This paper describes the design process of a three-phase voltage source PWM grid-connected inverter with direct current control, which is applied to photovoltaic grid-connected power generation system. The control strategy of the inverter is analyzed and studied, and a prototype is designed using Mitsubishi's intelligent power module IPM50RSA060 and Texas Instruments (TI)'s DSP chip TMS320LF2407. The final experimental results show that the inverter using PWM control is suitable for small and medium-sized power photovoltaic grid-connected power generation systems and has broad application prospects.
1 Photovoltaic grid connection
Power generation system composition
The photovoltaic grid-connected power generation system is mainly composed of solar panels (i.e. photovoltaic arrays), grid-connected inverters, filter reactors and DSP control circuits. The structure of the entire system is shown in Figure 1.
As shown in Figure 1, the photovoltaic grid-connected power generation system uses solar panels to convert solar energy into DC power, and then uses the controlled current source characteristics of the grid-connected inverter to control the inverter to operate in the power generation state, converting DC power into AC power to feed the grid.
The energy conversion and transfer process of the entire system is realized by using the grid-connected inverter circuit composed of IPM modules, and the control of the grid-connected inverter is completed by generating the PWM signal of the driving main circuit through DSP.
2 Grid-connected inverter control principle
According to the working principle of the photovoltaic grid-connected power generation system, the grid-connected inverter is the core device of the entire grid-connected power generation system, and the performance of the grid-connected inverter determines the performance of the entire system. For the photovoltaic grid-connected power generation system shown in Figure 1, the grid-connected inverter designed in this paper adopts a three-phase half-bridge inverter topology, and its structure is shown in Figure 2.
The voltage and current signals output by the AC side of the grid-connected inverter satisfy the following equations:
In the above model, L represents the inductance parameter on the AC side, and R is the parasitic resistance in the inductor. Since the equivalent impedance of the inductor is much larger than the resistance, the effect of R on the regulator design can be ignored during the system design process.
According to the mathematical model of the three-phase voltage source PWM grid-connected inverter, it can be seen that the grid-connected inverter controls the output current by controlling the output voltage of the three-phase voltage source inverter bridge arm. While controlling the output current, in order to increase the power generation of the photovoltaic grid-connected inverter system and make full use of the maximum power that the photovoltaic array can provide under the same lighting conditions, the maximum power point tracking (MPPT) technology is introduced in the control system of the corresponding photovoltaic grid-connected inverter device.
Figure 2 shows the control structure of the grid-connected inverter. It can be seen from Figure 2 that the outer loop of the control structure of the grid-connected inverter is the power loop, which adopts the self-optimizing MPPT algorithm. The self-optimizing algorithm calculates the output power at the current moment by sampling the output voltage and current signals of the current inverter device, and then compares it with the output power calculated at the previous moment. According to the output power, the working point of the grid-connected inverter is continuously adjusted, and finally the working point of the grid-connected inverter changes along the maximum power curve of the photovoltaic array. The inverter calculates the DC voltage loop command signal of the photovoltaic array at this power point according to the MPPT algorithm. The error signal of the voltage loop outputs the current loop amplitude command after passing through the PI regulator link. The amplitude command is multiplied by the synchronization signal of the grid voltage as the synchronization command signal of the current loop. The output current of the system is controlled by the current error and the inner loop proportional regulator. The gain of the current loop determines whether the system output current can accurately track the command signal, and at the same time determines whether the photovoltaic grid-connected system can achieve maximum power grid-connected power generation with a unity power factor. 3 Hardware Design
The digital controller is the core component of the grid-connected inverter device. The grid-connected inverter mainly uses the digital controller to realize data sampling, regulator calculation and PWM drive signal generation, and can also realize the communication function with the human-machine interface. The controller here chooses TI's DSP chip TMS320LF2407. The DSP chip is a high-speed dedicated microprocessor that maintains the characteristics of the general microprocessor system and has a better computing ability for digital signal processing than general microprocessors. It adopts an improved Harvard structure, multi-group bus technology to realize parallel operation mechanism, and a special multiplication and accumulator structure, as well as a very flexible instruction system, all of which greatly increase the computing speed and improve the flexibility of the system. At the same time, F2407 integrates many peripherals. F2407 contains a CPU with an operating rate of 20MIPS (million instructions per second), 32KB flash memory (Flash), 2592 words of data memory; 10-bit analog-to-digital converter; synchronous serial peripheral interface (SPI), asynchronous serial communication interface (SCI) and CAN communication interface; 4 power-down modes are available, using simulation technology based on JTAG scanning; event manager for PWM control, including 4 general timers, 9 comparison units, 12 PWM outputs. Its digital-to-analog converter can process 16 analog signals, can sample and convert 2 analog signals at the same time, and the A/D conversion time is less than 1μs. Its PWM waveform production unit contains programmable dead zone control, which can output asymmetric PWM waveforms, symmetric PWM waveforms or space vector PWM waveforms.
The inverter main circuit uses the intelligent power module IPM50RSA060 from Mitsubishi Corporation of Japan, which has 6 IGBTs forming a three-phase bridge arm, and also integrates various IGBT drive circuits and abnormal situation detection units, such as short circuit detection, overcurrent detection, undervoltage detection, overtemperature detection, etc. When any of the above abnormal signals is detected, the F0 signal of the IPM module can be sent to the power drive protection pin of the DSP through optical coupling isolation to achieve corresponding protection.
4 Software Design
By taking advantage of the DSP control circuit and combining it with the control algorithm of the inverter device, the inverter control system software with fixed switching frequency is designed. The system software consists of a main program and an interrupt service subroutine. Figure 3 is a flowchart of the interrupt service program for the software to realize the generation of PWM signals.
5 Experimental Results
Using the above scheme, this paper designed a 5kW prototype. Considering that the grid-connected inverter is directly connected to the power grid, the AC side output current determines the performance of the grid-connected inverter. Therefore, the system experiment mainly focuses on the waveform of the grid-connected output current and the power factor of the device.
As can be seen from Figure 4, the three-phase system has a good sinusoidal output current waveform, and the three-phase current remains balanced. As can be seen from Figure 5, when the grid-connected power generation is running, the grid side has a negative unity power factor.
6 Conclusion
This article comprehensively describes the DSP-based photovoltaic grid-connected inverter and its control software and hardware implementation. The designed grid-connected inverter can effectively realize the photovoltaic array grid-connected power generation function, and can output a smooth sinusoidal current with a unity power factor during power generation, and the waveform reduces the harmonic injection into the power grid. In the design process of the grid-connected inverter device, the high-speed digital signal processor and intelligent power module hardware with high integration, powerful protection function, and reliable performance are used to simplify the hardware design and cost of the grid-connected inverter device, while improving the reliability of the device operation.
Previous article:Design of digital inverter power supply based on ADMC331
Next article:Single-phase sine wave active inverter grid-connected power supply system
Recommended ReadingLatest update time:2024-11-16 15:31
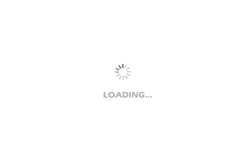
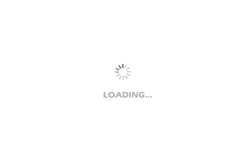
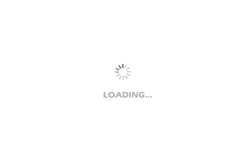
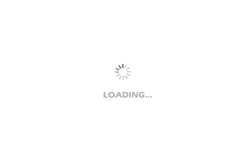
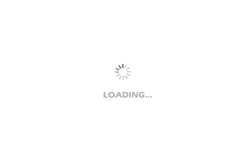
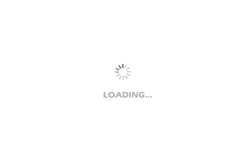
- Popular Resources
- Popular amplifiers
- MathWorks and NXP Collaborate to Launch Model-Based Design Toolbox for Battery Management Systems
- STMicroelectronics' advanced galvanically isolated gate driver STGAP3S provides flexible protection for IGBTs and SiC MOSFETs
- New diaphragm-free solid-state lithium battery technology is launched: the distance between the positive and negative electrodes is less than 0.000001 meters
- [“Source” Observe the Autumn Series] Application and testing of the next generation of semiconductor gallium oxide device photodetectors
- 采用自主设计封装,绝缘电阻显著提高!ROHM开发出更高电压xEV系统的SiC肖特基势垒二极管
- Will GaN replace SiC? PI's disruptive 1700V InnoMux2 is here to demonstrate
- From Isolation to the Third and a Half Generation: Understanding Naxinwei's Gate Driver IC in One Article
- The appeal of 48 V technology: importance, benefits and key factors in system-level applications
- Important breakthrough in recycling of used lithium-ion batteries
- Innolux's intelligent steer-by-wire solution makes cars smarter and safer
- 8051 MCU - Parity Check
- How to efficiently balance the sensitivity of tactile sensing interfaces
- What should I do if the servo motor shakes? What causes the servo motor to shake quickly?
- 【Brushless Motor】Analysis of three-phase BLDC motor and sharing of two popular development boards
- Midea Industrial Technology's subsidiaries Clou Electronics and Hekang New Energy jointly appeared at the Munich Battery Energy Storage Exhibition and Solar Energy Exhibition
- Guoxin Sichen | Application of ferroelectric memory PB85RS2MC in power battery management, with a capacity of 2M
- Analysis of common faults of frequency converter
- In a head-on competition with Qualcomm, what kind of cockpit products has Intel come up with?
- Dalian Rongke's all-vanadium liquid flow battery energy storage equipment industrialization project has entered the sprint stage before production
- Allegro MicroSystems Introduces Advanced Magnetic and Inductive Position Sensing Solutions at Electronica 2024
- Car key in the left hand, liveness detection radar in the right hand, UWB is imperative for cars!
- After a decade of rapid development, domestic CIS has entered the market
- Aegis Dagger Battery + Thor EM-i Super Hybrid, Geely New Energy has thrown out two "king bombs"
- A brief discussion on functional safety - fault, error, and failure
- In the smart car 2.0 cycle, these core industry chains are facing major opportunities!
- The United States and Japan are developing new batteries. CATL faces challenges? How should China's new energy battery industry respond?
- Murata launches high-precision 6-axis inertial sensor for automobiles
- Ford patents pre-charge alarm to help save costs and respond to emergencies
- New real-time microcontroller system from Texas Instruments enables smarter processing in automotive and industrial applications
- Explanation of common parameters of transformers
- GD32E231 Learning 2: GPIO drive OLED and TC0 timing interrupt
- Ofweek Talent Network recruitment and job search results, let's talk about it
- A flaw in the MSP430F672x, 673x microcontrollers
- Looking forward to Huawei's operating system!
- Test parameters of 1630MHz125 amplifier
- Analysis of the types of pads and design standards in PCB design
- Why should the power supply be set to +3.3V?
- Analysis of the composition and working principle of the radio frequency identification system
- Arduino Bluetooth Obstacle Avoidance Car