4-20mA current loop signals are often used in industrial environments to transmit data such as process temperature or container pressure over long distances. This method of signal transmission is preferred because it is simple, noise-resistant, safe, and can be transmitted over long distances without data corruption. These current loops are also low-power systems because the current used to transmit data is relatively low. Previously, power that was not utilized, or power lost during signal transmission, was dissipated within the transmitter; but now, with modern integrated circuits, even this small amount of power is saved to support the normal operation of the necessary functions in the system.
4-20mA Current Loop System Basics
Figure 1 shows a typical 4-20mA current loop system. A semi-regulated 24V DC power supply powers both the current loop and the transmitter components. The transmitter measures the important signal (such as temperature, pressure, and other parameters) and outputs a 2-20mA current that is proportional to the strength of the signal. This current is transmitted through the wire to a receiver system. The current then encounters a resistor to form a voltage, which is read by an analog-to-digital converter (ADC) and further processed. The connection is connected back to the voltage source that powers the loop, thus completing the loop.
Figure 1 Basic 4-20mA current loop system
Using these current loops in industrial applications has many benefits:
Current loops are simple circuits that require only a simple power supply, a transmitter that measures and then generates the current, a transmission line, and a receiver circuit. The power supply only needs to provide enough voltage to overcome various system voltage drop issues; the excess loop voltage is just dropped at the transmitter. Because the current is low, only a small amount of power is consumed, so less heat is generated.
The current loop contains only one current loop. Therefore, according to Kirchhoff's current law, the current through all components in the loop is equal. This achieves high noise immunity, which is key for applications in industrial environments.
l Safety is achieved because the signal level is as low as 4mA. If there is damage inside the loop or the loop connection is disconnected, the receiver cannot read the current, which indicates a fault rather than a minimum signal level.
l As long as the supply voltage is high enough to overcome the system voltage drop, the ideal current representing the measured signal is maintained by the transmitter. Therefore, high-voltage drop and low-cost small-gauge wire is used for interconnection, which only requires an increase in the supply voltage. Most importantly, the line can tolerate a relatively large voltage drop, so a large number of wires can be used. In this way, physical isolation can be achieved between the instrument under test and the control room where the measurement data is processed, providing safety protection for the personnel in the control room.
Basic system improvements
We can use the excess loop voltage, which would otherwise be dropped at the transmitter, to power receiver circuits. Figure 2 shows a power supply inserted in the current loop. The supply is located in the control room along with the receiver circuit it powers—effectively converting the excess loop voltage into useful output power.
Figure 2 Utilization of excess loop voltage in a 4-20mA current loop
Since the receiver resistor is no longer referenced to ground, a level shifting circuit may be required to interface with the data converter input. Any high-end current shunt monitor (such as TI INA138, etc.) can provide this very simple circuit. These devices measure the small sense resistor voltage drop across the common-mode voltage, thereby reducing the necessary voltage drop across the receiver resistor. This allows more voltage to be used by the power supply, thereby reducing energy waste.
This power supply typically provides a regulated 3.3V output to power level shifters, data converters, and all other low-power devices in the control room. For example, a microprocessor from TI's MSP430TM platform that examines received data and makes decisions, and a low-power RF device from TI's CC430 series that transmits data wirelessly to other places. Wireless transmitters are particularly useful if there is a cost savings to be made by not having to purchase and install wiring for particularly long current loops. The power consumption of these devices must be very low because the amount of excess energy that can be extracted from the current loop is limited.
Finally, the power supply must also be able to work with such low power supplies—4mA minimum and 20mA maximum. Since the voltage generated by this current is an excess voltage of the loop, the power supply must accept a wide input voltage range and still provide a stable output. Even more difficult for this power supply is starting the system with a current-limited power supply. Generally speaking, higher output power is required during startup to charge the output capacitor and provide the startup current to the load. It is much higher than the amount consumed by the system during normal operation. If the power supply is to provide this high power during startup, its output power will exceed the amount provided by the current loop. If this happens, the voltage entering the power supply will continue to drop before the power supply turns off. As a result, its input voltage will rise again before it turns back on and the process repeats itself. Startup oscillation is a problem we need to overcome when the power supply operates from such a small input power.
Energy utilization solutions
As mentioned earlier, a waste-energy power supply must have a wide input voltage range, be able to operate from very small input powers, and avoid startup oscillations when powered from a current-limited power supply. TI's TPS62125 is such a power supply because it operates from a 3-17V input, requires only 11 µA of operating current, and has a programmable enable threshold voltage with adjustable hysteresis. There are three small changes to the circuit suggested in the TPS62125 data sheet:
1. Add a 15V Zener diode to the device input to protect it from excess loop voltages exceeding its 17V rating. This diode is not necessary if a low-voltage current loop system is used. A Zener diode with a maximum voltage of 15.6V gives good results.
2. Add bulk capacitors to the device input to store enough energy for startup and load changes. Depending on the power requirements of the load during startup, this capacitor may not be needed. A total of about 200 µF of capacitors will allow a smooth startup of the example load, which requires a 3.3V, 50Ma power supply for 30ms at startup and only 10mA after startup. Bulk capacitors can also provide storage energy for periodic high power requirements that may occur, such as: temperature measurement, data converter reading operations, or sending data through the antenna.
3. The device's enable threshold voltage is adjusted so that the device turns on when its voltage reaches 12 V. The device is programmed to shut down when its input drops to 4 V. Once enabled, the device efficiently converts this repurposed energy into its 3.3 V output.
For example, for a power solution, we choose 4V as the shutdown voltage in order to provide a specified margin from the input voltage to the output voltage, so that the device can maintain a regulated output of 3.3V. A 12V startup voltage is used to meet various system requirements. We assume that the 24V power supply varies between 18V and 30V, and the current loop voltage drop totals a maximum of 6V, so that the device can withstand a minimum of 12V in extreme cases. Therefore, we choose 12V as the point to start the power supply because it is the minimum voltage that the device may withstand. In addition, the 12V minimum voltage can achieve sufficient intervals between the startup voltage and the shutdown voltage, so that the power supply starts into a high power load state without startup oscillation.
The power solution described above is started and shut down by TI’s XTR111. The XTR111 is a 4-20mA current loop transmitter that can always provide less than 4mA of current. Figure 3 shows the startup of this solution. Once the transmitter is enabled, it starts to provide current, which raises the input voltage to the 12V turn-on point of the power supply. The power supply output voltage rises into the regulation region and then immediately provides 50mA of load startup current. This slightly reduces the input voltage of the power supply, but the power supply maintains regulation of the output voltage due to its wide voltage range and large input capacitors. After the load startup energy consumption lasts for 30ms, the load current decreases to a steady state, that is, the 10mA level. The input voltage rises further and is controlled by the Zener diode to remain at the 15V level. As we have already noticed, the current provided by the current loop always remains below 4mA.
Figure 3 Startup of waste energy utilization power supply
Figure 4 shows a zoomed-in view of Figure 3. The power supply draws stored energy from the bulk capacitor to meet the startup load current demand while the current loop always provides less than 4 mA. This energy draw reduces the input voltage by about 2 V, but this is acceptable for this power supply.
Figure 4: Waste energy utilization power supply providing load starting current
Finally, the waste-energy power supply stores enough energy in a bulk capacitor and then operates over a wide enough input voltage range to provide sustained power pulses to the load. The power supply shown in Figure 5 provides 20mA of current to the load for 100ms per second and maintains regulation of the power supply output voltage.
Figure 5: Waste energy utilization power supply providing load power pulse
in conclusion
In a 4-20mA current loop system, we can make effective use of the wasted power. This power can power the data converters and microprocessors needed in the control room to process the data from the current loop, and it can also power low-power RF transmitters, thereby expanding the application range of the 4-20mA current loop and saving the cost of such systems by reducing the amount of wiring required. A power supply with a wide input voltage range, operating with very low power and being able to start up with a current-limited power supply without oscillation can make the wasted energy re-use and continue to play its role in the system.
Previous article:Description of power supply grounding standards
Next article:Switching Power Supply Principle
Recommended ReadingLatest update time:2024-11-16 19:55
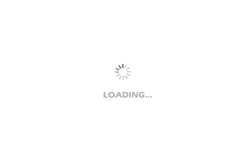
- Popular Resources
- Popular amplifiers
- MathWorks and NXP Collaborate to Launch Model-Based Design Toolbox for Battery Management Systems
- STMicroelectronics' advanced galvanically isolated gate driver STGAP3S provides flexible protection for IGBTs and SiC MOSFETs
- New diaphragm-free solid-state lithium battery technology is launched: the distance between the positive and negative electrodes is less than 0.000001 meters
- [“Source” Observe the Autumn Series] Application and testing of the next generation of semiconductor gallium oxide device photodetectors
- 采用自主设计封装,绝缘电阻显著提高!ROHM开发出更高电压xEV系统的SiC肖特基势垒二极管
- Will GaN replace SiC? PI's disruptive 1700V InnoMux2 is here to demonstrate
- From Isolation to the Third and a Half Generation: Understanding Naxinwei's Gate Driver IC in One Article
- The appeal of 48 V technology: importance, benefits and key factors in system-level applications
- Important breakthrough in recycling of used lithium-ion batteries
- Innolux's intelligent steer-by-wire solution makes cars smarter and safer
- 8051 MCU - Parity Check
- How to efficiently balance the sensitivity of tactile sensing interfaces
- What should I do if the servo motor shakes? What causes the servo motor to shake quickly?
- 【Brushless Motor】Analysis of three-phase BLDC motor and sharing of two popular development boards
- Midea Industrial Technology's subsidiaries Clou Electronics and Hekang New Energy jointly appeared at the Munich Battery Energy Storage Exhibition and Solar Energy Exhibition
- Guoxin Sichen | Application of ferroelectric memory PB85RS2MC in power battery management, with a capacity of 2M
- Analysis of common faults of frequency converter
- In a head-on competition with Qualcomm, what kind of cockpit products has Intel come up with?
- Dalian Rongke's all-vanadium liquid flow battery energy storage equipment industrialization project has entered the sprint stage before production
- Allegro MicroSystems Introduces Advanced Magnetic and Inductive Position Sensing Solutions at Electronica 2024
- Car key in the left hand, liveness detection radar in the right hand, UWB is imperative for cars!
- After a decade of rapid development, domestic CIS has entered the market
- Aegis Dagger Battery + Thor EM-i Super Hybrid, Geely New Energy has thrown out two "king bombs"
- A brief discussion on functional safety - fault, error, and failure
- In the smart car 2.0 cycle, these core industry chains are facing major opportunities!
- The United States and Japan are developing new batteries. CATL faces challenges? How should China's new energy battery industry respond?
- Murata launches high-precision 6-axis inertial sensor for automobiles
- Ford patents pre-charge alarm to help save costs and respond to emergencies
- New real-time microcontroller system from Texas Instruments enables smarter processing in automotive and industrial applications
- The problem of Bluetooth main module sending data to CC2541
- [Silicon Labs BG22-EK4108A Bluetooth Development Evaluation] 4. Download BootLoader and establish Bluetooth connection...
- b_l475e start
- Is there such a rule in C: When a hexadecimal number starts with a letter (AF), a 0 should be added in front, such as 0XA8, which should be written as 0X0A8
- C6000 Basic Instruction Set
- Current protection working principle
- 2020 02 02 Should be distributed at 20:20 Leave a footprint
- Can you provide a text box where I can paste the names of the 8 teachers I often invite directly, so that I don’t have to search them one by one?
- EEWORLD University ---- Miz702 zynq video advanced tutorial (Milinke)
- [National Technology N32G430] 6. STK33B62 optical sensor detection