1. Comparison and selection of solutions
1 Circuit topology scheme
Solution 1: The power factor correction circuit adopts the flyback topology structure. The advantage is that the power factor correction and the power converter are combined into one, which can greatly reduce the circuit loss and improve the overall efficiency of the circuit. The disadvantage is that there are fewer types of active power factor correction control chips , and the circuit is relatively complex. It is difficult to design a suitable interface circuit with the microcontroller, and it is not easy to use the microcontroller for control.
Solution 2: Separate the power factor correction circuit from the main control circuit and use a Boost-type power factor correction circuit followed by a power converter. The advantage is that the circuit structure is simple and does not involve the control of the power factor correction circuit by the microcontroller. It only needs to make the power factor correction part output a stable voltage. The disadvantage is that it will reduce the overall efficiency of the design to a certain extent.
Since this question requires the function of step voltage regulation, the microcontroller needs to have good and stable control over the PWM control chip, so option 2 is selected.
2 Power Converter Solution
Solution 1: Use a half-bridge conversion circuit. The advantages are high utilization of the high-frequency transformer, large transmission power, and high circuit efficiency. The disadvantages are that the circuit is more complicated and there is a risk of shoot-through.
Solution 2: Use a single-ended flyback conversion circuit. The advantage is that the circuit structure is simple, but the disadvantage is that the high-frequency transformer has a low utilization rate, an air gap needs to be left, and the circuit efficiency is not high.
Since this problem requires a maximum load of only 10 1W LEDs and the transmission power is relatively small, option 2, the flyback circuit topology, is adopted.
3 Closed-loop feedback control scheme
Solution 1: Use software closed-loop feedback control, that is, use a single-chip microcomputer to sample various parameters, and then directly control the PWM control chip by the single-chip microcomputer to adjust the duty cycle. The advantage is that the circuit structure is simple, and the disadvantage is that the feedback loop will be affected by factors such as sampling accuracy, sampling speed, and single-chip microcomputer operation speed, making the feedback system unstable.
Solution 2: Use hardware closed-loop feedback control, that is, use hardware circuits to build feedback circuits, and let the PWM control chip itself adjust the duty cycle according to the feedback signal, while the microcontroller only assists in adjusting the PWM control chip. The advantages are fast feedback speed and high adjustment accuracy, and the disadvantage is that it is susceptible to external interference.
4 Active Power Factor Correction Solution
Solution 1: Use UC3854 as the main control chip of the active power factor correction circuit. The advantage is that the power factor correction coefficient can reach 99.5%, and the disadvantage is that the peripheral circuit is very complicated and difficult to debug. Solution 2: Use MC33260 as the main control chip of the active power factor correction circuit. The advantage is that the peripheral circuit is simple, and the disadvantage is that the power factor correction rate is slightly lower than that of UC3854.
220VAC is stepped down to 36VAC by an industrial frequency transformer, input into the power factor correction circuit through the startup impact current suppression circuit, and then powered on by the high-frequency isolation transformer to the LED lamps connected in series. The voltage and current are sampled at the LED lamps and returned to the PWM control chip and the single-chip microcomputer. The single-chip microcomputer gives a reference voltage to control the PWM control chip, thereby achieving the purpose of controlling the constant current of the LED lamp.
The overall structure diagram of the system is shown in Figure 1.

Figure 1 System overall block diagram
2. Circuit and Program Design
1 Power converter main circuit and device selection
The PWM control chip uses SG3525. The main features of SG3525 are: the output stage adopts push-pull output, dual-channel output, and the duty cycle is adjustable from 0 to 50%. The maximum drive current of each channel can reach 200mA, and the peak current of the input and pull current can reach 500mA.
Pins 1 and 2 of SG3525 are the inverting input and non-inverting input of the internal error amplifier respectively. The inverting input receives the feedback voltage signal, and the non-inverting input is a given voltage reference, which is generally connected to the voltage divider of the 16-pin voltage reference. Since the question requires that the current step is adjustable during constant current output, the non-inverting input is connected to the reference voltage generated by the microcontroller DAC module.
The current sampling of the load is completed by the sampling resistor connected in series between the LED load and the ground, and is respectively given to the microcontroller and the PWM control chip after a first-level follower and a first-level in-phase amplification; the voltage sampling is completed by the voltage division on the load and the current sampling resistor, and is respectively given to the microcontroller and the PWM control chip after a first-level follower. In order to complete the switching between constant voltage and constant current mode, an N-channel MOSFET is added as an electronic switch between the voltage sampling loop and the current sampling loop and the PWM control chip to complete the switching. In order to ensure the stability of the feedback, a first-level follower is added after the MOSFET to pass the feedback signal to the PWM control chip.

Figure 2 PWM control module
2 Control circuit and control program design
Since the control part of this design does not require a large amount of calculation and the requirement for calculation speed is not very high, but ADC and DAC modules are needed to sample voltage and current and control the PWM control chip, the C8051F020 microcontroller is selected as the core processing chip. It has a high-speed 8051 microcontroller core, 8 12-bit ADCs and 2 12-bit DACs, which can fully meet the design requirements.
Since this LED constant current power supply is in a stable state most of the time when it is working, and there is no requirement for a fast response speed, it is not necessary to sample the voltage and current signals simultaneously, but can be sampled separately. The mode switching and reference voltage adjustment do not need to be completed in the interrupt service. Only the key program for stepping the current adjustment needs to be completed in the interrupt service. [page]
3. Protection circuit design
The overvoltage protection circuit is not designed separately, but integrated into the current control circuit. It is completed by switching between the constant current control loop and the constant voltage control loop. When the microcontroller detects that the voltage on the load is higher than 36V, the microcontroller controls the constant current control loop to switch to the constant voltage control loop, and controls the load voltage to be slightly higher than 36V. When it is detected that the load current drops below the set current again, the constant voltage mode is switched to the constant current mode again to achieve the purpose of overvoltage protection.

Figure 3 Control program flow chart
4 Power Factor Correction Circuit Design
The low-power power factor correction chip MC33260 is selected, which works in the current critical mode. The application of MC33260 is simple and reliable. Through current detection and voltage feedback, the voltage is kept constant through PI regulation. The required voltage is obtained through PWM control of the switch tube. It can achieve the function of 0.998 power factor correction and output stable DC voltage.

Figure 4 Power factor correction module
5. Automatic dimming circuit design, power-on impact circuit and EMI suppression circuit design
The automatic voltage regulation circuit uses a photoresistor as a photosensor, and uses a relatively strong light source to convert the intensity of light into high and low level signals. The voltage signal is collected back to the microcontroller using the built-in ADC of the microcontroller. When the light intensity is high, the microcontroller controls the switch to constant current mode, and the set load current value is 100mA, so that the brightness of the LED decreases as the light intensity increases.
The power-on impact circuit uses a thermistor in series at the power input end. When the temperature is low, the resistance is large. As the temperature of the resistor increases, the resistance gradually decreases, achieving the purpose of suppressing excessive switching impact current.
The EMI suppression circuit uses the characteristics of inductance and capacitance to allow AC with a frequency of about 50Hz to pass through the filter smoothly, but high-frequency interference waves above 50Hz are filtered out by the filter. This allows the high-frequency harmonics generated by the switching power supply to be filtered out without polluting the power grid.

Figure 5 Power-on surge current and EMI suppression module
3. Theoretical Analysis and Calculation
1 Constant current control method and parameter calculation
Connect a sampling resistor with a smaller resistance in series between the LED load and the low. Assuming the current flowing through the LED is I, the voltage across the sampling resistor is:

Where R0 is the resistance value of the sampling resistor, and R0=Ω. The voltage remains unchanged after the first stage, and the next stage is a common-mode amplifier circuit, and the amplification factor is:

The next level is followed by a voltage that remains unchanged, so the voltage returned to the PWM control chip is:

The microcontroller gives the PWM control chip a reference voltage UREF through the DAC. The PWM control chip adjusts the duty cycle to adjust the voltage of the secondary winding and thus adjust the load current. Through the closed-loop negative feedback regulation, U0=UREF, and the current flowing through the load is:

As long as the output voltage of the DAC module of the single-chip microcomputer is adjusted according to the above formula, the load will operate at a required constant current value.
2 Design and calculation of isolation transformer
The output voltage of the power factor correction circuit is 55V. The required load is 10 LED lamps connected in series. The measured voltage during normal operation is about 34V. The transformer ratio is approximately:

Since the output duty cycle range of the PWM control chip is 0%~50%, the actual number of turns on the primary side is 45, the number of turns on the secondary side is 56, and the transformation ratio is 1.24.
3 Ways to Improve Efficiency
Selecting a suitable main circuit topology, using as few components as possible, and reducing the switching frequency; selecting switching devices with small conduction losses for the main circuit; using components with low operating voltage as much as possible when designing measurement and control circuits; and using digital methods to implement control circuits as much as possible can effectively improve the efficiency of the system.
4 Filter parameter calculation
The flyback voltage converter needs to output DC, so all harmonics should be filtered out as much as possible. The LC passive low-pass filter circuit can meet the requirements. The switching frequency of the flyback converter is 32kHz, and the cutoff frequency of the designed filter should be lower than 32KHz, that is:

Since this system is a constant current system, a larger L value should be used and the C value should be appropriately reduced, and the L and C values should be set accordingly. A 470μF electrolytic capacitor is selected, and the inductance value is about 0.78mH according to calculations, and a homemade I-shaped filter inductor is used. [page]
4. Test plan and test results
1. Test instruments and equipment
(1) Power frequency transformer
(2) 4.5-digit digital multimeter DT9203
(3) Agilent Oscilloscope DSO5012A
2 Test Data
(1) Output current tracking test:
Table 1 Output current display tracking test

(2) Voltage regulation test (set current to 150mA):
Table 2 Voltage Regulation Test

When the current changes from 32V to 40V, the range is 149mA to 150mA and the adjustment rate is 0.6%. The voltage adjustment rate Su≤1%. To meet the requirements:
(3) Load regulation test
The input voltage is 36.23V, the set current is 300mA, and the output current fluctuation range is 209mA~300mA when the load increases from 5 LEDs to 10 LEDs. The adjustment rate is 0.4%. The load adjustment rate SL≤1% meets the requirements.
Table 3 Load Regulation Test

(4) Efficiency test
U2=36V, load is 10 LEDs, I0=300mA.
Table 4 Efficiency η parameter test

(5) Power factor test
The measured power factor is 0.998, which meets the requirements.

Figure 6 Power factor correction waveform
Previous article:Design of Embedded Alarm System Based on GPRS
Next article:The design of serial port protocol network based on single chip microcomputer
Recommended ReadingLatest update time:2024-11-16 14:57
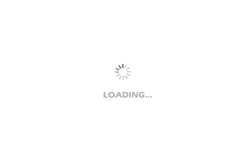
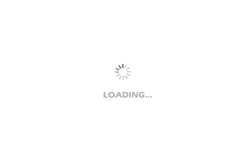
- Popular Resources
- Popular amplifiers
Professor at Beihang University, dedicated to promoting microcontrollers and embedded systems for over 20 years.
- Innolux's intelligent steer-by-wire solution makes cars smarter and safer
- 8051 MCU - Parity Check
- How to efficiently balance the sensitivity of tactile sensing interfaces
- What should I do if the servo motor shakes? What causes the servo motor to shake quickly?
- 【Brushless Motor】Analysis of three-phase BLDC motor and sharing of two popular development boards
- Midea Industrial Technology's subsidiaries Clou Electronics and Hekang New Energy jointly appeared at the Munich Battery Energy Storage Exhibition and Solar Energy Exhibition
- Guoxin Sichen | Application of ferroelectric memory PB85RS2MC in power battery management, with a capacity of 2M
- Analysis of common faults of frequency converter
- In a head-on competition with Qualcomm, what kind of cockpit products has Intel come up with?
- Dalian Rongke's all-vanadium liquid flow battery energy storage equipment industrialization project has entered the sprint stage before production
- Allegro MicroSystems Introduces Advanced Magnetic and Inductive Position Sensing Solutions at Electronica 2024
- Car key in the left hand, liveness detection radar in the right hand, UWB is imperative for cars!
- After a decade of rapid development, domestic CIS has entered the market
- Aegis Dagger Battery + Thor EM-i Super Hybrid, Geely New Energy has thrown out two "king bombs"
- A brief discussion on functional safety - fault, error, and failure
- In the smart car 2.0 cycle, these core industry chains are facing major opportunities!
- The United States and Japan are developing new batteries. CATL faces challenges? How should China's new energy battery industry respond?
- Murata launches high-precision 6-axis inertial sensor for automobiles
- Ford patents pre-charge alarm to help save costs and respond to emergencies
- New real-time microcontroller system from Texas Instruments enables smarter processing in automotive and industrial applications
- SinlinxA33 Development Board Linux Interrupt Programming 4-Final Code (1)
- Production of msp430g2553 emulator download line
- EEWORLD University Hall ---- Computer Vision Course Tsinghua University Wang Mingzhe
-
EEWORLD University Hall----Live Replay:
takes you to learn about ADI's digital health biosensor series - Switching power supply using microcontroller for loop control
- [Recruitment] Shenzhen foreign companies are urgently recruiting RF antenna engineers, looking forward to your joining
- No more confusion! A guide to choosing a cordless vacuum cleaner
- [Raspberry Pi 3B+ Review] GCC Compiles HelloWorld & Lighting Program
- 【Evaluation of EVAL-M3-TS6-665PN development board】——by landeng1986
- [GD32E231 DIY Contest] (I): Development Environment Construction + TIMER5