The H-bridge cascade multilevel converter uses a method of connecting multiple power units in series to achieve high voltage output. Its output mostly uses a multi-level phase-shifted PWM control method to achieve lower output voltage harmonics, smaller dv/dt and common-mode voltage and smaller torque pulsation. To achieve high voltage, it is only necessary to simply increase the number of units. This implementation method has low technical difficulty. Each power unit is a separate DC power supply, which is independent of each other. The control of one unit will not affect other units. The main difference between the implementation method of the H-bridge cascade inverter and the single-bridge inverter lies in the PWM control method. This article discusses the PWM control method of the H-bridge cascade inverter.
2 H-bridge cascade inverter structure
Each power unit is an independent DC power supply, and its design method is shown in Figure 1 below:
Figure 1 Power unit structure diagram |
According to the description of the power unit in the above figure, the power unit of this implementation can generate three levels, namely +Udc, 0, and -Udc. When S1 and S4 are turned on, and S2 and S3 are turned off, the load obtains a voltage of +Udc; when S2 and S3 are turned on, and S1 and S4 are turned off, the load obtains a voltage of -Udc; when S1 and S3 (or S2 and S4) are turned on, and S2 and S4 (or S1 and S3) are turned off, the load obtains a voltage of 0 (Note: In the control process, it is necessary to strictly avoid the two power devices in the same bridge arm being turned on at the same time, that is, the two control signals of the same bridge arm are required to be opposite). Therefore, it can be seen that when different PWM control strategies are used, different PWM waveforms can be generated.
3 Carrier phase shift control theory
Generally speaking, N-1 triangular carriers are required for inverter modulation of the N level. In the carrier phase shift modulation method, all triangular waves have the same frequency and amplitude, but the phases of any two adjacent carriers must have a certain phase shift, and its value is
4 PWM control strategy
The inverter usually outputs in the form of a sinusoidal wave. For a single-phase bridge, its output can usually be divided into two modes: unipolar modulation and bipolar modulation (due to space limitations, the specific implementation method can be found in the references). The inverter based on the H-bridge method can also output a waveform similar to the single-phase bridge output, and its PWM control strategy should be slightly adjusted. The waveforms output by unipolar modulation and bipolar modulation differ in performance. Since unipolar modulation can output three levels, while bipolar modulation can only output two levels, the dv/dt of bipolar modulation is larger, which has a greater impact on the insulation of the motor. In the product design process, a unipolar modulation waveform is usually used as the final output waveform. This paper takes the structure of the H-bridge cascade inverter and the SPWM generated by the carrier phase shift method as the control signal of each power unit to achieve the output of a unipolar SPWM waveform. Several PWM control strategies are discussed and studied below:
1) Single-arm chopping: The so-called single-arm chopping method is that S1 and S2 are used as half-cycle control signals. When the positive half cycle is, S1 is turned on and S2 is turned off; when the negative half cycle is, S1 is turned off and S2 is turned on; the control signal of S3 is SPWM signal.
Figure 2 S3 control signal waveform |
Figure 3 S1 control signal waveform |
Figure 4 Power unit output waveform |
3) Unipolar modulation: Although the single bridge arm chopping method can achieve an output waveform similar to the single-phase bridge unipolar modulation, this control method has inherent defects. Here we introduce another control method. As shown in Figure 1, S1 is controlled by the control signal shown in Figure 5, S3 is controlled by the control signal shown in Figure 6, and S2 and S4 are the reverse signals of the control signals of S1 and S2 respectively. The control signals shown in Figures 5 and 6 are symmetrical SPWM signals with a fundamental phase difference of 180 degrees. Since the fundamental phase difference is 180 degrees, the duty cycle of the carrier cycle corresponding to the two control signals is 1, that is, complementary. There are four combinations of output waveforms: S1 is on, S3 is off, output +Udc; S1 is on, S3 is on, output 0; S1 is off, S3 is off, output 0; S1 is off, S3 is on, output -Udc. See the left side of the dotted line in the figure, the first three switch combinations will appear, and the right side of the dotted line will appear the last three switch combinations, that is, the PWM wave with a duty cycle that satisfies the sinusoidal change as shown in Figure 7 can be output.
Figure 5 Left bridge arm control signal |
Figure 6 Right bridge arm control signal |
Figure 7 H-bridge unipolar modulation output waveform |
The PWM control implemented in this way realizes the transformation from unipolar SPWM to bipolar SPWM, and realizes the power balance of the left and right bridge walls. At the same time, the inverter output voltage harmonics obtained in this way are very low, and the output does not need to use a filter, which is called a perfect harmonic-free inverter. In the inverter control, DSP control is usually used. Since DSP can only output two levels, it cannot directly realize unipolar SPWM and requires the assistance of external devices. This method uses the combination logic relationship of the power unit (the logic relationship is shown in Table 1) to replace the function of the external device, saving devices, reducing development costs and development difficulties, and is simple to control and easy to implement.
Table 1 Logical relationship |
In high-power and high-voltage inverter technology, PWM control technology is one of its core technologies. A good PWM control strategy is the guarantee of product performance. In this paper, the PWM control method of H-bridge cascade high-power and high-voltage inverter is mainly discussed, three implementation methods are given, and their implementation methods and performance are analyzed and compared.
Previous article:Load management and load switch design and implementation in power supplies
Next article:Realization of Programmable Filter Based on MAX267
Recommended ReadingLatest update time:2024-11-15 15:27
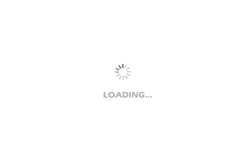
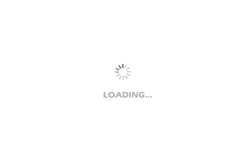
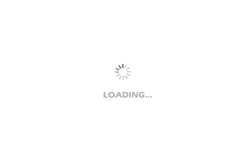
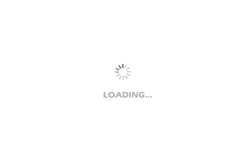
- Popular Resources
- Popular amplifiers
-
西门子S7-12001500 PLC SCL语言编程从入门到精通 (北岛李工)
-
Small AC Servo Motor Control Circuit Design (by Masaru Ishijima; translated by Xue Liang and Zhu Jianjun, by Masaru Ishijima, Xue Liang, and Zhu Jianjun)
-
Intelligent Control Technology of Permanent Magnet Synchronous Motor (Written by Wang Jun)
-
100 Examples of Microcontroller C Language Applications (with CD-ROM, 3rd Edition) (Wang Huiliang, Wang Dongfeng, Dong Guanqiang)
- MathWorks and NXP Collaborate to Launch Model-Based Design Toolbox for Battery Management Systems
- STMicroelectronics' advanced galvanically isolated gate driver STGAP3S provides flexible protection for IGBTs and SiC MOSFETs
- New diaphragm-free solid-state lithium battery technology is launched: the distance between the positive and negative electrodes is less than 0.000001 meters
- [“Source” Observe the Autumn Series] Application and testing of the next generation of semiconductor gallium oxide device photodetectors
- 采用自主设计封装,绝缘电阻显著提高!ROHM开发出更高电压xEV系统的SiC肖特基势垒二极管
- Will GaN replace SiC? PI's disruptive 1700V InnoMux2 is here to demonstrate
- From Isolation to the Third and a Half Generation: Understanding Naxinwei's Gate Driver IC in One Article
- The appeal of 48 V technology: importance, benefits and key factors in system-level applications
- Important breakthrough in recycling of used lithium-ion batteries
- LED chemical incompatibility test to see which chemicals LEDs can be used with
- Application of ARM9 hardware coprocessor on WinCE embedded motherboard
- What are the key points for selecting rotor flowmeter?
- LM317 high power charger circuit
- A brief analysis of Embest's application and development of embedded medical devices
- Single-phase RC protection circuit
- stm32 PVD programmable voltage monitor
- Introduction and measurement of edge trigger and level trigger of 51 single chip microcomputer
- Improved design of Linux system software shell protection technology
- What to do if the ABB robot protection device stops
- Learn ARM development(19)
- Learn ARM development(14)
- Learn ARM development(15)
- Analysis of the application of several common contact parts in high-voltage connectors of new energy vehicles
- Wiring harness durability test and contact voltage drop test method
- From probes to power supplies, Tektronix is leading the way in comprehensive innovation in power electronics testing
- From probes to power supplies, Tektronix is leading the way in comprehensive innovation in power electronics testing
- Sn-doped CuO nanostructure-based ethanol gas sensor for real-time drunk driving detection in vehicles
- Design considerations for automotive battery wiring harness
- Do you know all the various motors commonly used in automotive electronics?
- Application of 4G solar energy monitoring
- I heard there are gifts for watching videos?
- GD32E231 analog IIC driver LPS22HH
- Today's live broadcast: ADI's vital signs monitoring solutions in wearable products
- ESP8266-01S connected to Gizwits IoT platform
- The characteristics of low-power Bluetooth determine that it is worth looking forward to~
- [Runhe Neptune Review] Three code modifications
- 【AT32F421 Review】+Serial Communication Test
- Have you ever seen such a collection circuit? ADC signal collection
- Where is Bluetooth technology heading?