- LM317 high power charger circuit
- A brief analysis of Embest's application and development of embedded medical devices
- Single-phase RC protection circuit
- stm32 PVD programmable voltage monitor
- Introduction and measurement of edge trigger and level trigger of 51 single chip microcomputer
- Improved design of Linux system software shell protection technology
- What to do if the ABB robot protection device stops
- Allegro MicroSystems Introduces Advanced Magnetic and Inductive Position Sensing Solutions at Electronica 2024
- Car key in the left hand, liveness detection radar in the right hand, UWB is imperative for cars!
- After a decade of rapid development, domestic CIS has entered the market
- Aegis Dagger Battery + Thor EM-i Super Hybrid, Geely New Energy has thrown out two "king bombs"
- A brief discussion on functional safety - fault, error, and failure
- In the smart car 2.0 cycle, these core industry chains are facing major opportunities!
- The United States and Japan are developing new batteries. CATL faces challenges? How should China's new energy battery industry respond?
- Murata launches high-precision 6-axis inertial sensor for automobiles
- Ford patents pre-charge alarm to help save costs and respond to emergencies
- New real-time microcontroller system from Texas Instruments enables smarter processing in automotive and industrial applications
- RXD outputs a high level, how can we make it output a low level to turn on Q2?
- GaN Amplifiers - Gallium Nitride Technology
- Is this the price you paid for the CC3220SF board you have?
- The upcoming Circuit Playground Bluefruit
- C5000 Low Power DSP – Tools and Software
- Measuring a signal with an oscilloscope (first time using an oscilloscope)
- [GigaDevice GD32F310 Review] + UART Application
- Designing efficient, powerful, and fast electric vehicle charging stations
- 《GitHub Introduction and Practice》
- EEWorld invites you to disassemble (Issue 7) - Disassemble the weight loss tool and see what is inside the skipping rope