LED has been rapidly applied in various industries in recent years due to its many advantages such as environmental protection, long life and high photoelectric efficiency. The driving power supply of LED has become a hot topic. In theory, the service life of LED is more than 100,000 hours, but in actual application, LED is easily damaged due to improper design of the driving power supply and improper selection of driving mode.
Picture from the Internet
When designing an LED driver power supply , it is necessary to know the LED current and voltage characteristics. Due to different LED manufacturers and LED specifications, the current and voltage characteristics are different. Taking the typical specifications of white light LED as an example, according to the current and voltage change law of LED, the general application forward voltage is about 3.0-3.6V, the typical voltage is 3.3V, and the current is 20mA. When the forward voltage applied to both ends of the LED exceeds 3.6V, a small increase in the forward voltage may double the forward current of the LED, causing the temperature of the LED light source to rise too fast, thereby accelerating the LED light attenuation, shortening the life of the LED, and even burning the LED in severe cases. According to the voltage and current change characteristics of the LED, strict requirements are put forward for the design of the driver power supply.
At present, many manufacturers produce LED lighting products (such as guardrails, lamp cups, and projection lamps) that use resistors and capacitors to reduce voltage, and then add a voltage regulator diode to stabilize the voltage to supply power to the LED. This way of driving LEDs has great defects. First, the efficiency is low, and a large amount of power is consumed on the voltage-reducing resistor, which may even exceed the power consumed by the LED, and it is impossible to provide high-current drive, because the larger the current, the greater the power consumed on the voltage-reducing resistor. Therefore, many products do not dare to use the parallel connection method for LEDs, and all use the series connection method to reduce the current. Secondly, the ability to stabilize voltage is extremely poor, and it is impossible to ensure that the current passing through the LED does not exceed its normal working requirements. When designing products, the voltage at both ends of the LED is reduced to power the drive, which is at the cost of reducing the brightness of the LED. When driving LEDs using the resistor and capacitor voltage-reducing method, the brightness of the LED cannot be stable. When the power supply voltage is low, the brightness of the LED becomes dim, and when the power supply voltage is high, the brightness of the LED becomes brighter. The biggest advantage of driving LEDs using the resistor and capacitor voltage-reducing method is low cost.
According to the characteristics of LED current and voltage changes, it is feasible to use constant voltage to drive LED. Although the commonly used voltage stabilization circuit has the disadvantages of insufficient voltage stabilization accuracy and poor current stabilization ability, it may be overly precisely designed in some product applications. Its advantages are still irreplaceable by other driving methods.
Constant current driving is an ideal LED driving method, which can avoid the current fluctuation caused by the change of LED forward voltage, and the constant current makes the LED brightness stable. Therefore, many manufacturers choose constant current driving LED. There is another LED driving method that is feasible, which is neither constant voltage nor constant current, but through the design of the circuit, when the LED forward voltage increases, the driving current is reduced, ensuring the safety of LED products. Of course, the increase of forward voltage can only be within the tolerance range of LED, and too high will also damage the LED.
The ideal LED driving method is to use constant voltage and constant current. However, the cost of the driver increases. In fact, each driving method has its advantages and disadvantages. According to the requirements and application scenarios of LED products, it is critical to reasonably select the LED driving method and accurately design the driving power supply.
Previous article:Brief Analysis of LED Driving Power Supply
Next article:It's not easy — but the benefits of automotive LEDs outweigh the risks
Recommended ReadingLatest update time:2024-11-16 16:48
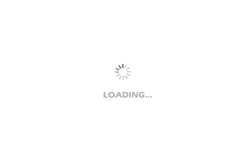
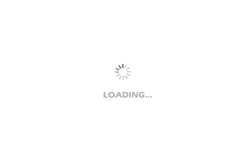
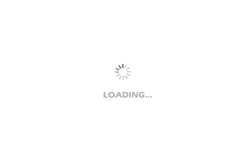
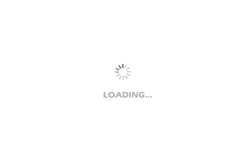
- Popular Resources
- Popular amplifiers
- MathWorks and NXP Collaborate to Launch Model-Based Design Toolbox for Battery Management Systems
- STMicroelectronics' advanced galvanically isolated gate driver STGAP3S provides flexible protection for IGBTs and SiC MOSFETs
- New diaphragm-free solid-state lithium battery technology is launched: the distance between the positive and negative electrodes is less than 0.000001 meters
- [“Source” Observe the Autumn Series] Application and testing of the next generation of semiconductor gallium oxide device photodetectors
- 采用自主设计封装,绝缘电阻显著提高!ROHM开发出更高电压xEV系统的SiC肖特基势垒二极管
- Will GaN replace SiC? PI's disruptive 1700V InnoMux2 is here to demonstrate
- From Isolation to the Third and a Half Generation: Understanding Naxinwei's Gate Driver IC in One Article
- The appeal of 48 V technology: importance, benefits and key factors in system-level applications
- Important breakthrough in recycling of used lithium-ion batteries
- Innolux's intelligent steer-by-wire solution makes cars smarter and safer
- 8051 MCU - Parity Check
- How to efficiently balance the sensitivity of tactile sensing interfaces
- What should I do if the servo motor shakes? What causes the servo motor to shake quickly?
- 【Brushless Motor】Analysis of three-phase BLDC motor and sharing of two popular development boards
- Midea Industrial Technology's subsidiaries Clou Electronics and Hekang New Energy jointly appeared at the Munich Battery Energy Storage Exhibition and Solar Energy Exhibition
- Guoxin Sichen | Application of ferroelectric memory PB85RS2MC in power battery management, with a capacity of 2M
- Analysis of common faults of frequency converter
- In a head-on competition with Qualcomm, what kind of cockpit products has Intel come up with?
- Dalian Rongke's all-vanadium liquid flow battery energy storage equipment industrialization project has entered the sprint stage before production
- Allegro MicroSystems Introduces Advanced Magnetic and Inductive Position Sensing Solutions at Electronica 2024
- Car key in the left hand, liveness detection radar in the right hand, UWB is imperative for cars!
- After a decade of rapid development, domestic CIS has entered the market
- Aegis Dagger Battery + Thor EM-i Super Hybrid, Geely New Energy has thrown out two "king bombs"
- A brief discussion on functional safety - fault, error, and failure
- In the smart car 2.0 cycle, these core industry chains are facing major opportunities!
- The United States and Japan are developing new batteries. CATL faces challenges? How should China's new energy battery industry respond?
- Murata launches high-precision 6-axis inertial sensor for automobiles
- Ford patents pre-charge alarm to help save costs and respond to emergencies
- New real-time microcontroller system from Texas Instruments enables smarter processing in automotive and industrial applications
- 【McQueen Trial】Use IPAD to program McQueen's car
- The STM32 FFT library calculates the amplitude normally, but the phase is different each time. Has anyone encountered this problem?
- EEWORLD University----UCD3138 Analog Front End (AFE) Module
- "Show goods" to come to a wave of commonly used development boards
- Measurement of the phase difference between a sine wave and a square wave
- [Sipeed LicheeRV 86 Panel Review] - 6 waft-ui component tests (3)
- Code size after keil compilation
- Tips for removing chip components on PCB
- Hardware System Engineer's Handbook
- Integrated operational amplifier practical circuit diagram